Rapid Tooling Services
Instant quotes and DFM feedback
Complex parts as fast as 2 days
2D drawings accepted
95.4% parts delivered on time and to-spec
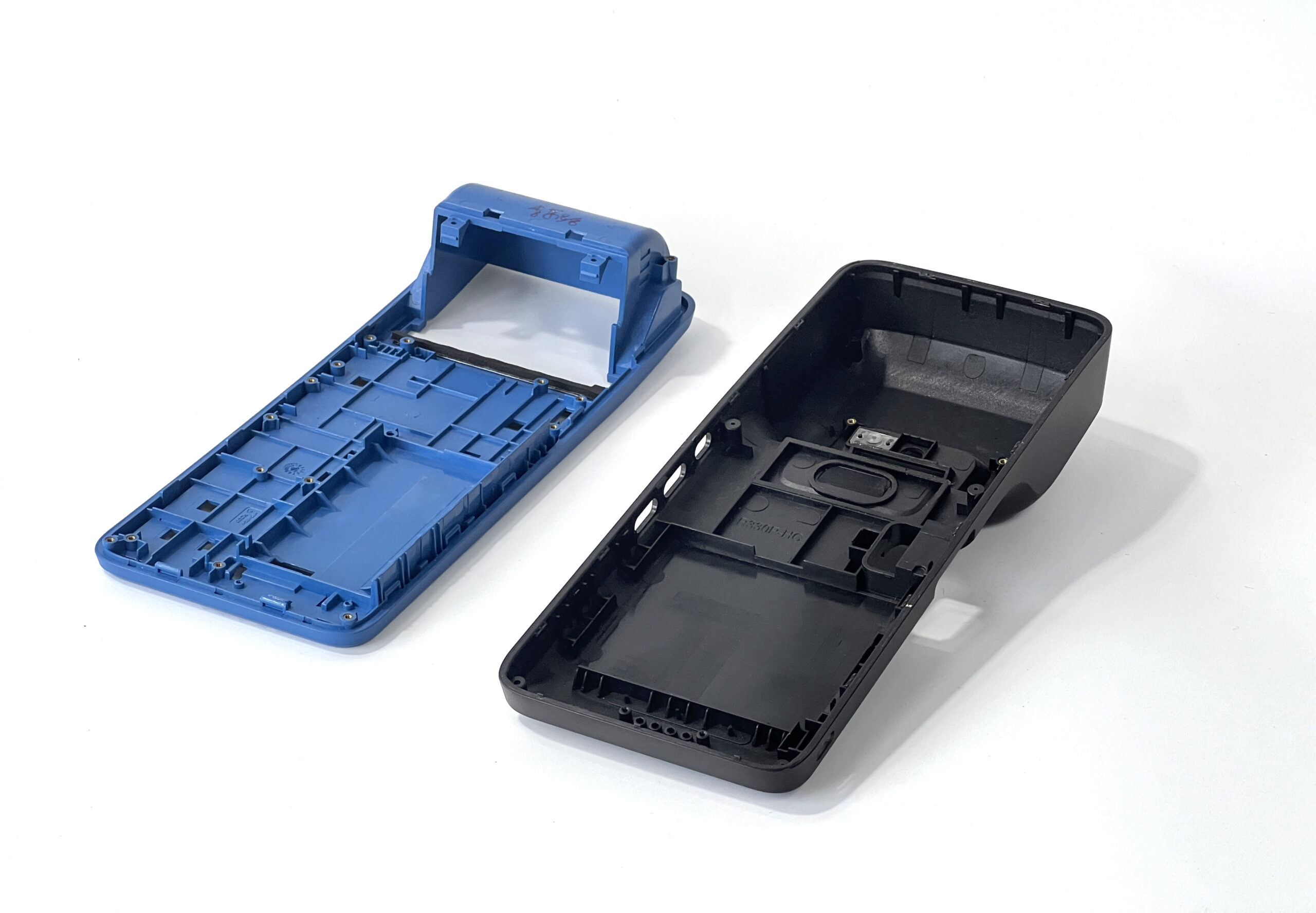
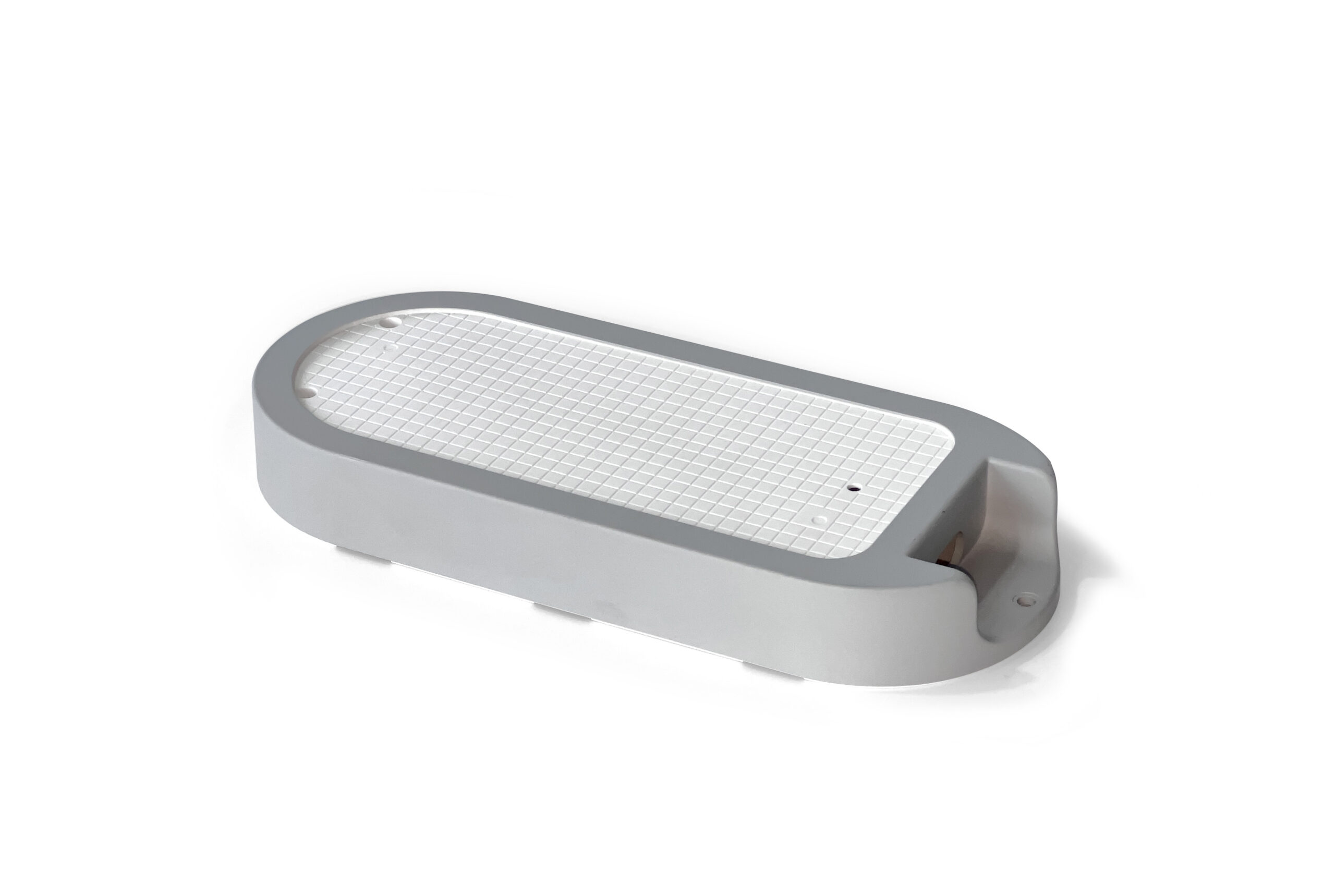
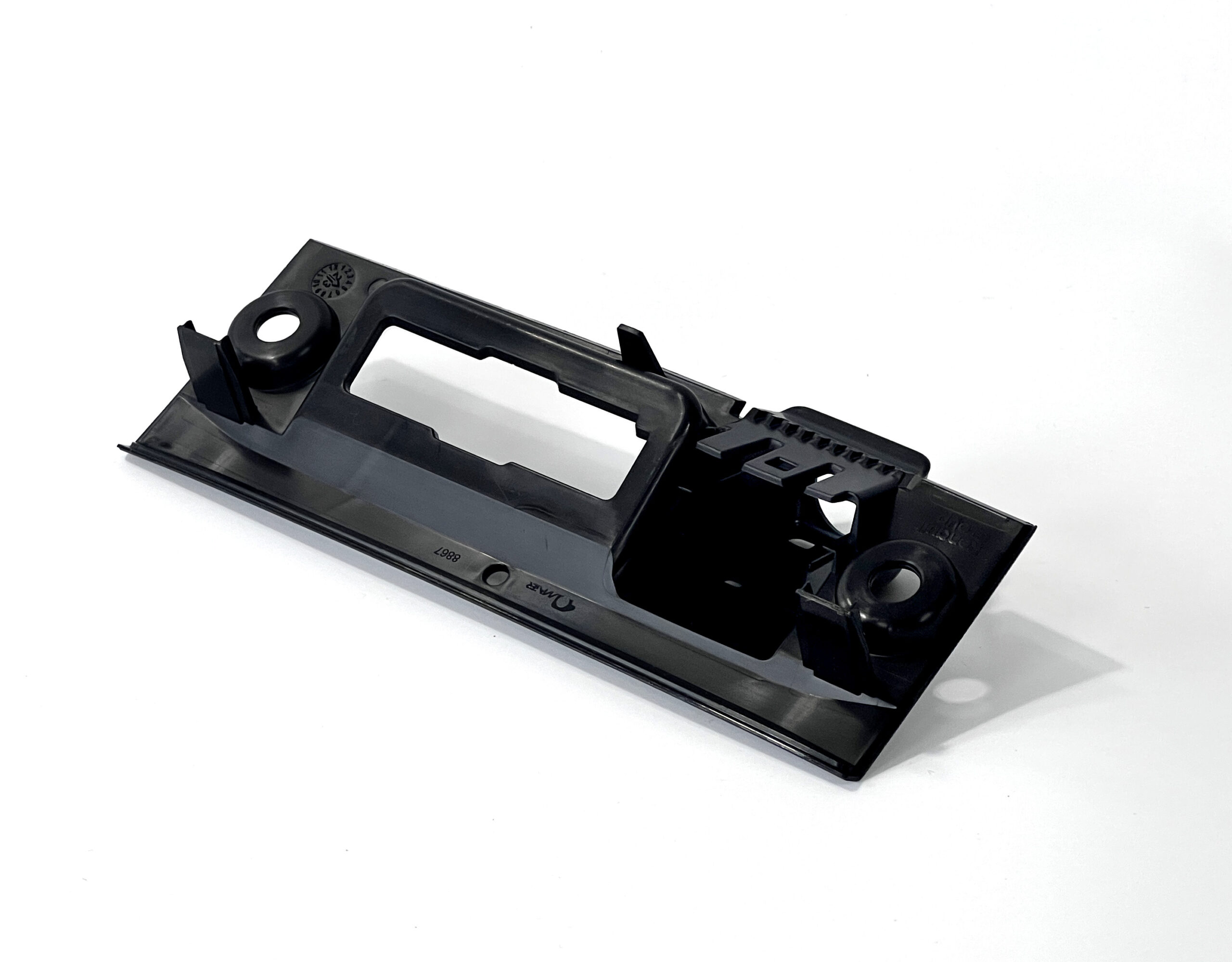
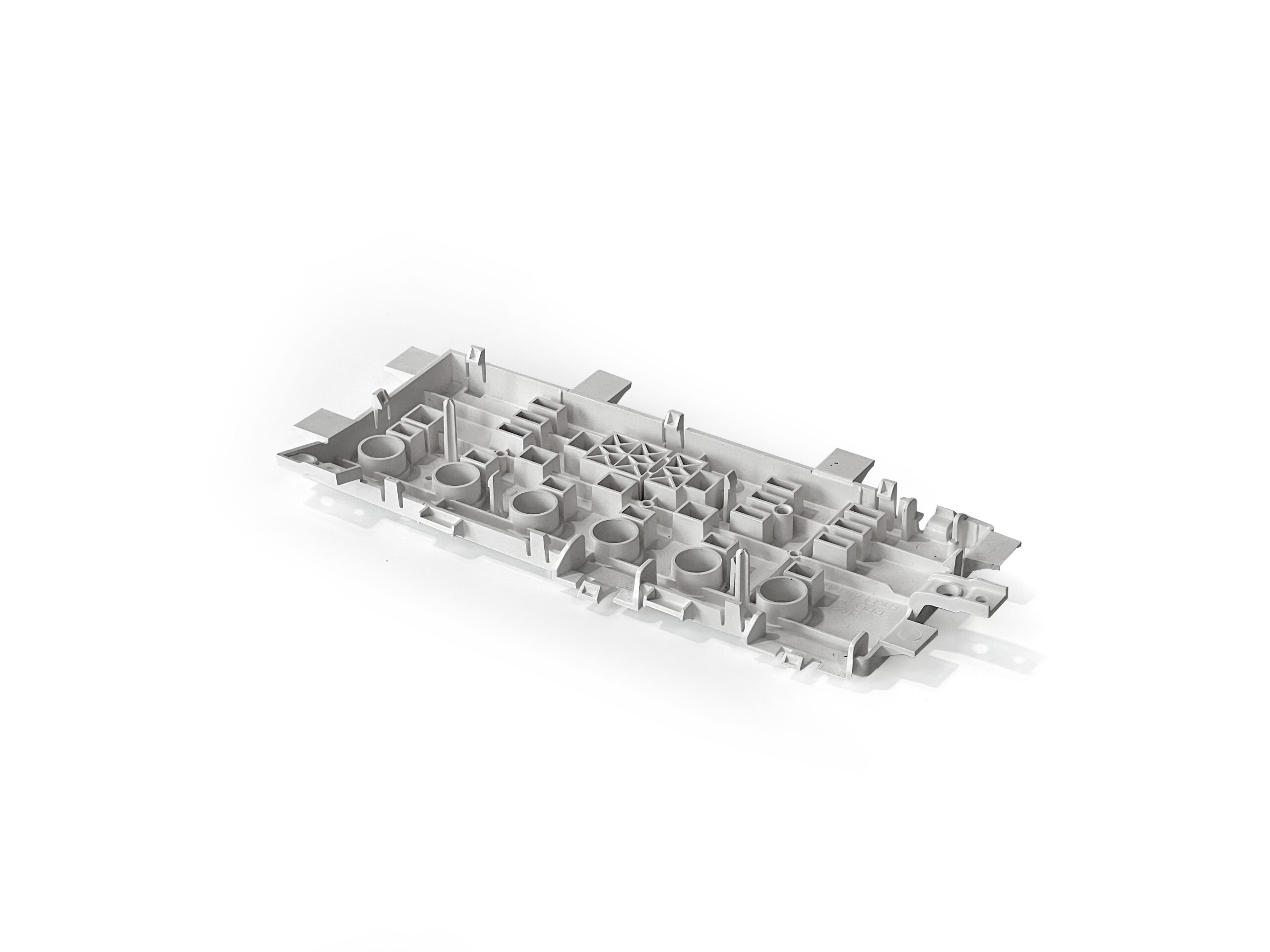
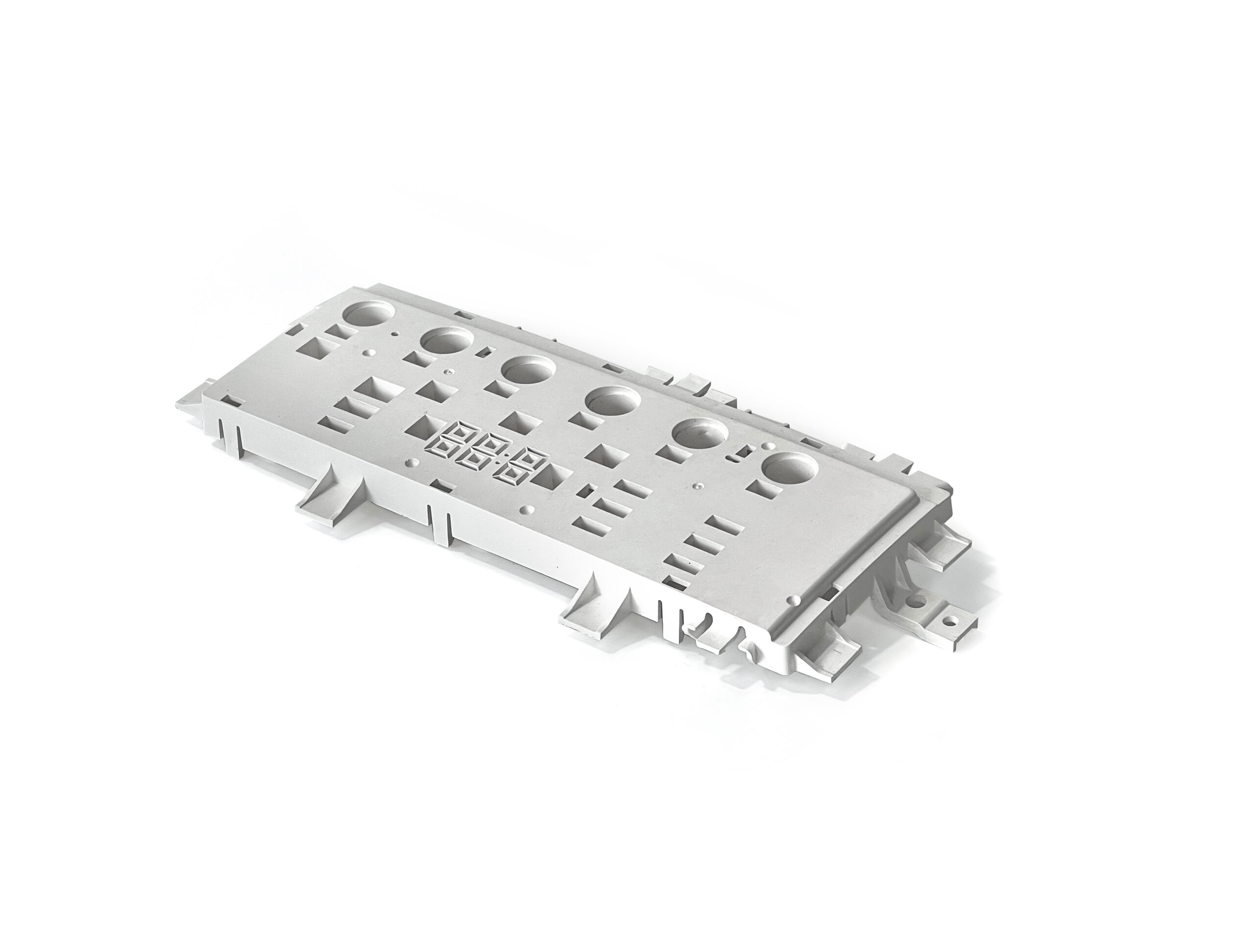
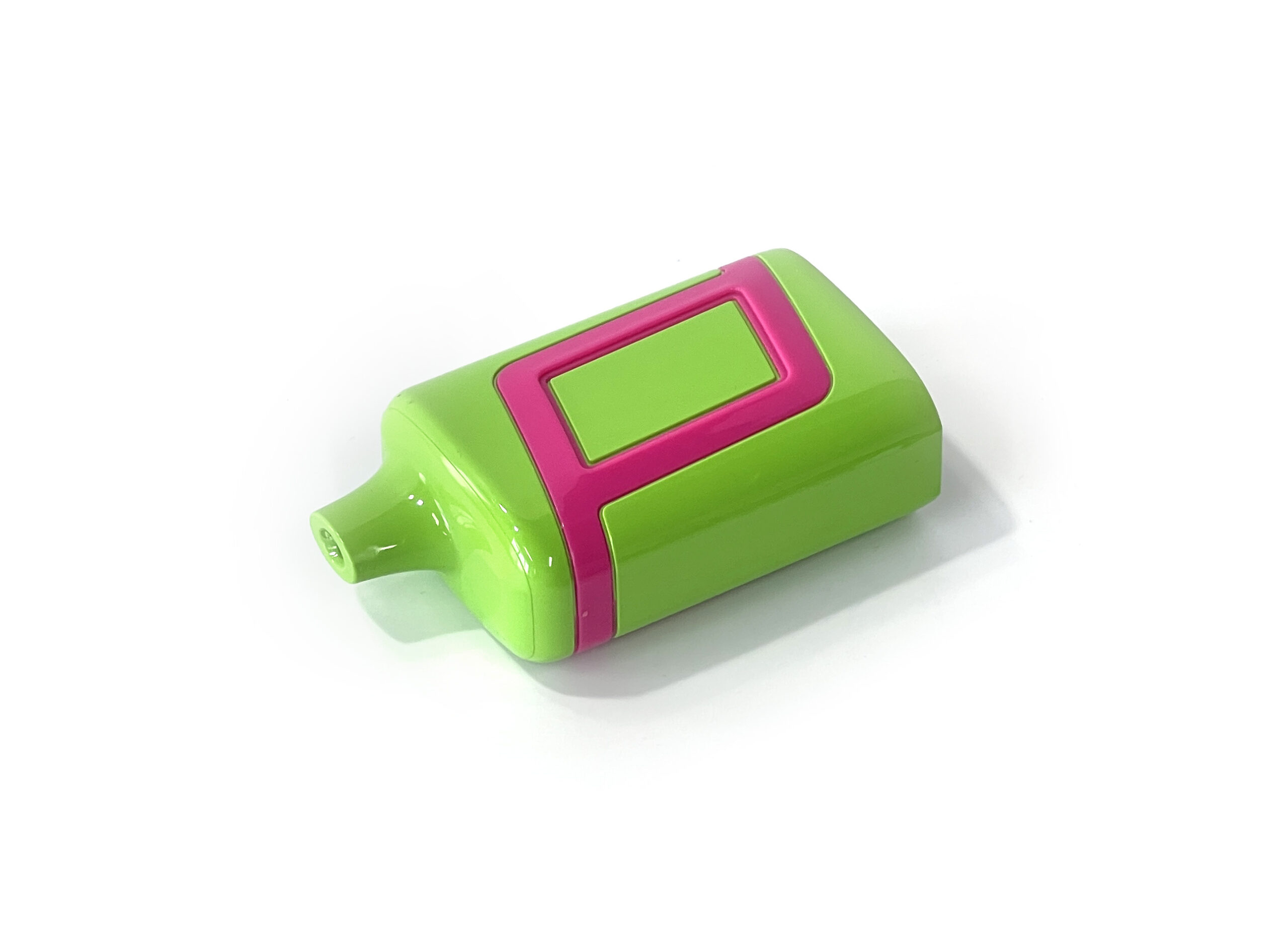
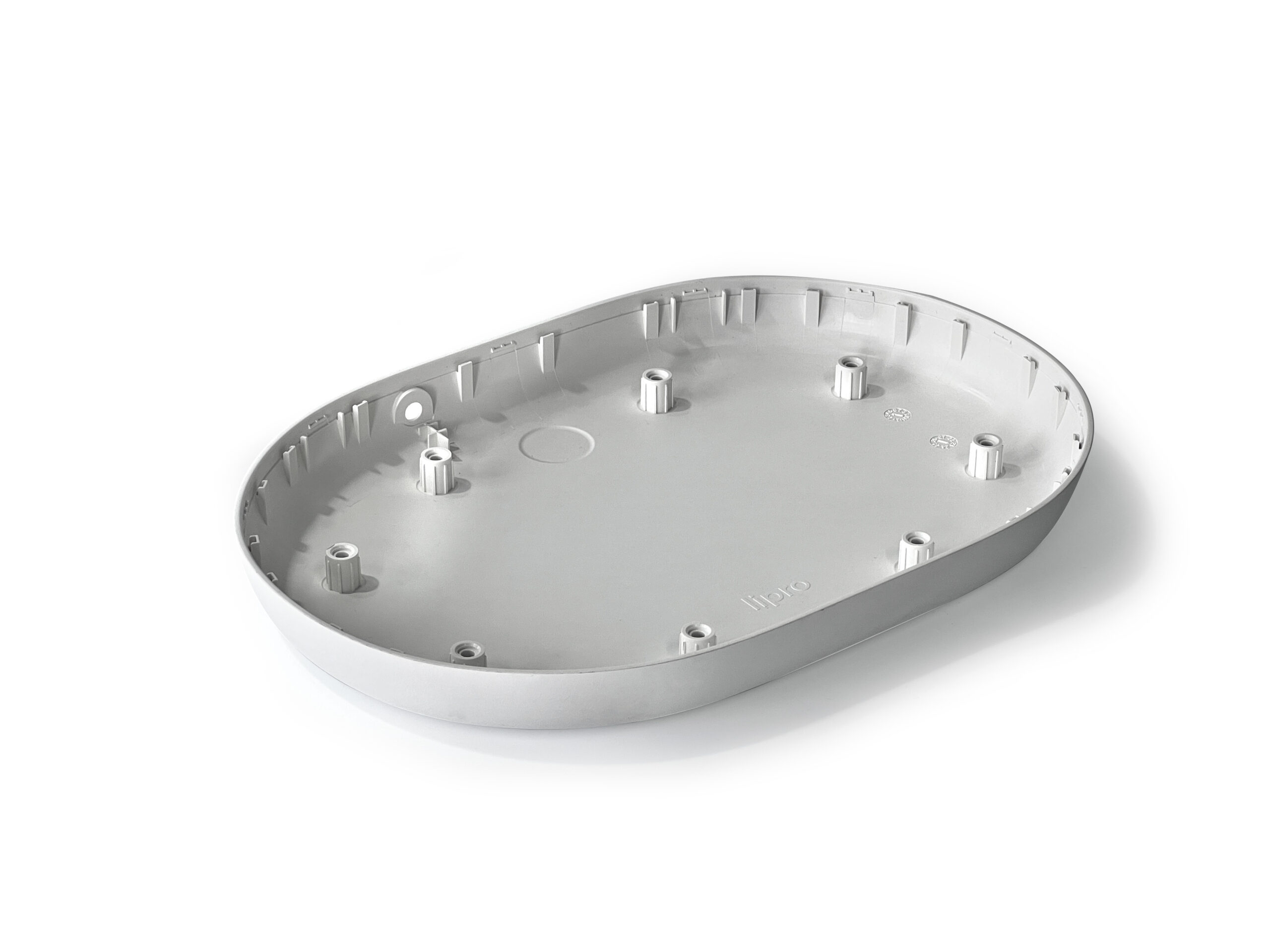
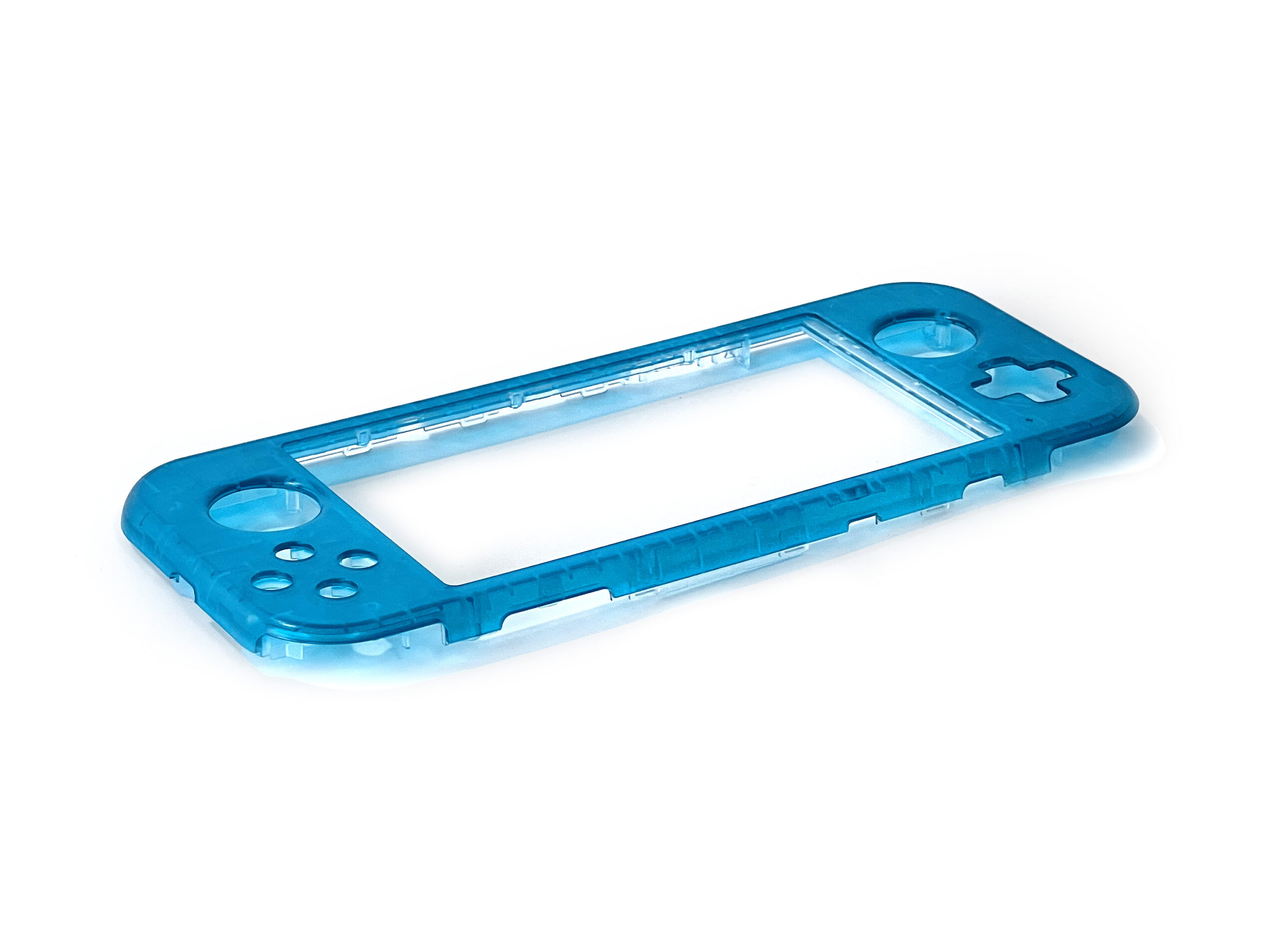
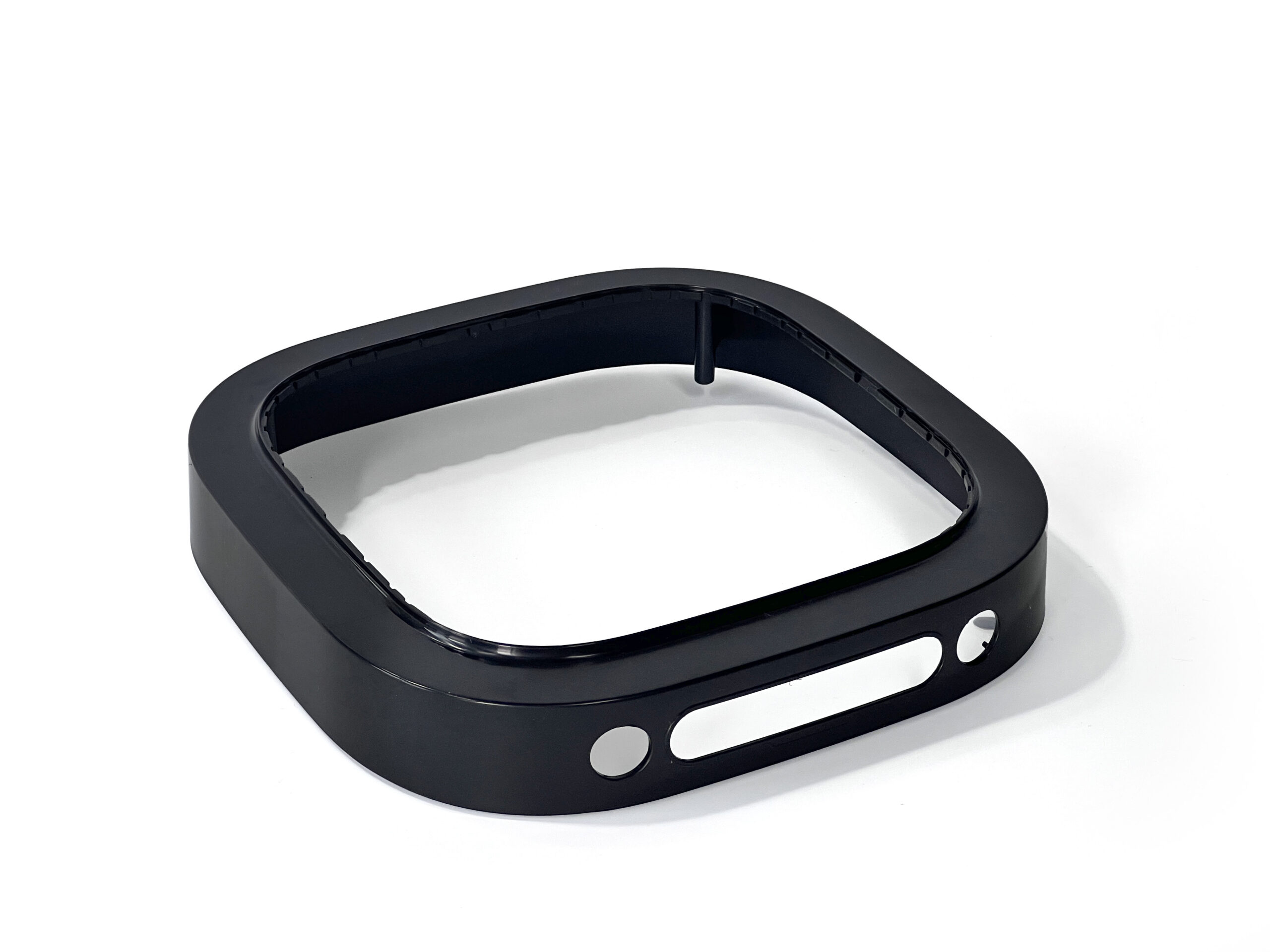
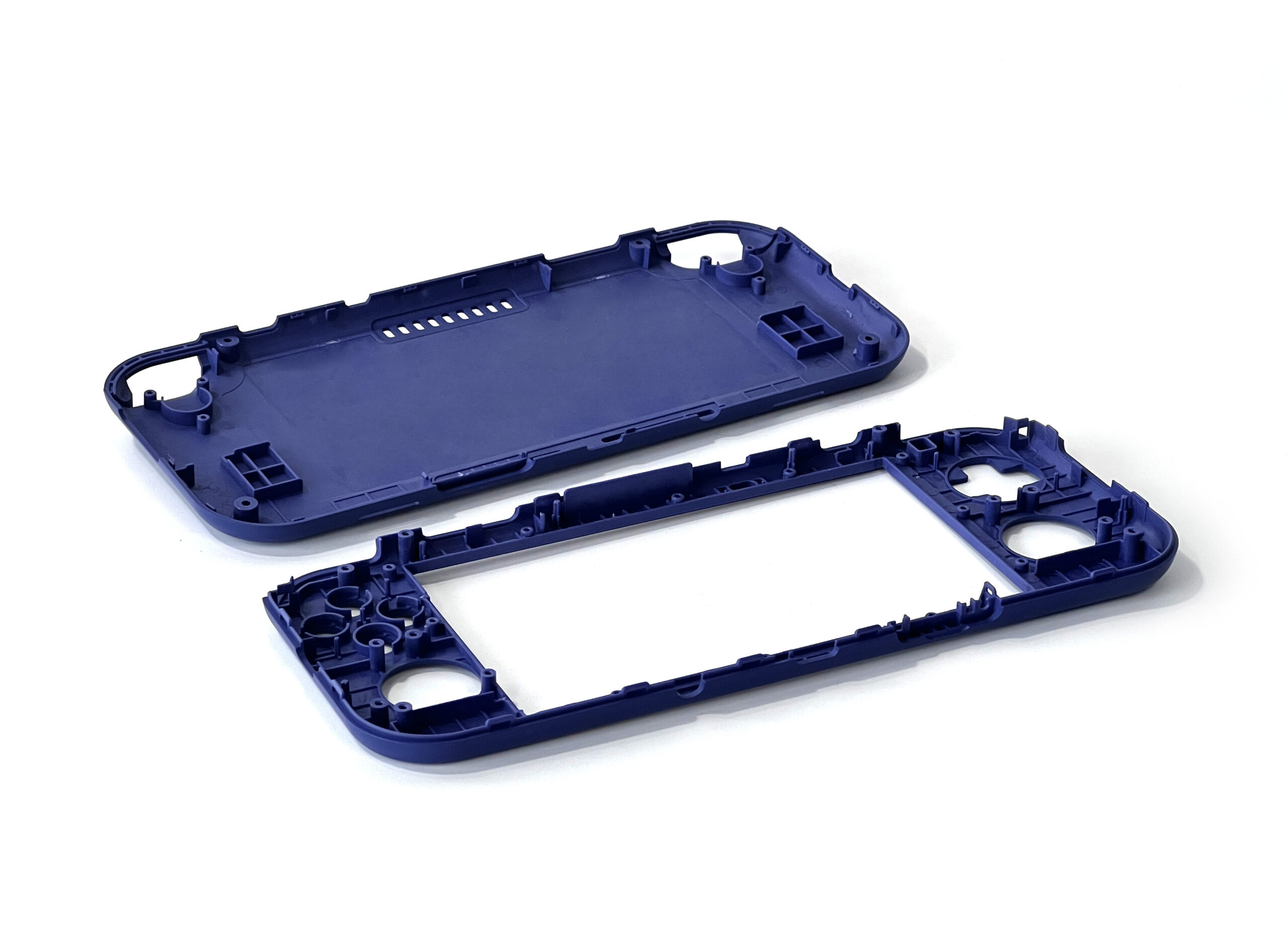
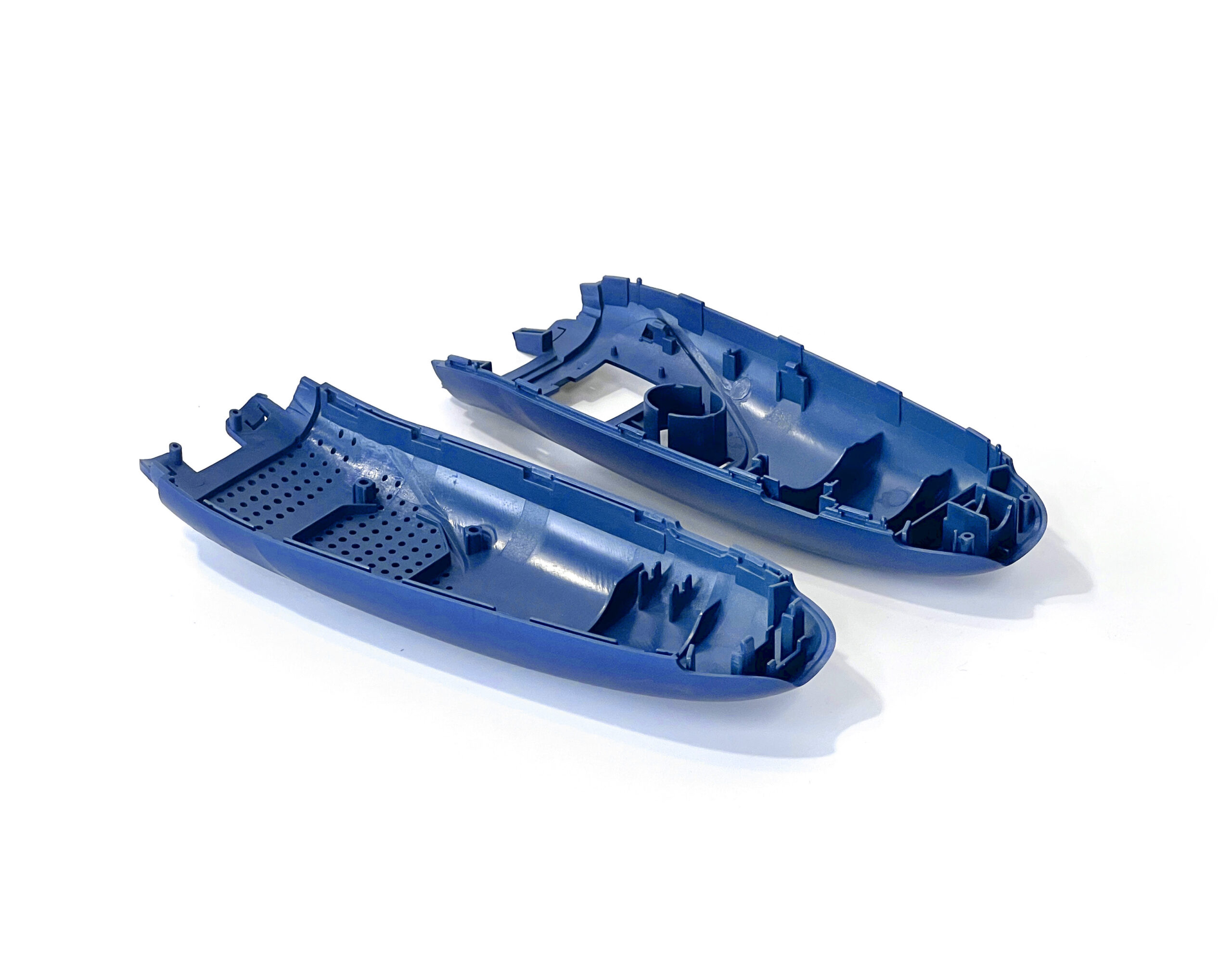
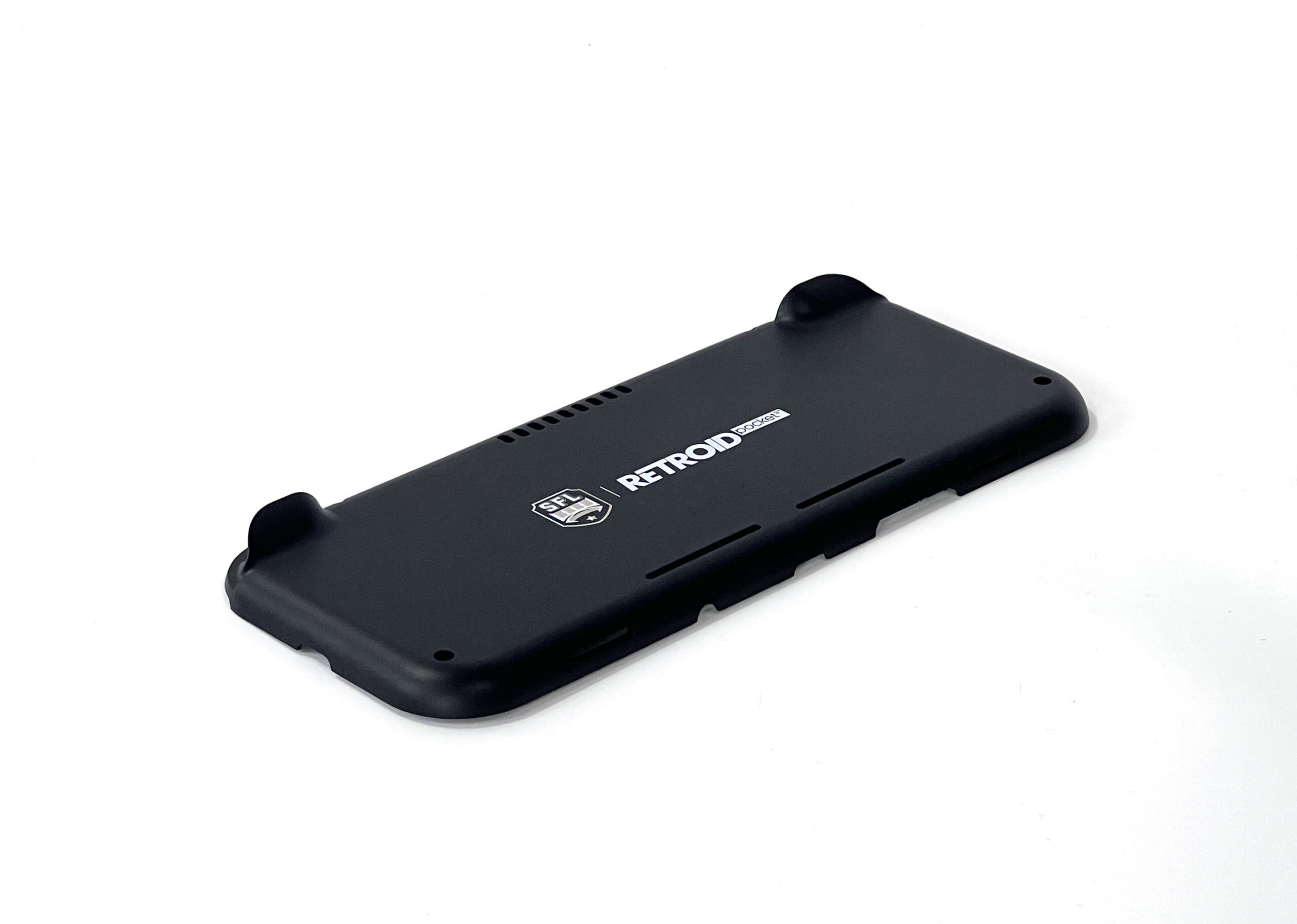
Rapid tooling making is a highly efficient and cost-effective technology that offers several advantages. It distinguishes by its short molding cycle, streamlined process, ease of implementation, low molding cost, high accuracy, and extended tooling lifespan, catering to functional requirements.
This technology is particularly well-suited for new product development and trial production, process and functional validation, and low-volume and diverse product manufacturing. CS Mold is a trusted rapid prototyping company, offering online rapid prototyping services. Leveraging our extensive expertise and tailored manufacturing capabilities, we are committed to expediting your product’s time-to-market.
Rapid tooling making is an advanced technology known for its exceptional efficiency and cost-effectiveness, offering several advantages. It stands out due to its short molding cycle, streamlined process, ease of implementation, low molding cost, high accuracy, extended tooling lifespan, catering to functional requirements. This technology proves especially suitable for new product development and trial production, as well as process and functional validation. Moreover, it excels in low-volume and diverse product manufacturing. With our vast expertise manufacturing capabilities and prototype machining services, we are dedicated to accelerating your product’s time-to-market.
Traditional manufacturing tooling involves complex and time-consuming processes like machining, casting, or injection molding, requiring significant time and cost investments. This makes them less suitable for rapid iterations or small production runs. Meanwhile, Rapid tooling uses 3D printing, CNC machining, and vacuum casting for quicker fabrication of tooling components. These methods are more flexible and resource-efficient than traditional techniques, suitable for prototyping, low-volume production, and bridge tooling.
In CS Mold, we generally use a shared mold base system to make rapid tooling. Therefore, the tooling cost is lower than the traditional manufacturing process. It is especially suitable for on-demand production and low-volume production.
At CS Mold, we are dedicated to utilizing only top-quality materials for rapid tooling, with a particular focus on steel, such as the renowned P20 steel. Steel is highly regarded for its exceptional properties, making it a popular and extensively employed material choice. With its solidity, durability, and superior quality, steel is well-suited for manufacturing wear-resistant and corrosion-resistant engineering-grade plastic molds. One of the key advantages of utilizing steel as a tooling material is its ability to enhance the glossy surface finish, resulting in an aesthetically appealing end product.
- Generate a 3D CAD model of the desired mold or tool.
- Transmit the CAD file to a machine that directly produces the physical mold or tool required for prototyping.
- The resulting mold or tool can be immediately utilized to manufacture prototypes, usually in a small quantity.
- Develop a 3D CAD model of the master mold or tool.
- Transfer the CAD file to a machine that constructs a durable master mold or tool, known as a pattern.
- Utilize the master pattern to generate additional molds or tools, employing diverse materials with varying properties.
A single master pattern has the capability to generate numerous tools or molds, accommodating both large and small production quantities. Consequently, this enables the production of a significantly larger number of prototypes.
- Faster production and shorter delivery times
- Multiple prototypes can be produced using a single mold or tool
- Allow for rapid production of multiple molds during design changes
- The main model is very durable and rarely damaged during the prototype production process、
- Hard or soft tools can be made according to customer needs. Hard tools are an ideal choice for complex designs, while soft tools can be used for simple designs or cost-effective prototype testing.
- Perfect for trying different materials
- May not be suitable for highly complex designs or materials that require durable molds or tools to produce complex details
Creating multiple molds for each new design iteration may result in higher product development costs
- Long production time and high cost
- If there are significant changes in the design during the prototype stage, this is not always a good choice
- Higher quality materials may be needed to make sturdy master molds
· Can produce multiple prototypes from a single mold or tool
·Allowing to make multiple molds quickly as your design changes
· Can make either hard or soft tools based on customer’s needs. Hard tools are ideal for complex designs,while soft tools can be used for simple designs or cost-effective prototype testing.
· Ideal for experimenting with different materials
· Could result in higher product development costs if create multiple moldsfor each new design iteration
· Not always a good option if the design will change significantly during the prototyping stage
· May require higher quality materials to make a robust master pattern
Opt for direct rapid tooling if your main goal is to swiftly assess a design concept’s feasibility. This method offers flexibility, allowing you to experiment with various dimensions and quickly iterate on your design.
Conversely, indirect rapid tooling is ideal for product designers ready to conduct extensive prototype testing. It facilitates thorough evaluation of various materials, finishes, and other characteristics crucial to the final product. Indirect rapid tooling is the preferred option for product designers that are ready to thoroughly test their prototypes and select materials or finishes for their end products.
By considering your specific needs and objectives, you can determine whether direct or indirect rapid tooling is the preferred option for your particular design and development stage. Or contact us to discuss.
Advantage of Rapid Tooling:
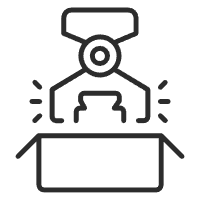
Fast Delivery
At CS Mold, our extensive inventory of shared mold bases and precision machines enables us to produce rapid parts with short lead times. We take pride in our ability to ship products to any location worldwide.
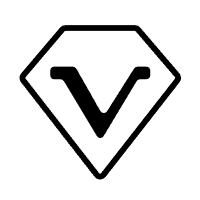
Best Quality and Competitive Price:
With our extensive tooling capabilities and a skilled team, we prioritize delivering high-quality parts while offering competitive pricing. Our expertise allows us to find cost-saving solutions tailored to your project. Additionally, our shared mold base system helps reduce tooling costs by 30-50% compared to traditional production tooling.

Multiple Material Options:
The rapid tooling process offers a wide range of material options. Any material available for injection molding can be utilized in rapid tooling. If you are uncertain about the most suitable material for your project, our engineers will assist you in selecting the right material based on your part's requirements.
How Make Rapid Tooling in CS Mold:
- Provide DfM within 36 hours after the customer confirms the order.
- Mold design and cutting of main steel shall be carried out simultaneously after approval by DfM.
- CNC machining of cavities and core inserts; The matching MUD will be checked and sent to the tooling workshop.
- Auxiliary tooling components are processed and sent to the tooling assembly workshop.
- Tooling assembly and polishing.
- The tooling will be sent to the injection molding workshop for testing after being inspected by the master.
- The initial sample after inspection by the engineer and sent to the. measurements Inspection
Rapid tooling making finds applications in diverse industries. Our team of experts specializes in delivering production solutions that expedite your product’s time to market.
WHY CHOOSE US
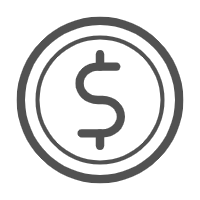
INSTANT QUOTING
Timely reply and provide the quote within 24 hours
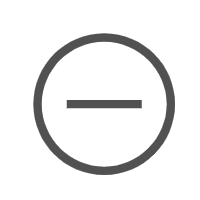
NO MOQ REQUIRED
Hord does not have minimum order quantity
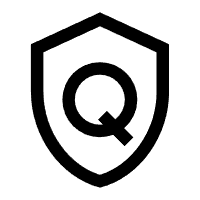
HIGH QUALITY
ISO 9001 & IATF 16949 certificated and inspect every step
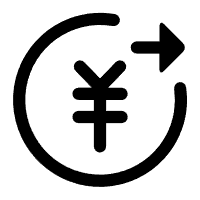
COST-EFFICIENT
+30% cost lower than western competitors
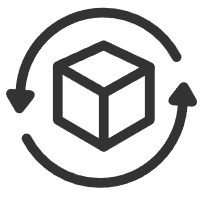
QUICK TUAROUND
Parts make in 7 days and delivery on time
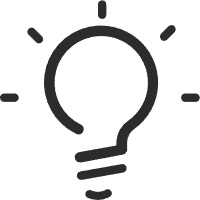
DFM ANALYSIS
Once receiving the inquiry, we will provide you with a preliminary DFM report
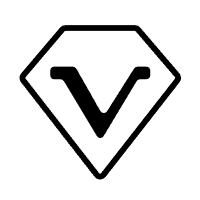
PROFESSIONAL SERVICES
More than 20 years of rapid tooling making
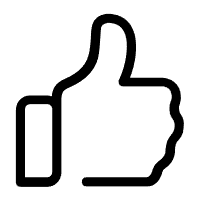
GOOD RAPUTATION FROM CUSTOMERS
Customers are satisfied with our services, products quality and delivery time.
OUR ADVANTAGE
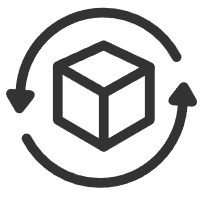
QUICK TUAROUND
Parts make in 5 days and delivery on time
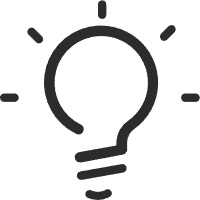
DFM ANALYSIS
Once receiving the inquiry, we will provide you with a preliminary DFM report
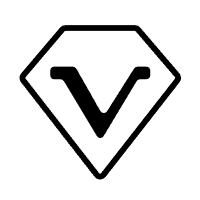
PROFESSIONAL SERVICES
More than 20 years of rapid tooling making
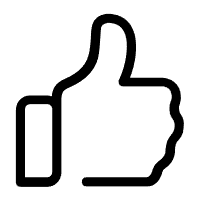
GOOD RAPUTATION FROM CUSTOMERS
Customers are satisfied with our services, products quality and delivery time.
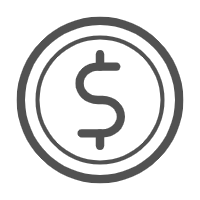
INSTANT QUOTING
Timely reply and provide the quote within 12 hours
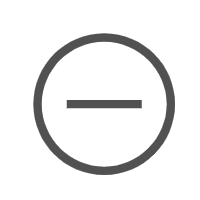
NO MOQ REQUIRED
CS Mold does not have minimum order quantity
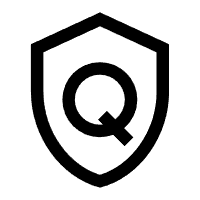
HIGH QUALITY
ISO 9001 & IATF 16949 certificated and inspect every step
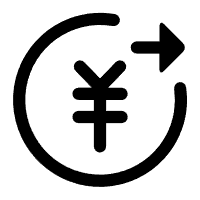
COST-EFFICIENT
+30% cost lower than western competitors
Materials commonly used for rapid tooling include aluminum, epoxy resins, and silicone. These materials offer good thermal and mechanical properties, making them suitable for producing molds for a range of materials, including plastics and some metals.
The lead time for rapid tooling can vary depending on factors such as the complexity of the tooling, the chosen rapid tooling technique, and the availability of materials. Generally, rapid tooling can be completed in a matter of days to a few weeks, offering significant time savings compared to traditional tooling methods.
Rapid tooling is typically more suitable for low to medium production volumes. While it can be used for limited high-volume production, traditional tooling methods may be more cost-effective and durable in such cases.
Rapid tooling has applications across various industries, including automotive, aerospace, consumer electronics, medical devices, and more. It is particularly useful in industries where fast prototyping, design validation, and short production runs are required.
