Plastic Injection Molding Service
High Quality Plastic Parts
Professional DFM Analysis Production parts as fast as 7-14 days
Dozens of materials and finishes are available
Cases of Plastic Injection Molding
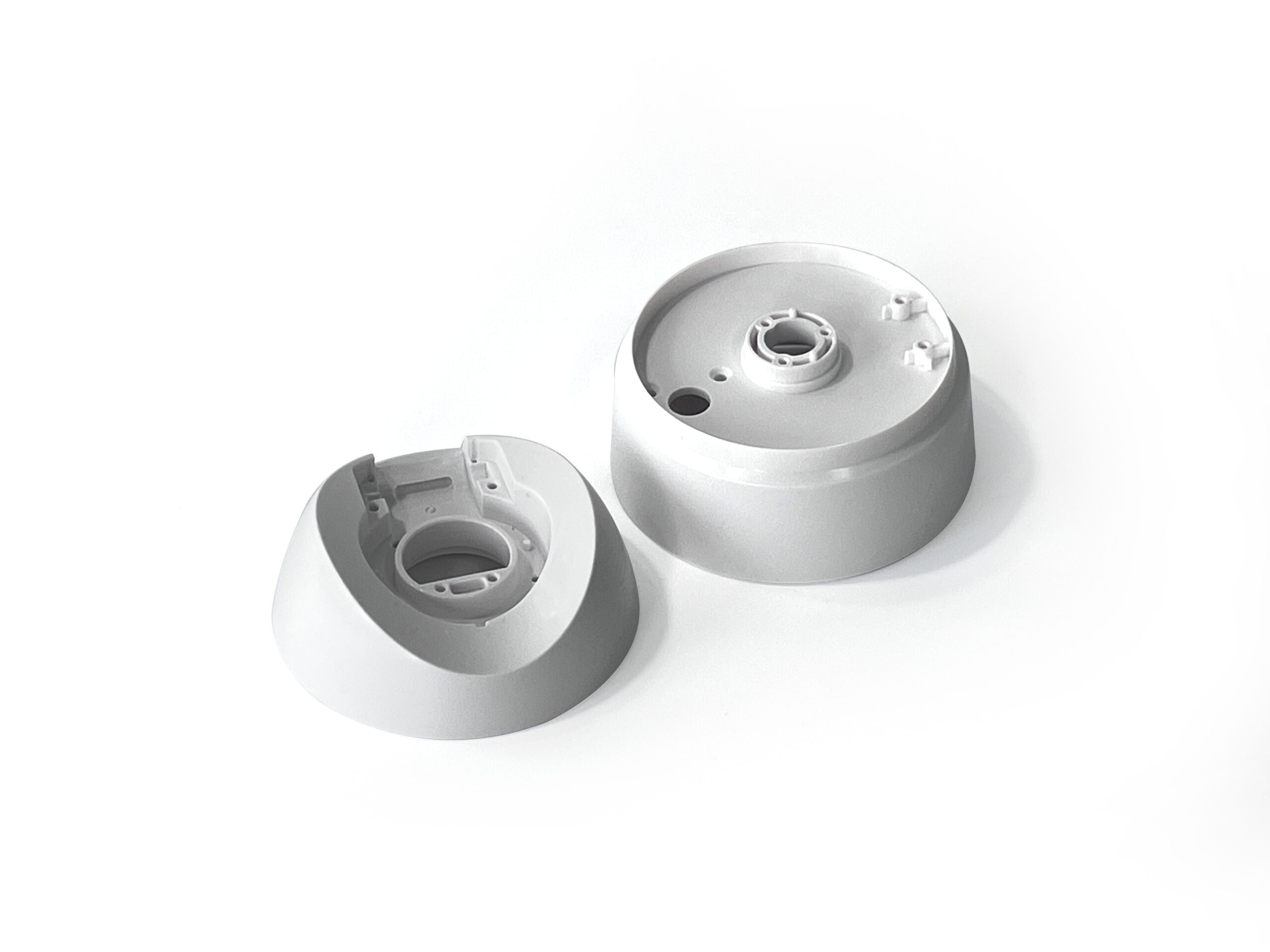
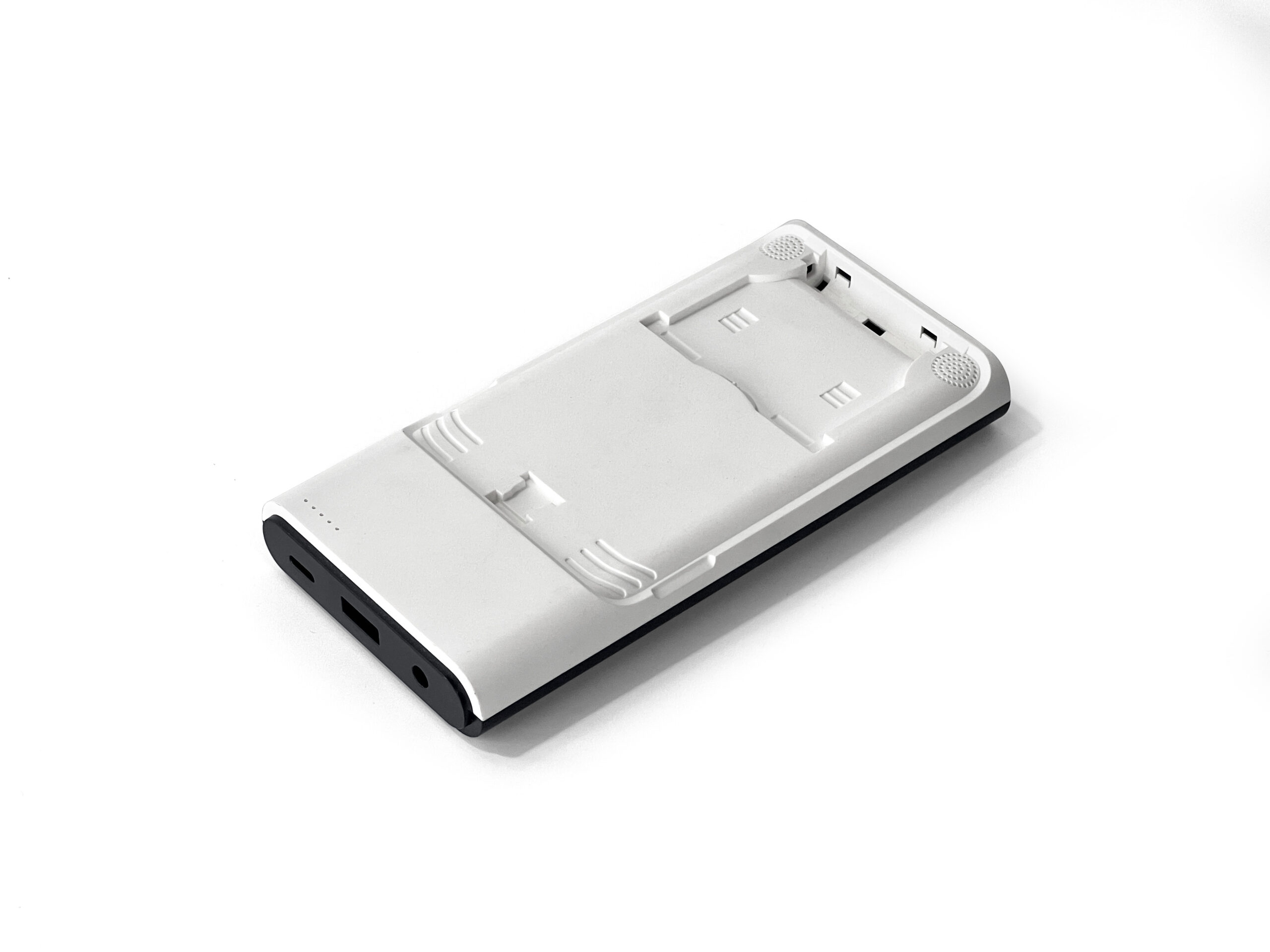
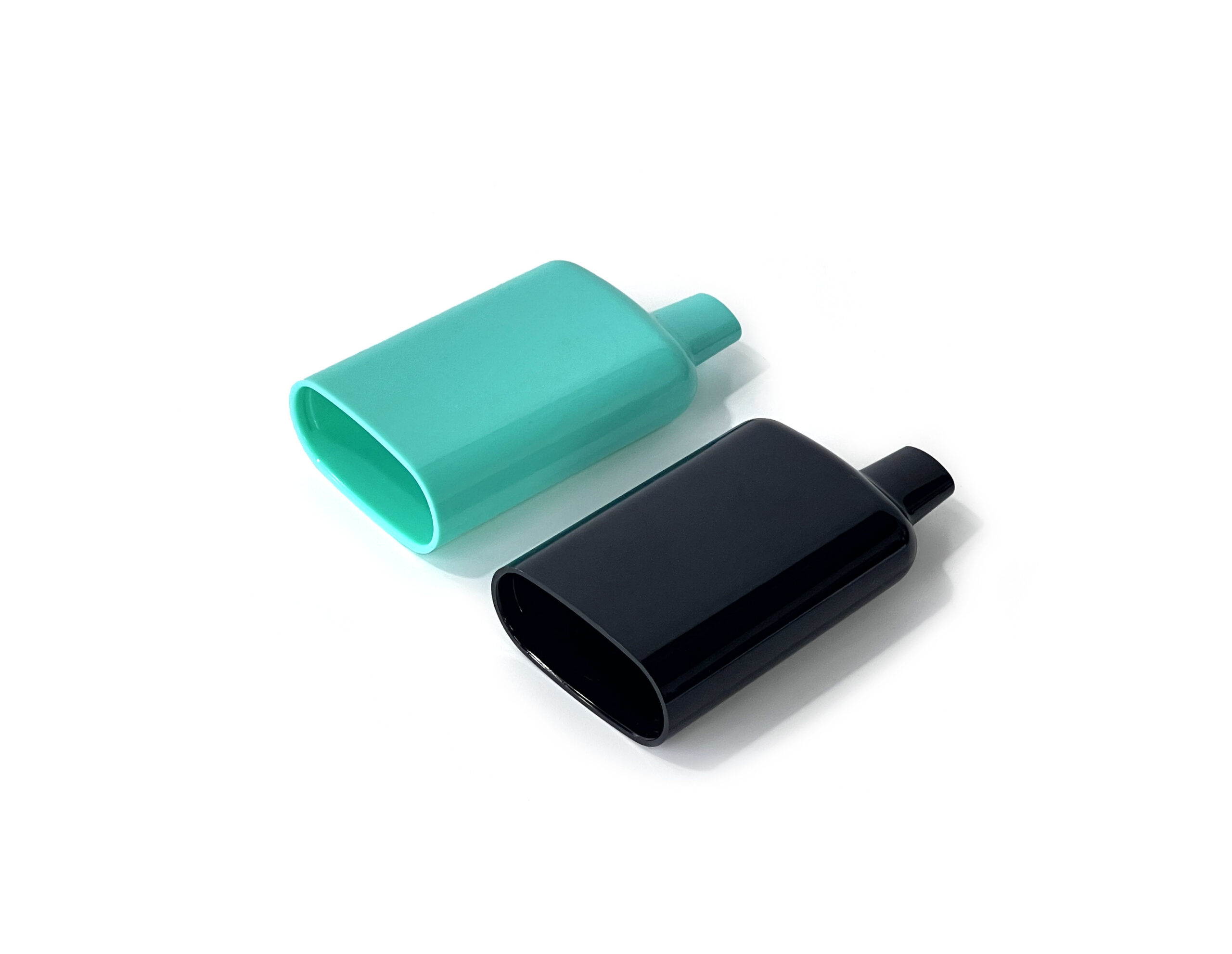
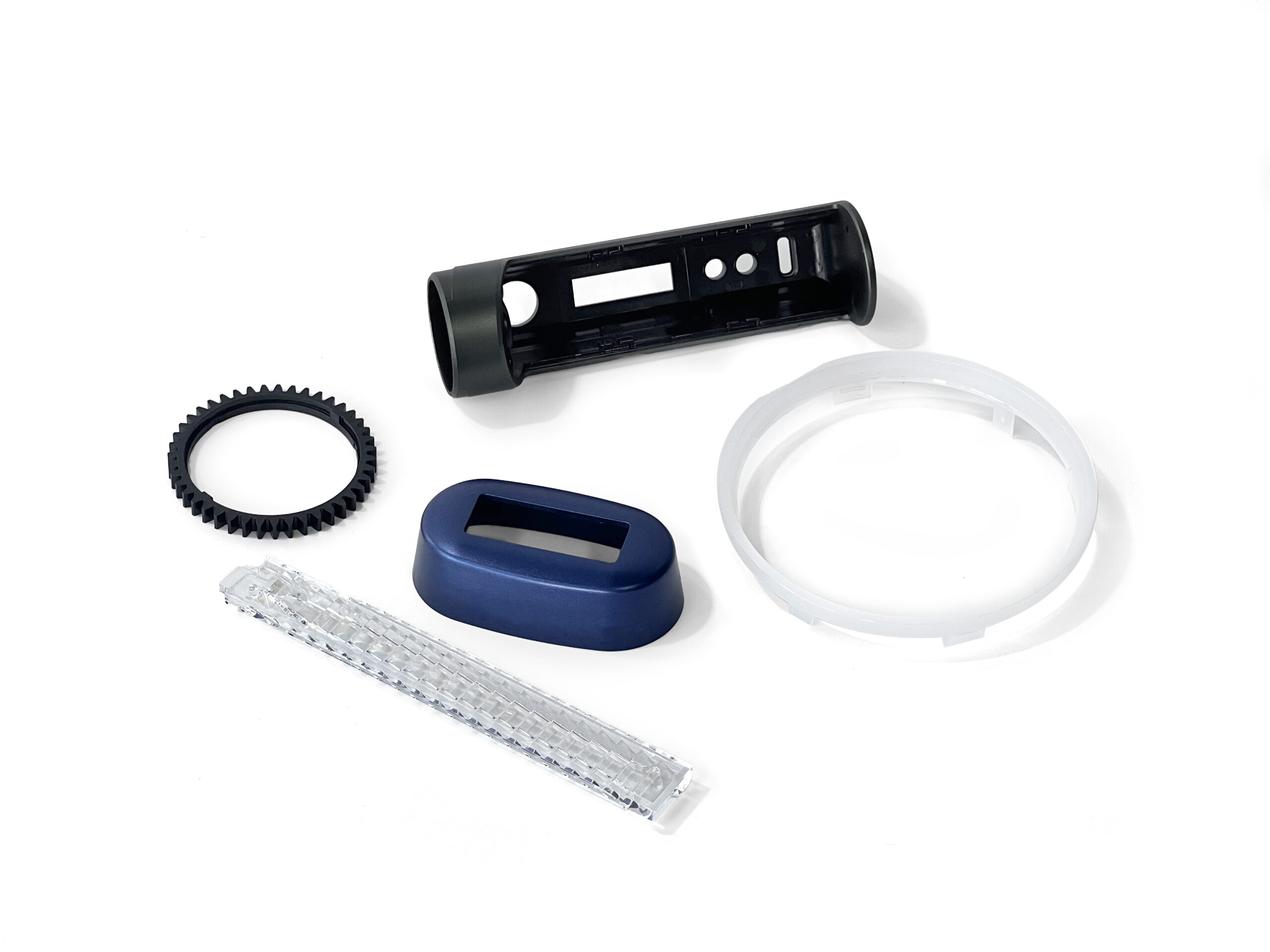
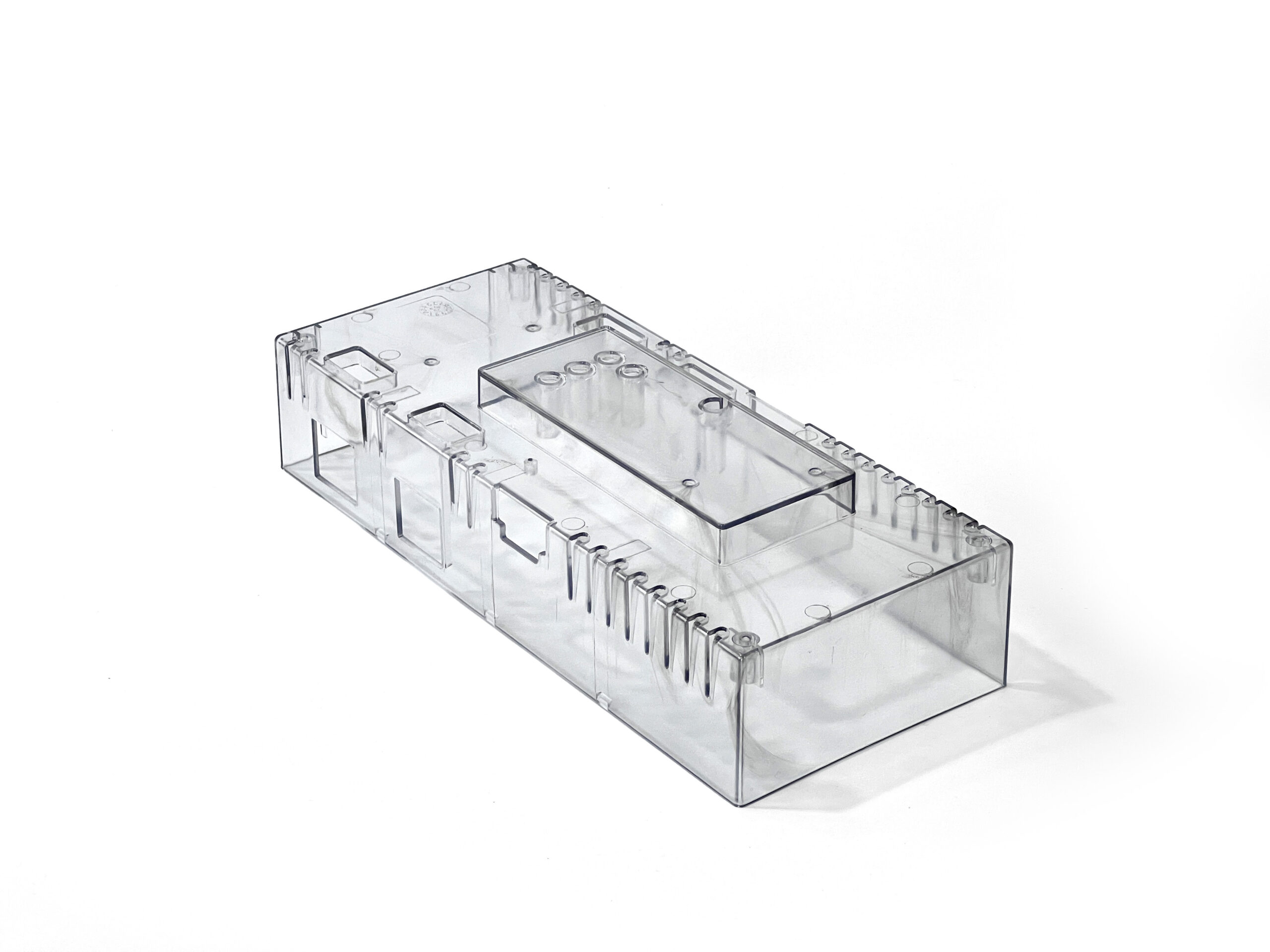
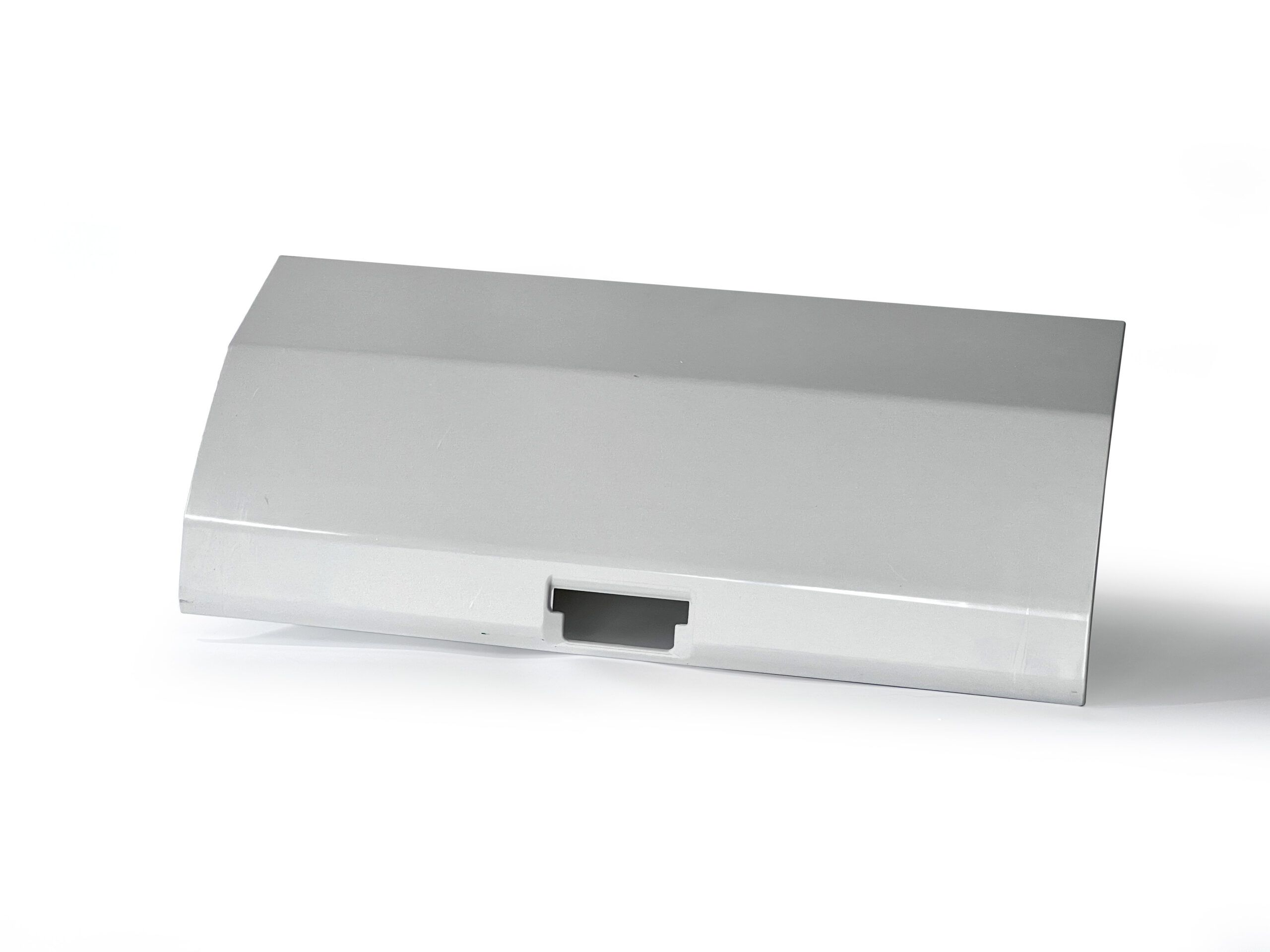
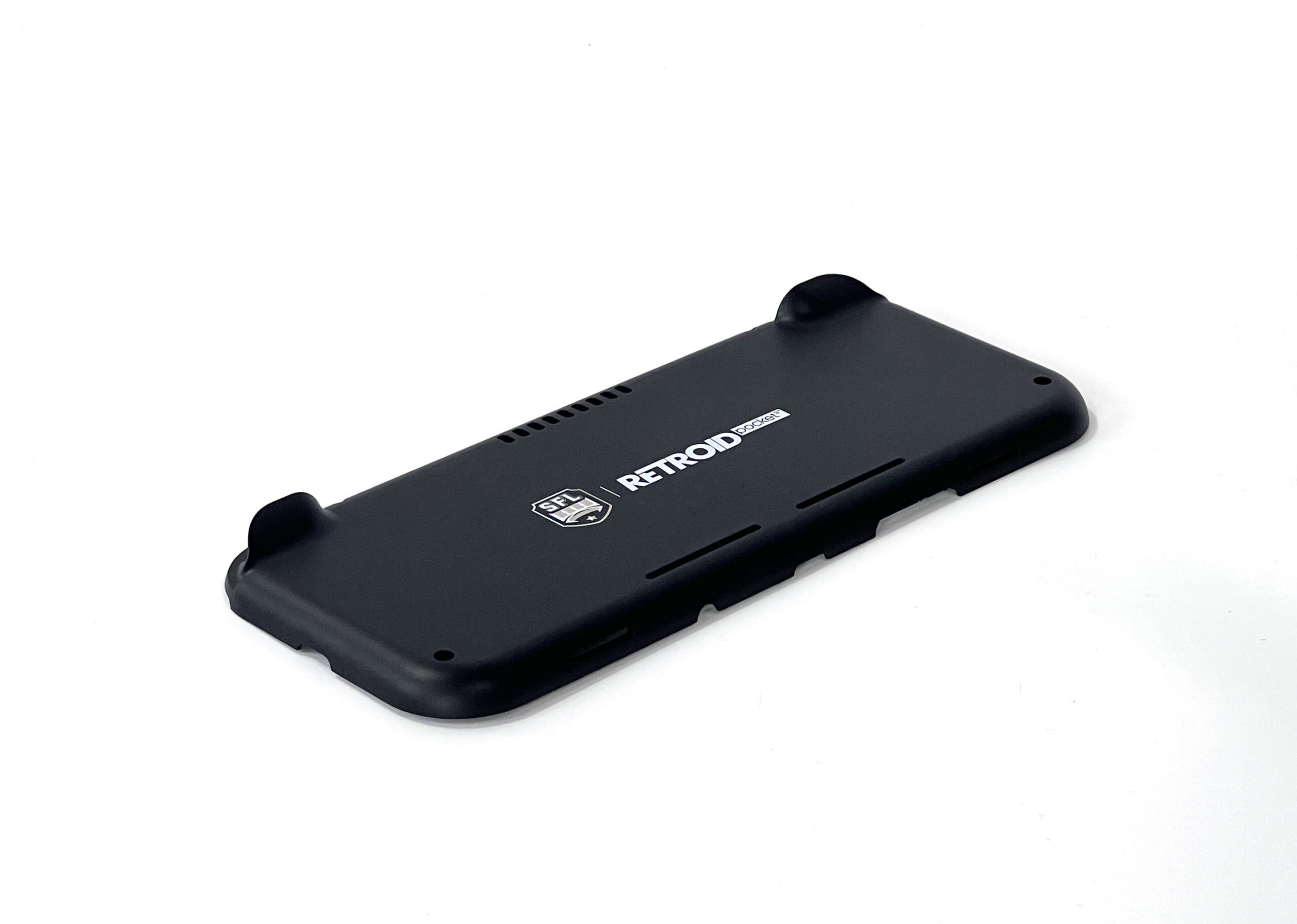
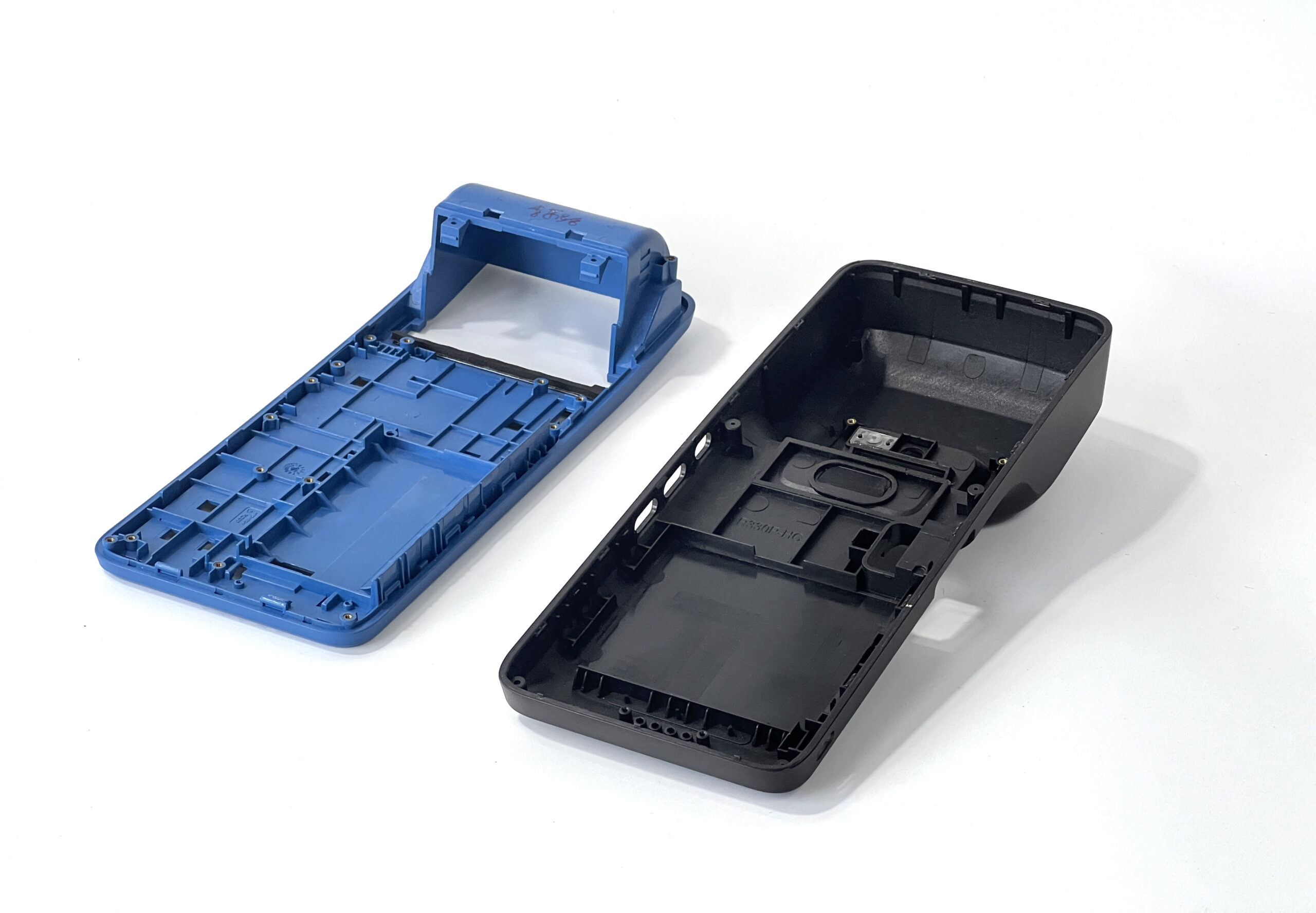
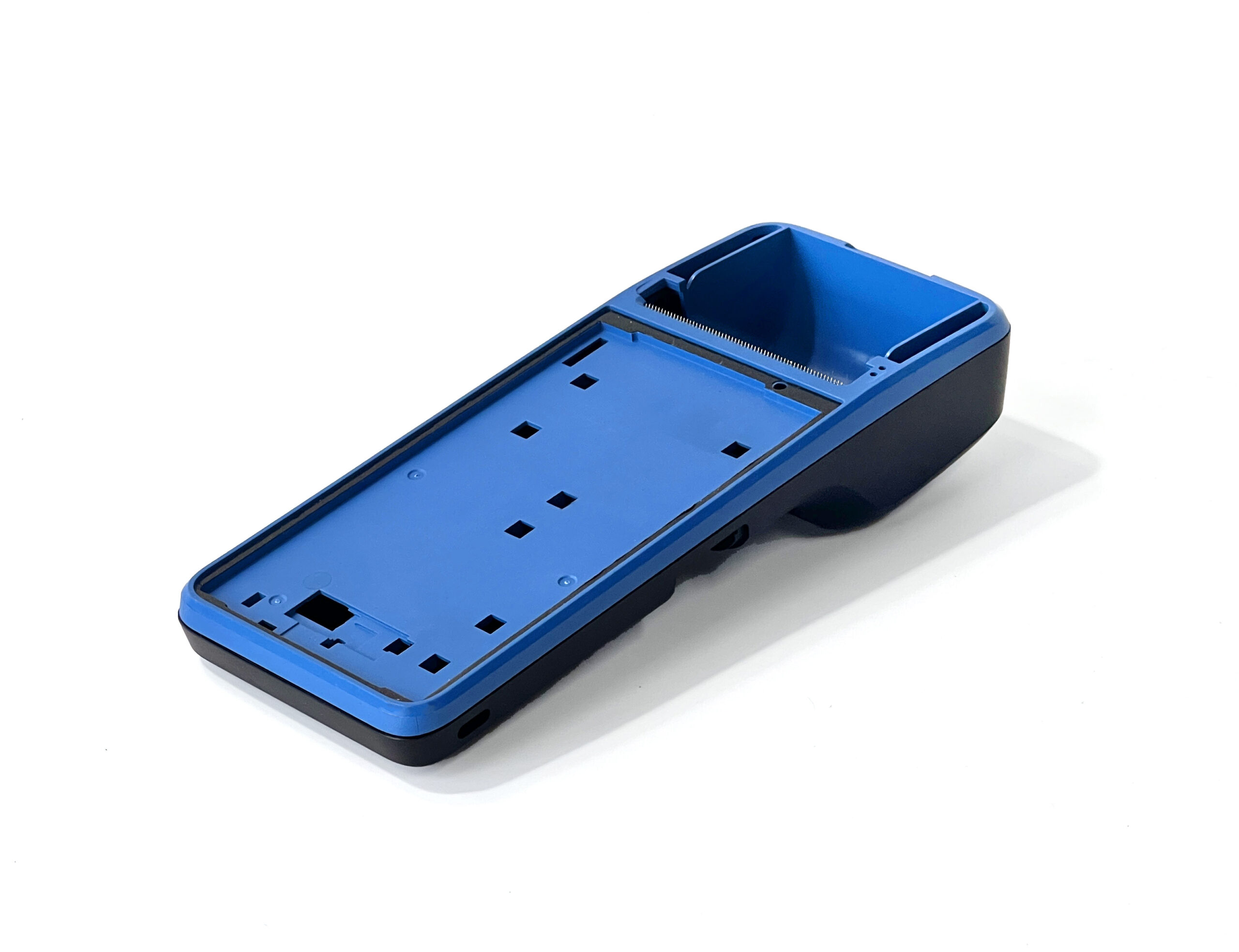
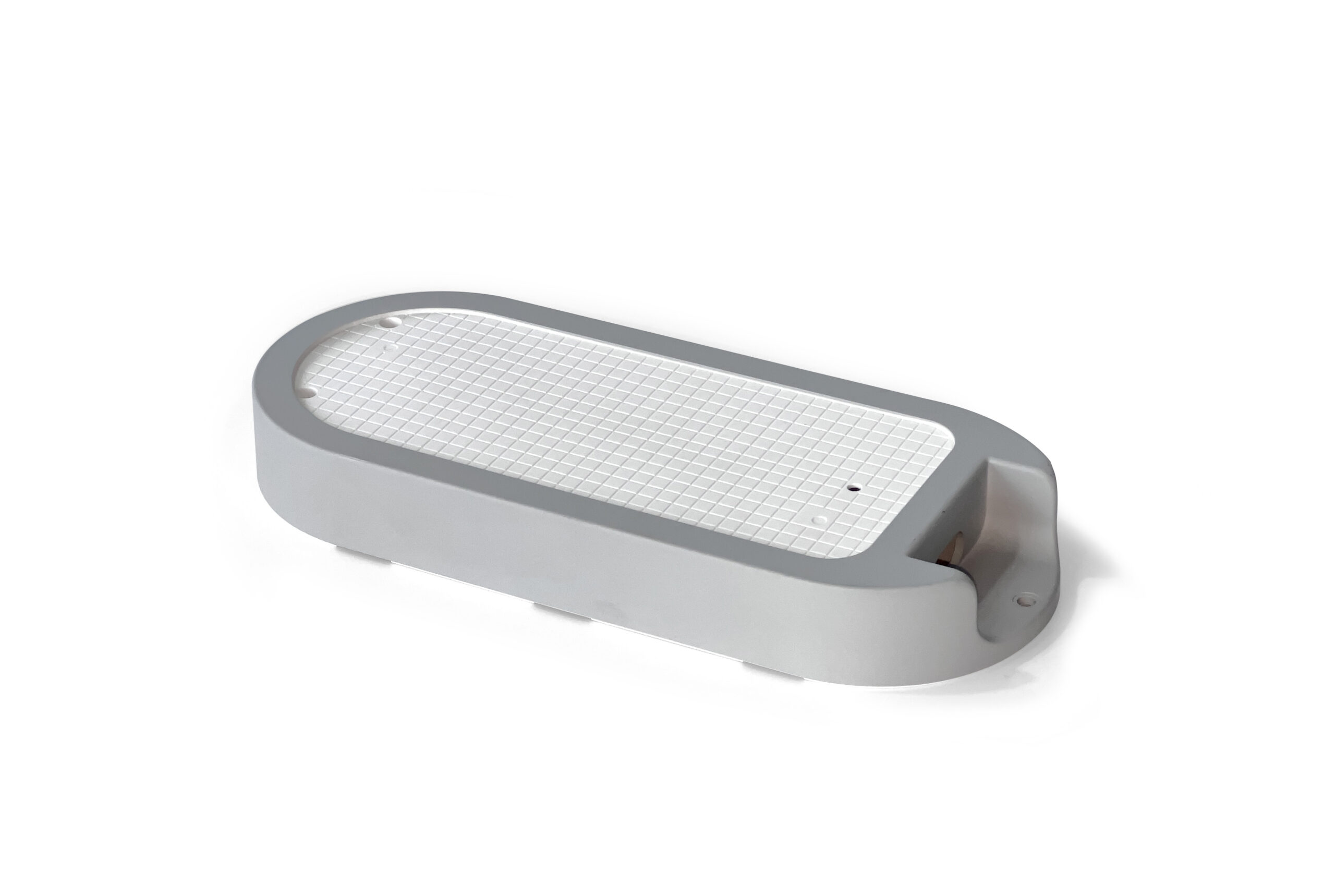
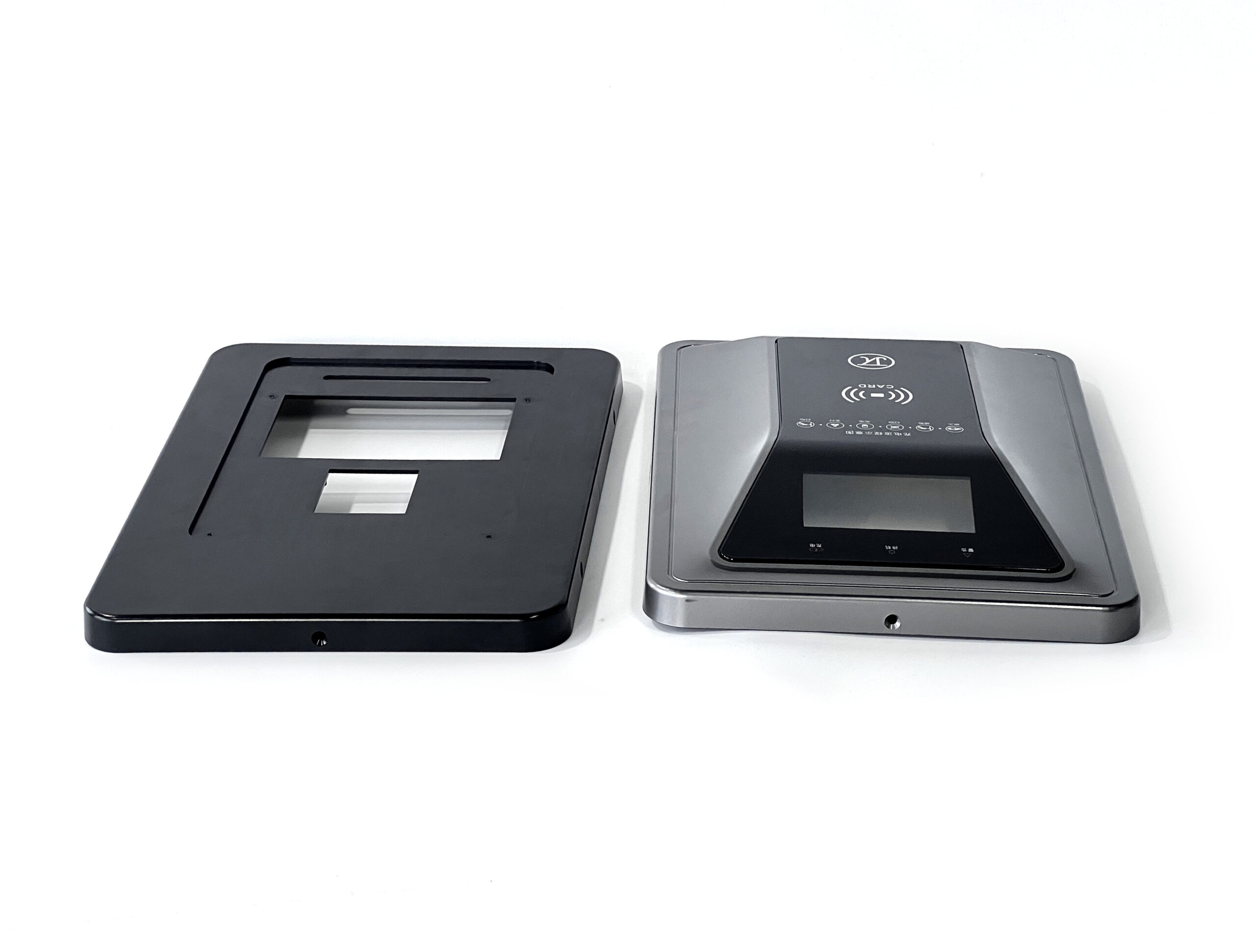
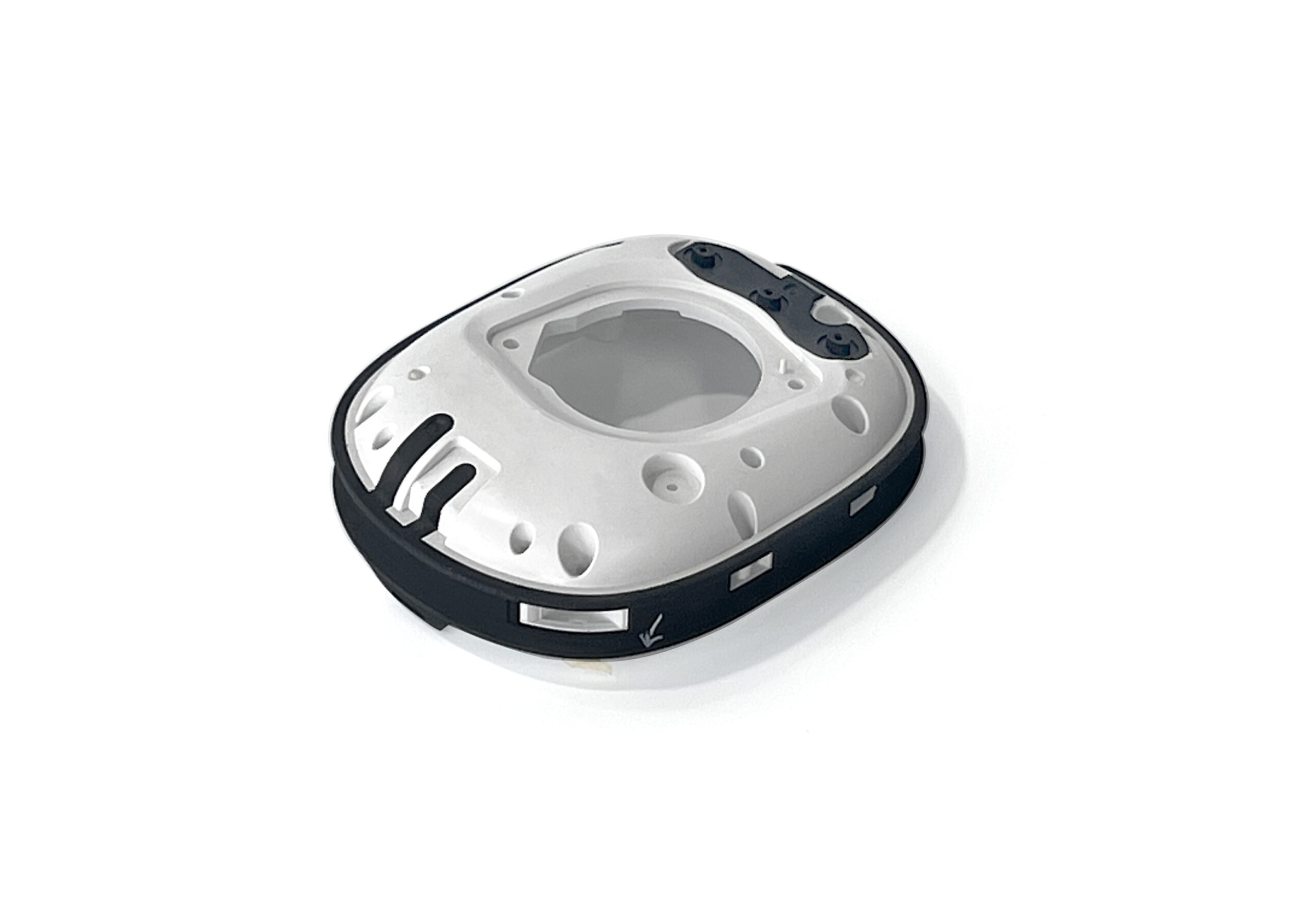
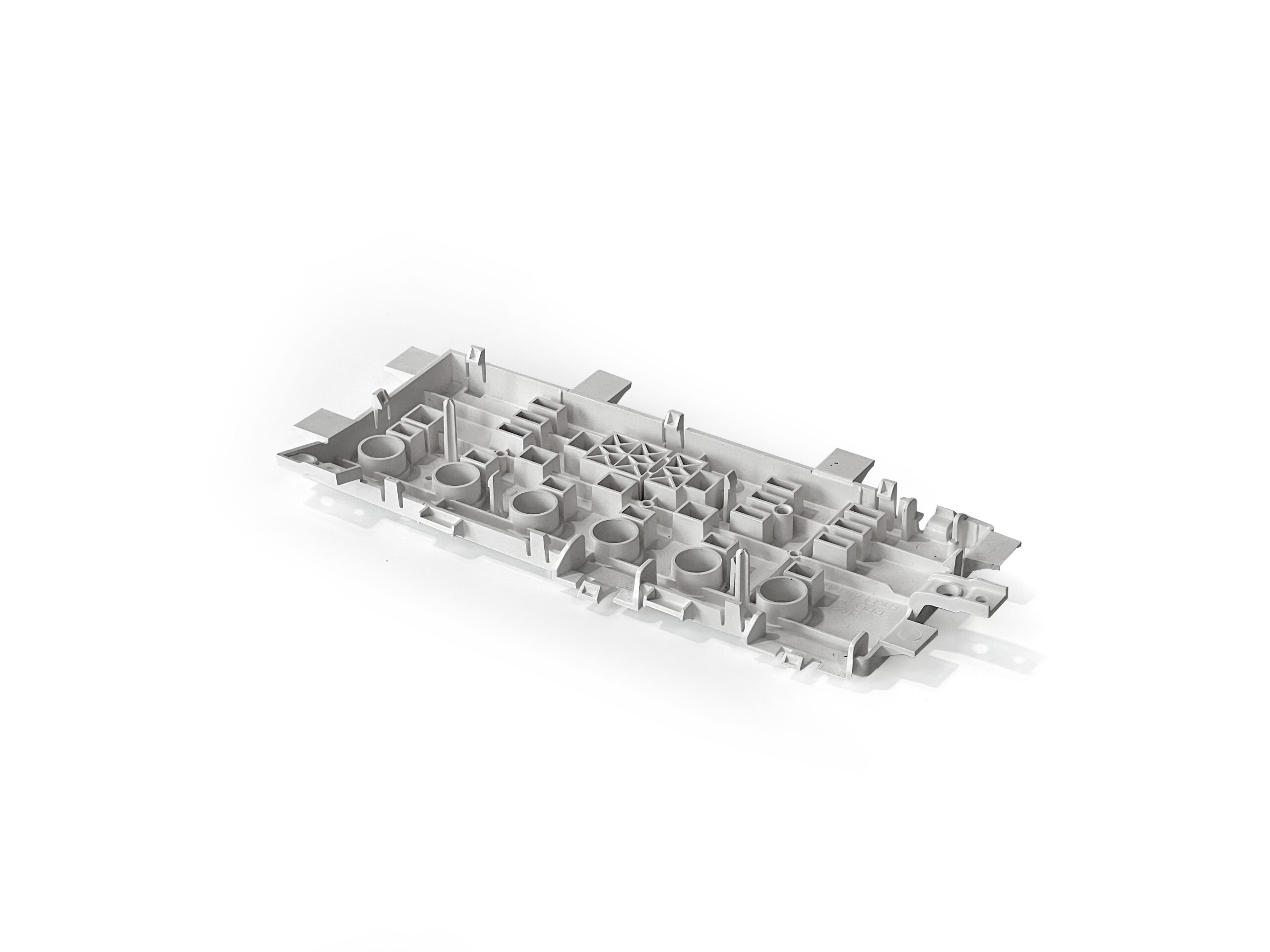
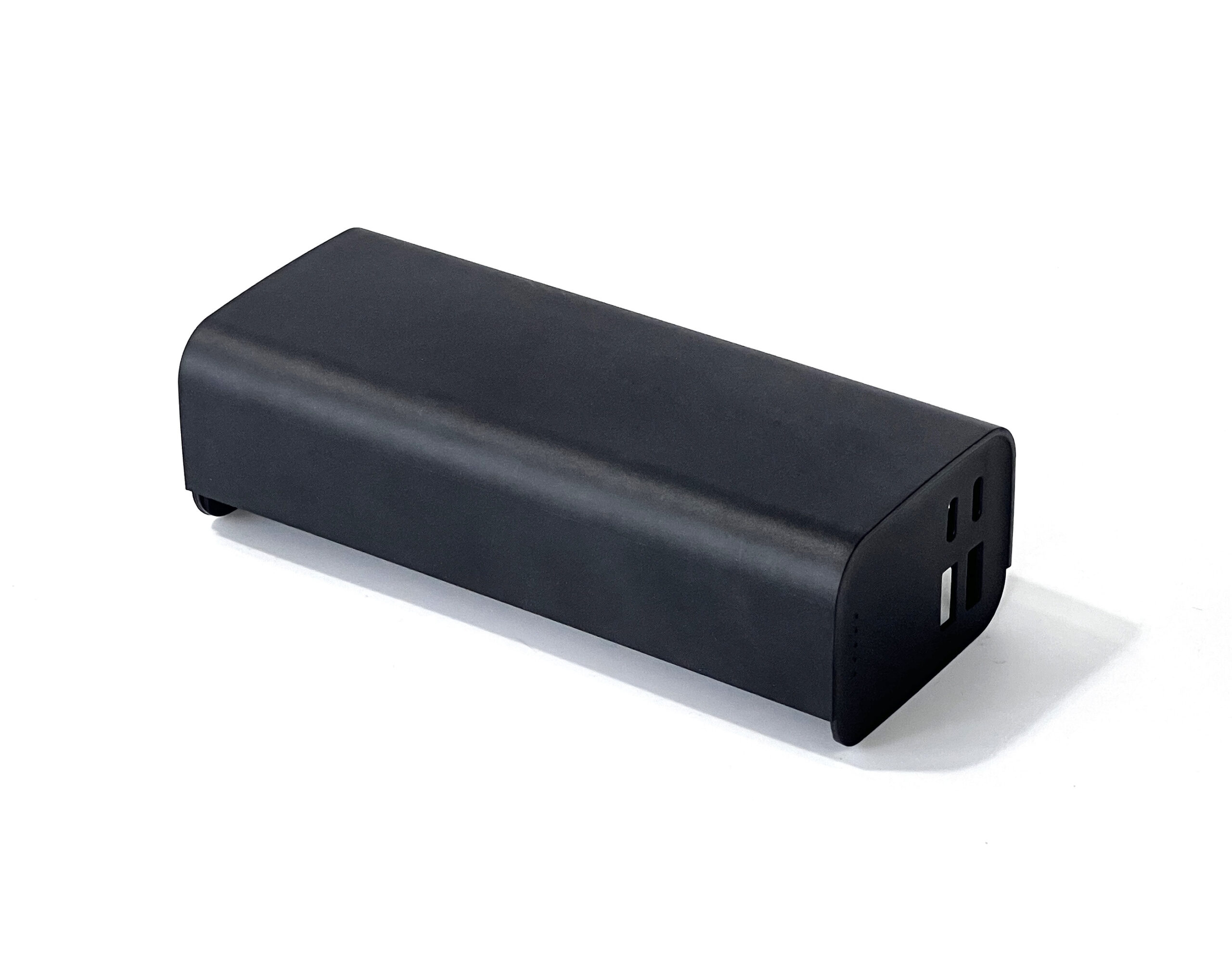
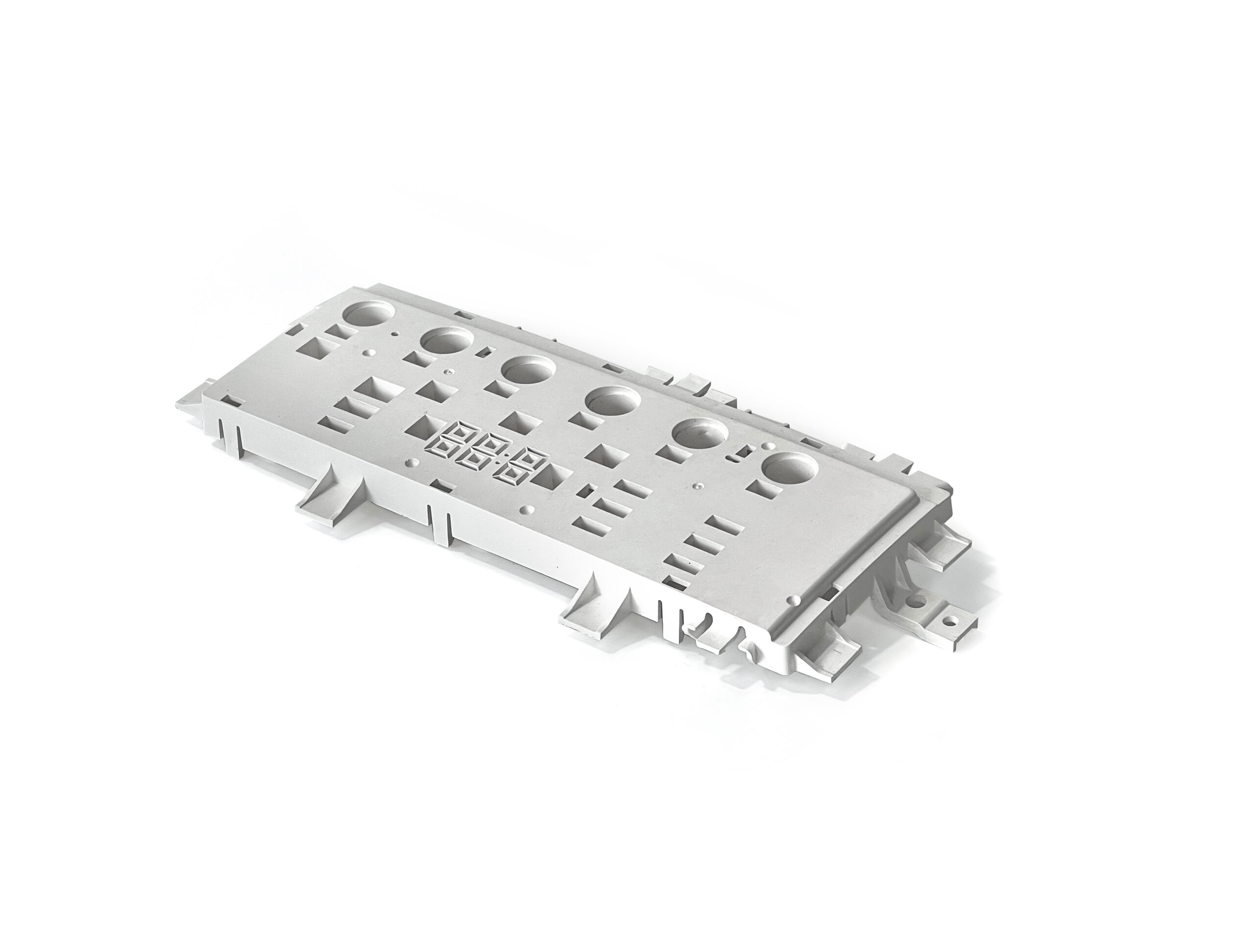
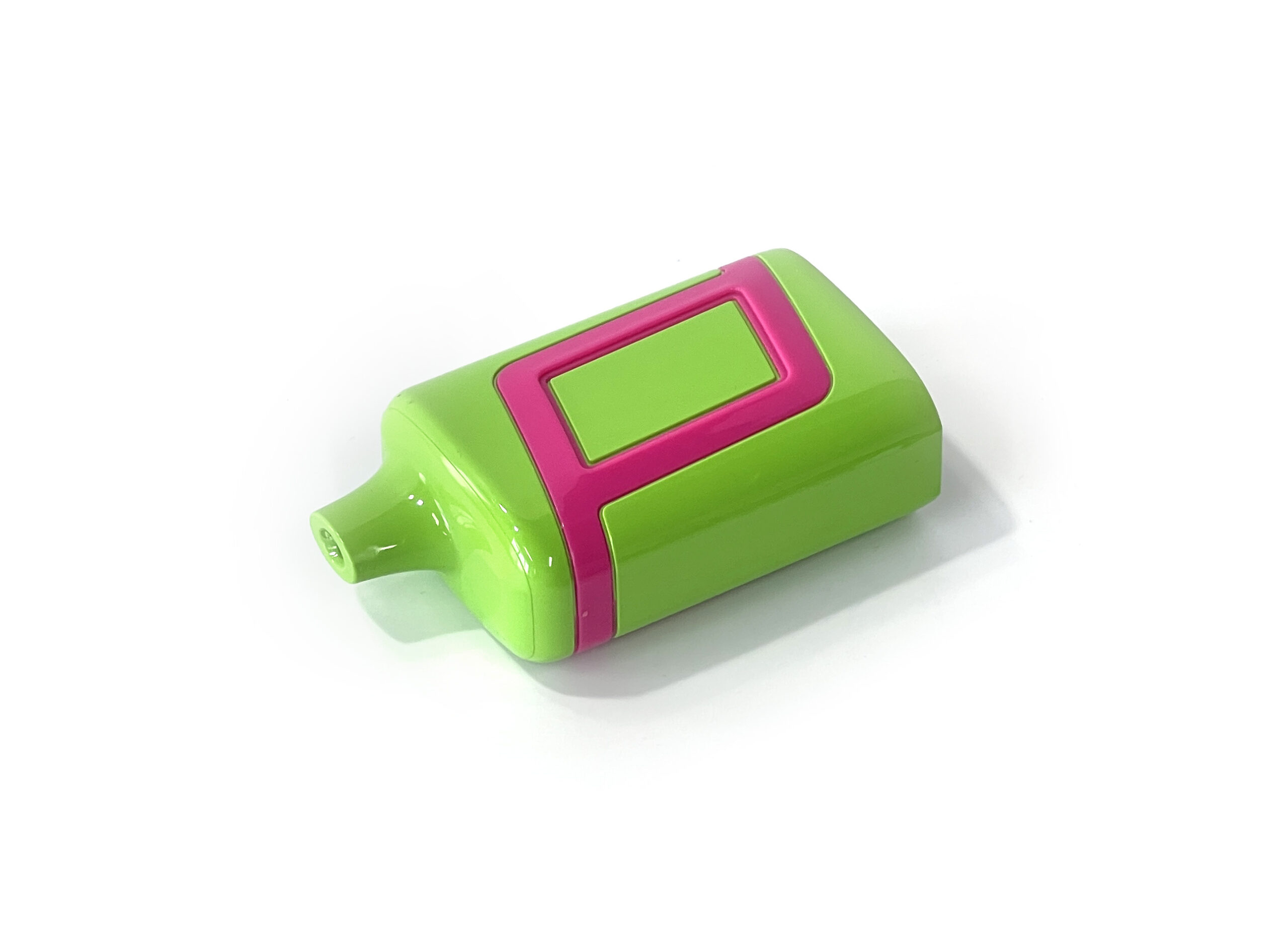
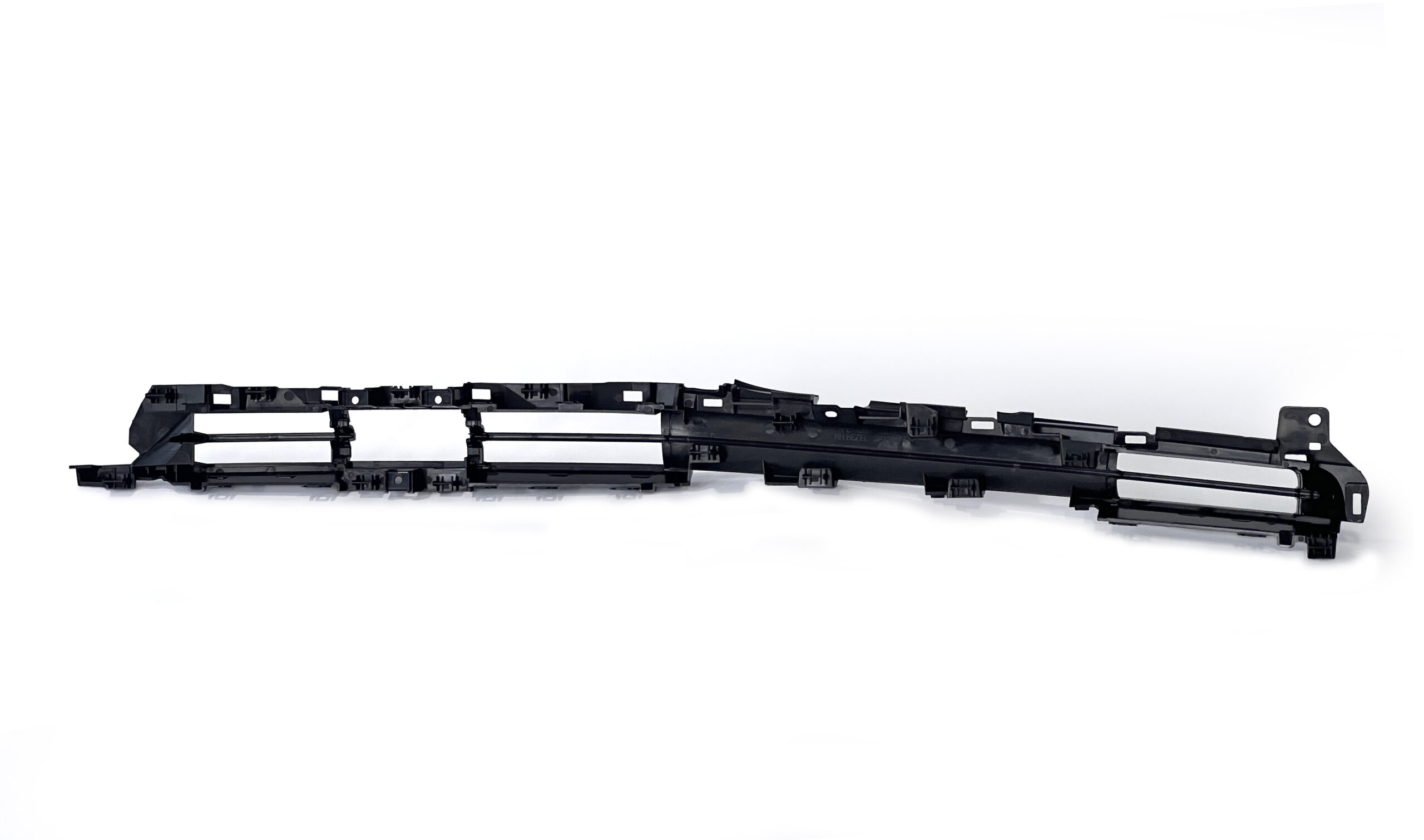
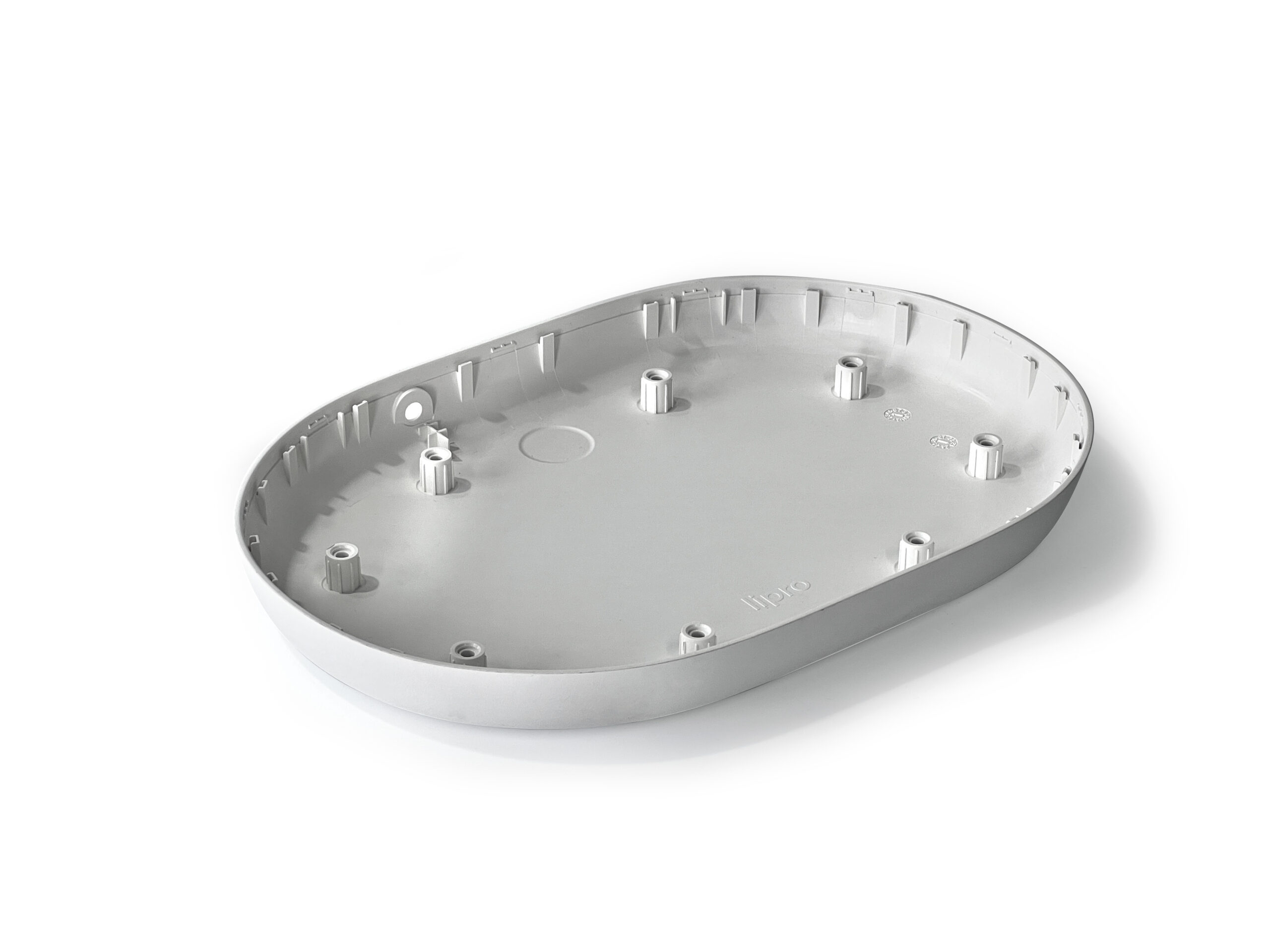
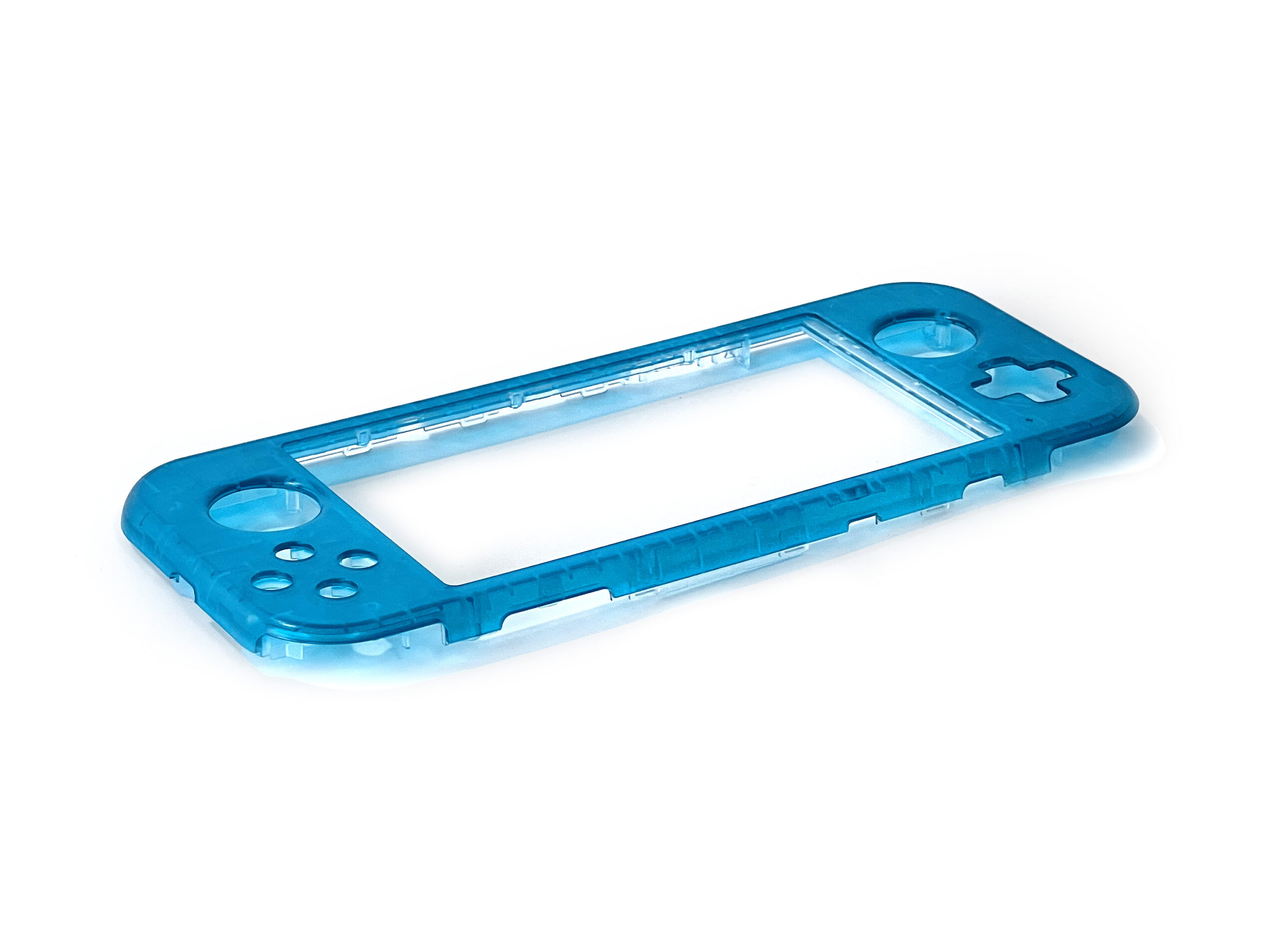
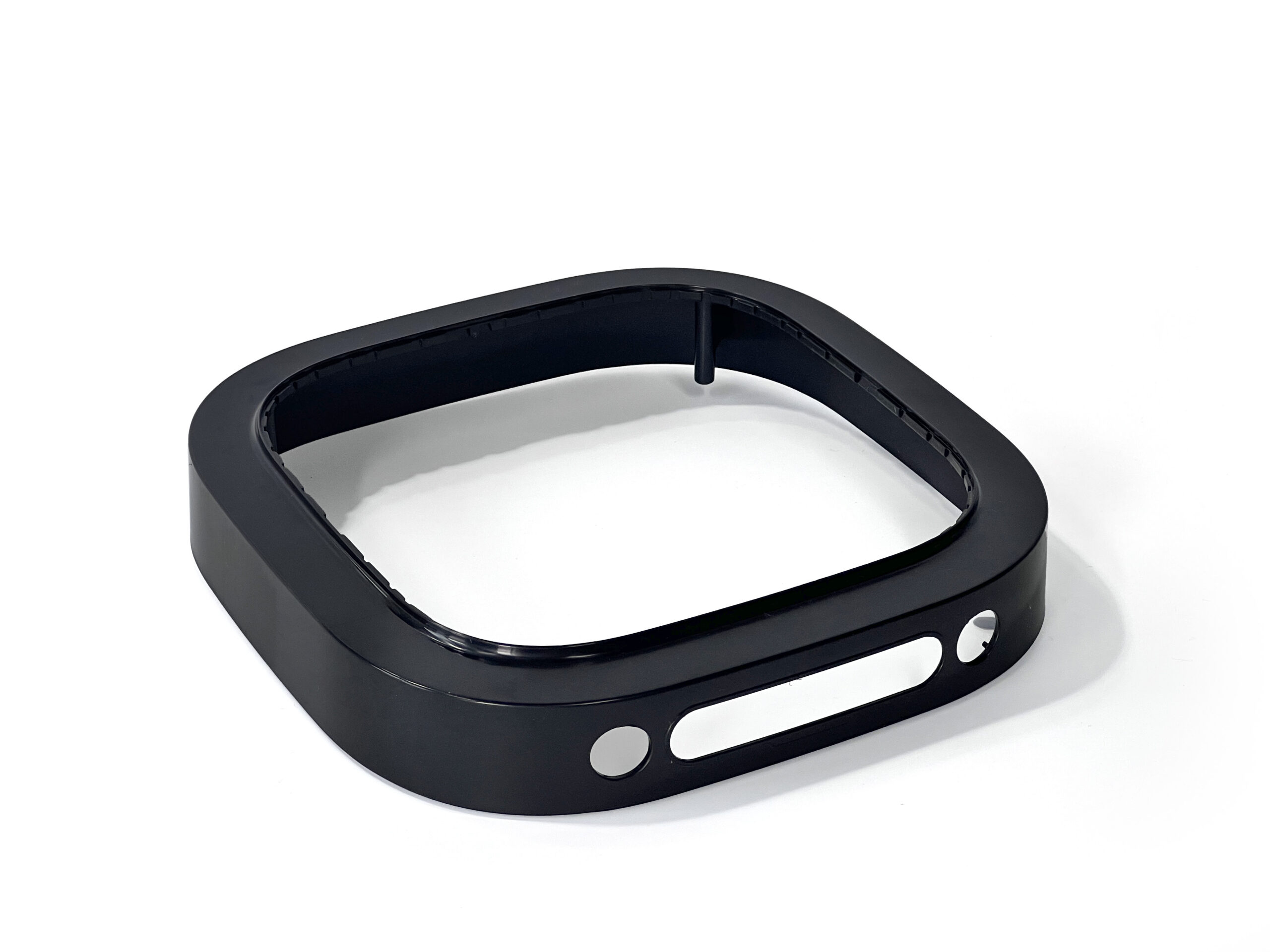
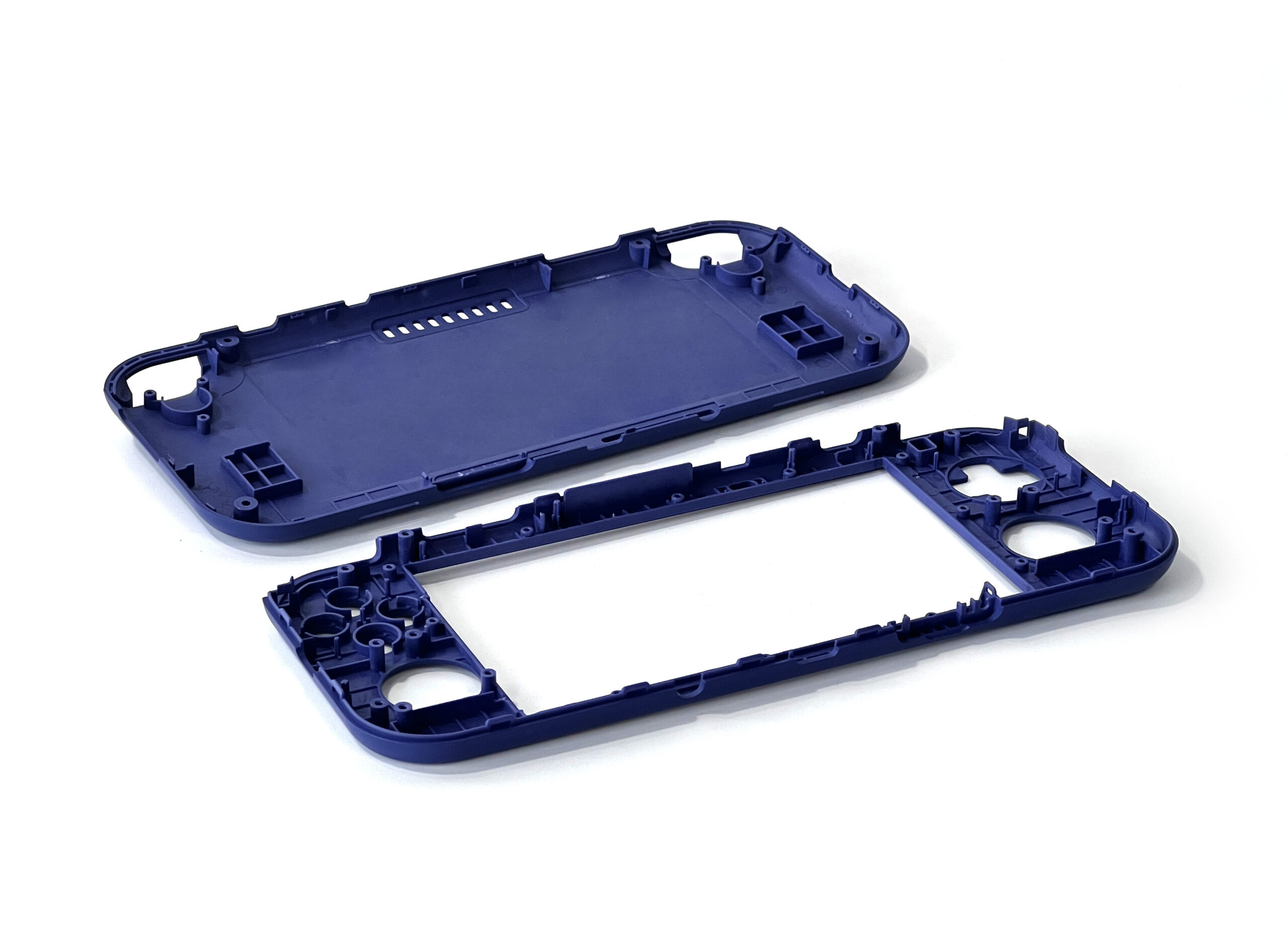
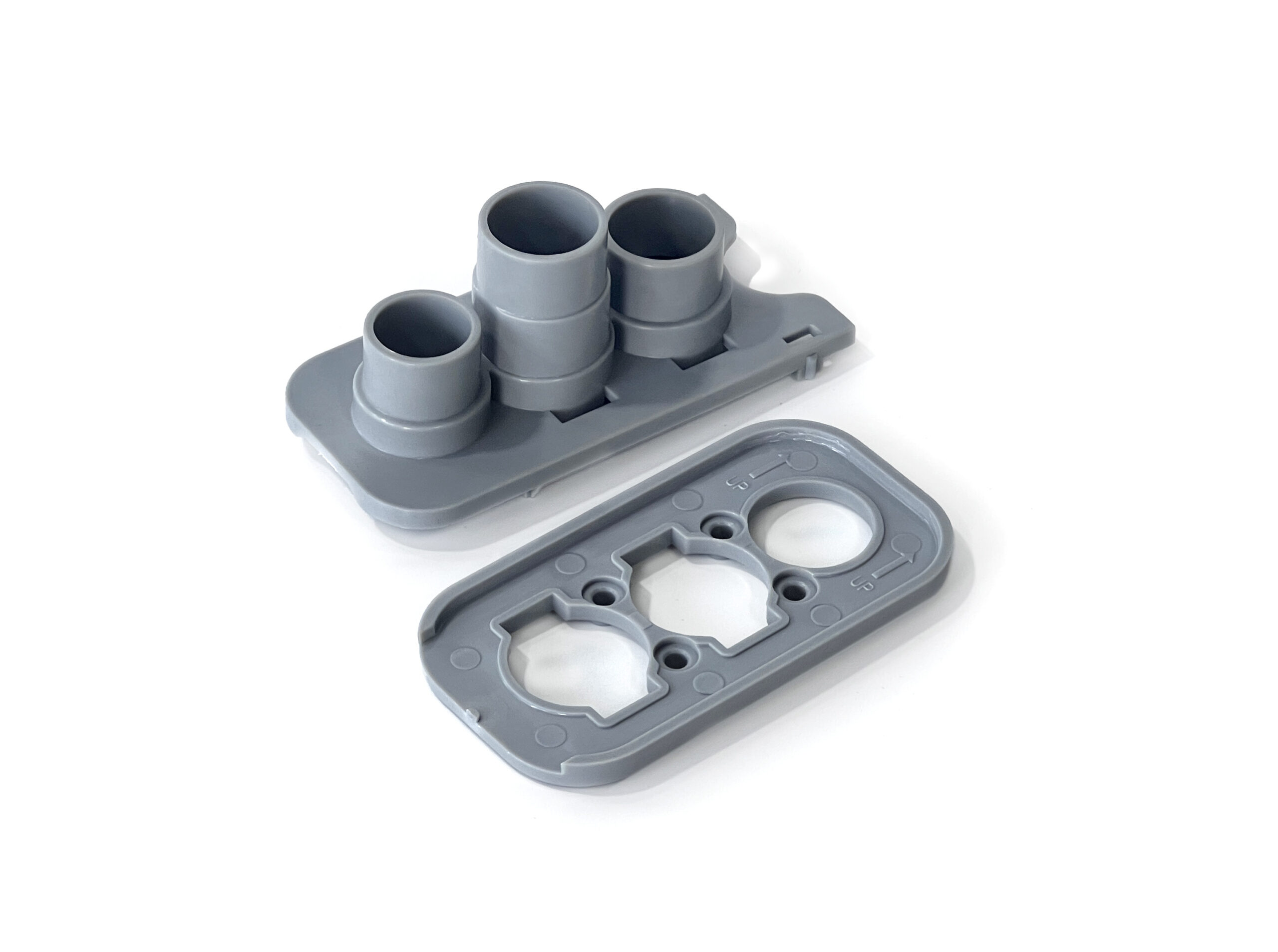
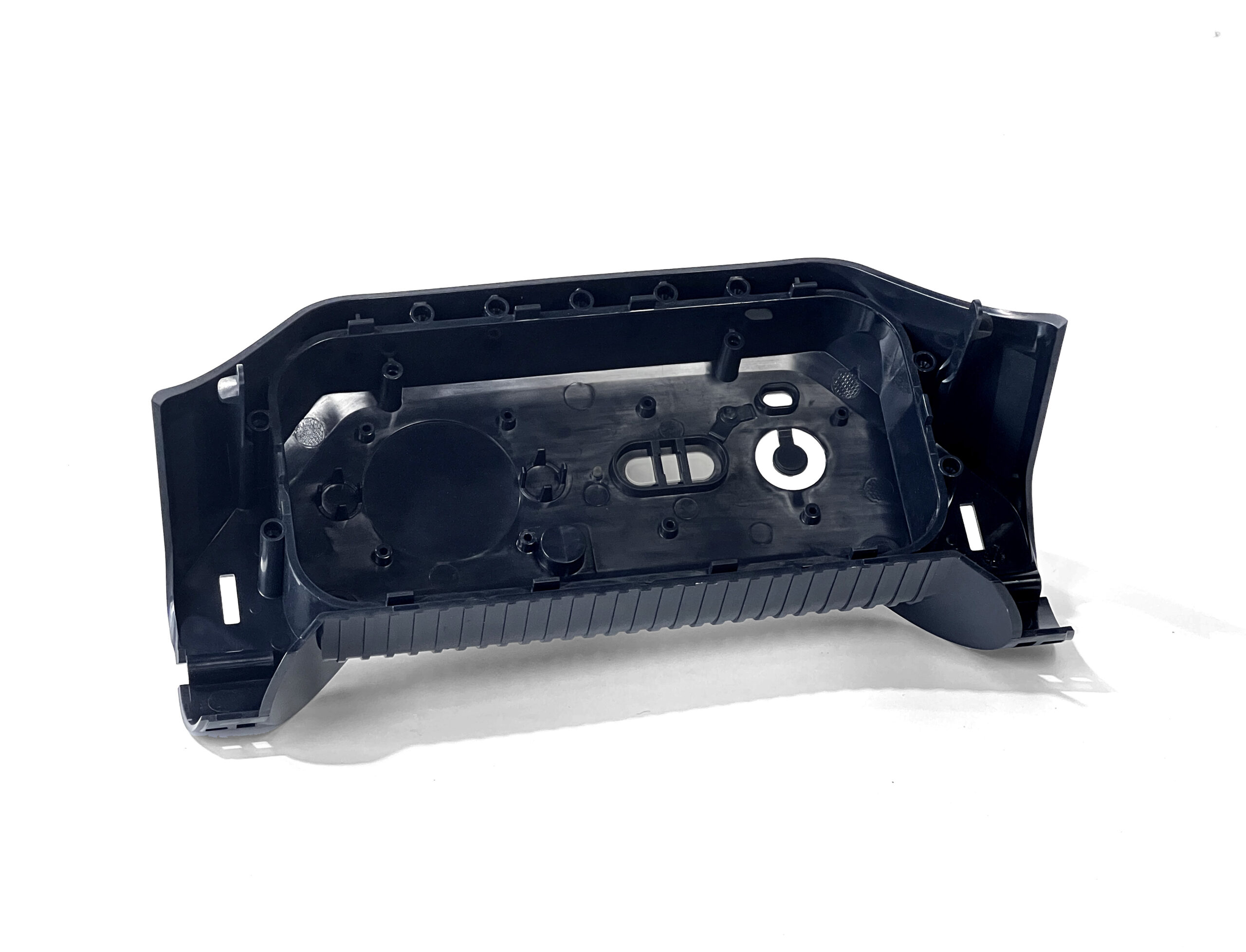
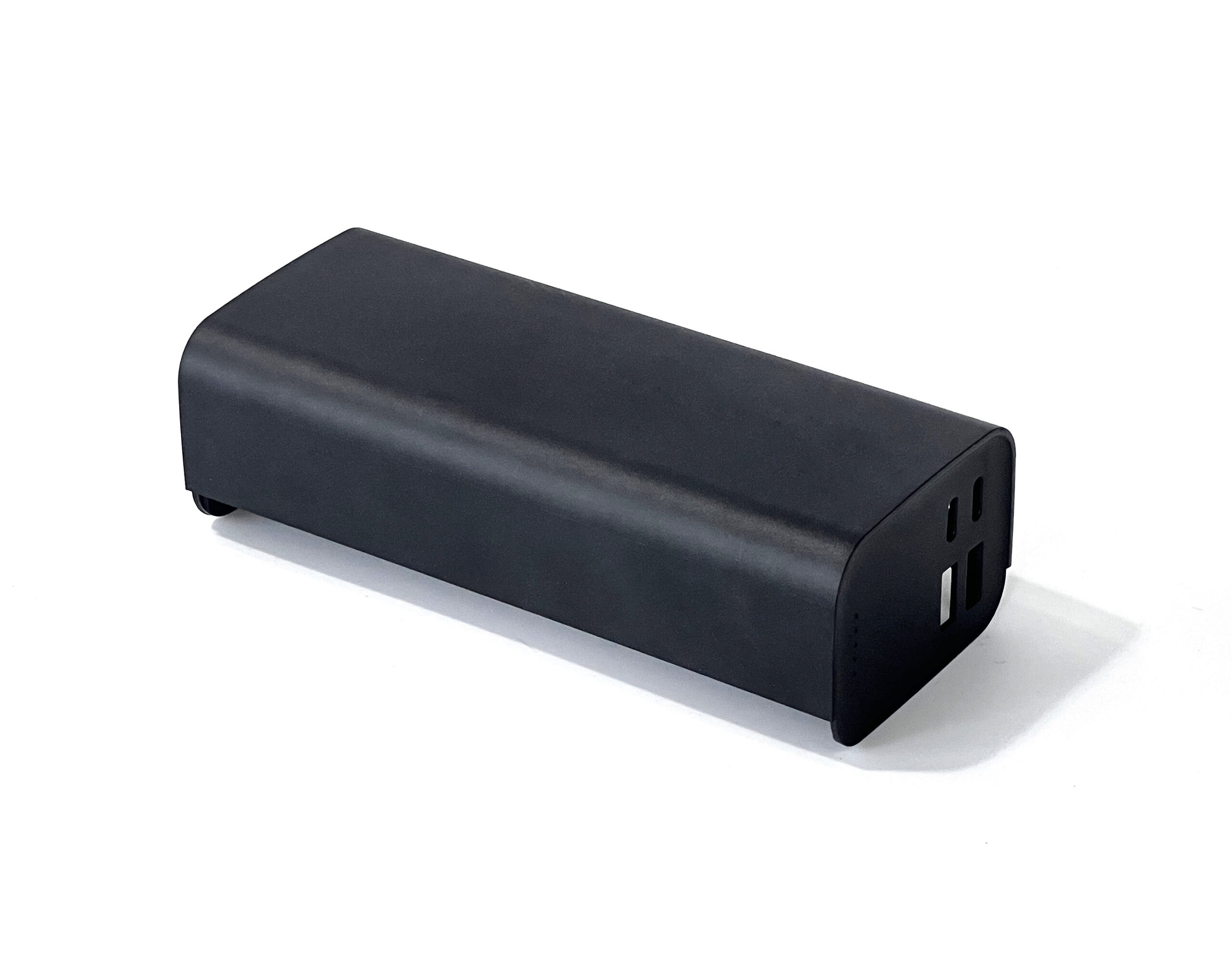
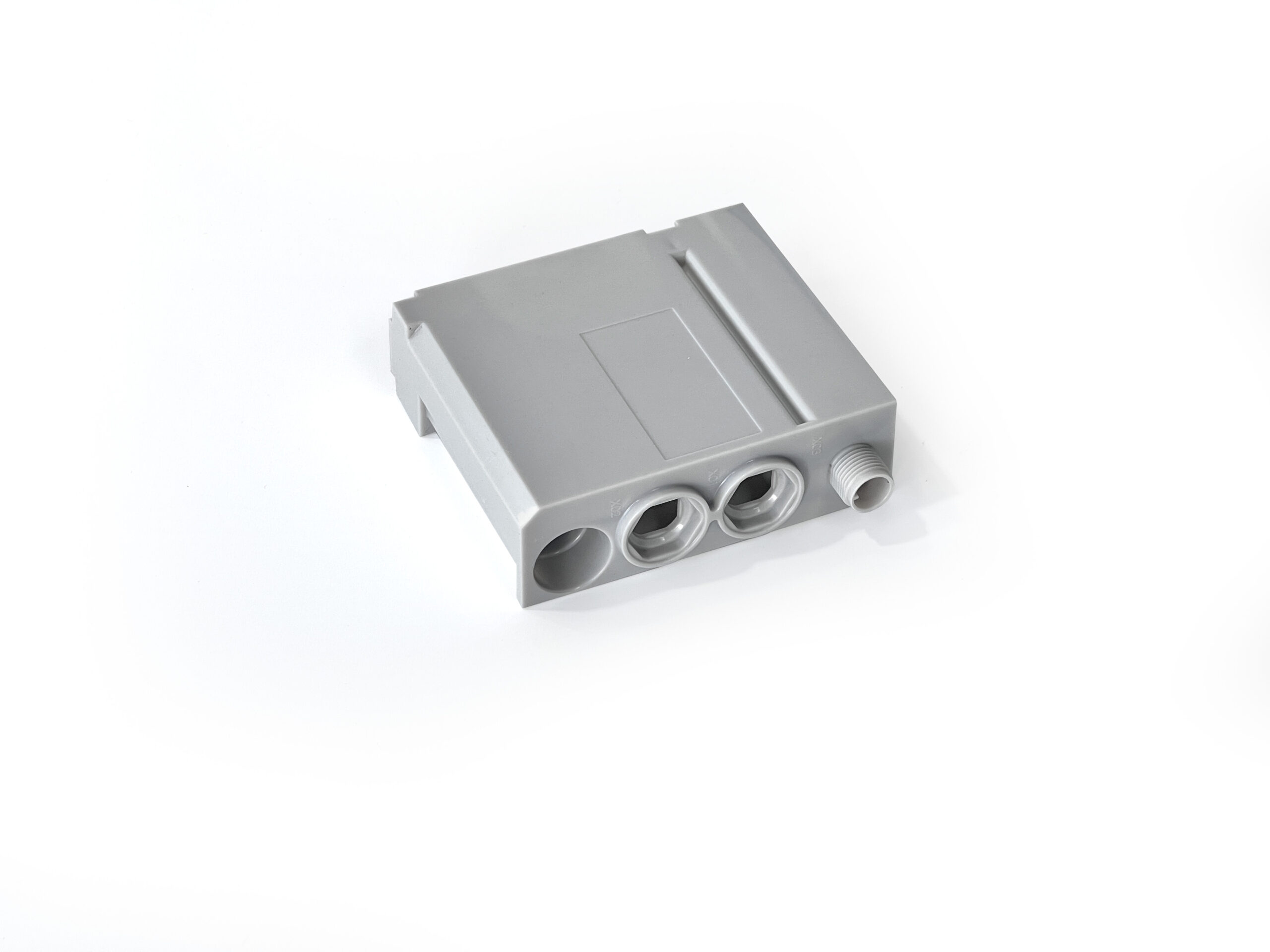
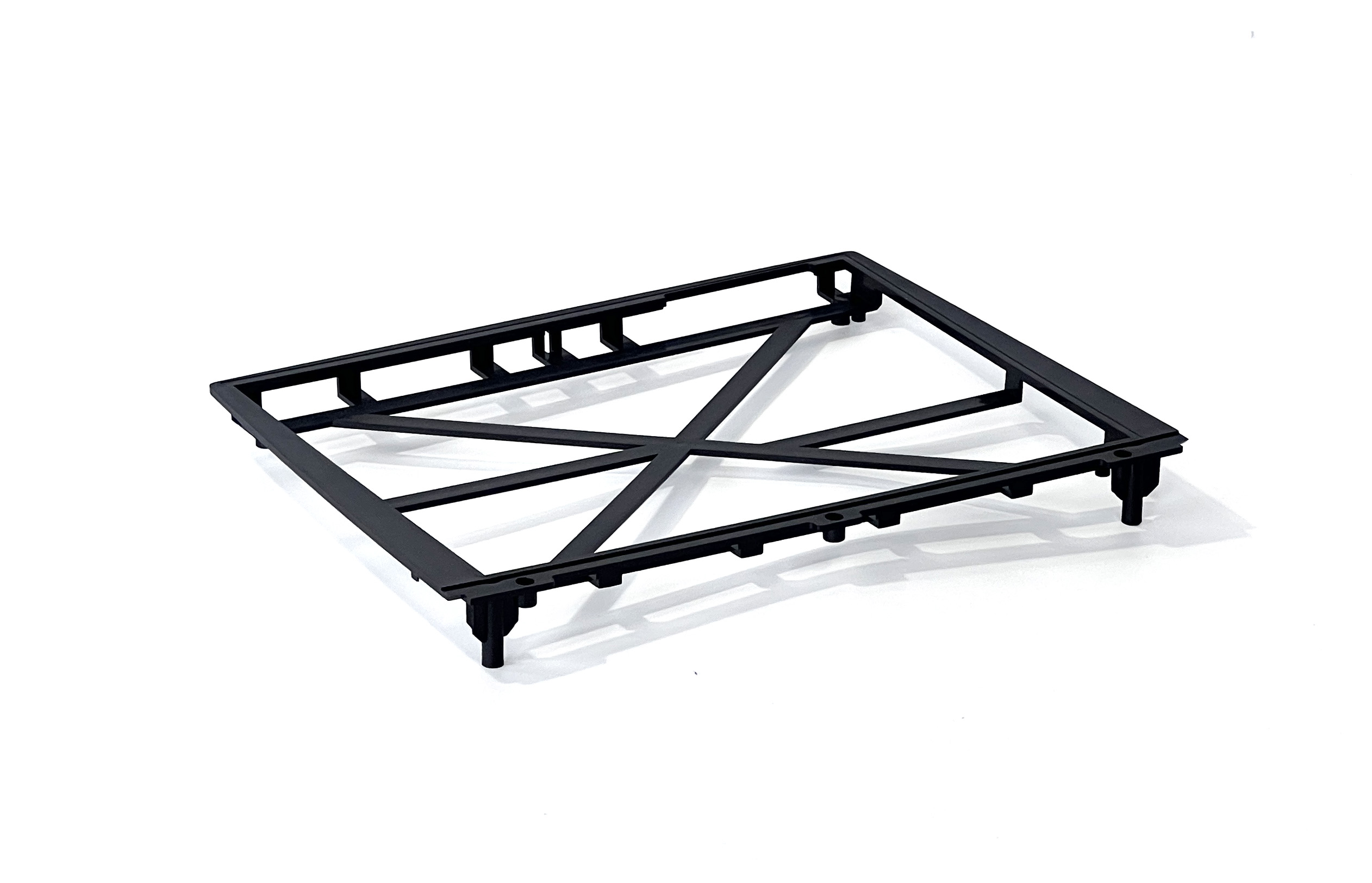
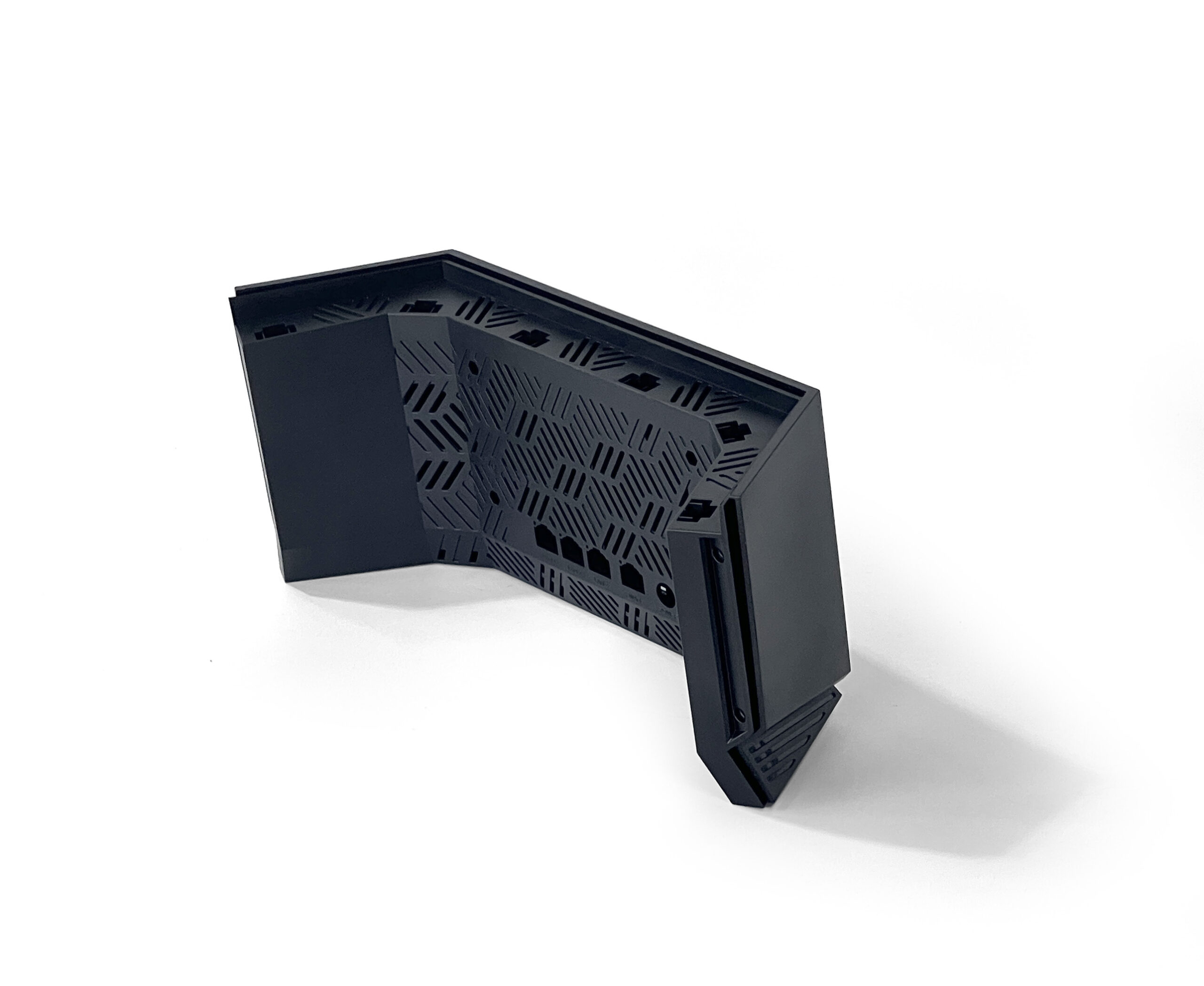

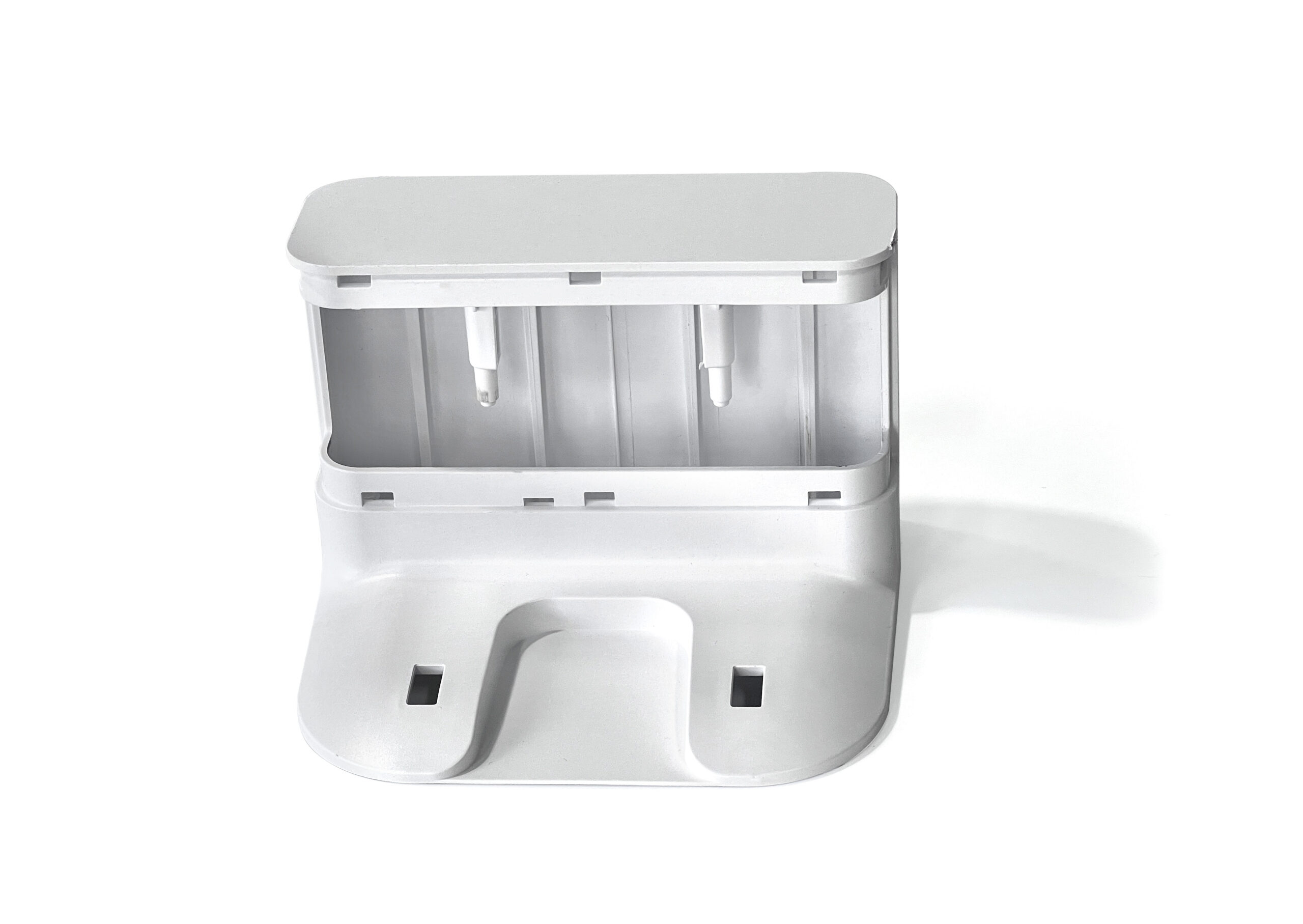
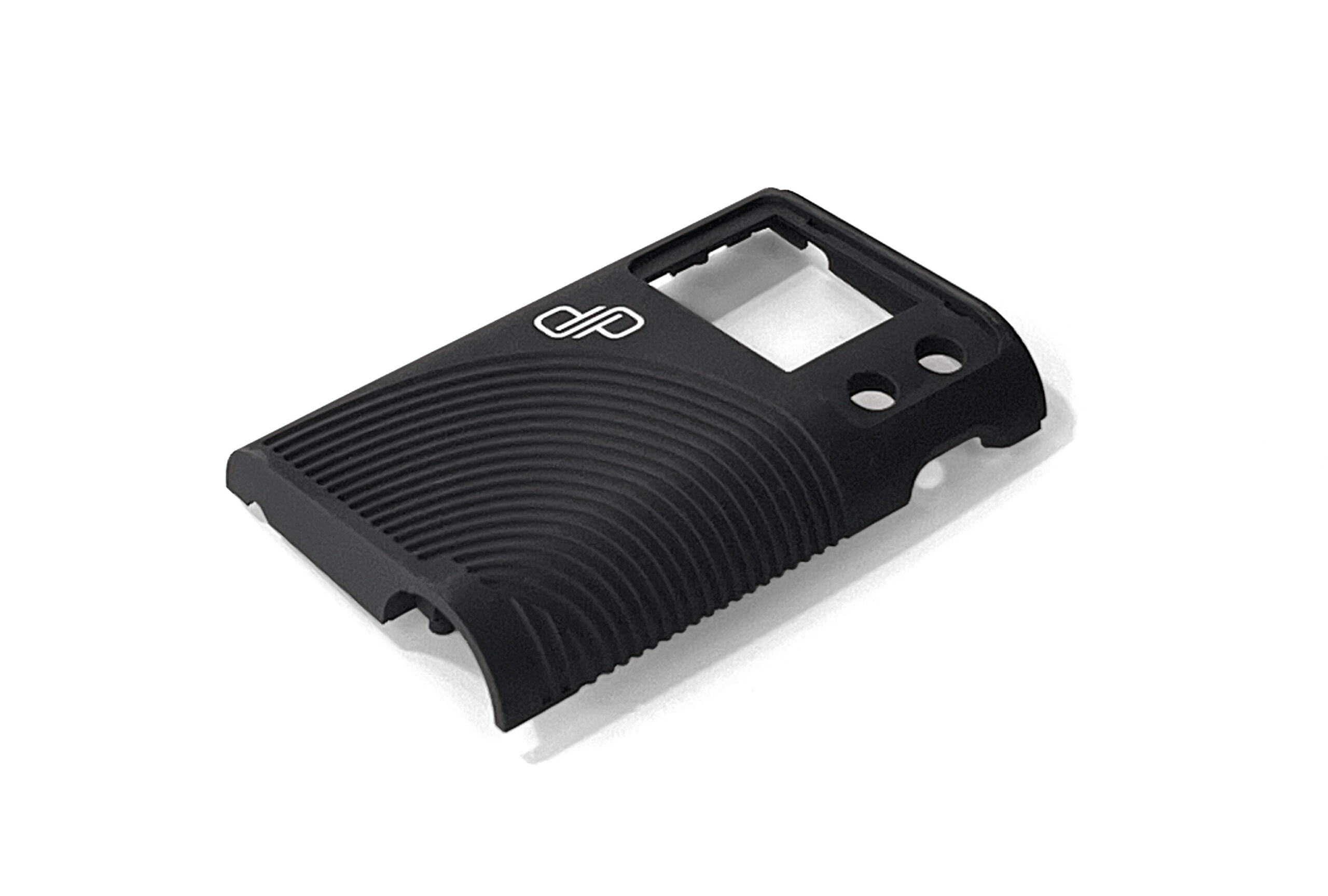
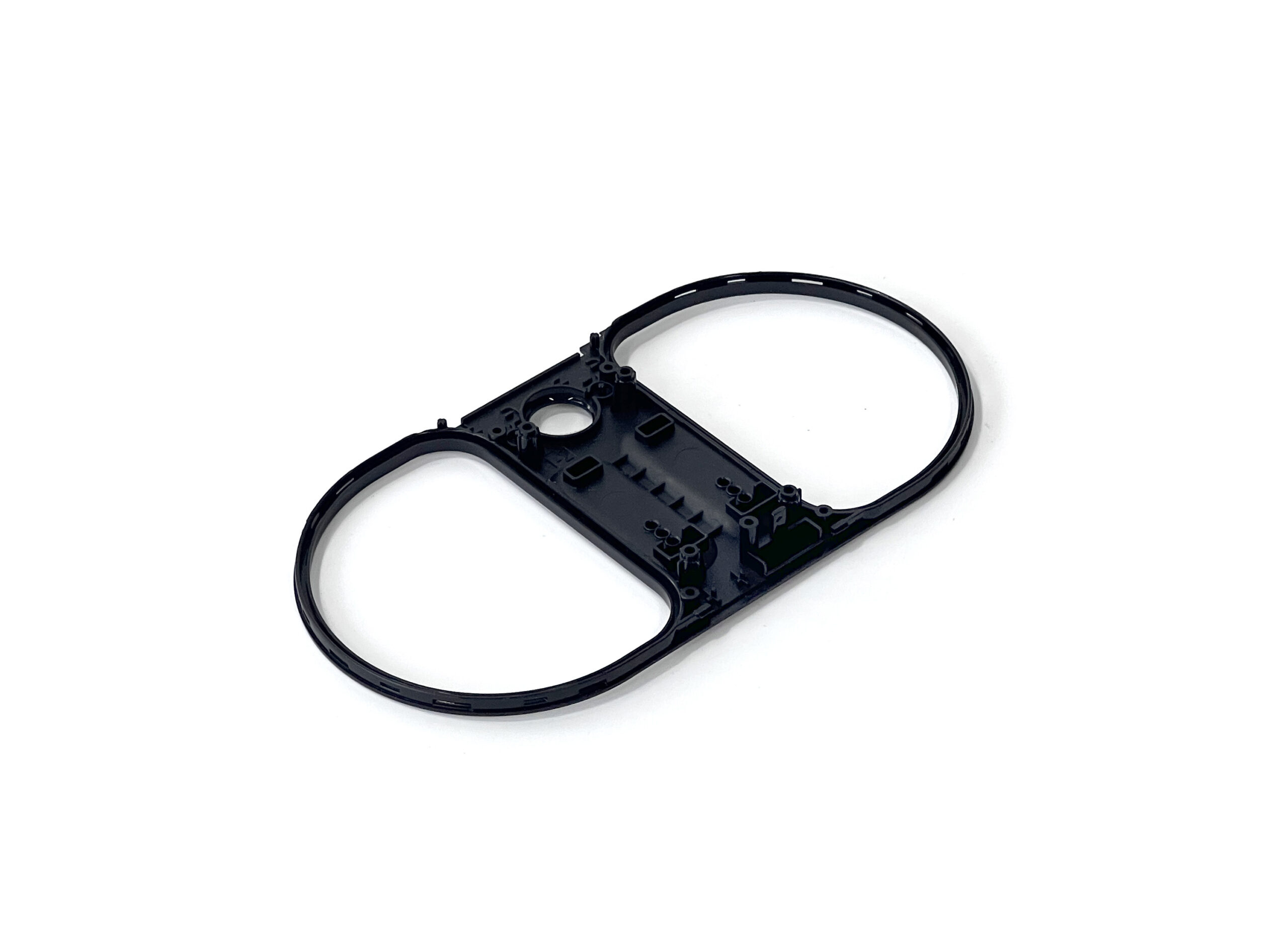
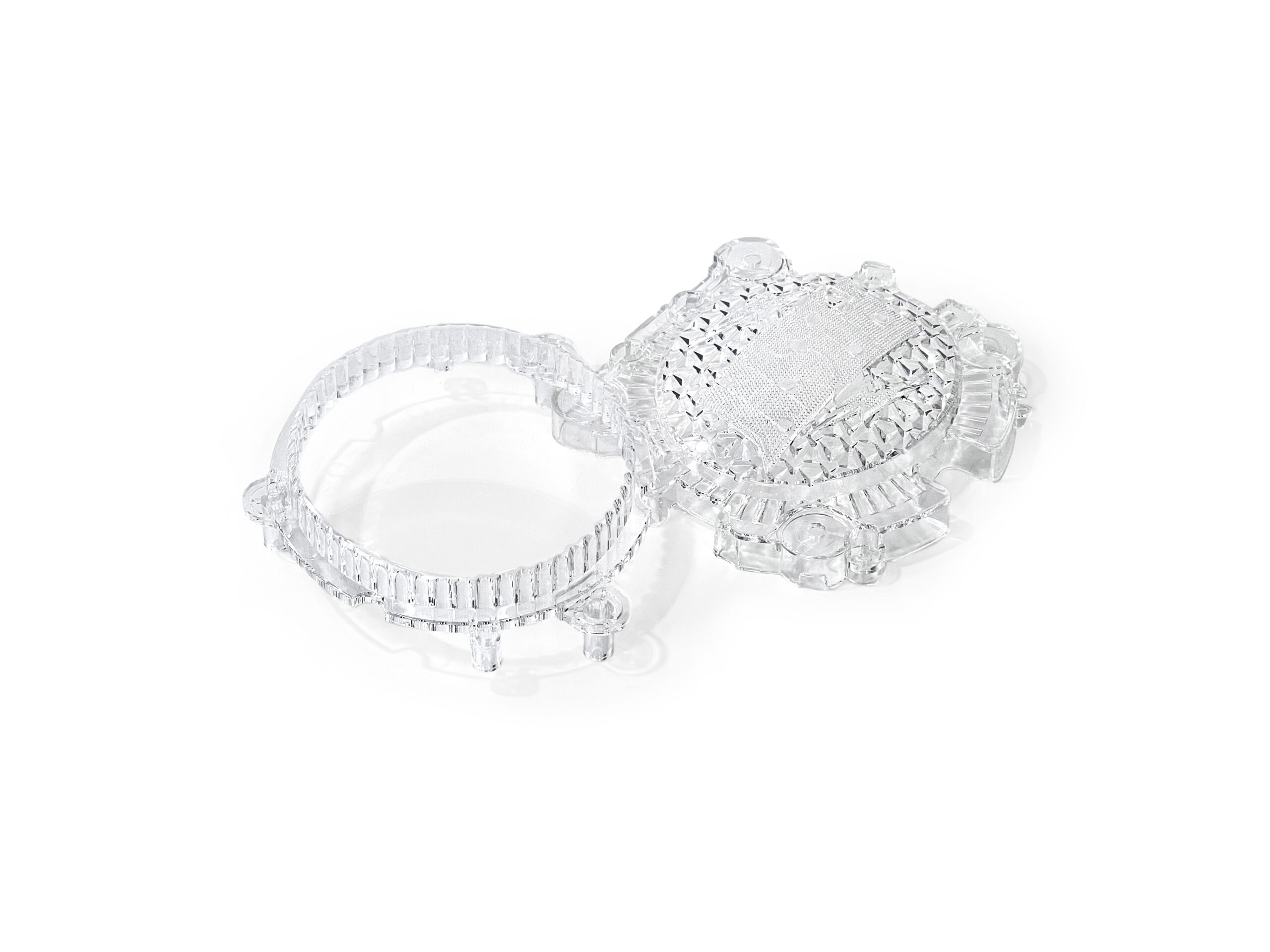
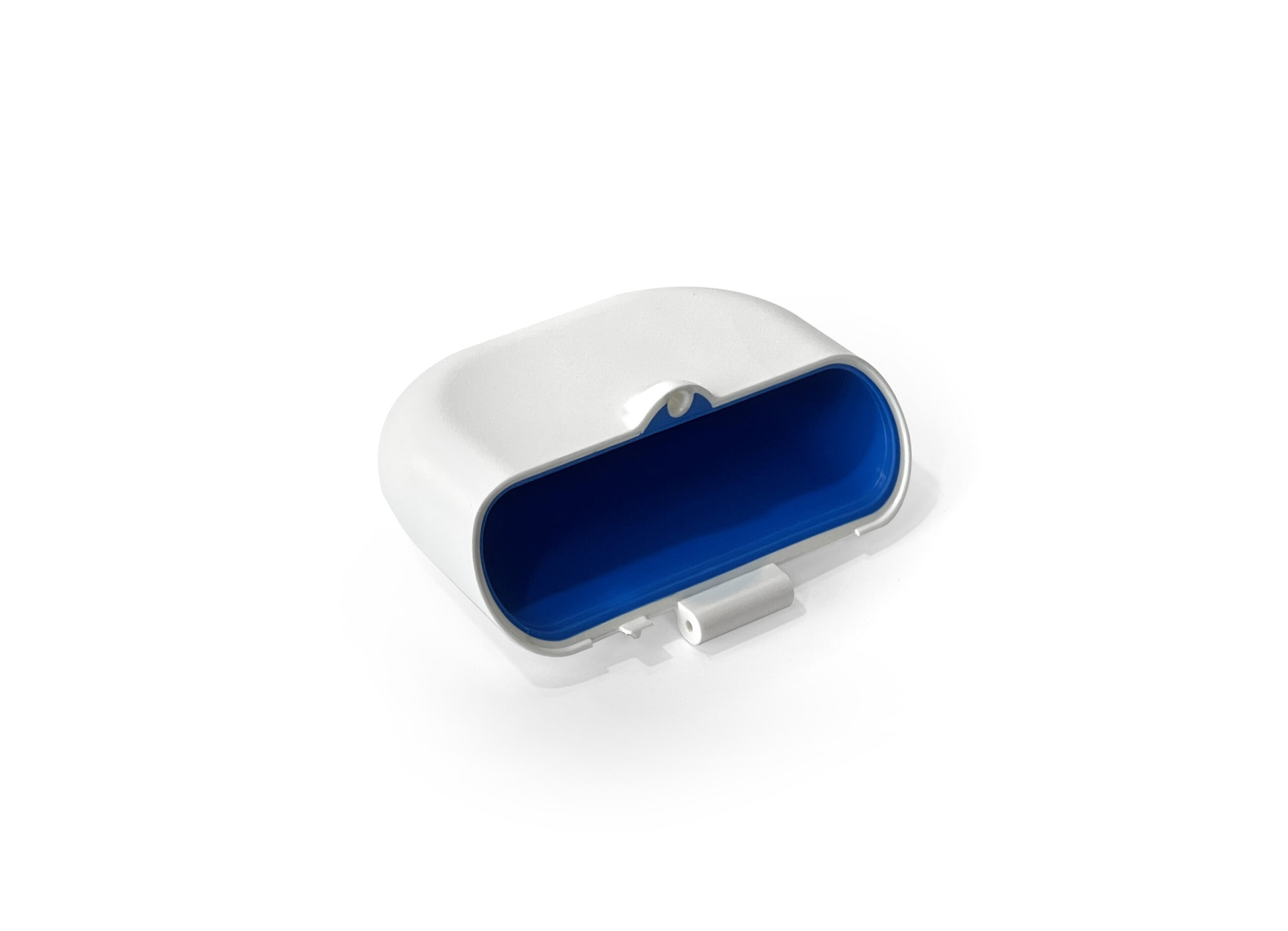
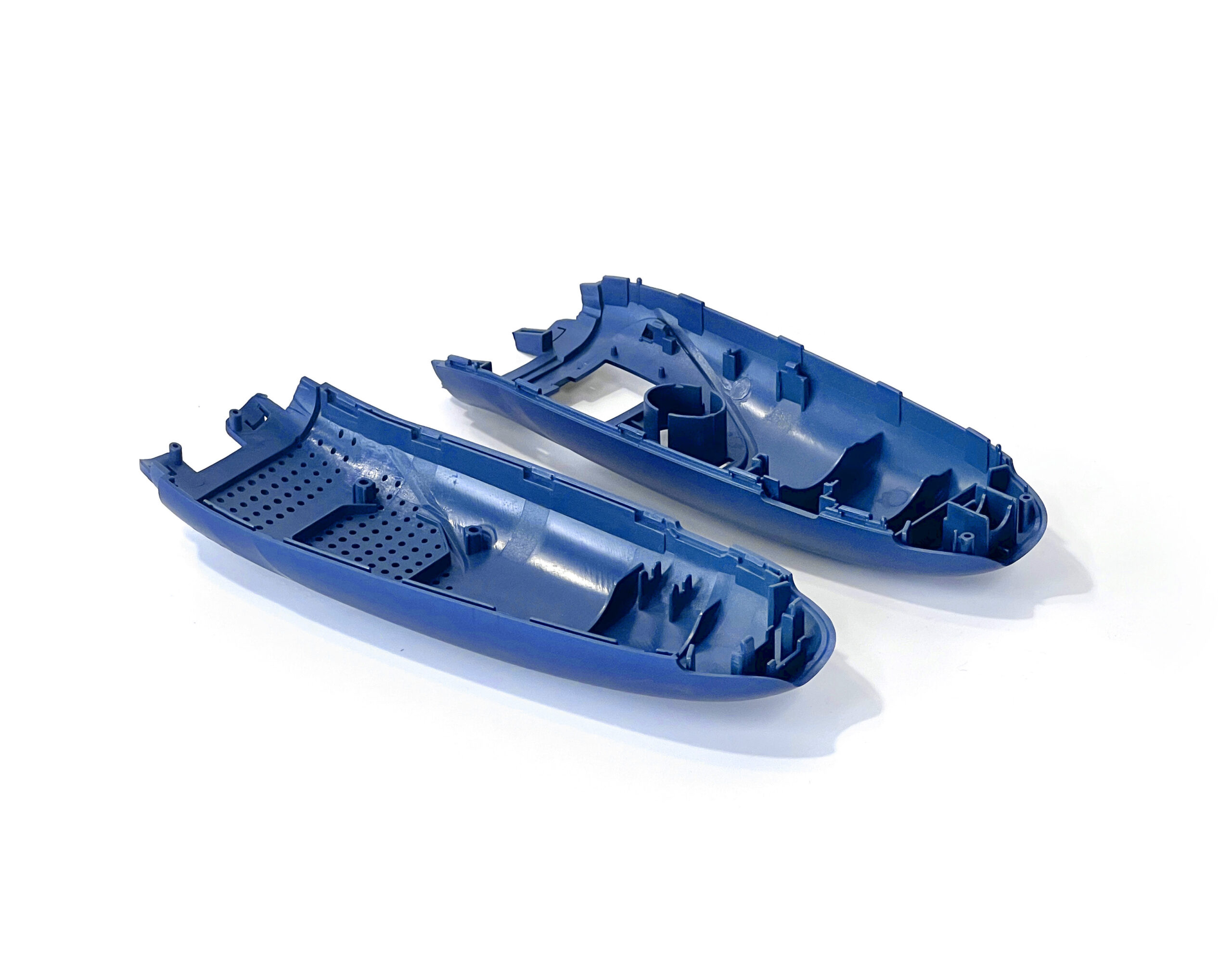
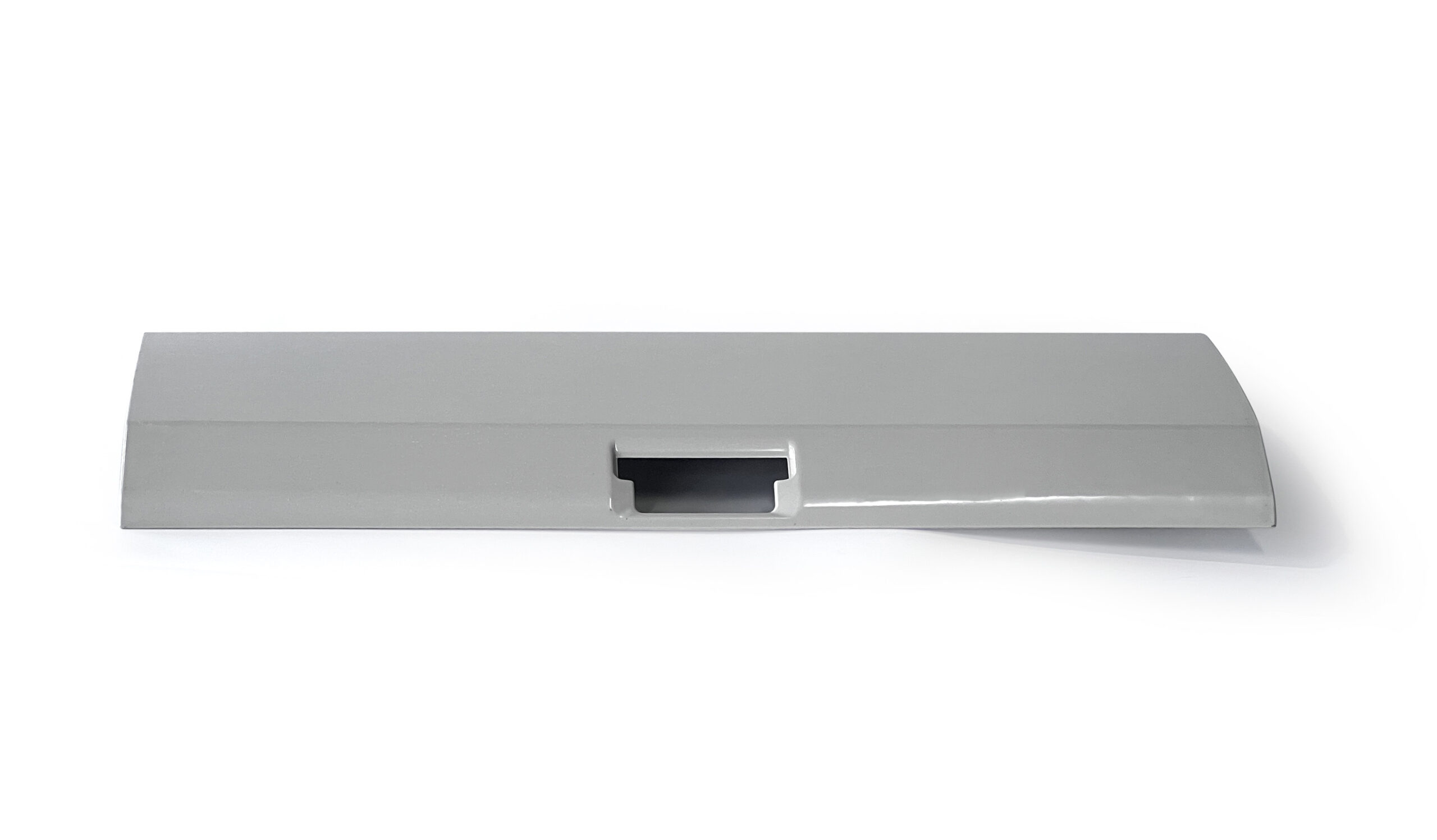
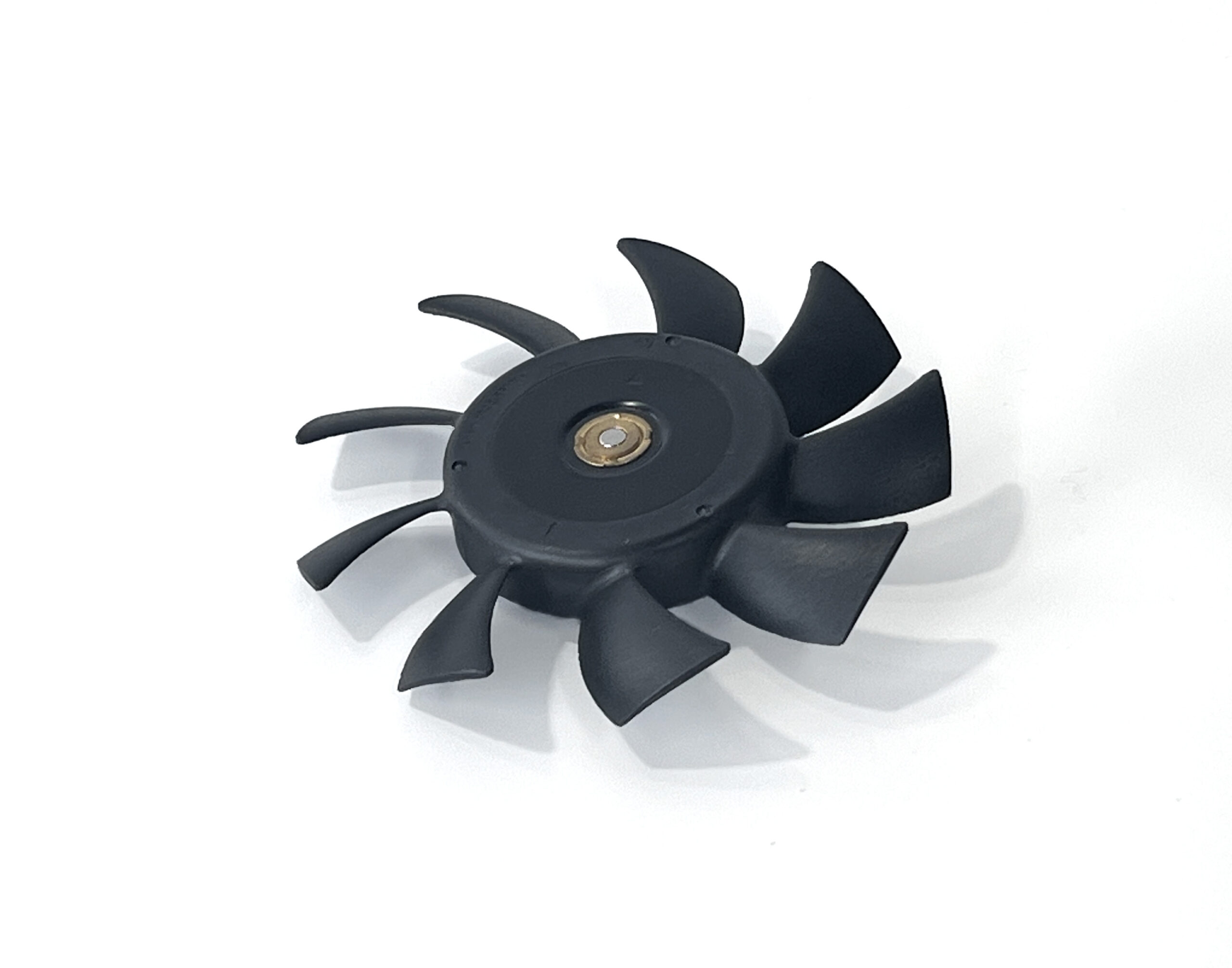
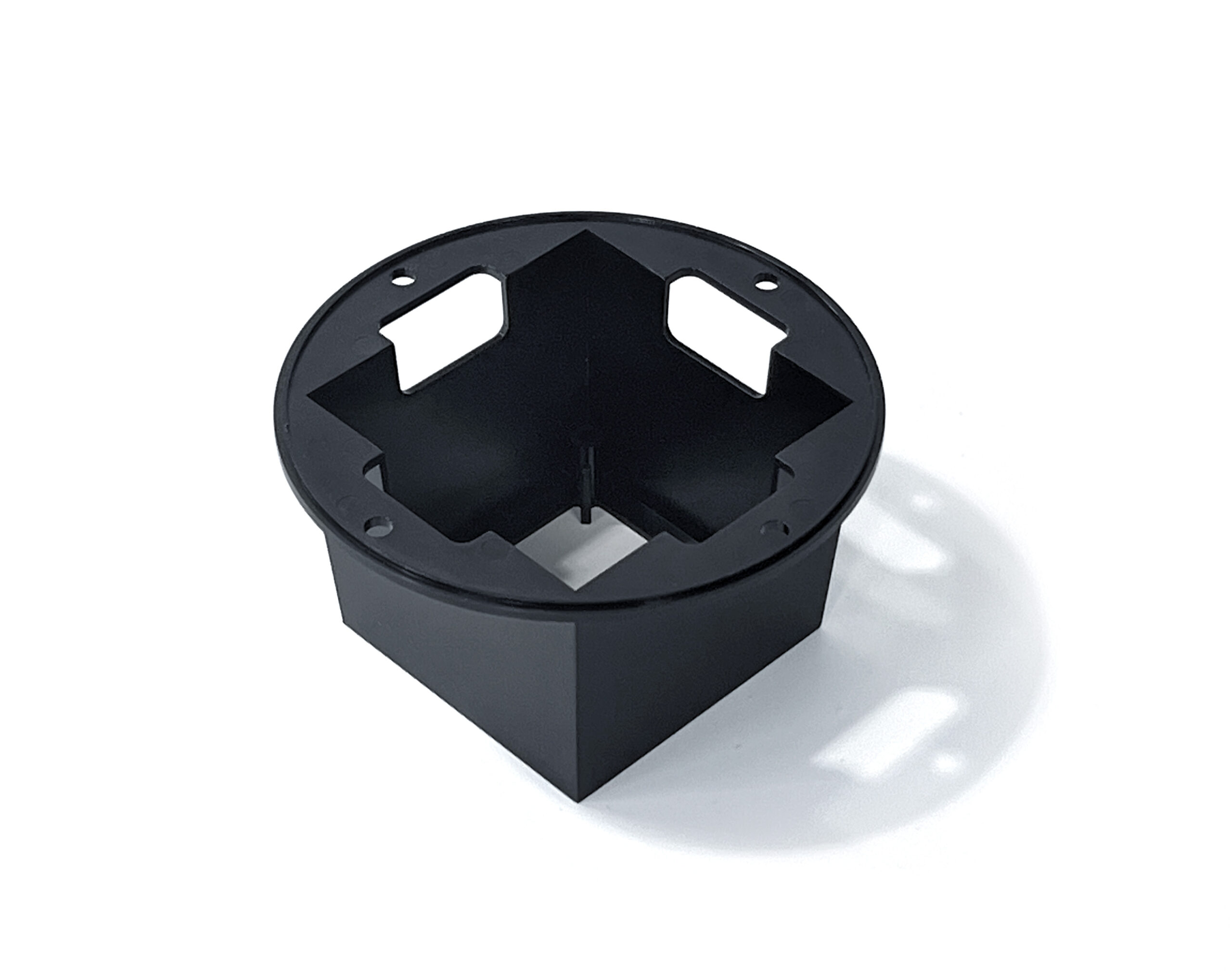
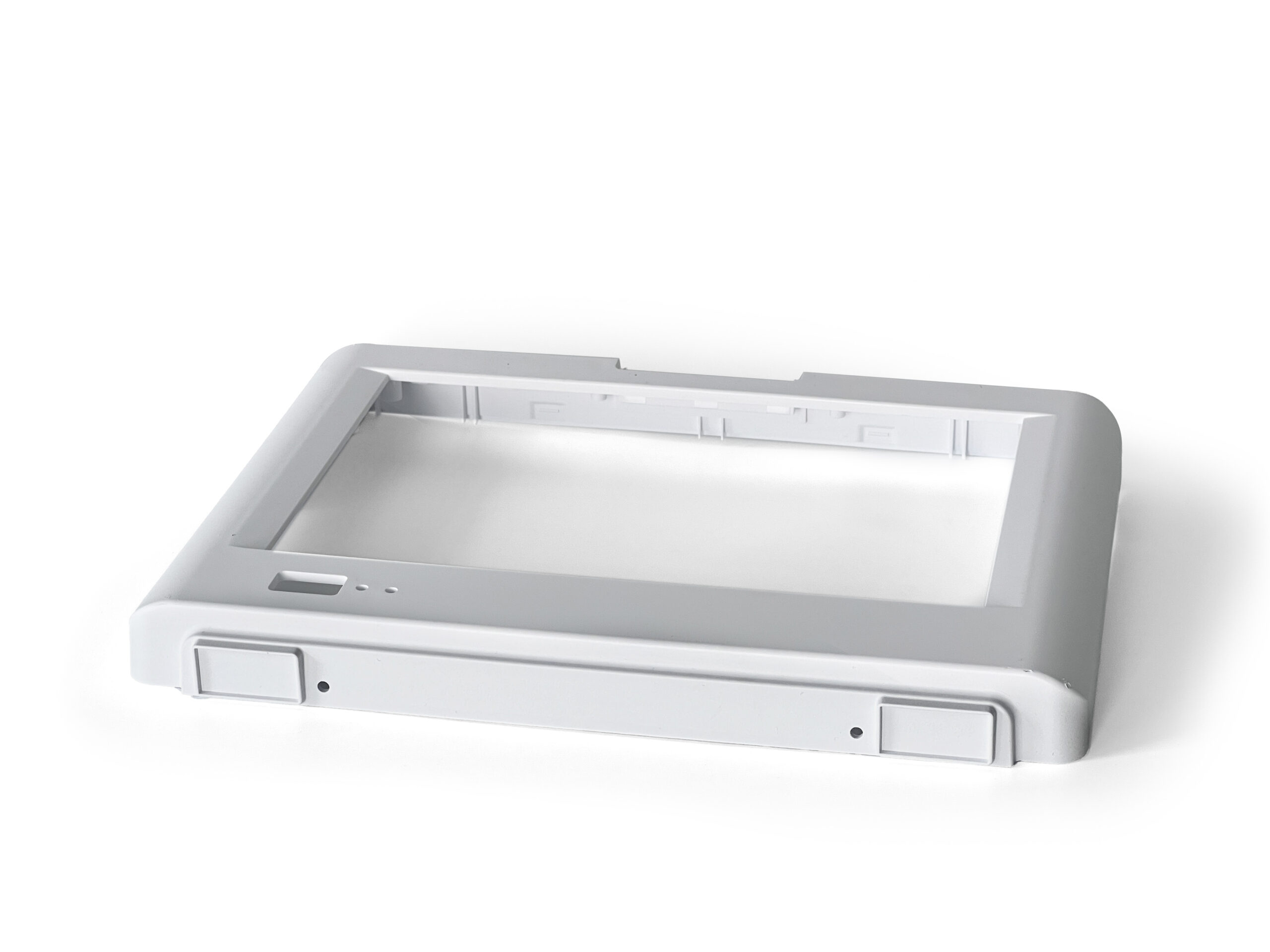
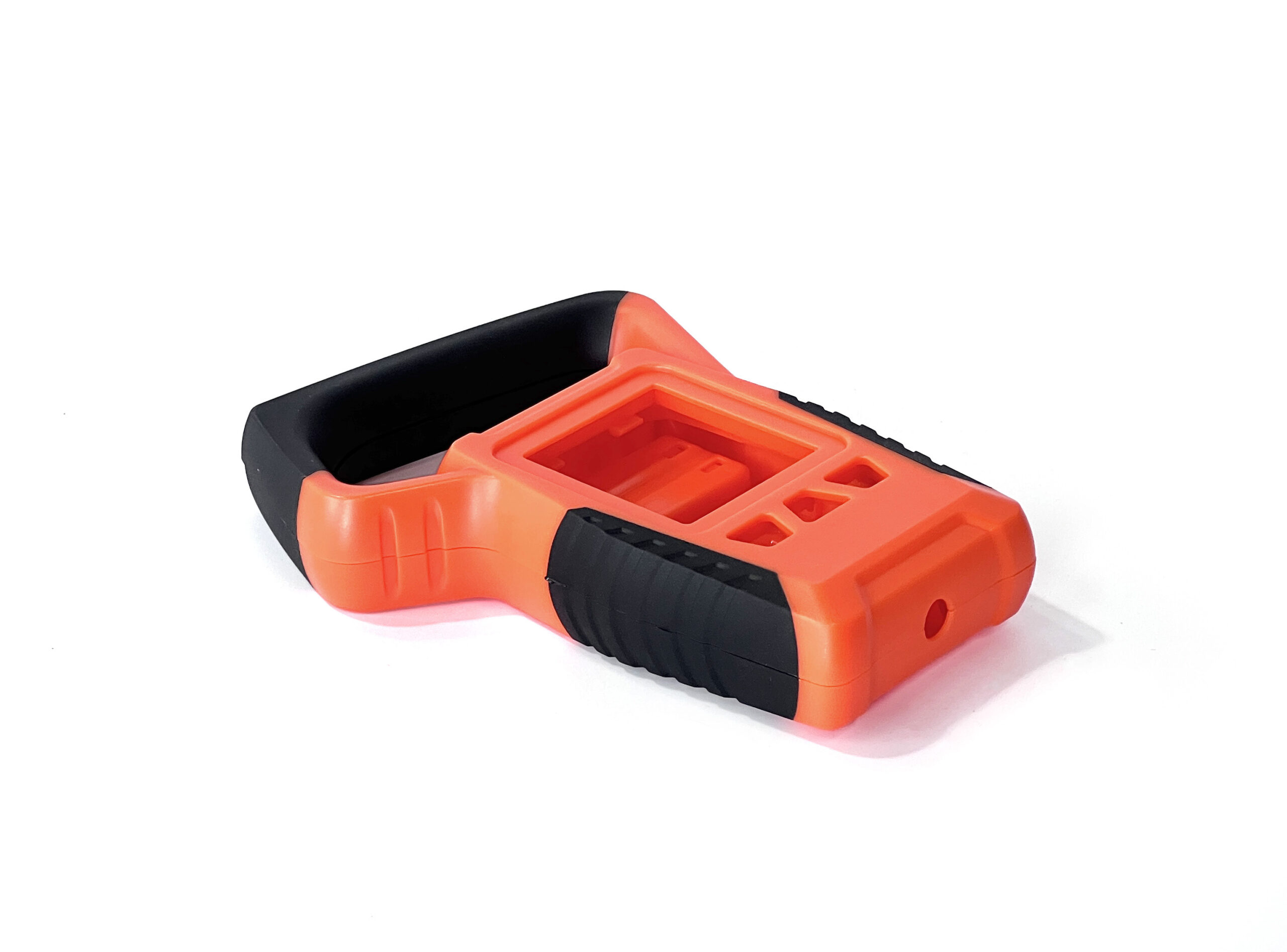
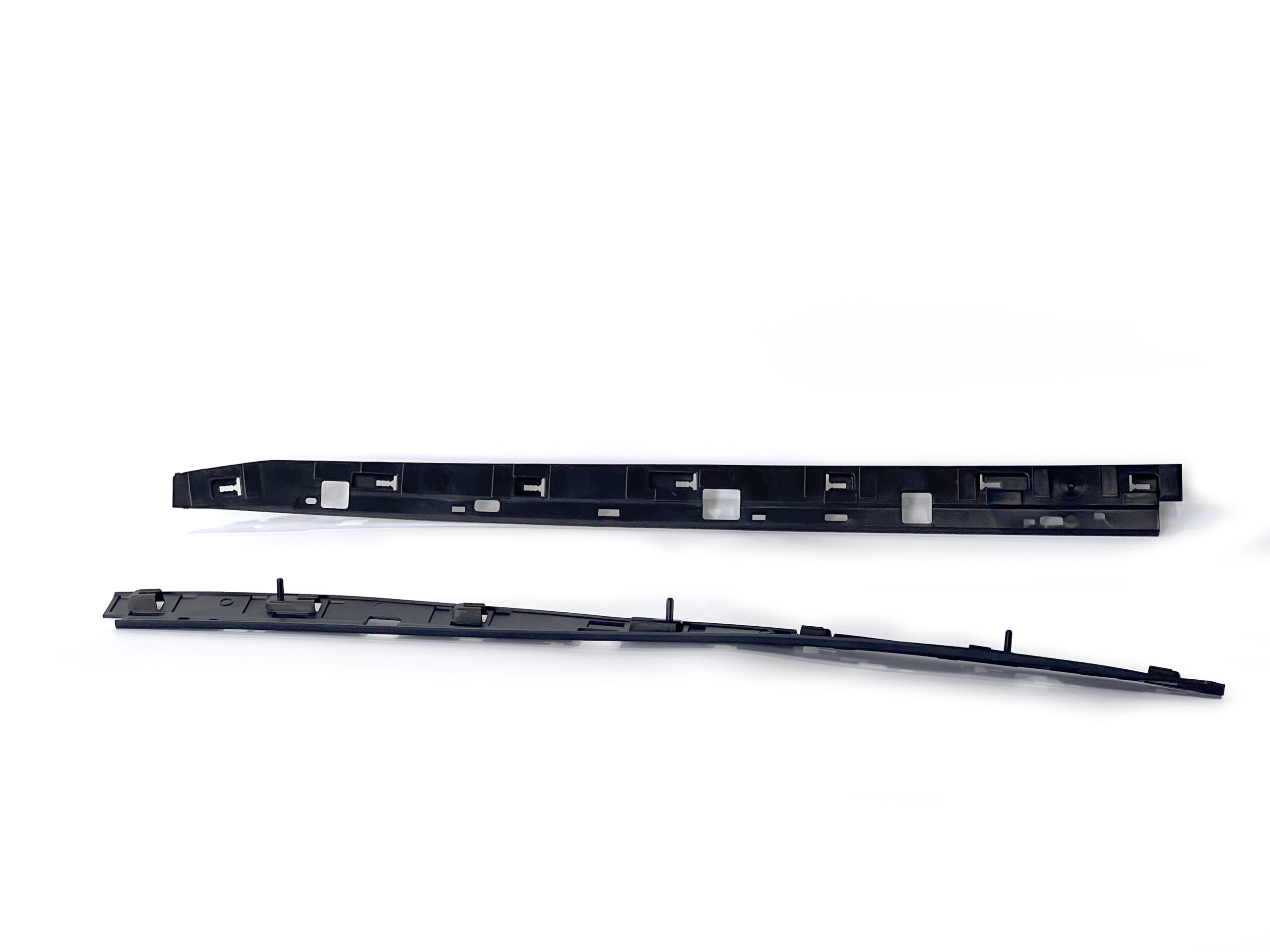
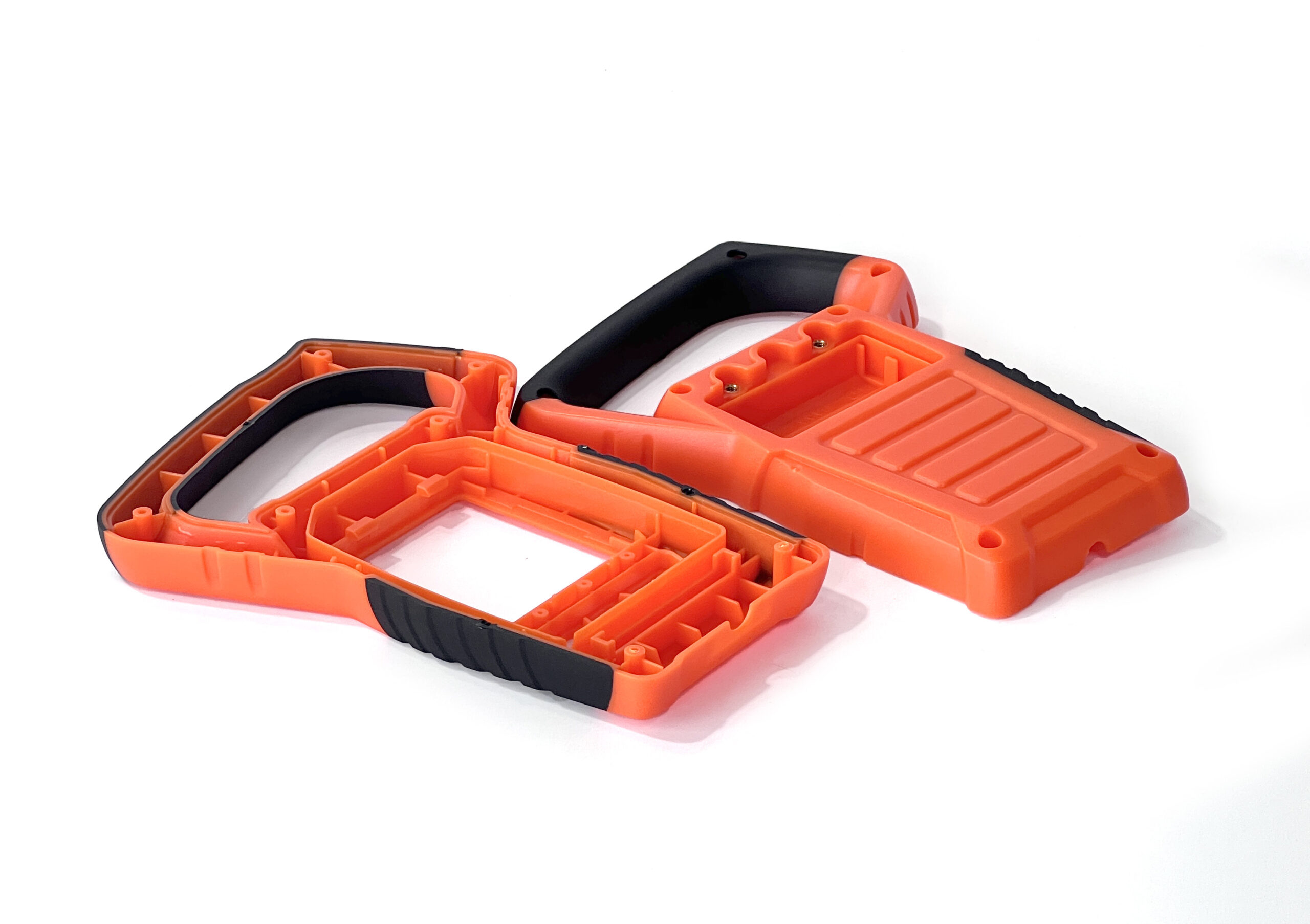
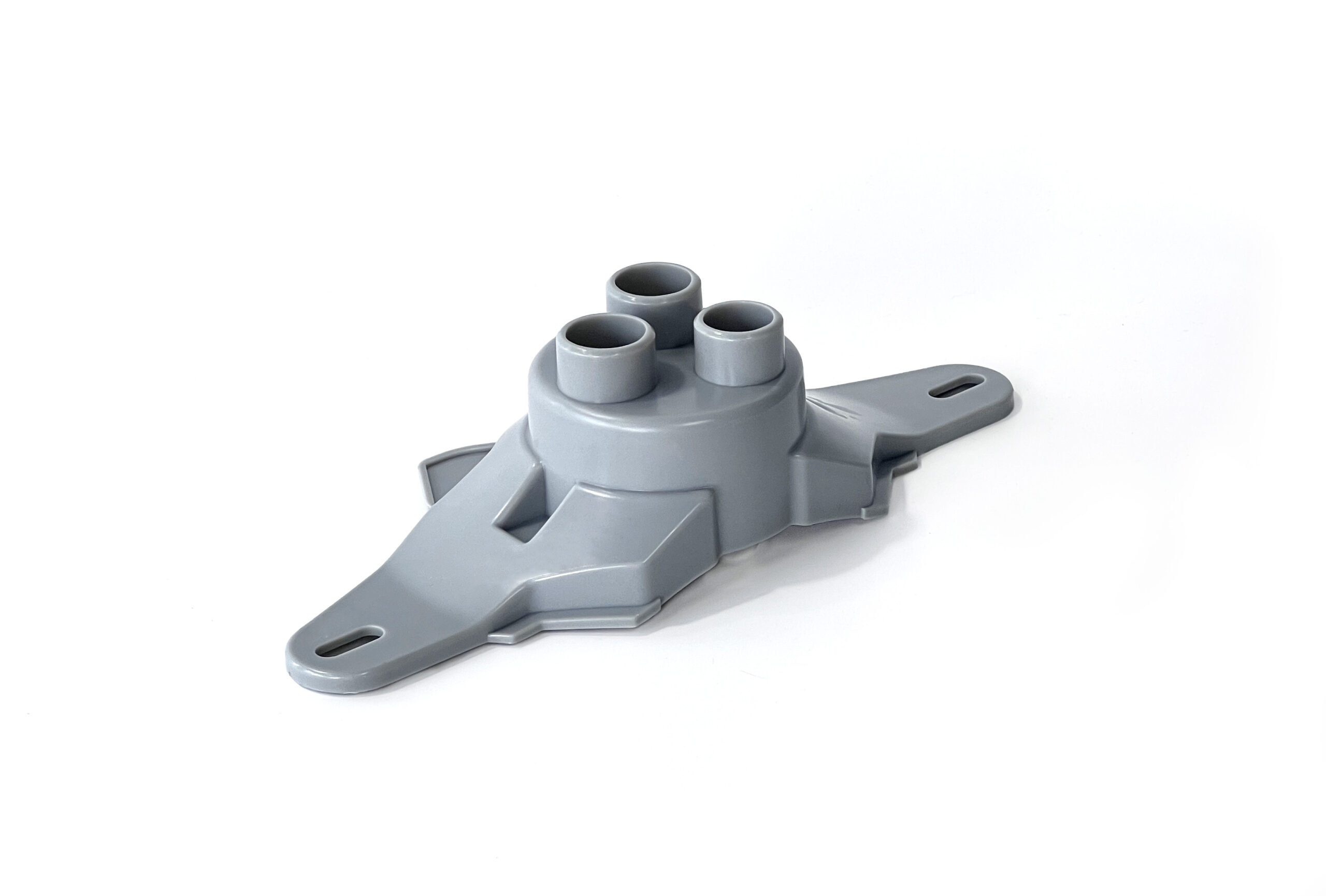
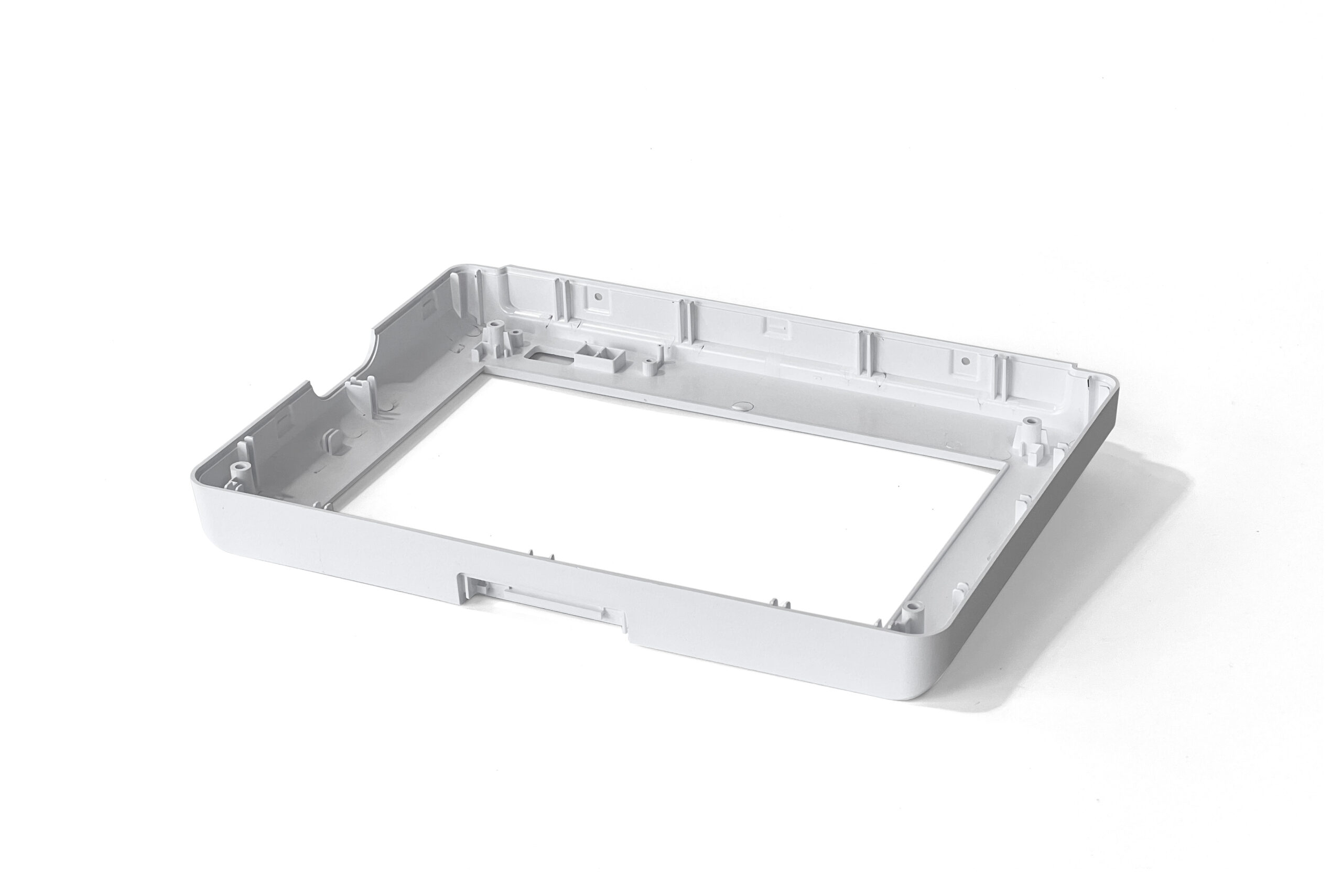
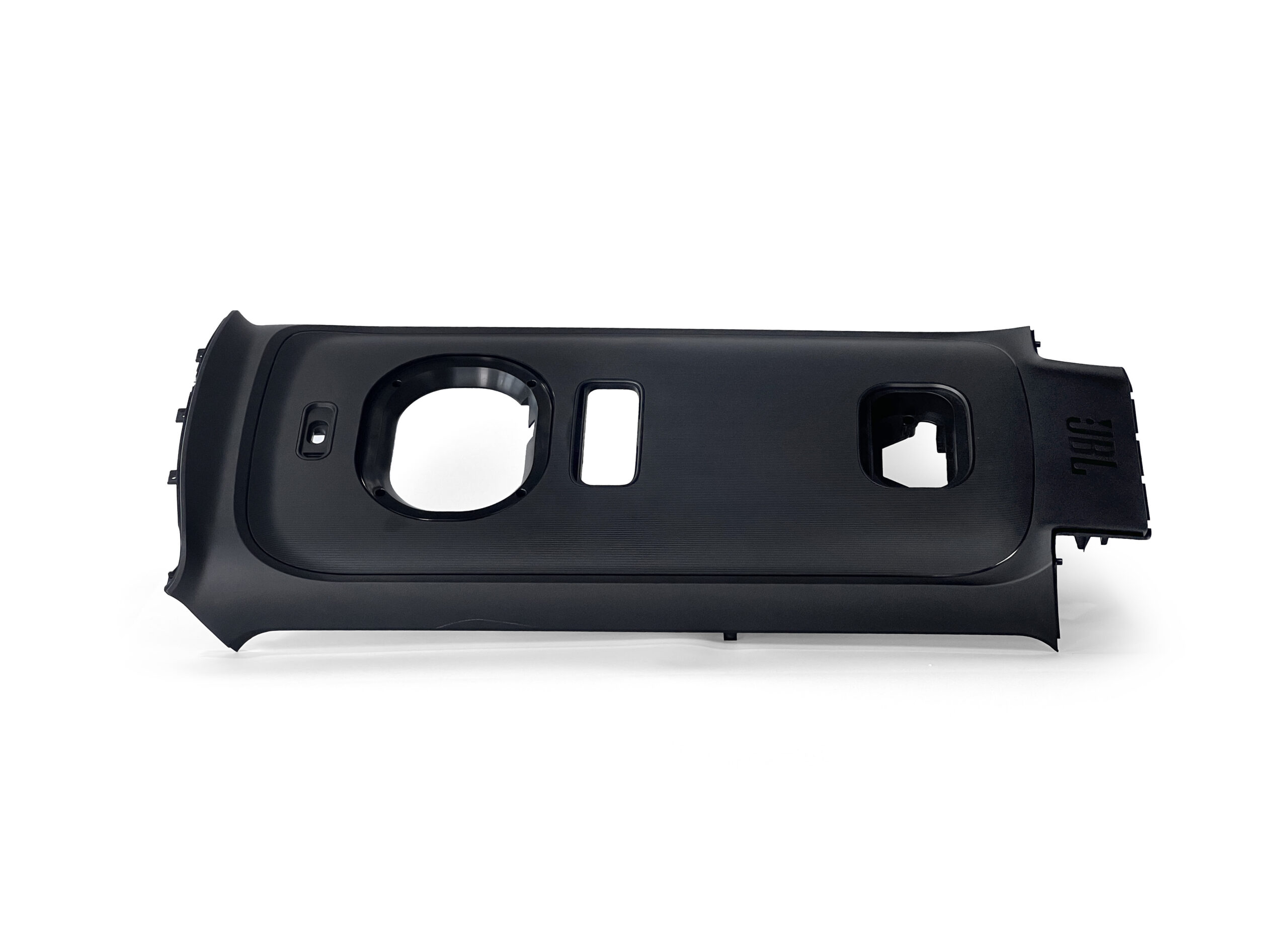
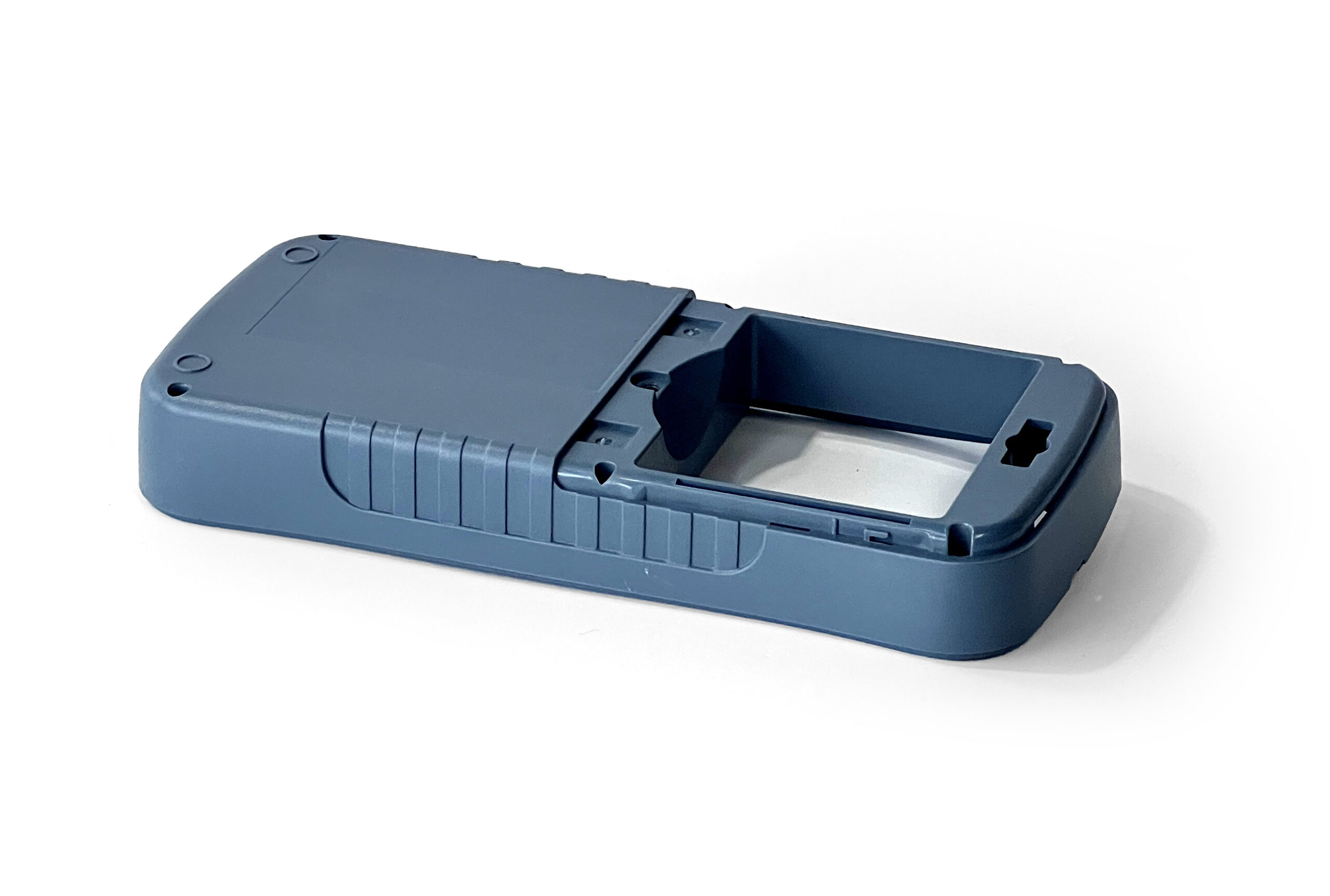
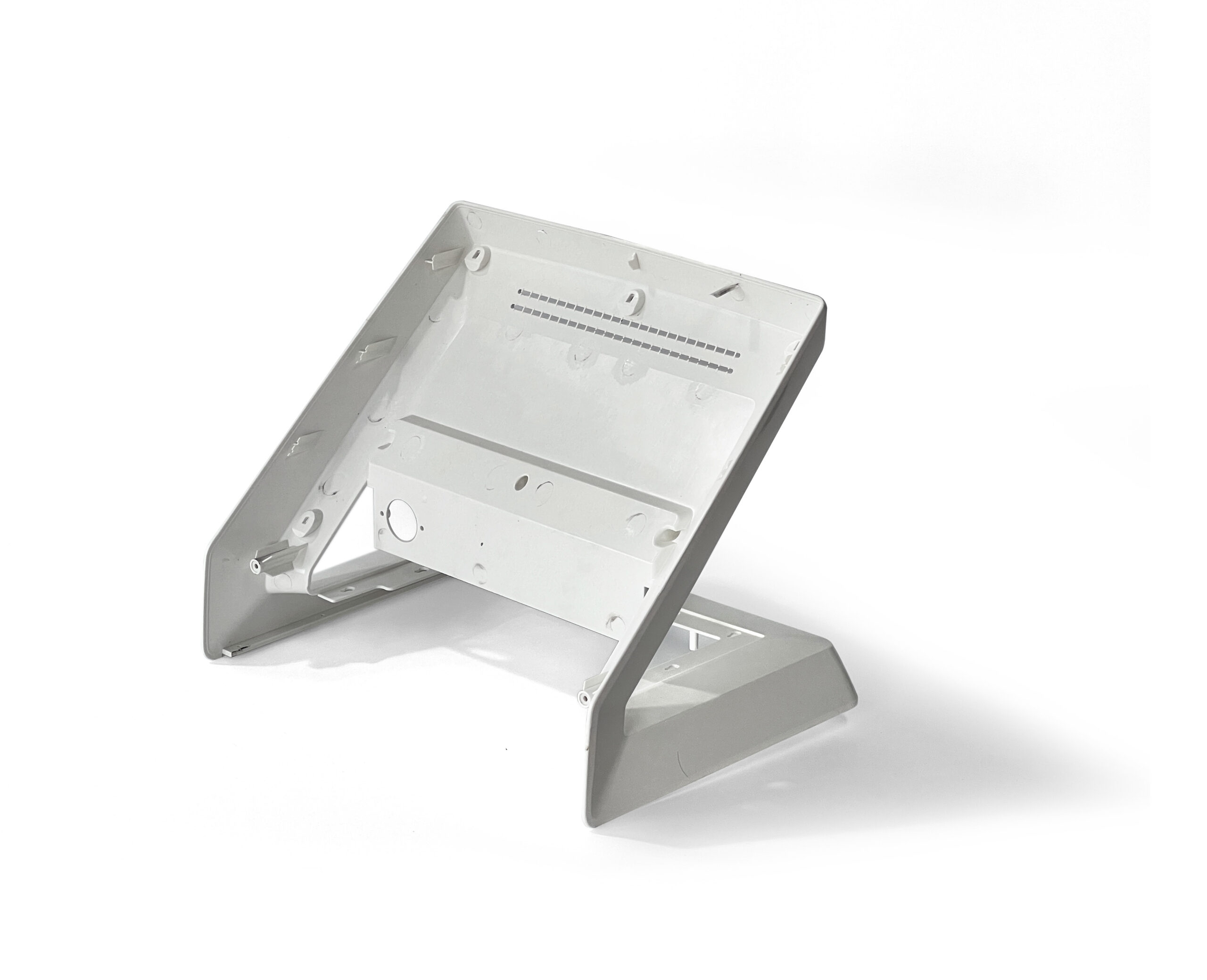
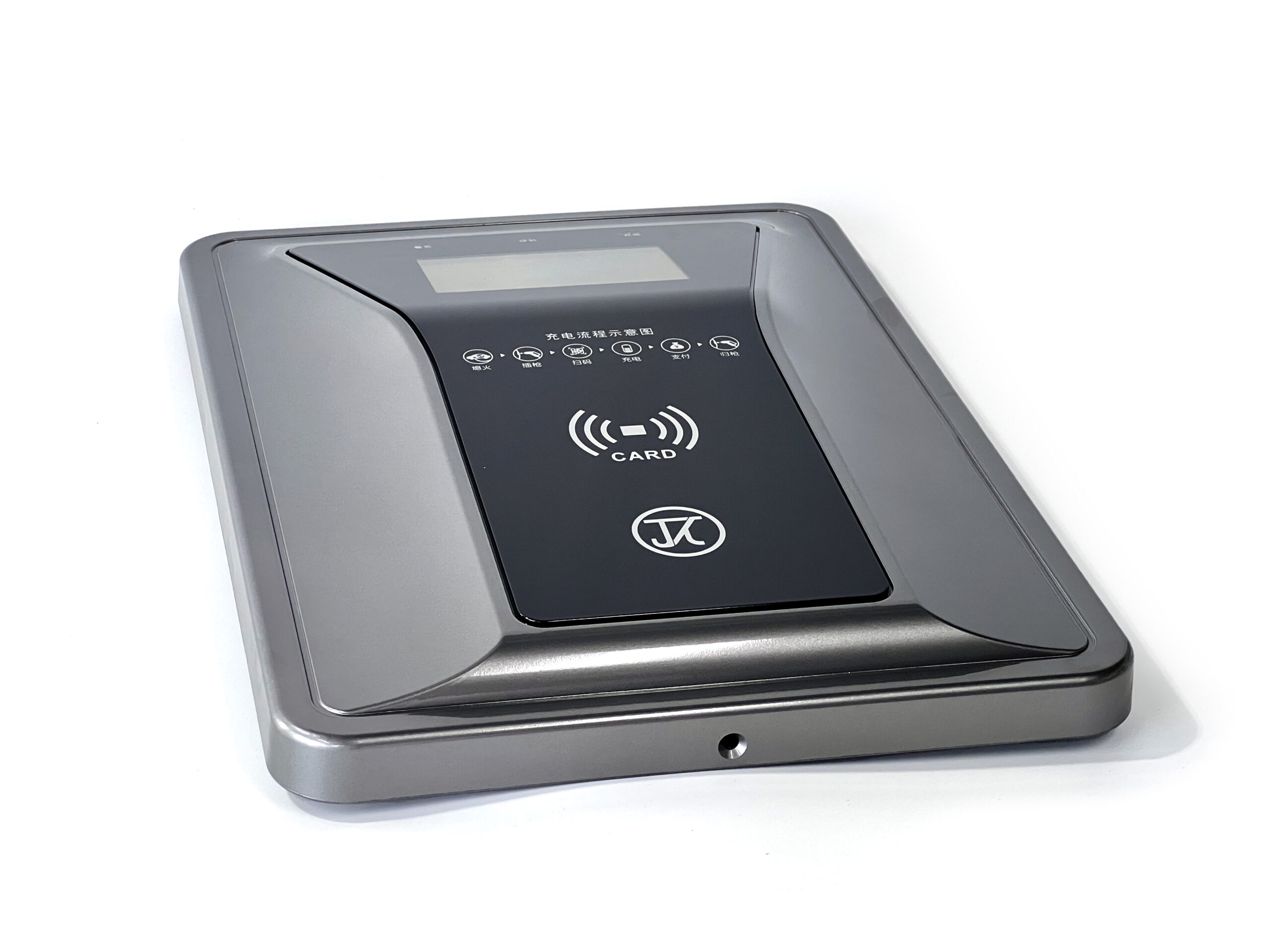
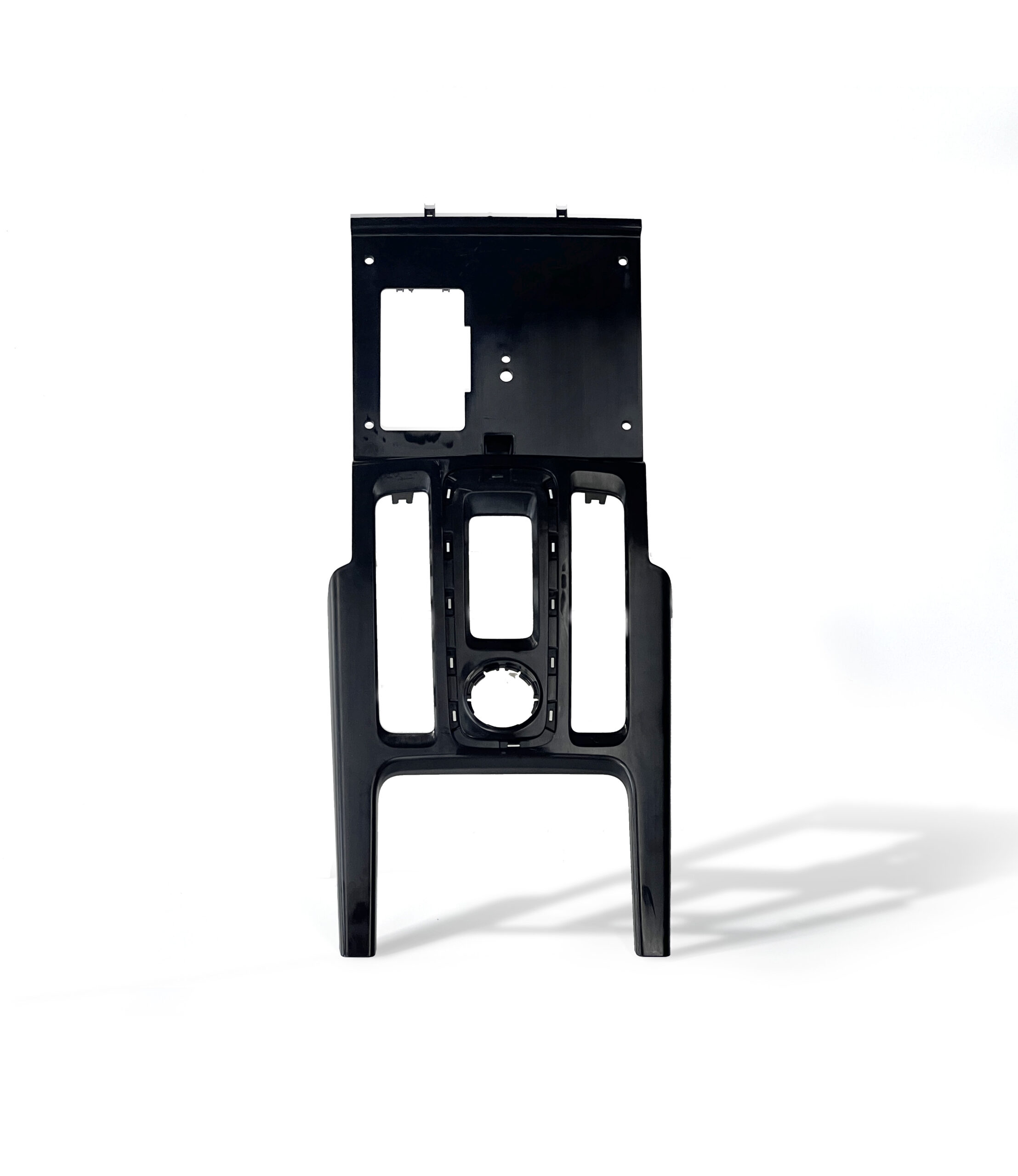
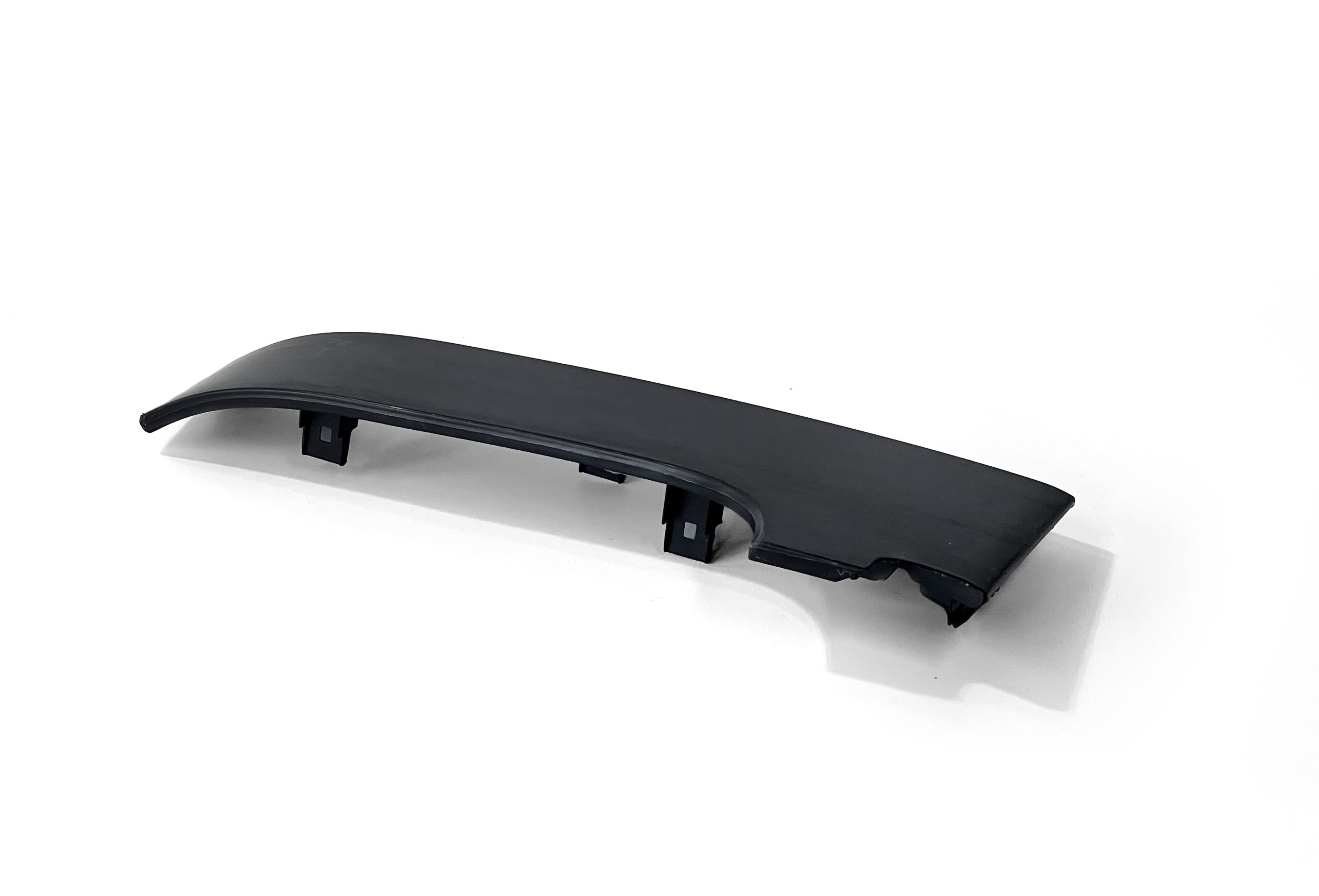
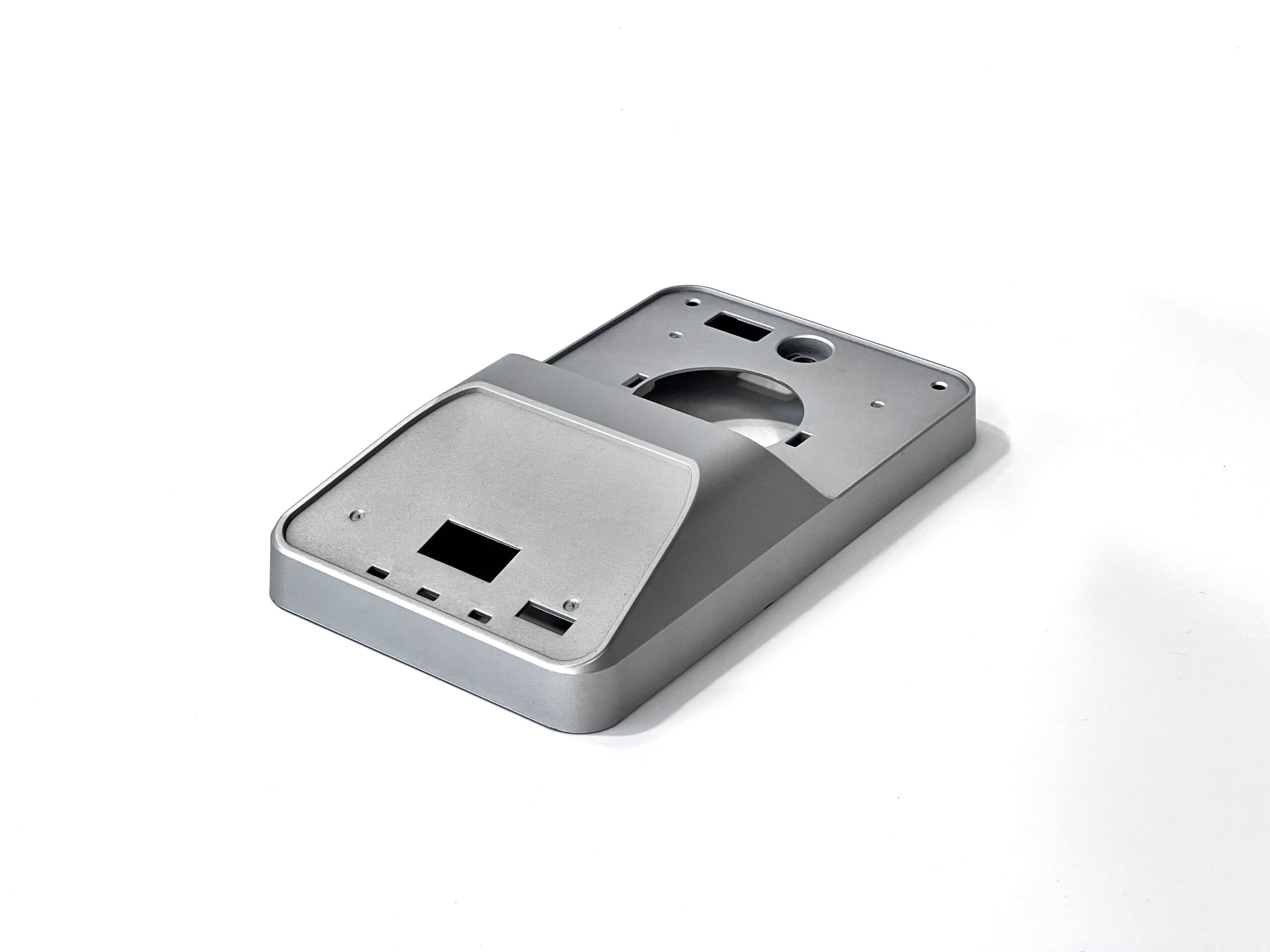
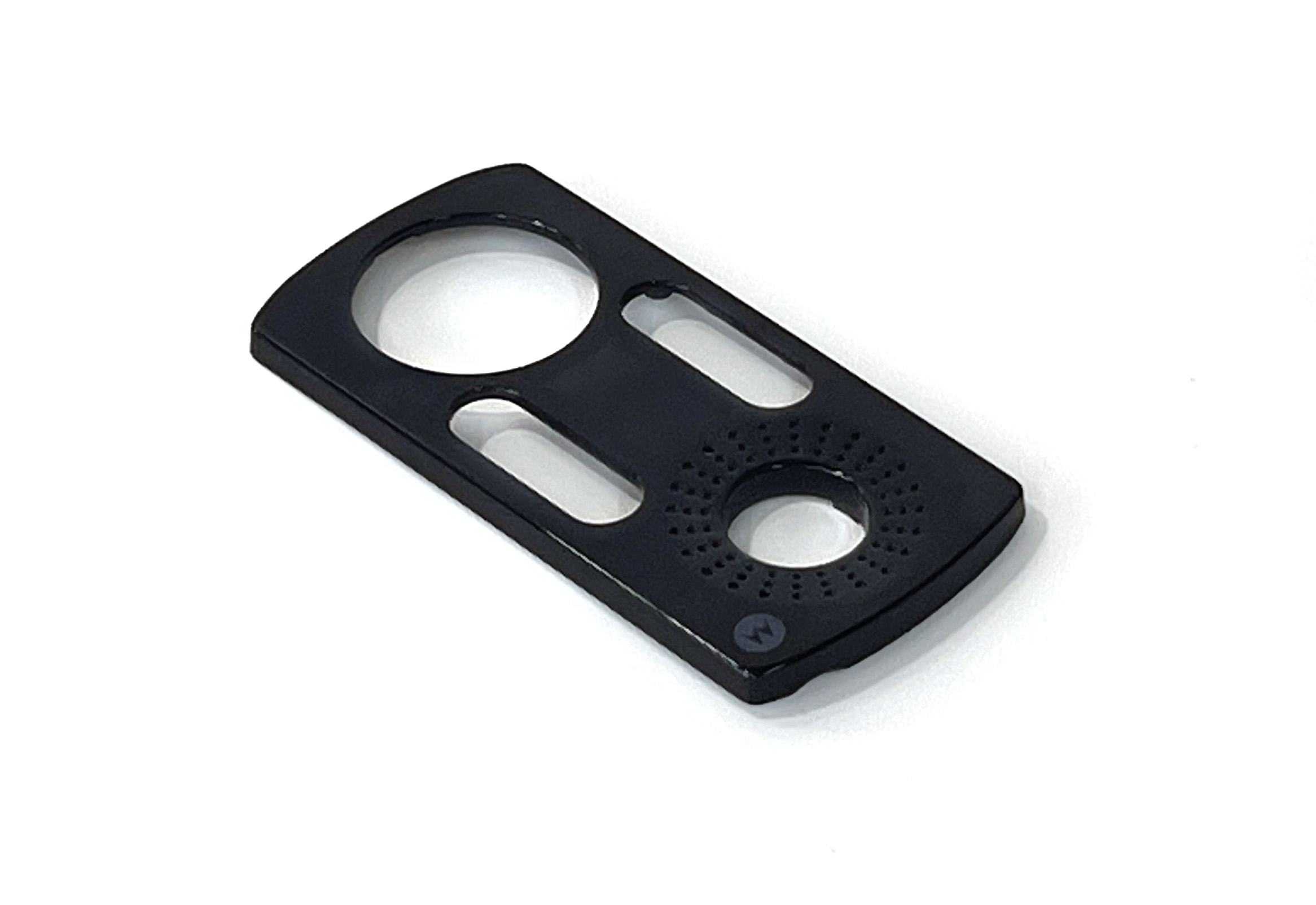
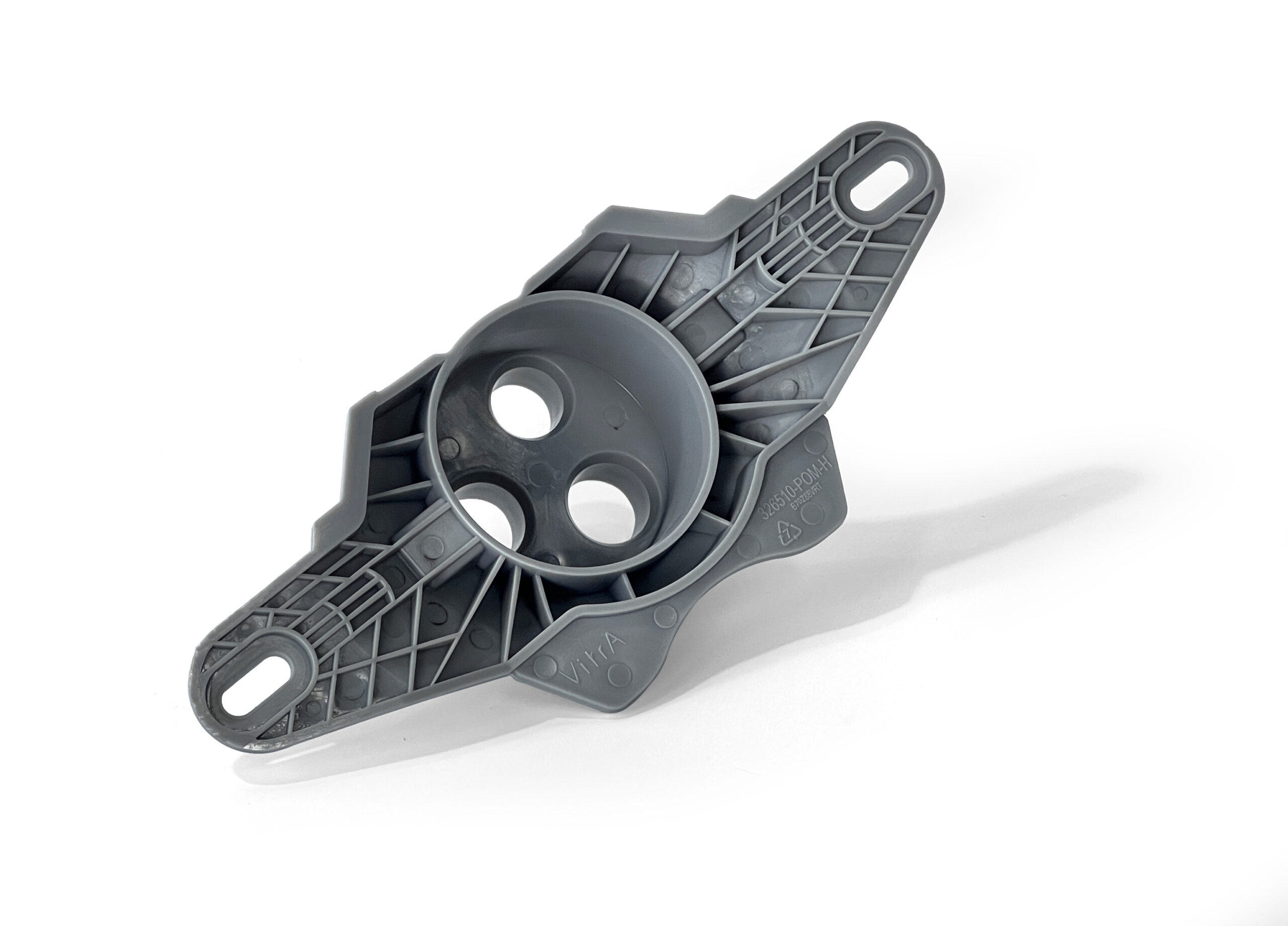
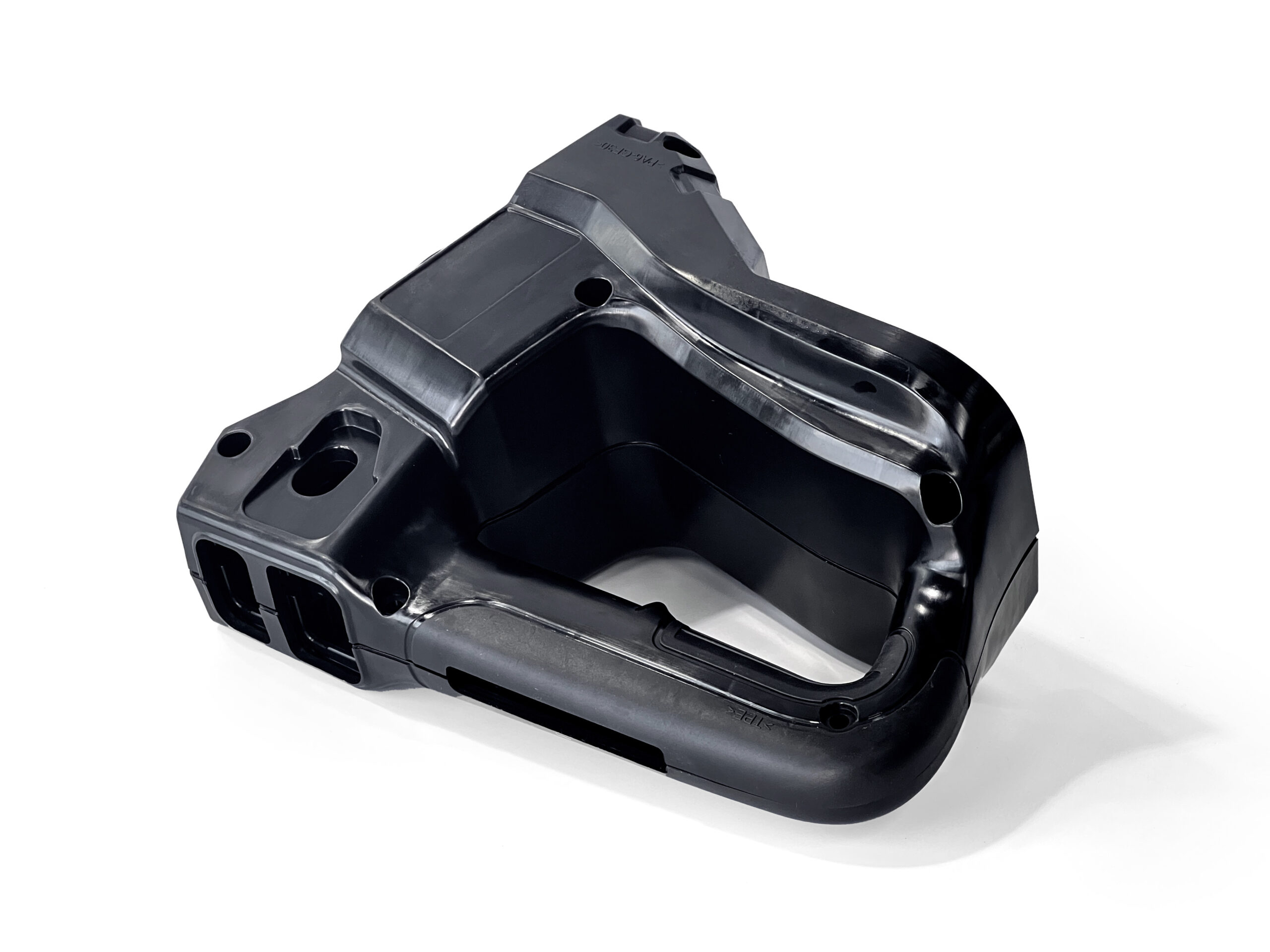
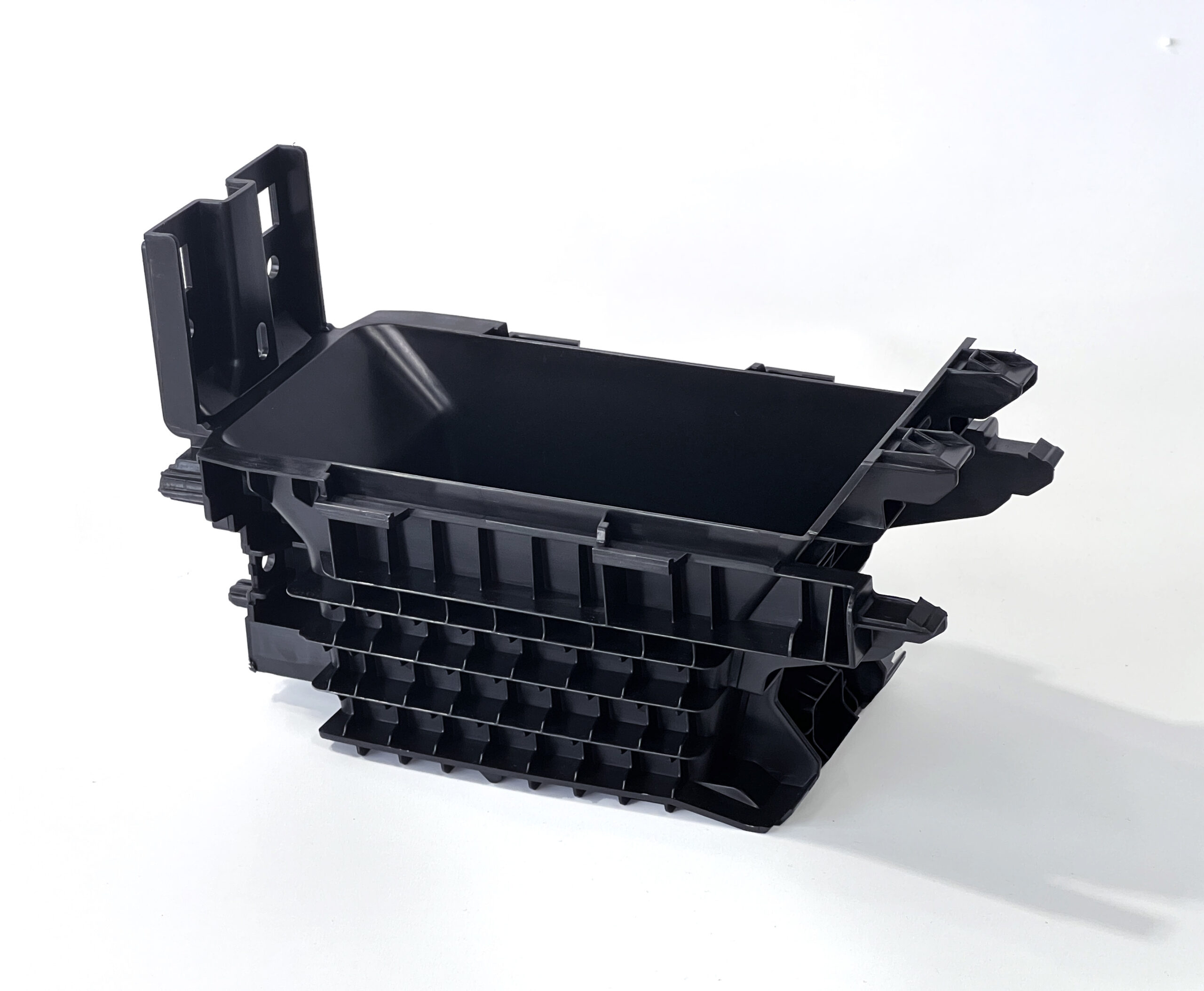
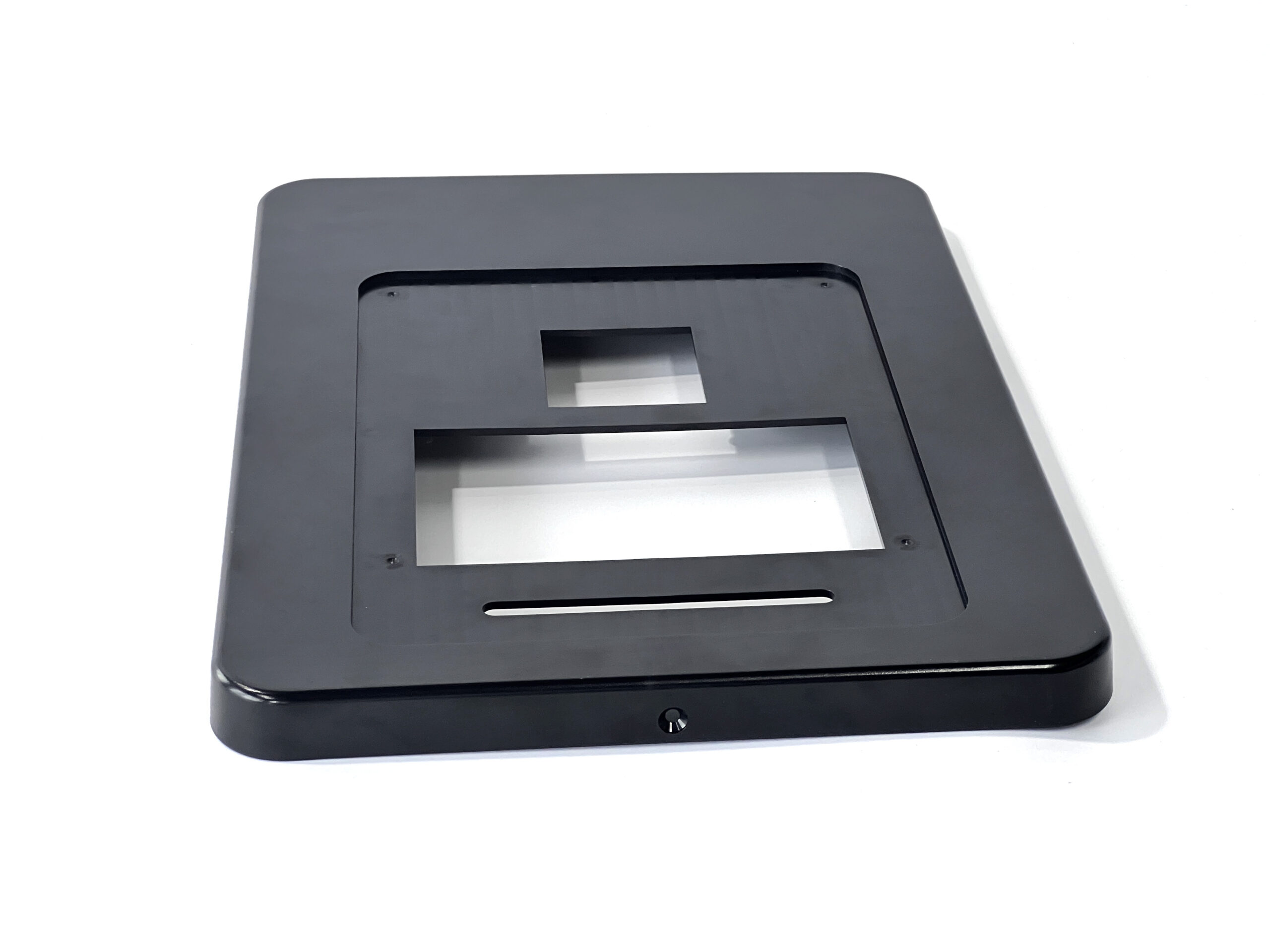
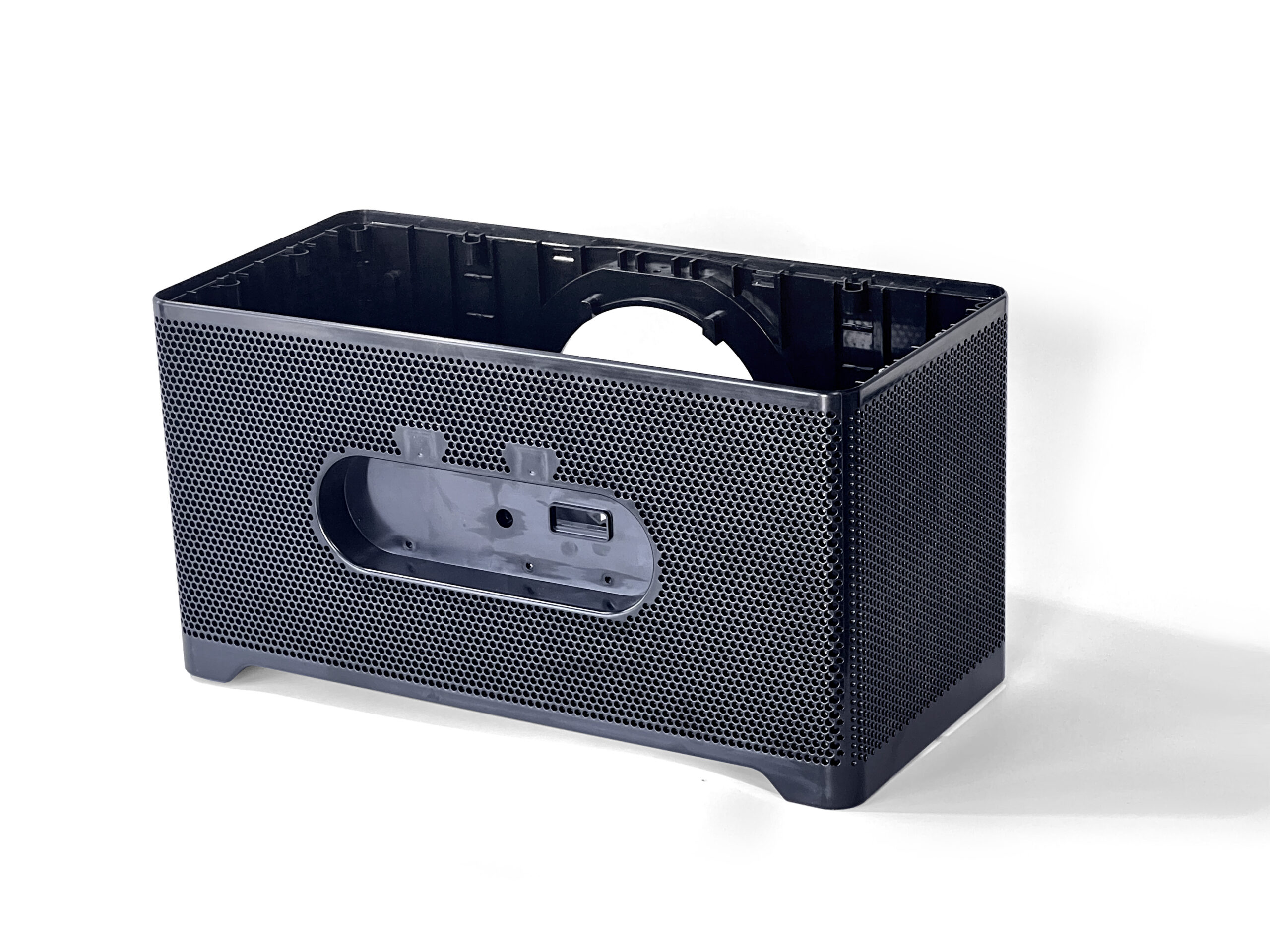
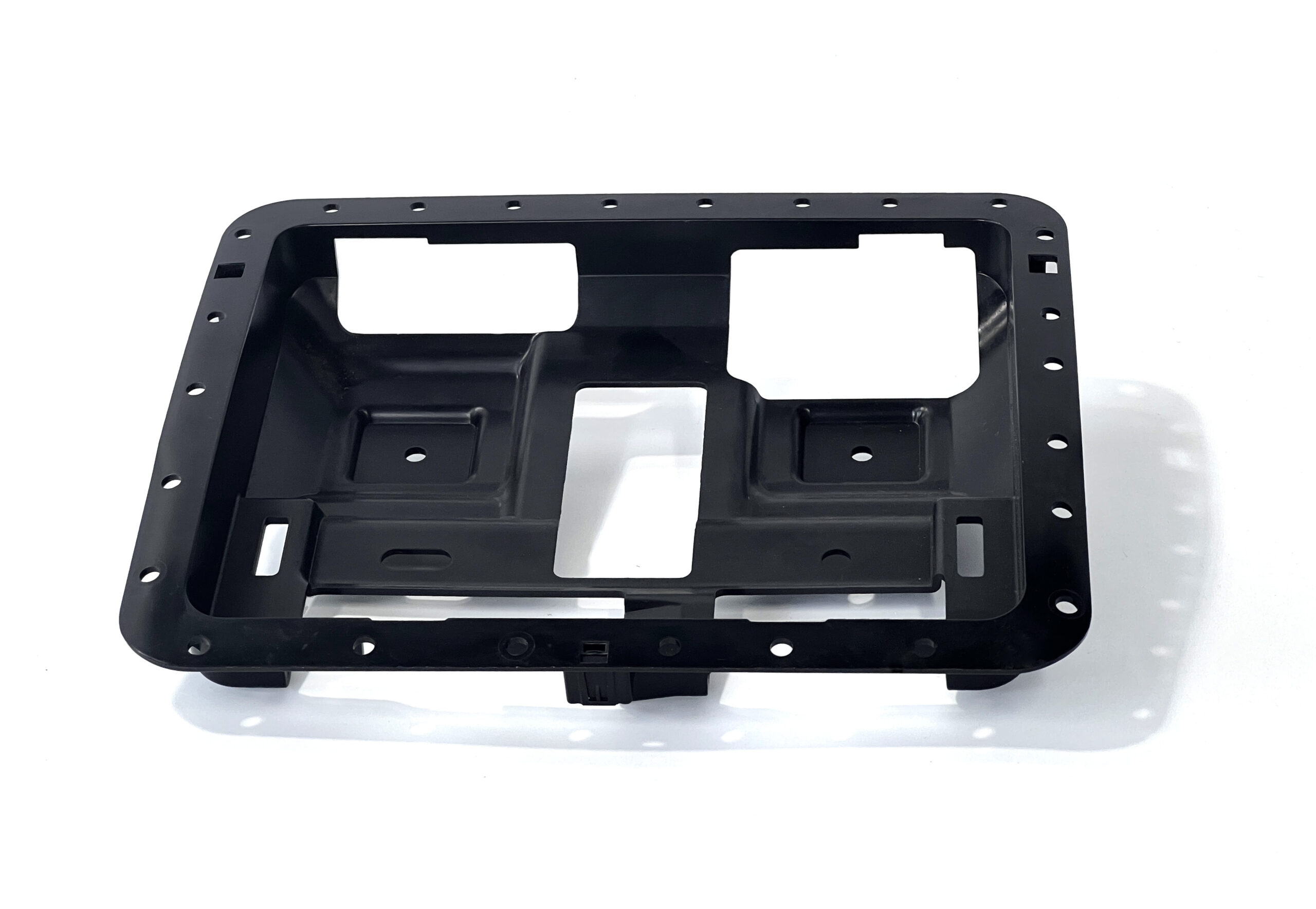
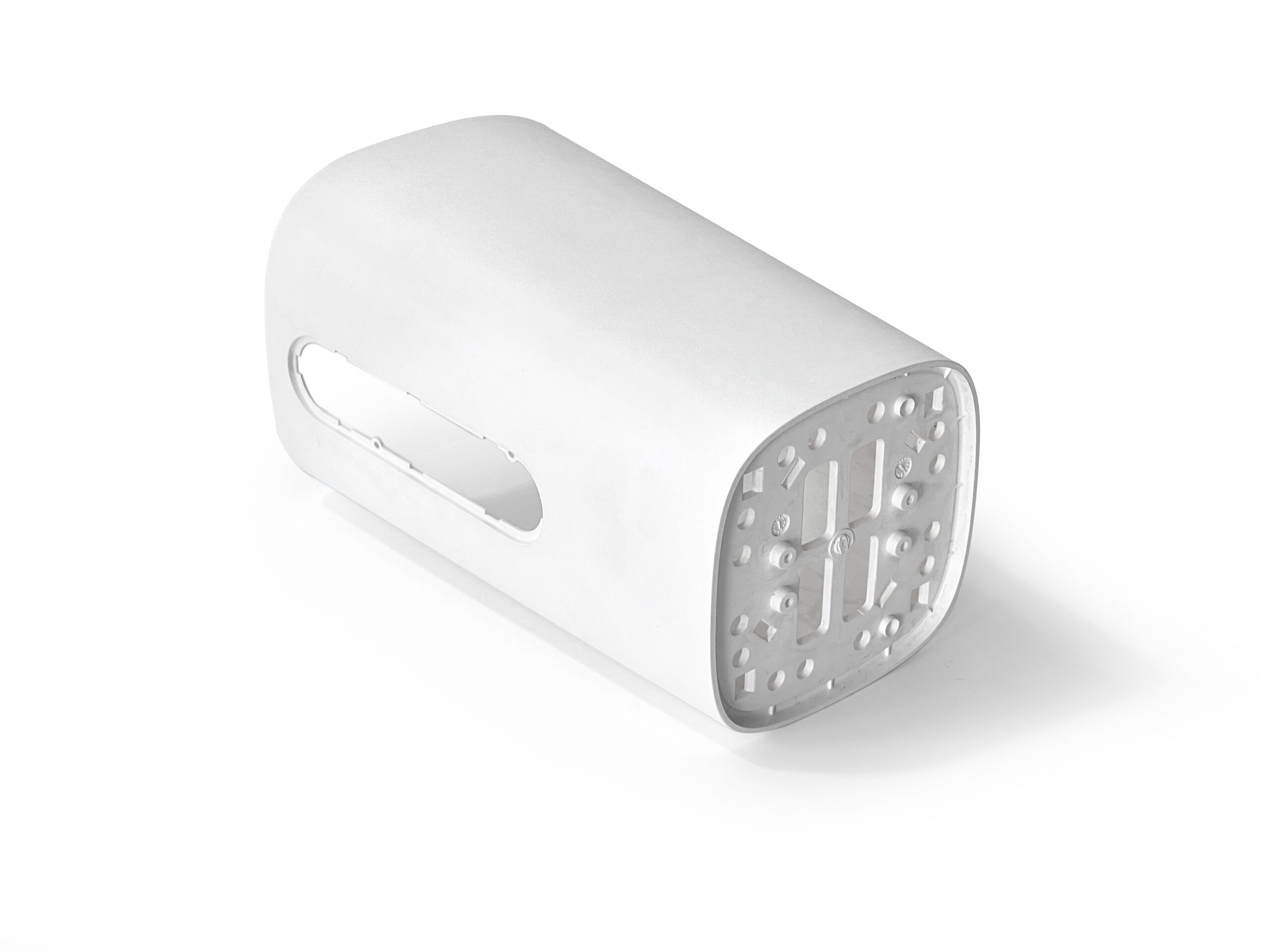
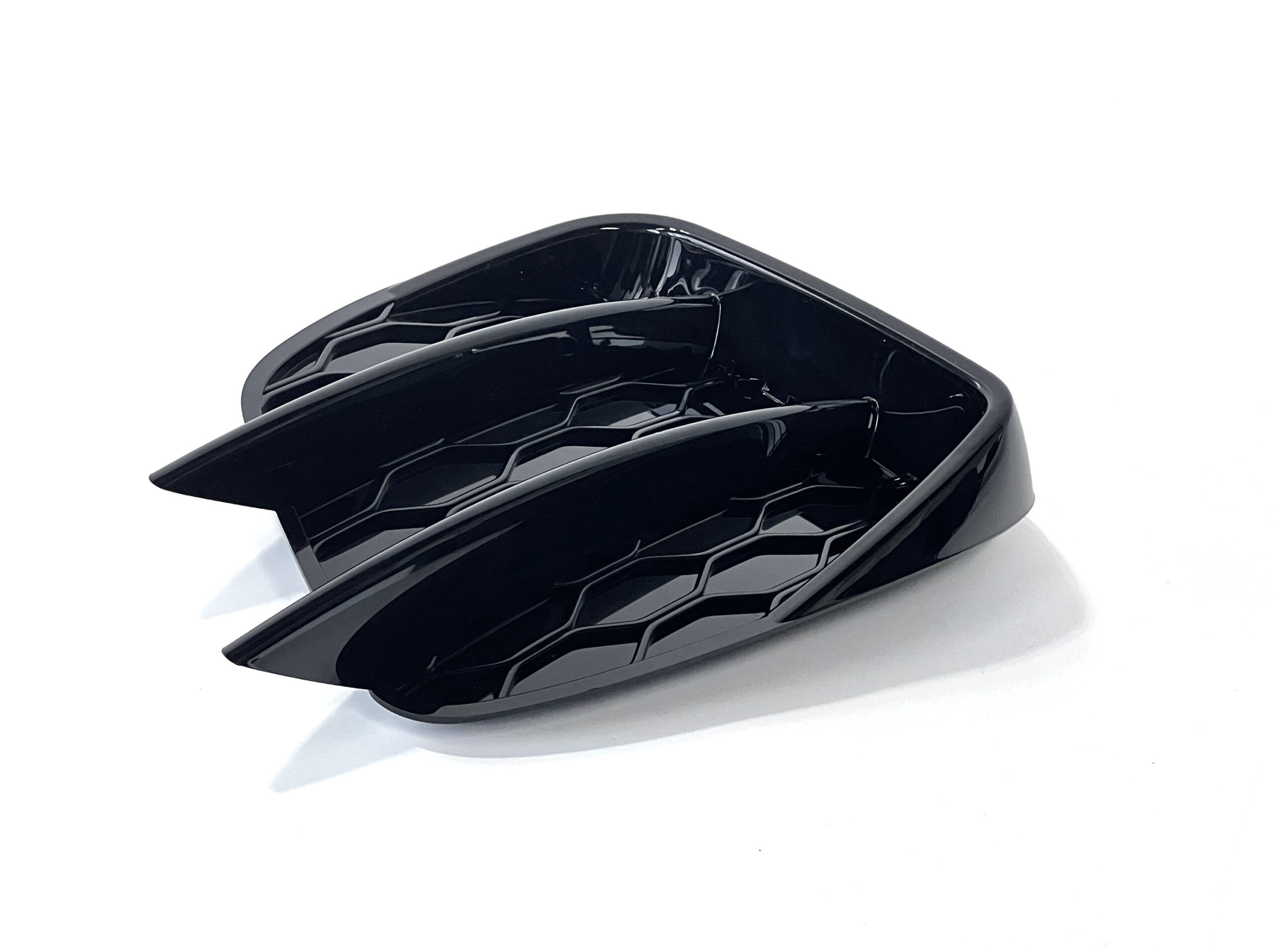
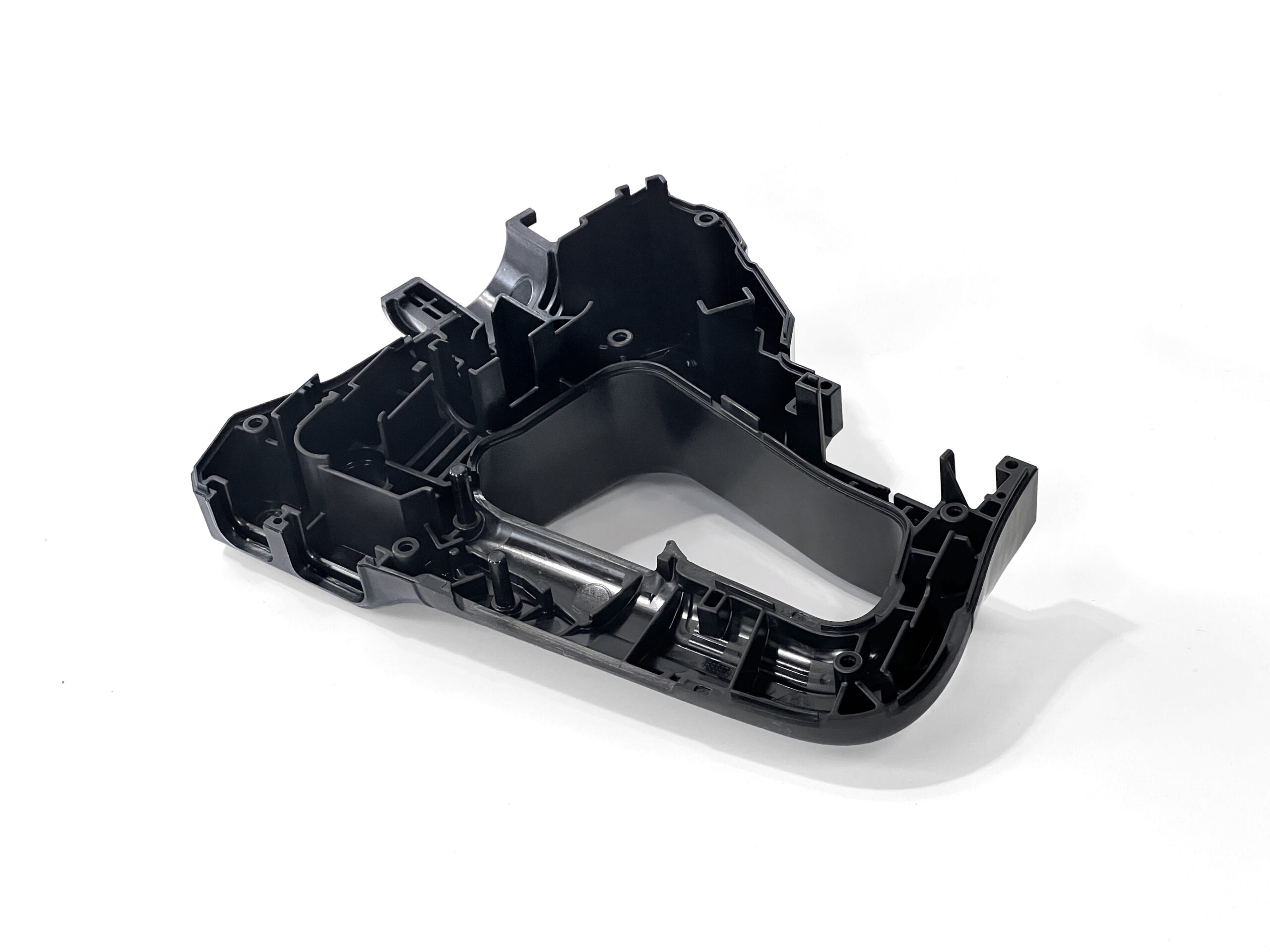
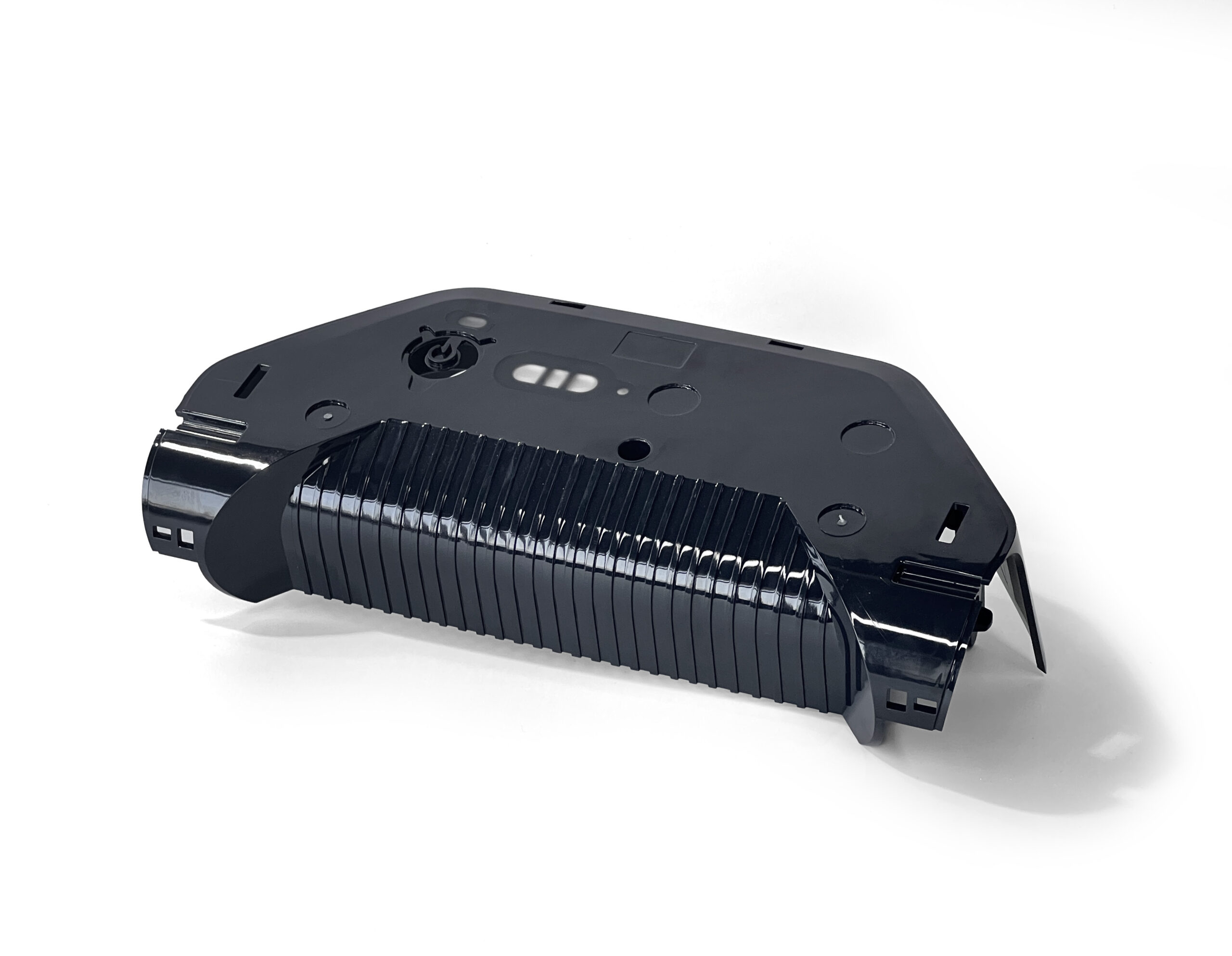
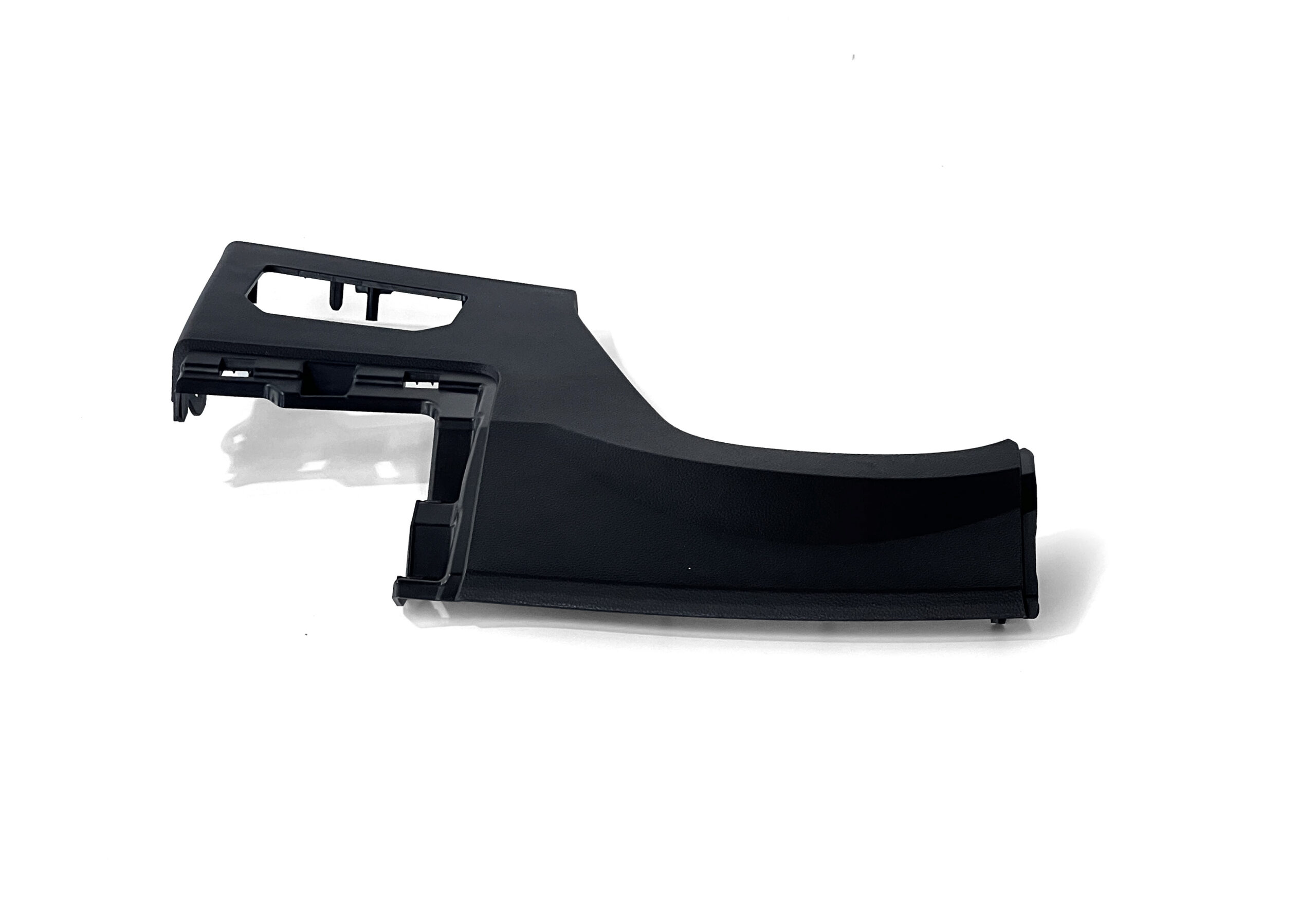
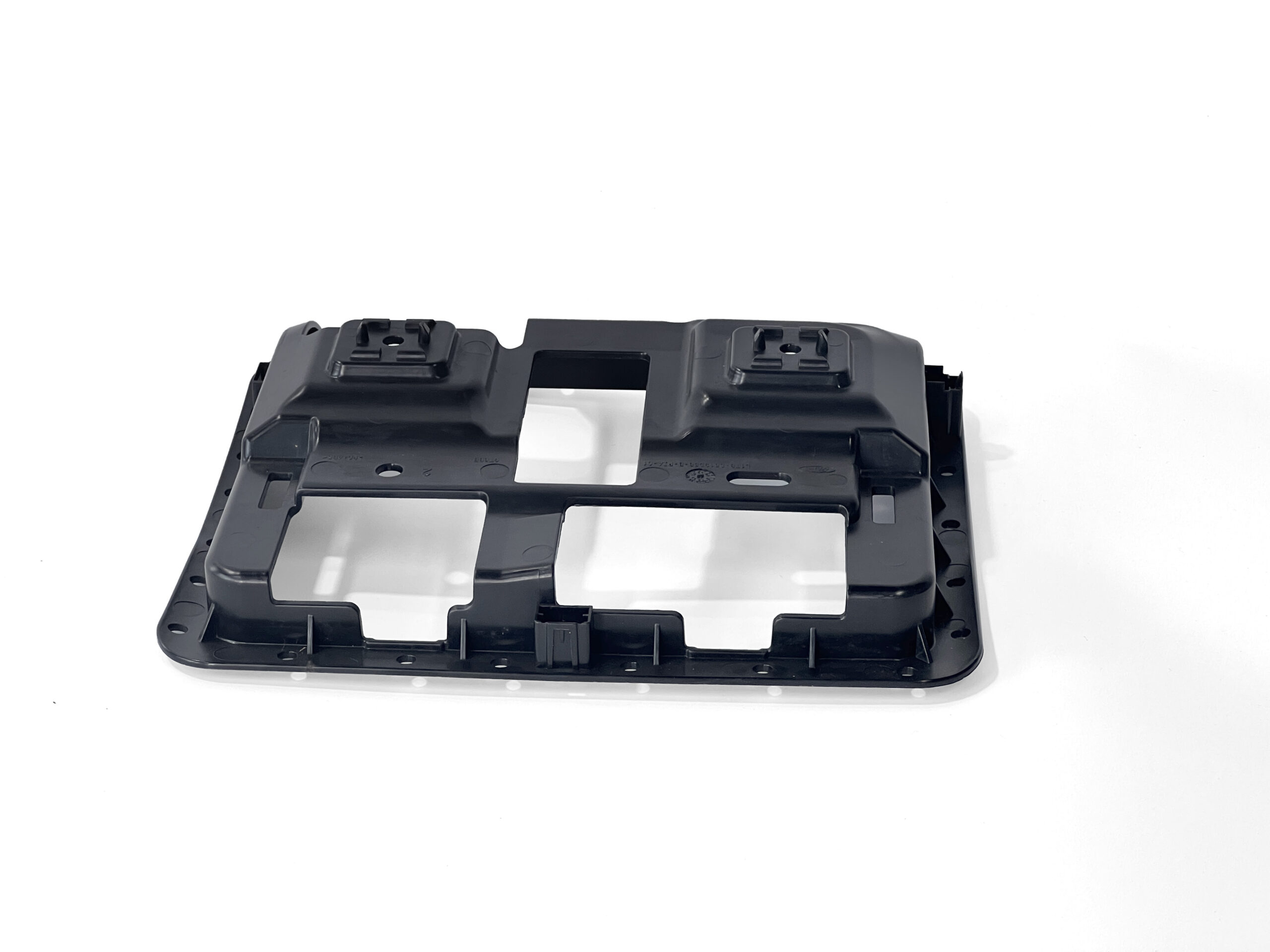
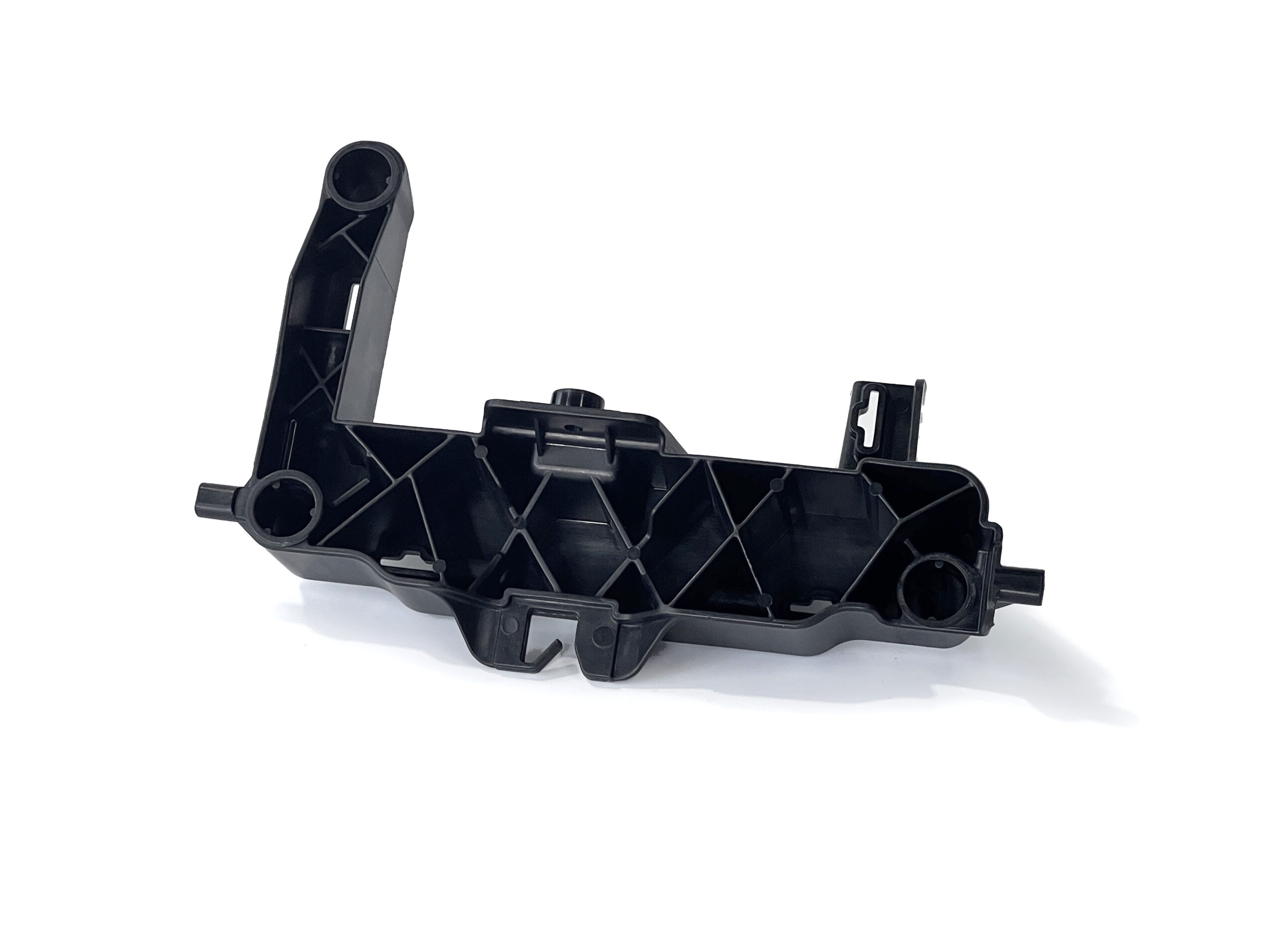
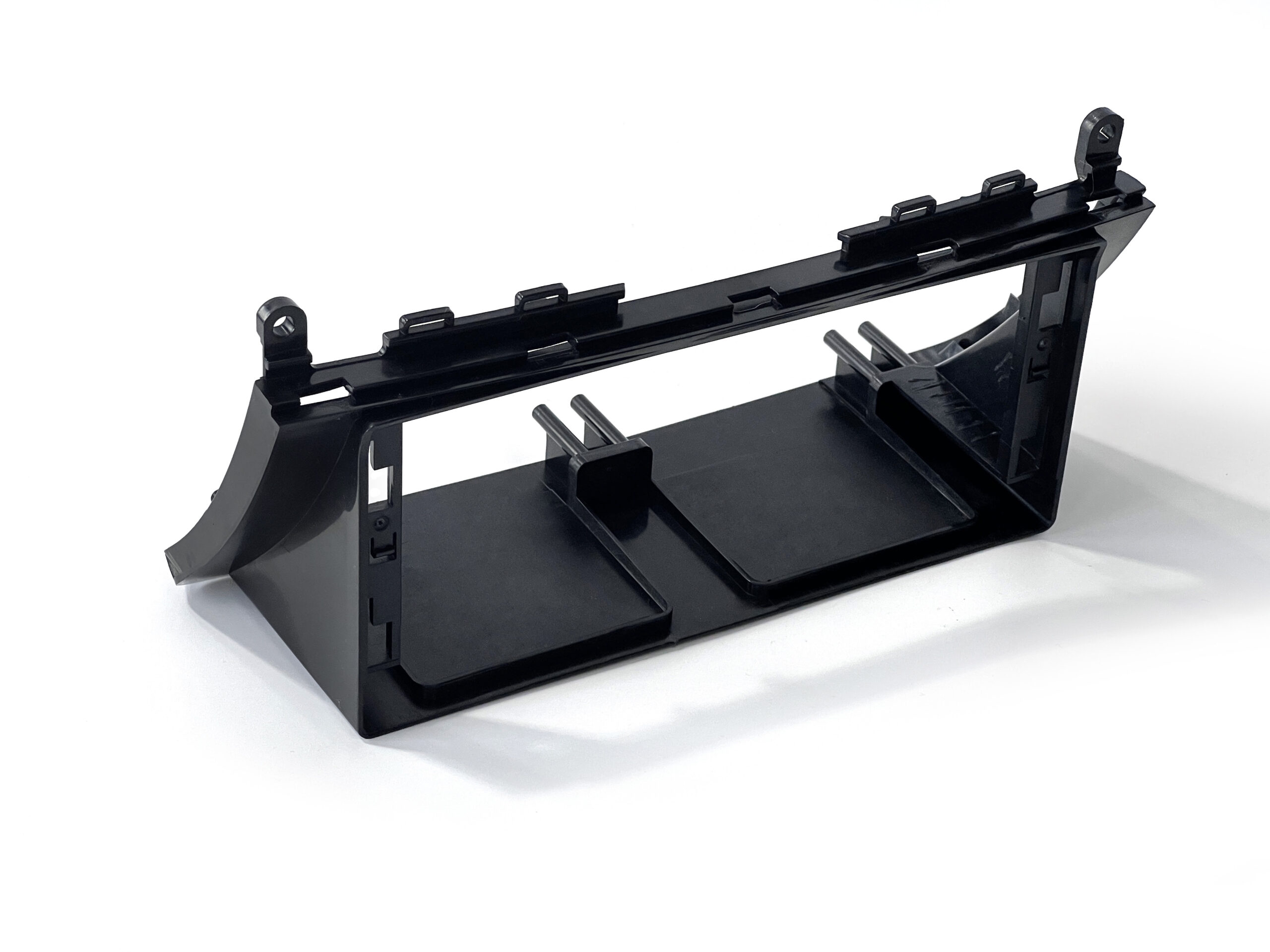
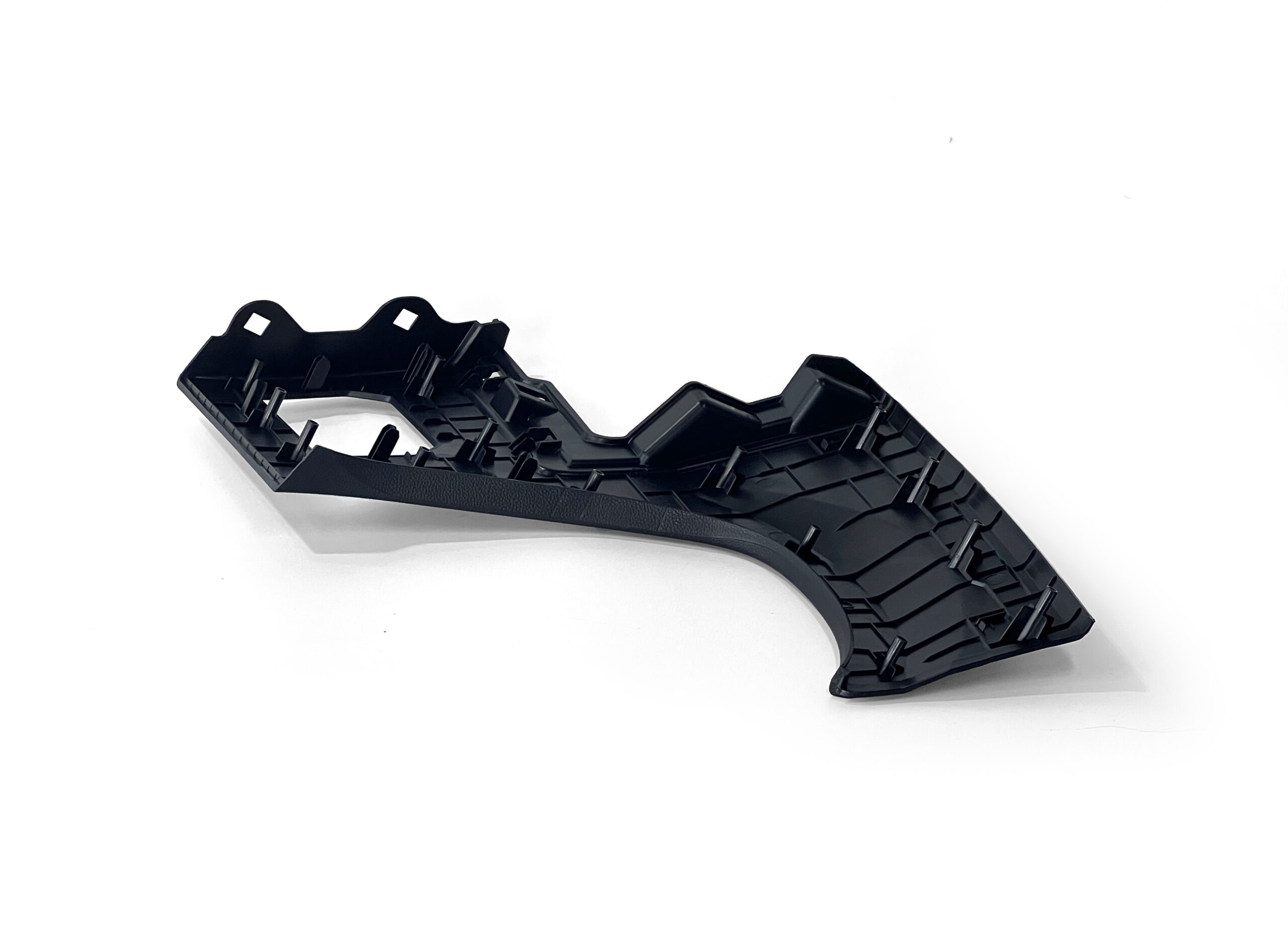
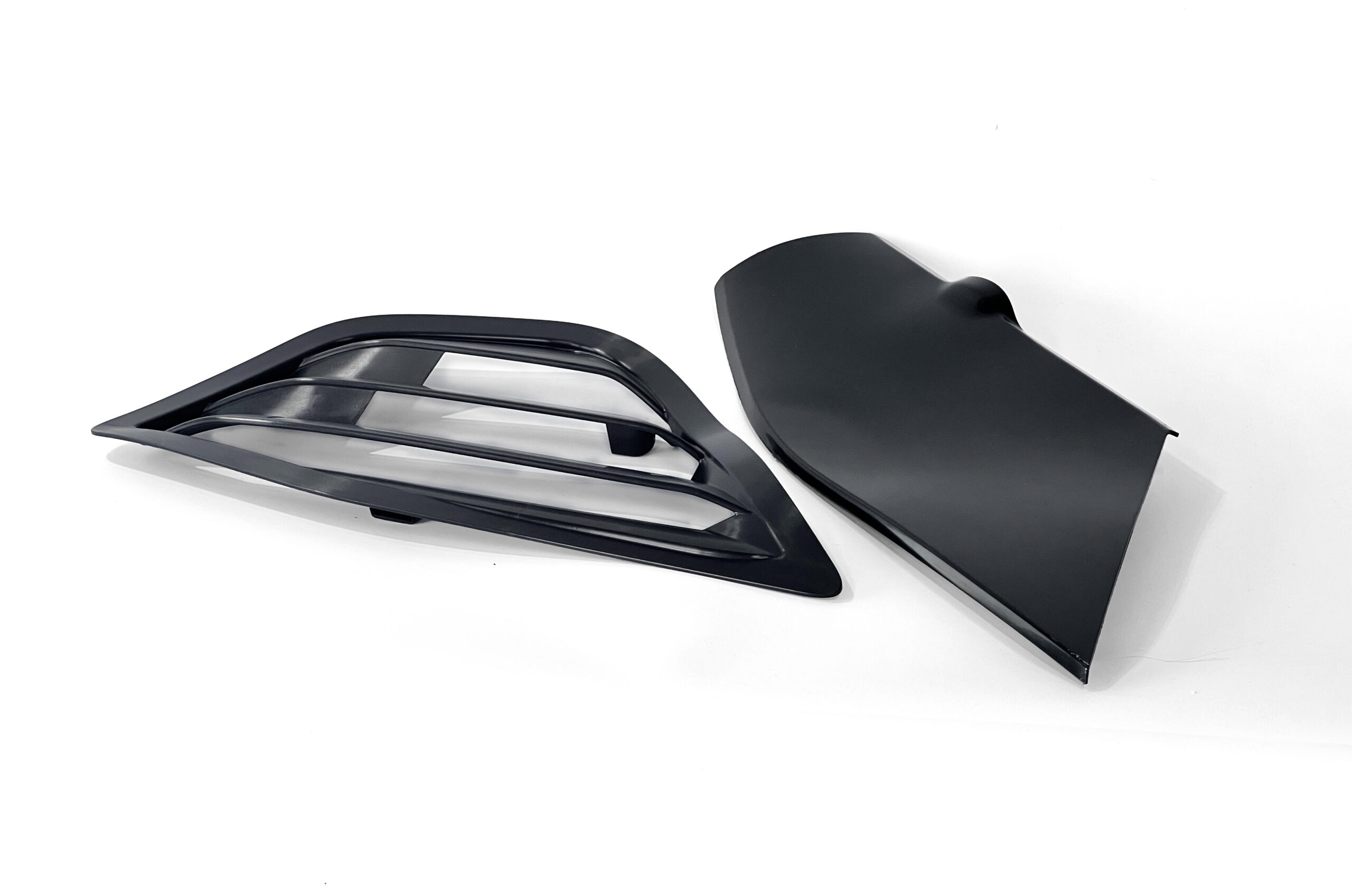
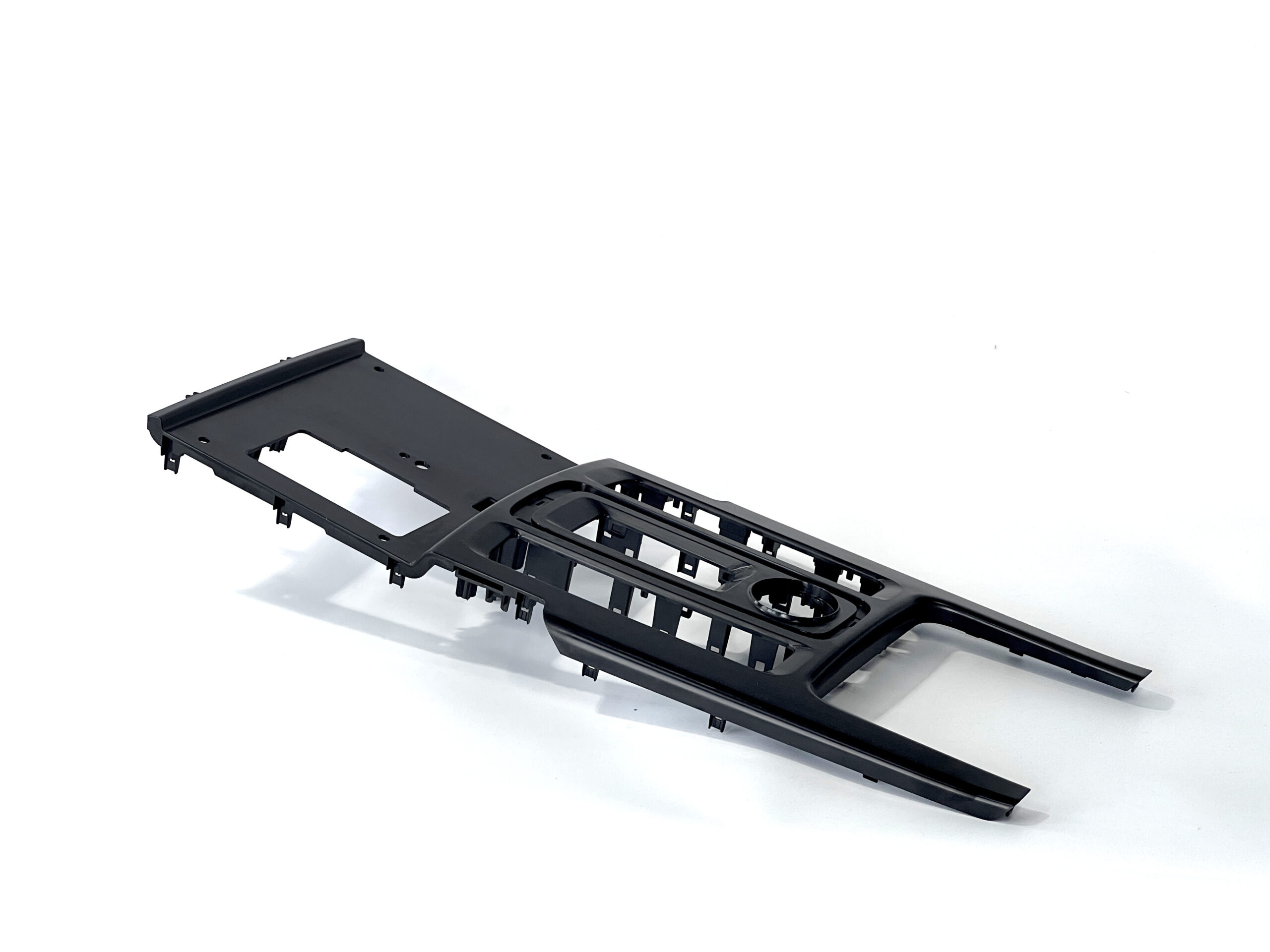
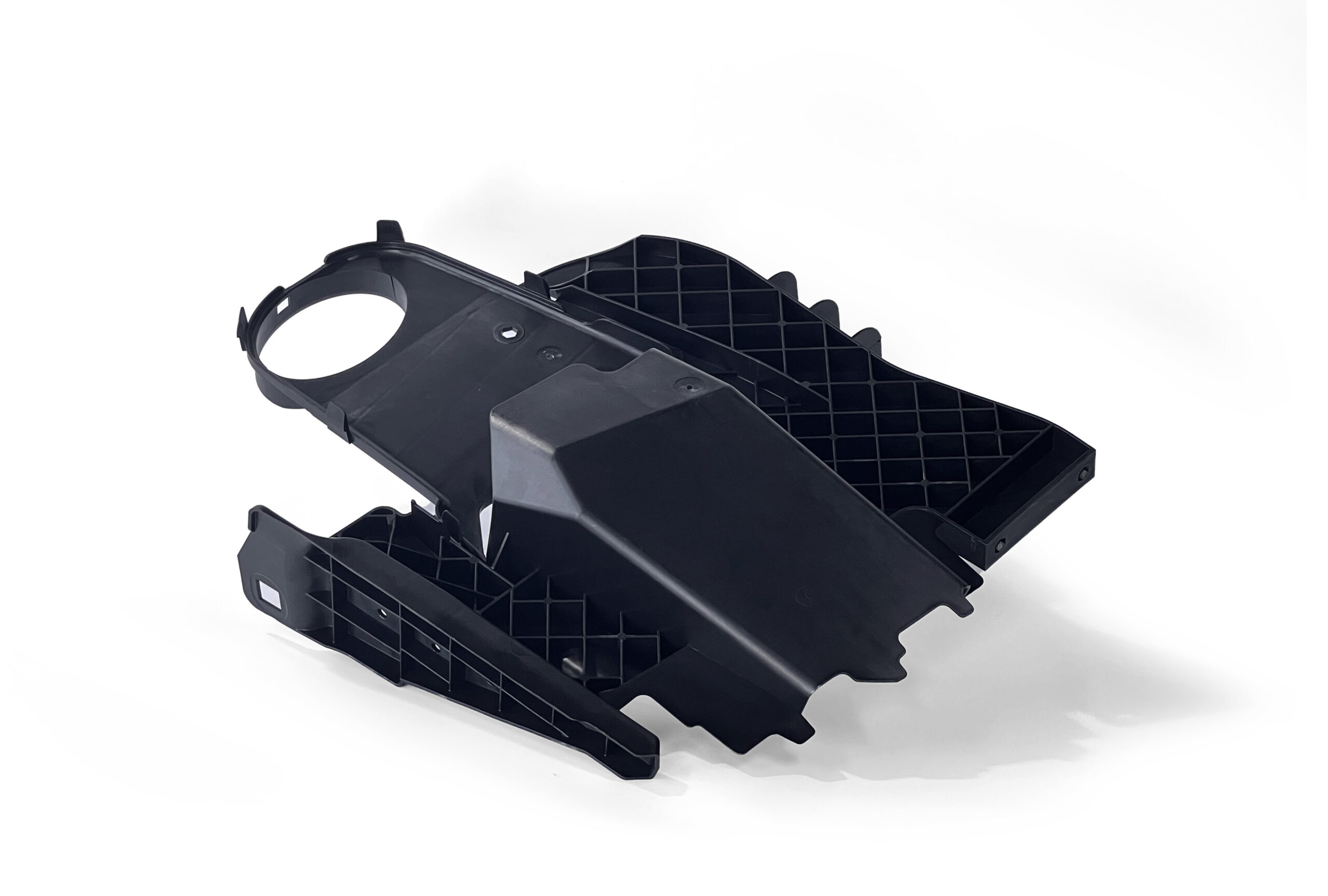

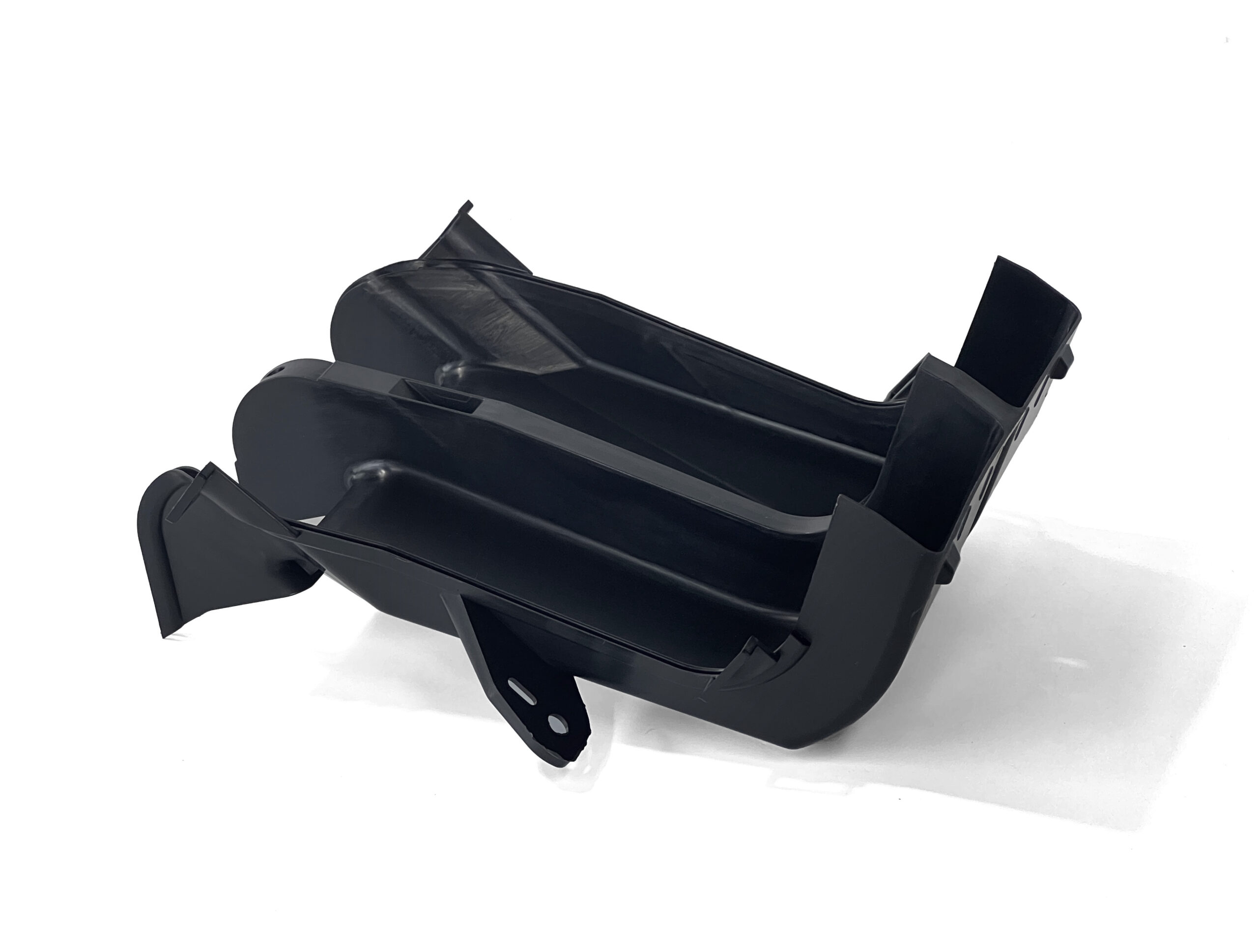
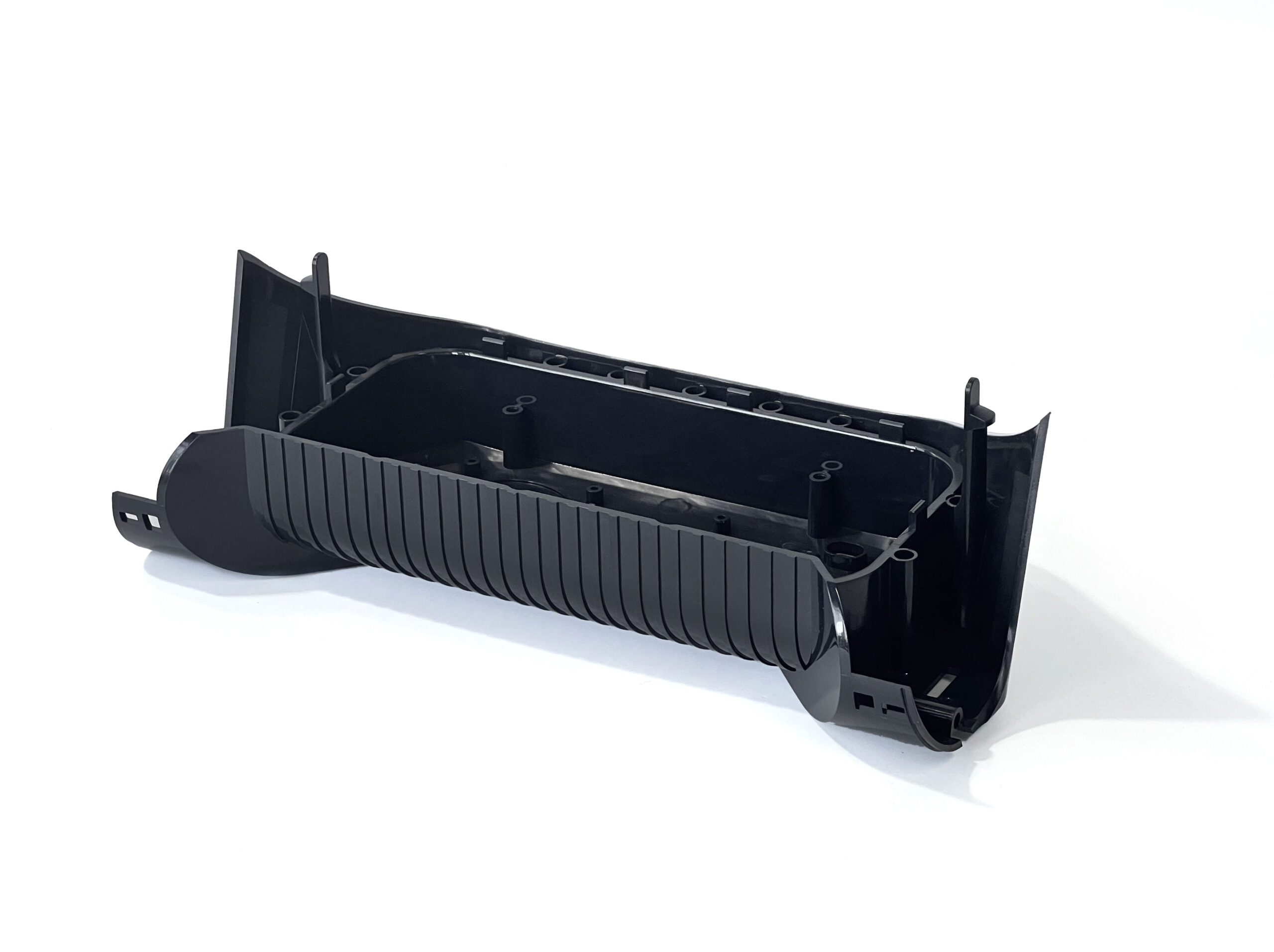
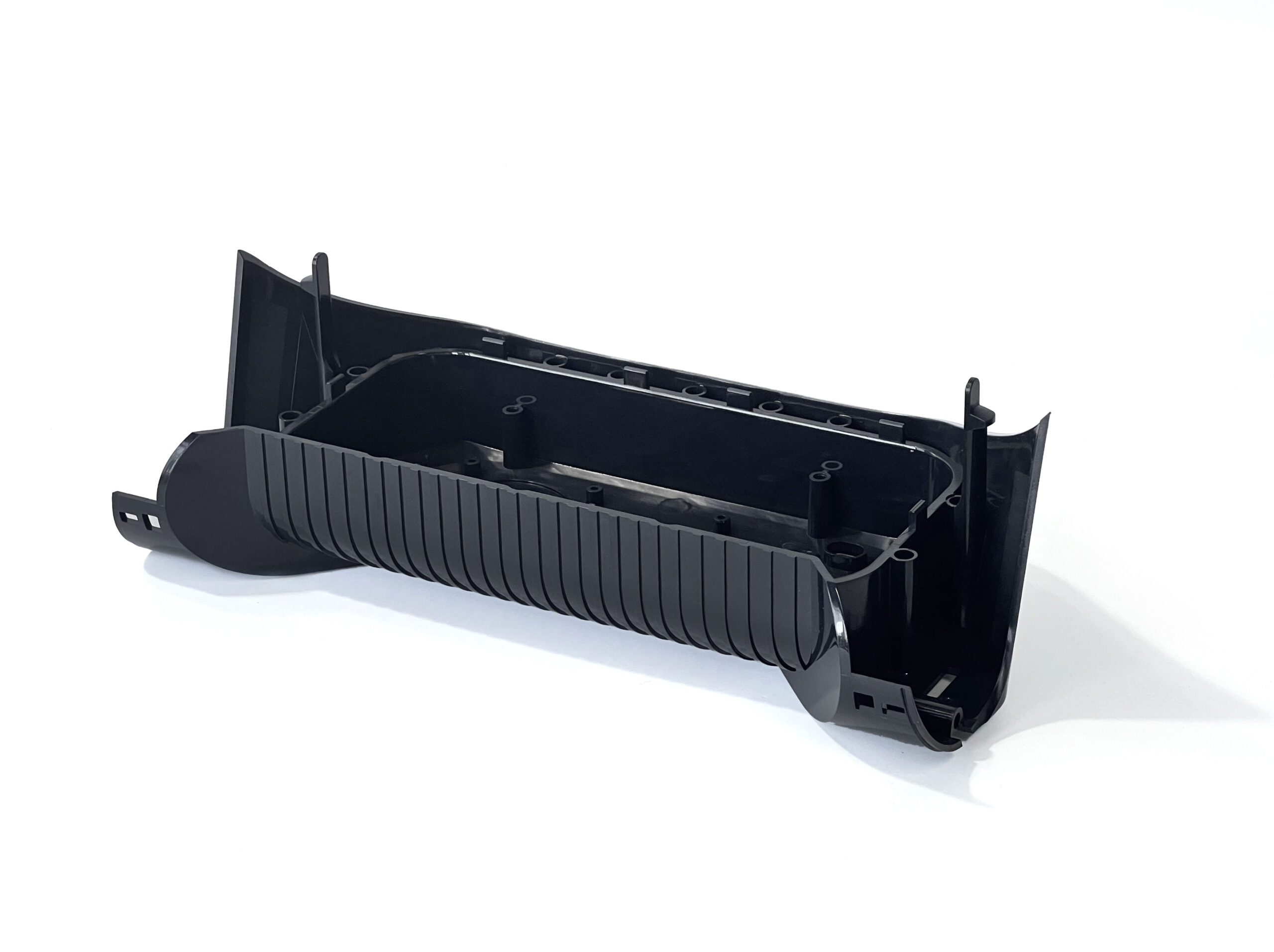
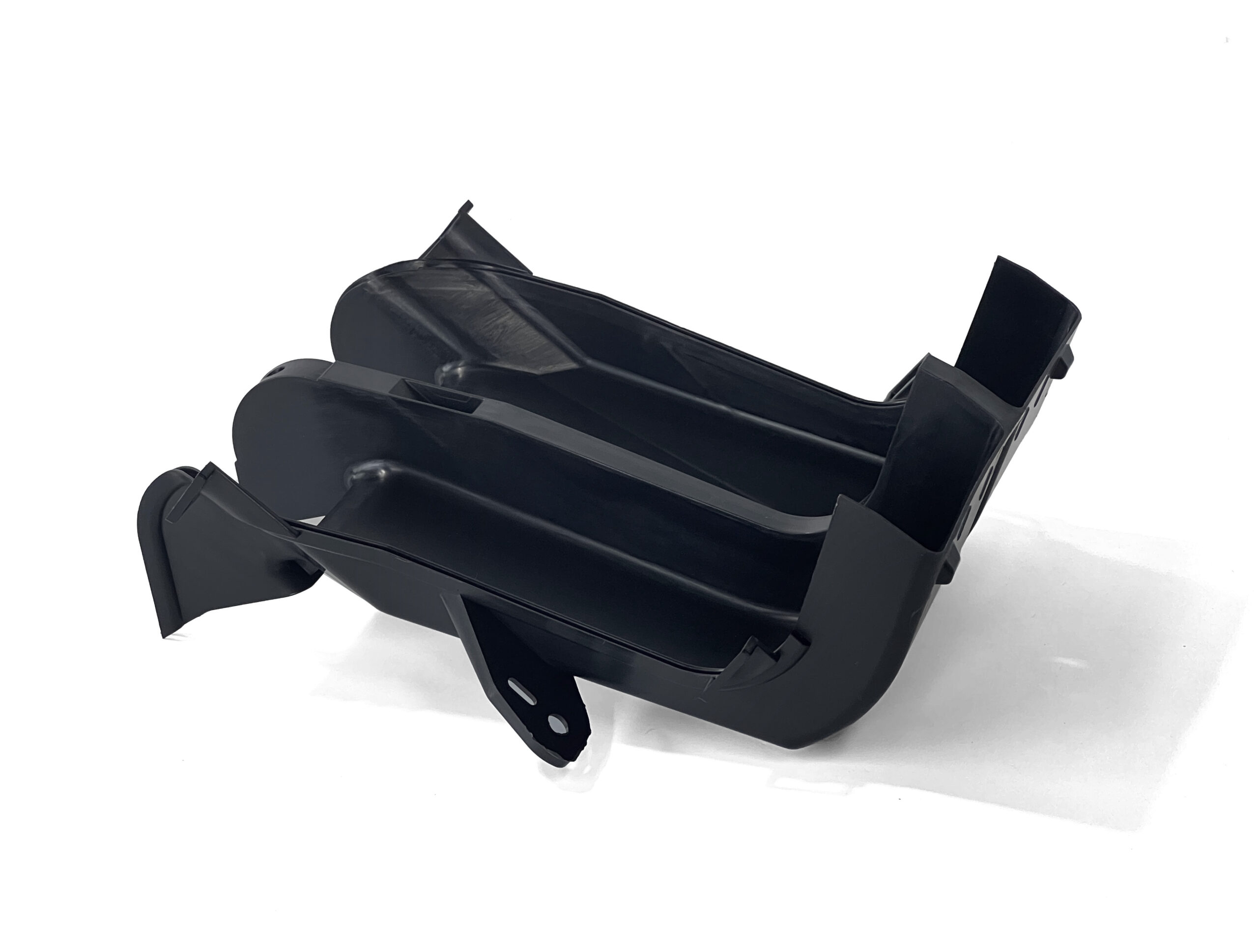
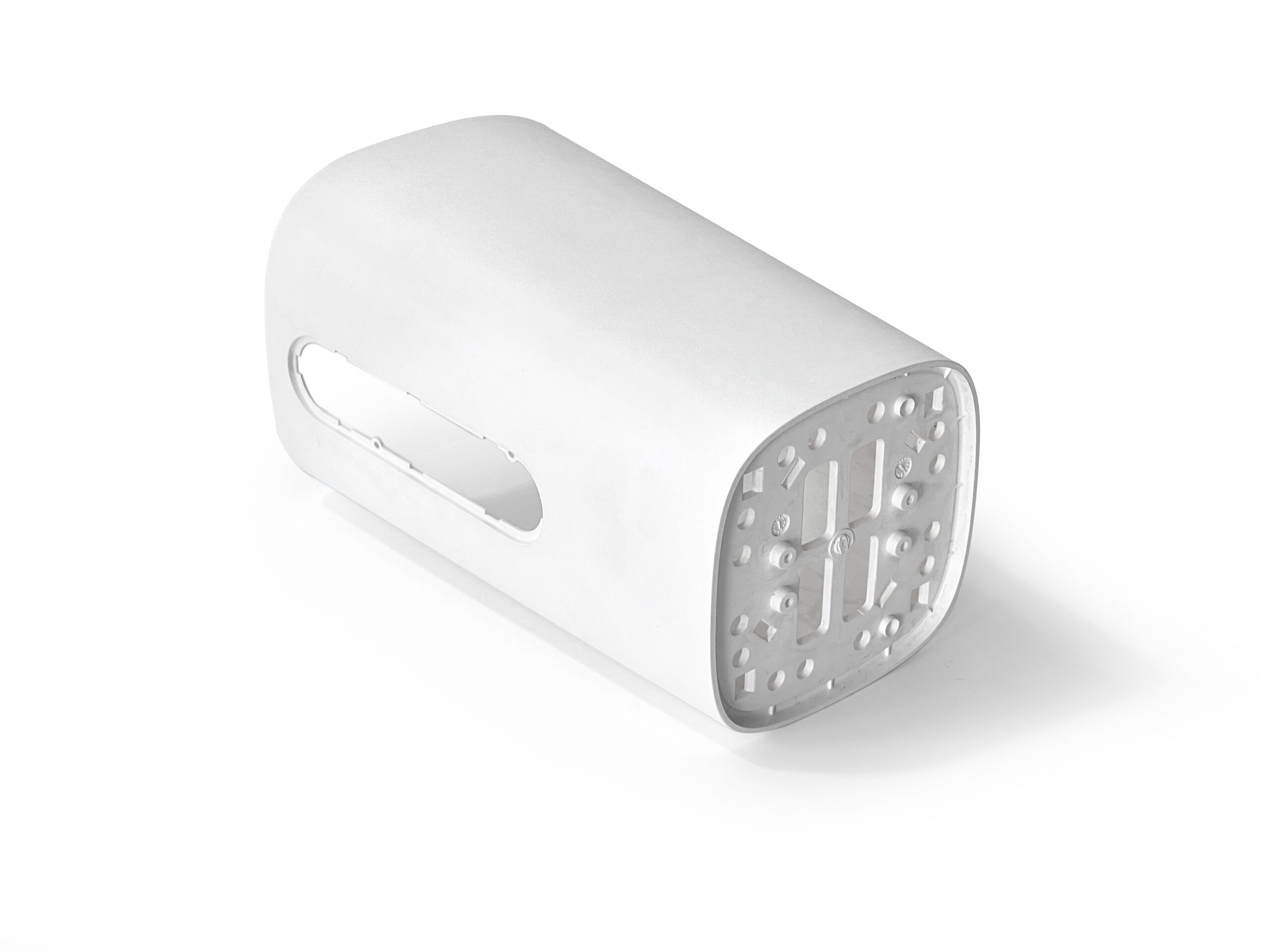

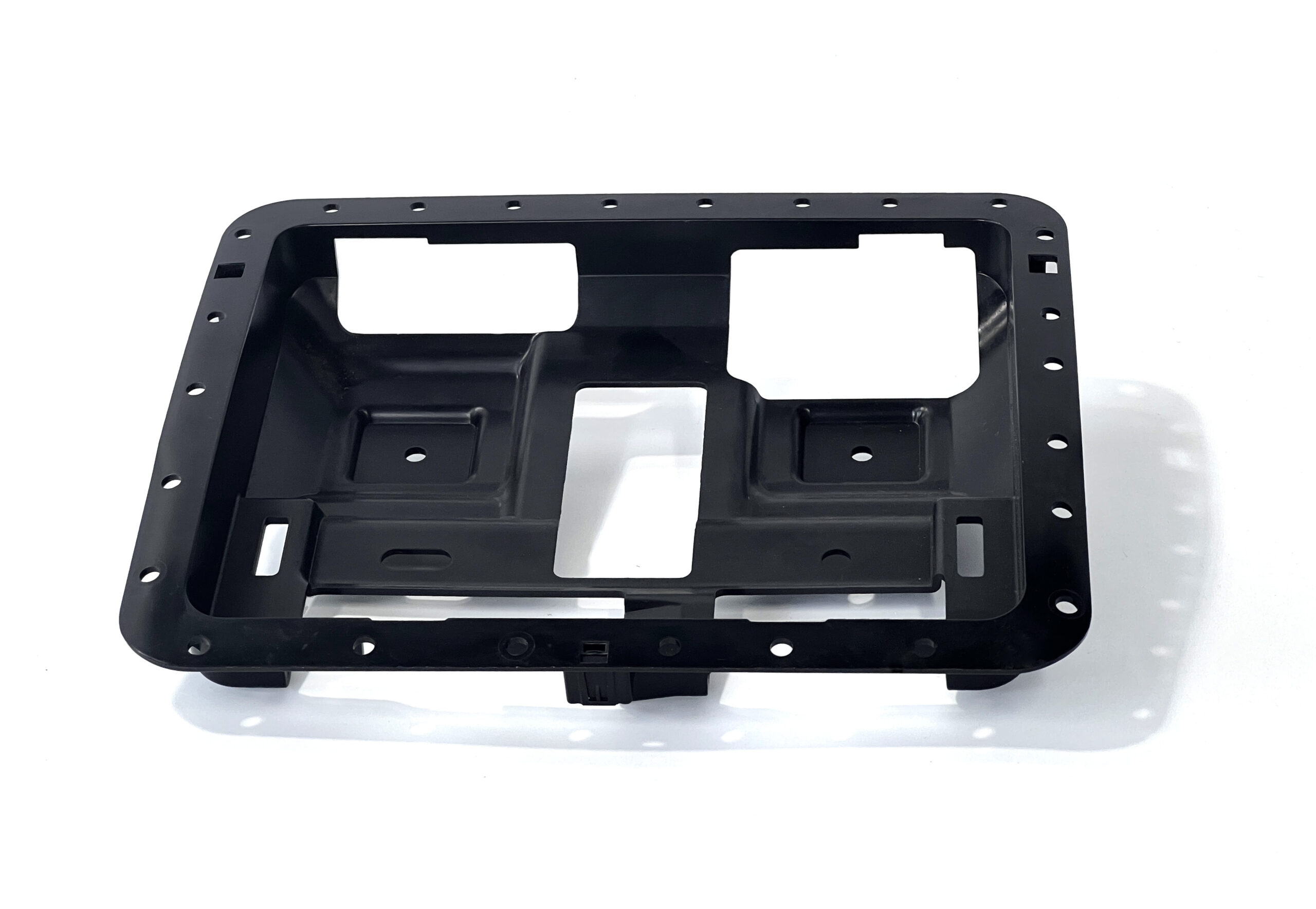
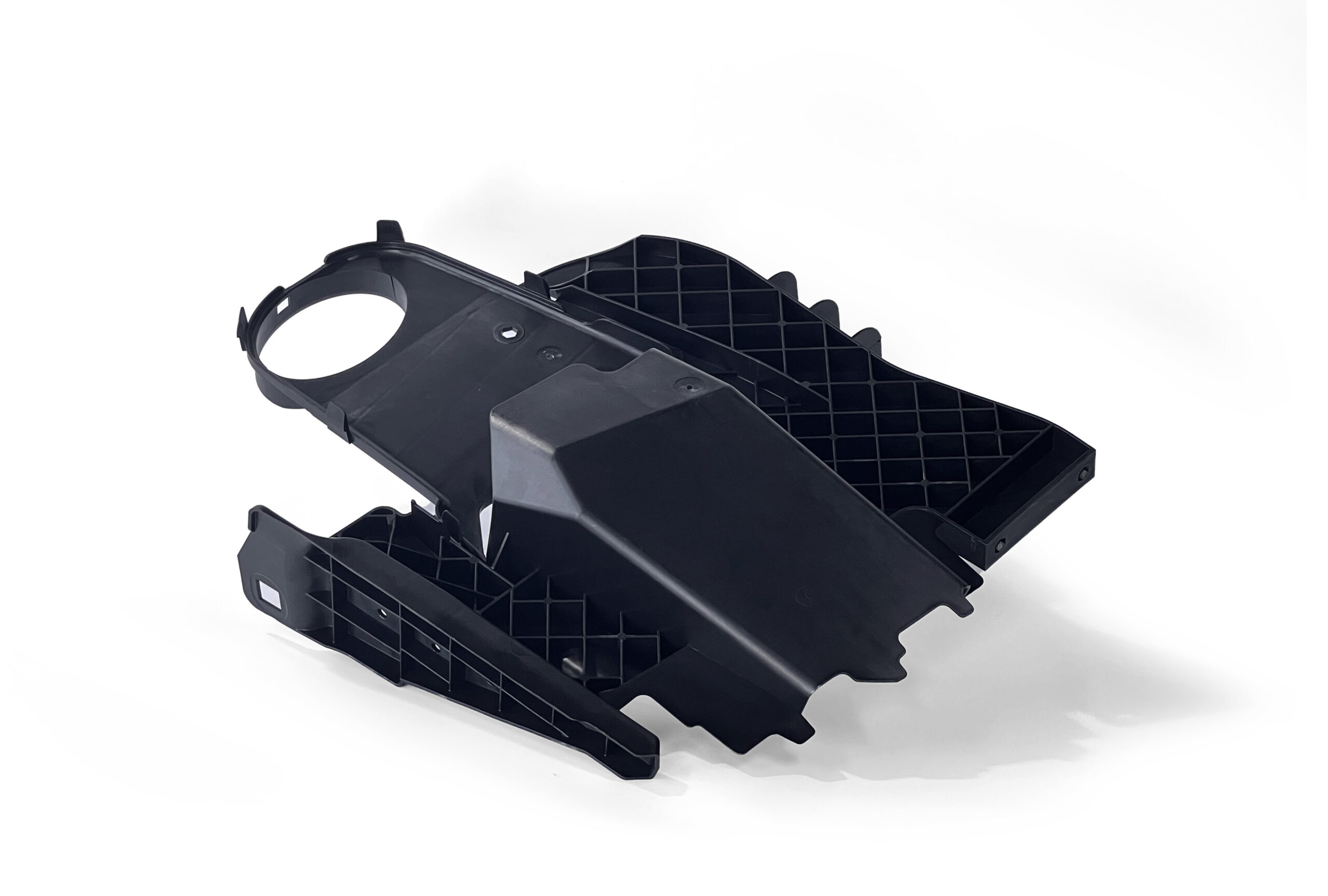
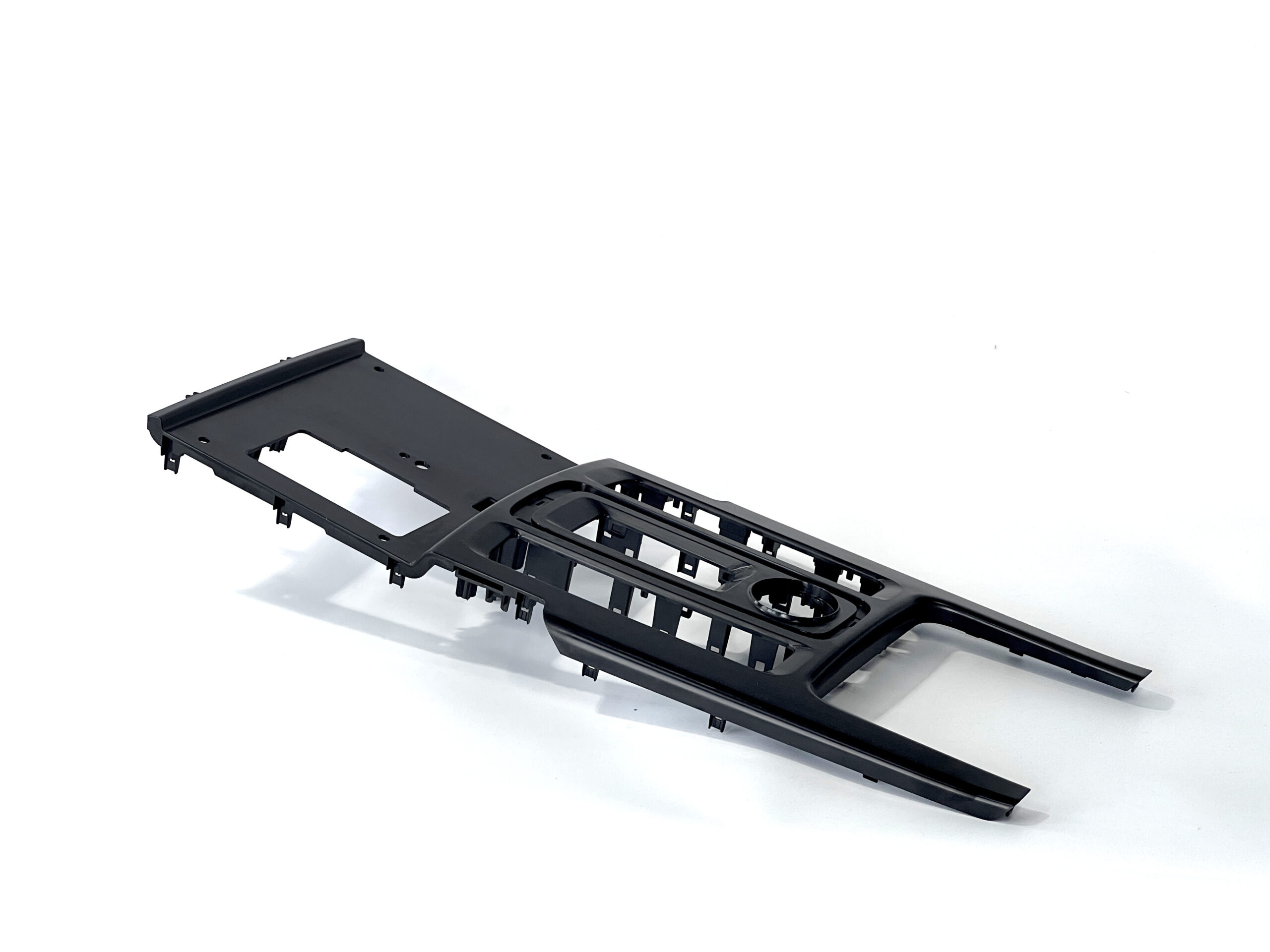
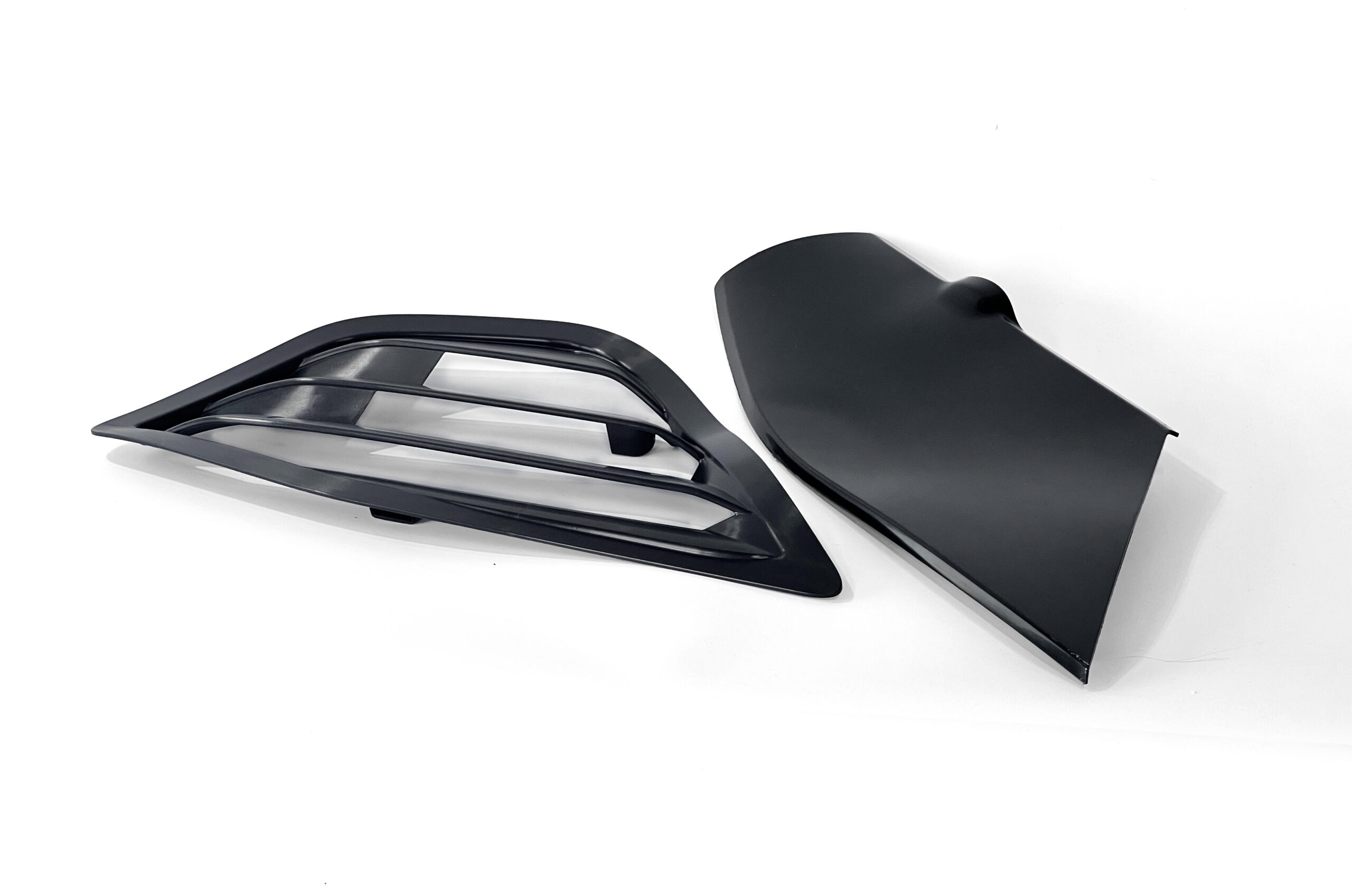
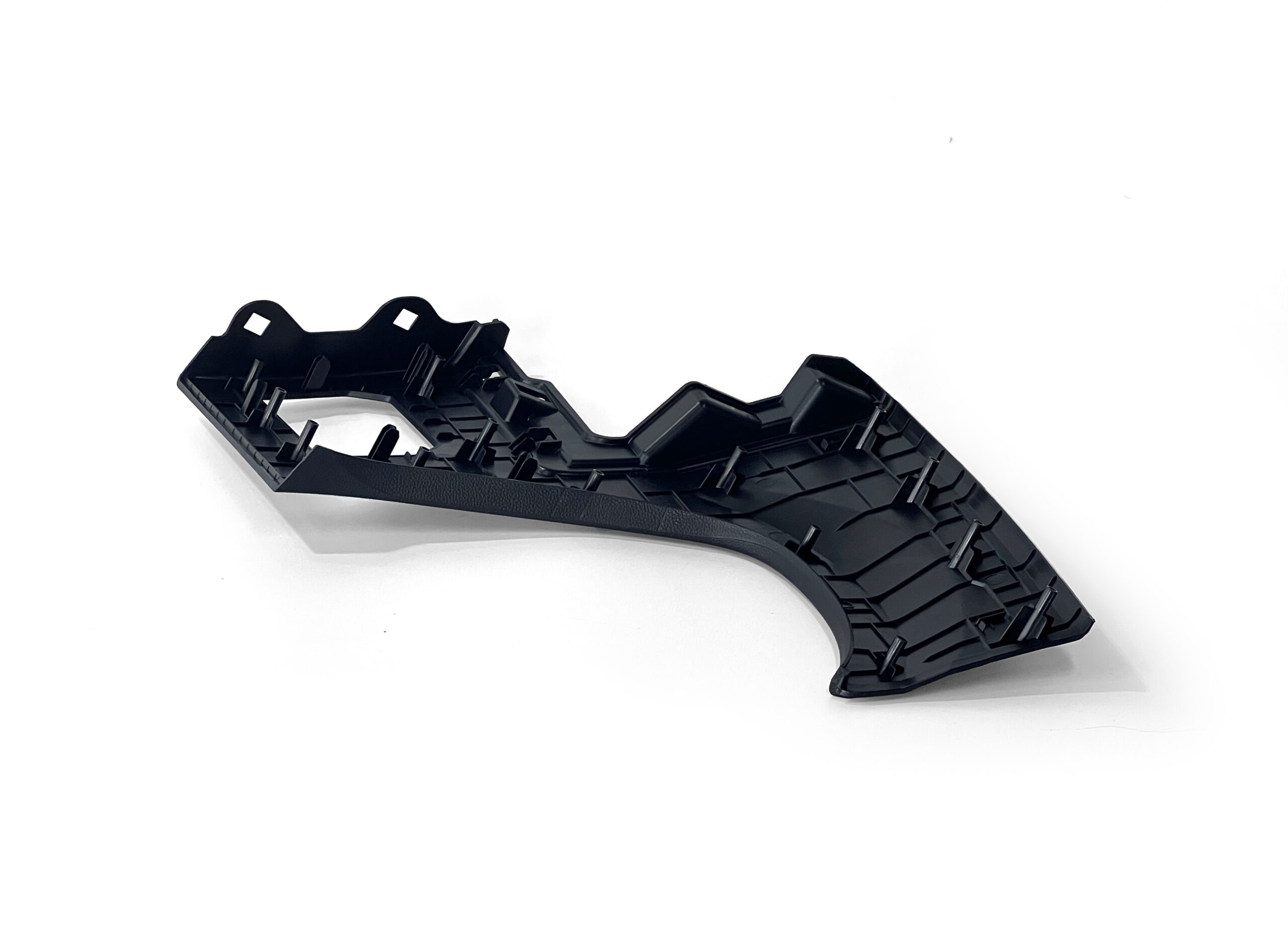
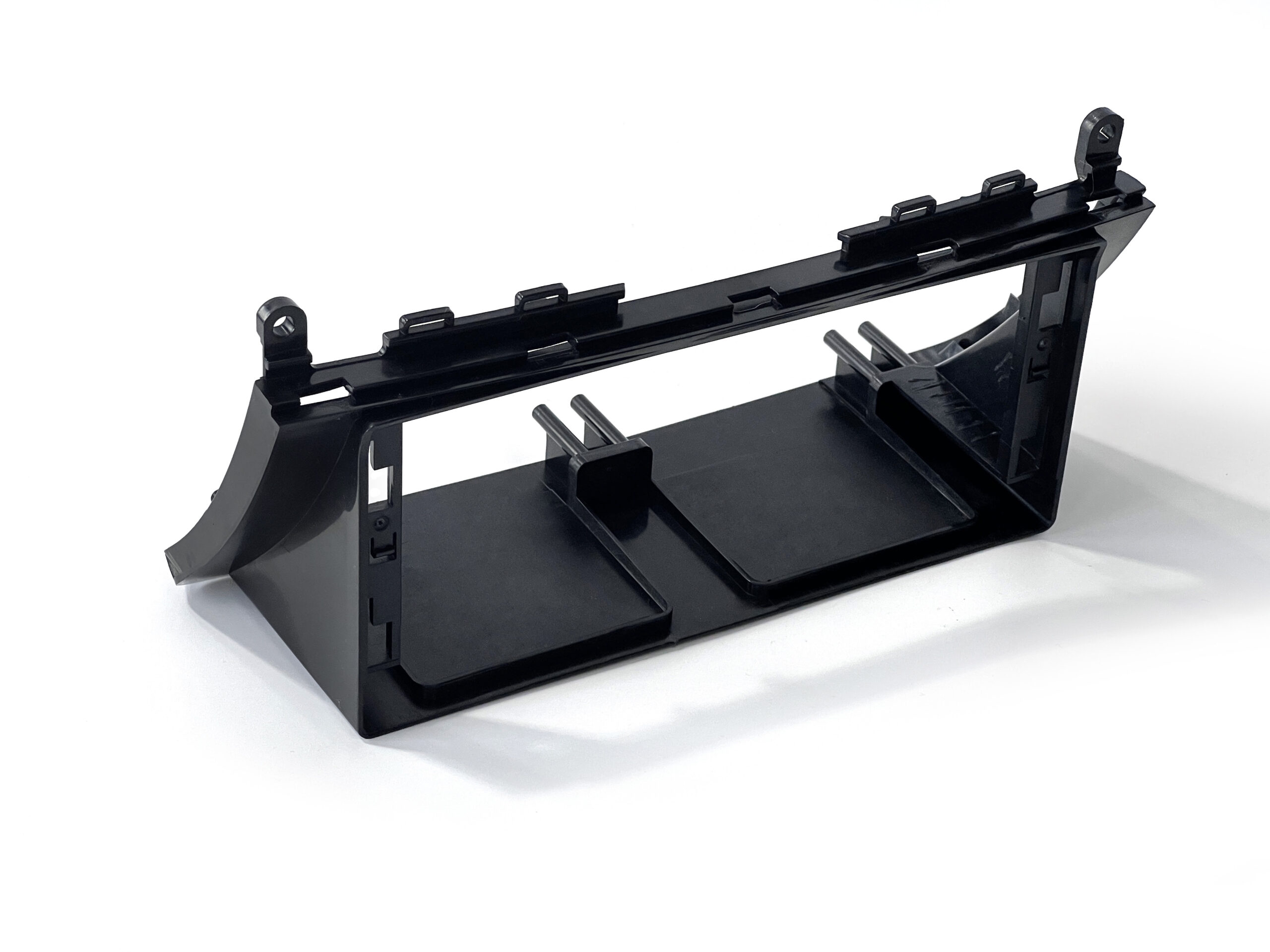
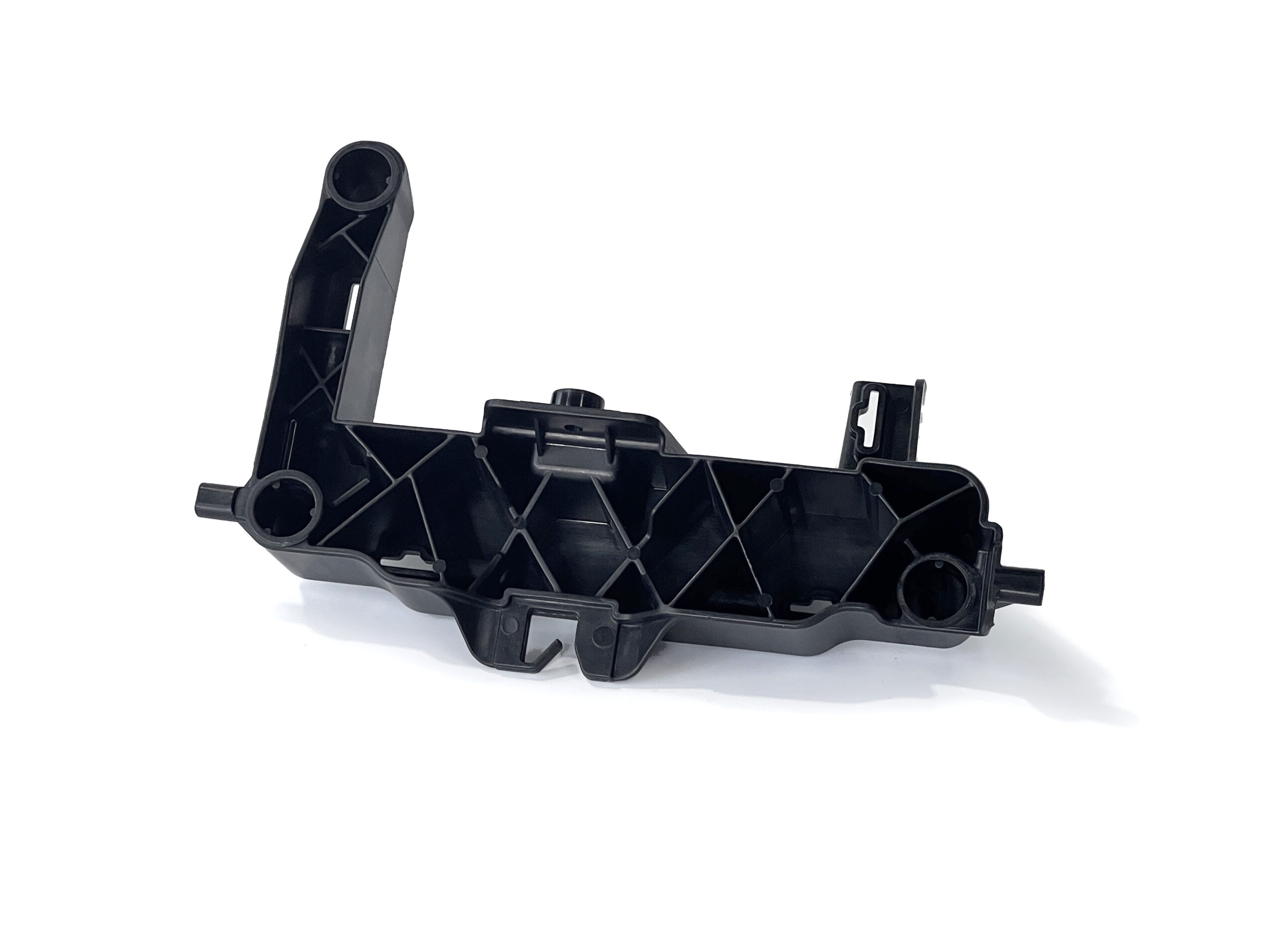
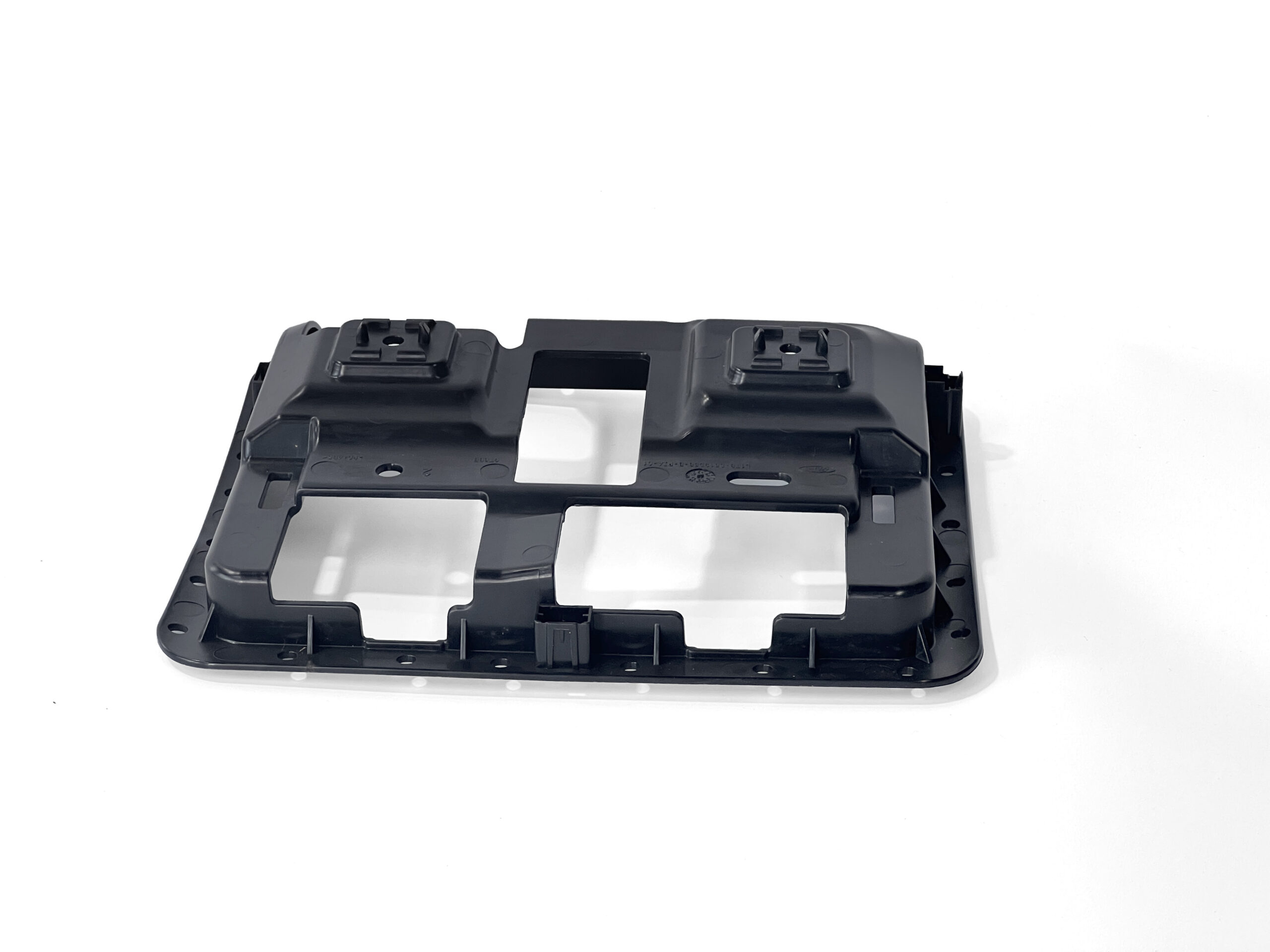
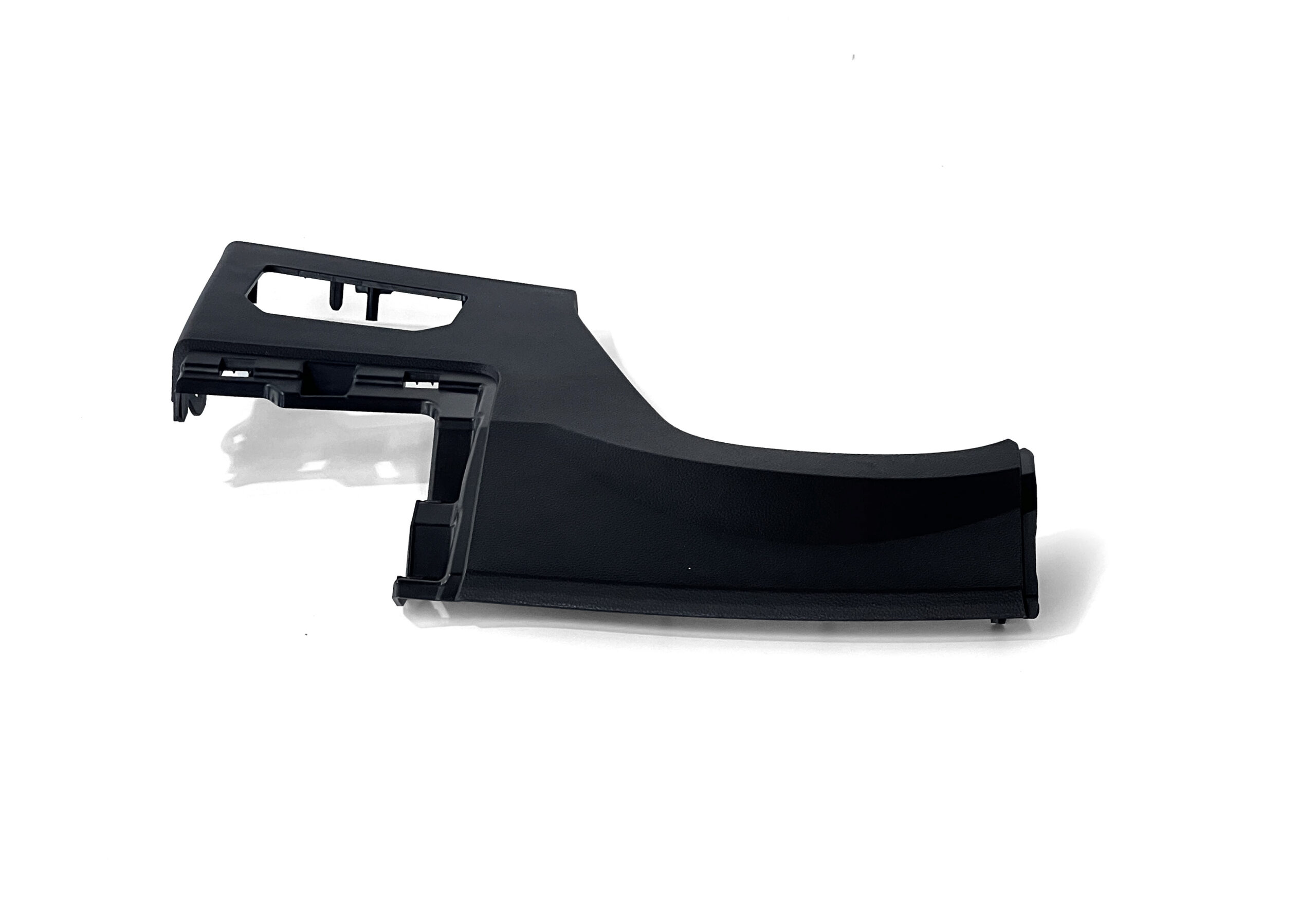
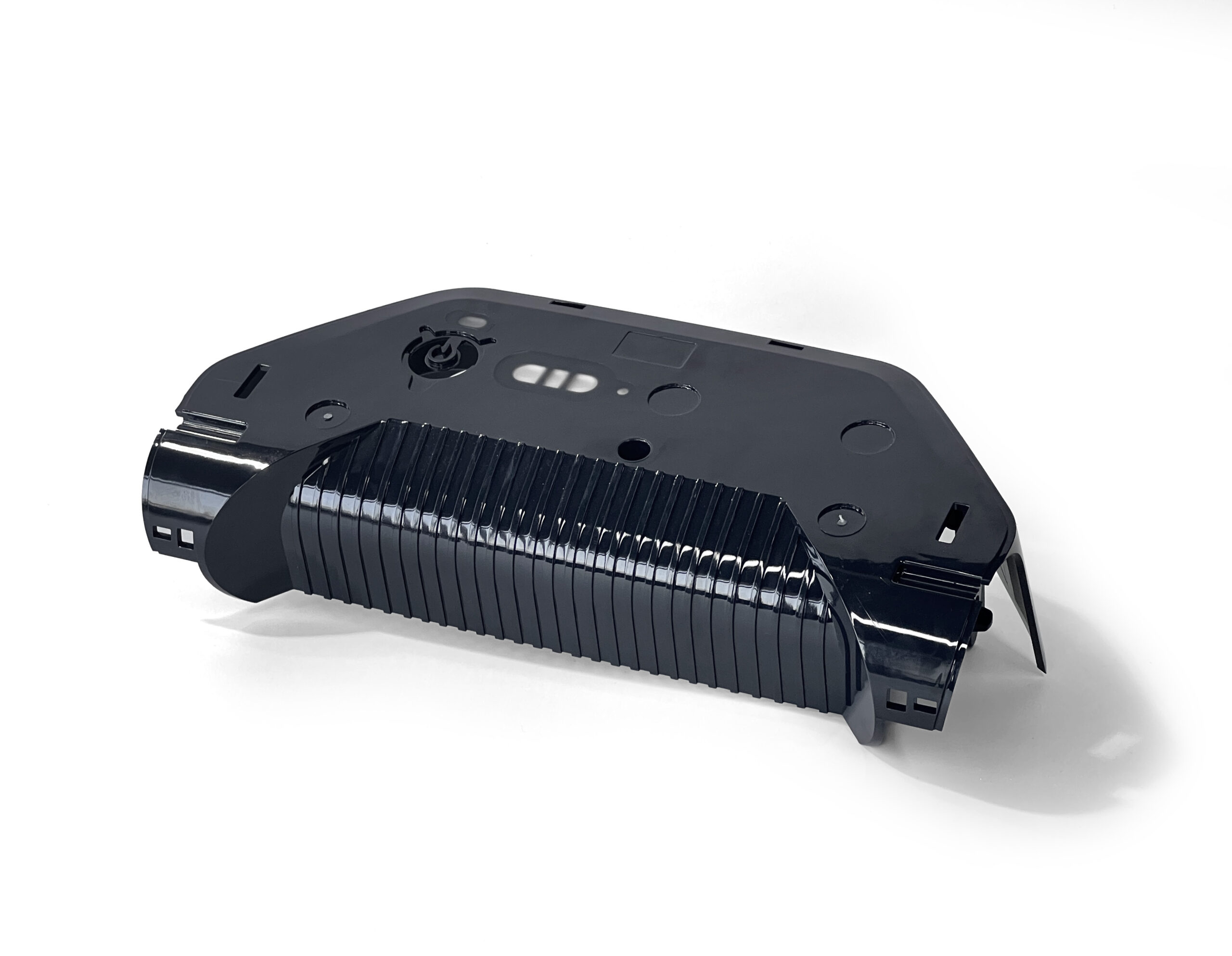
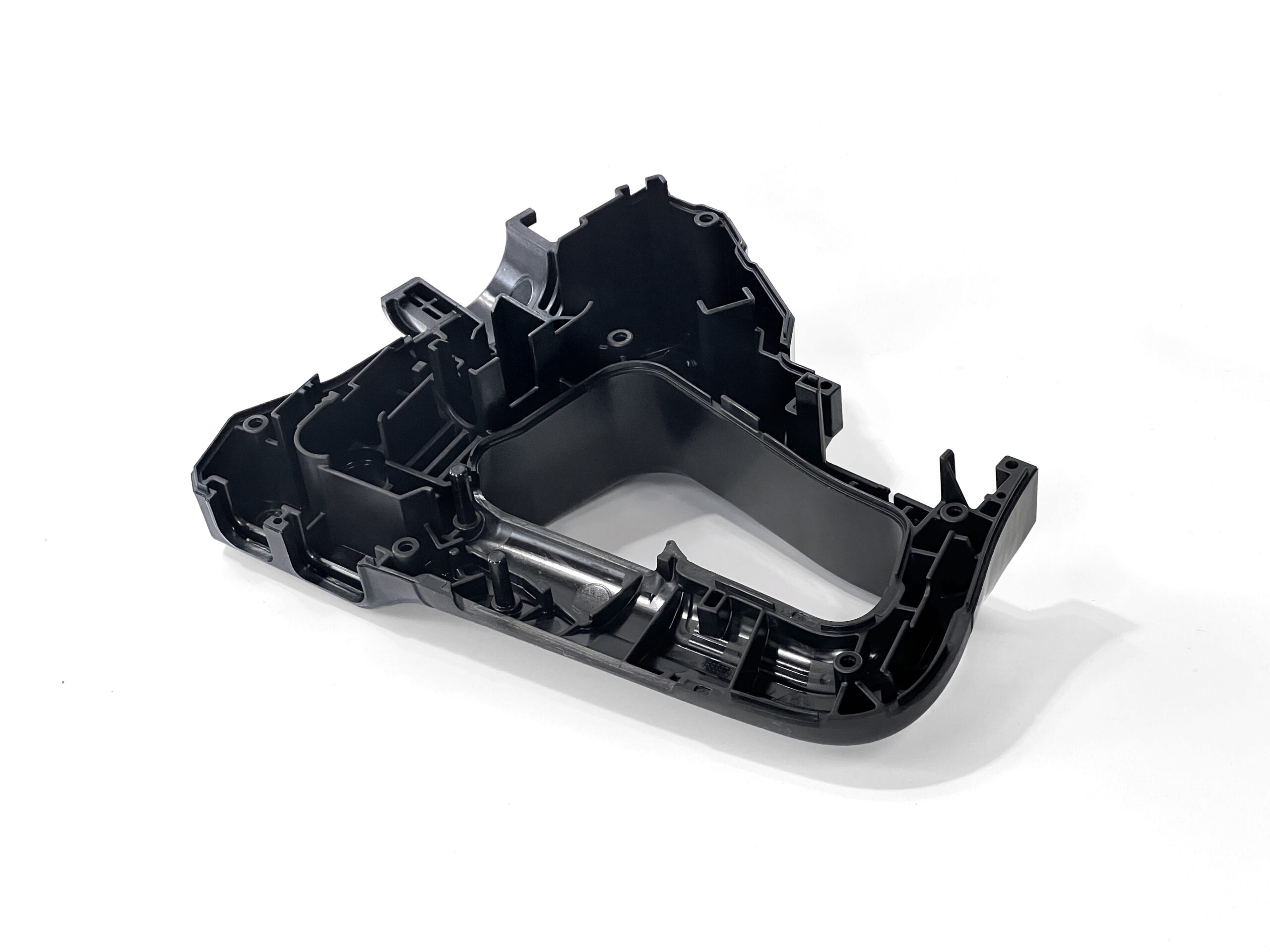
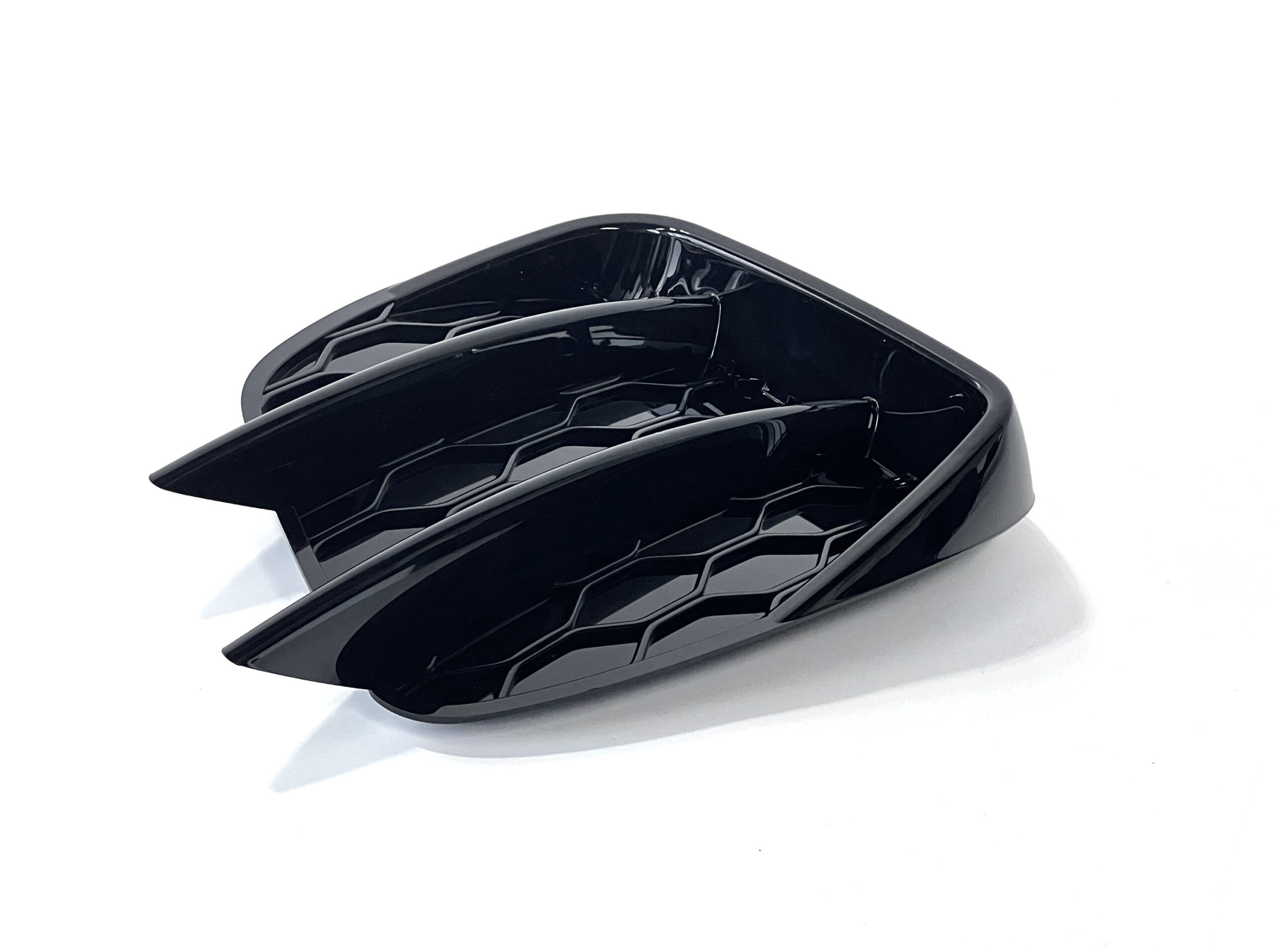
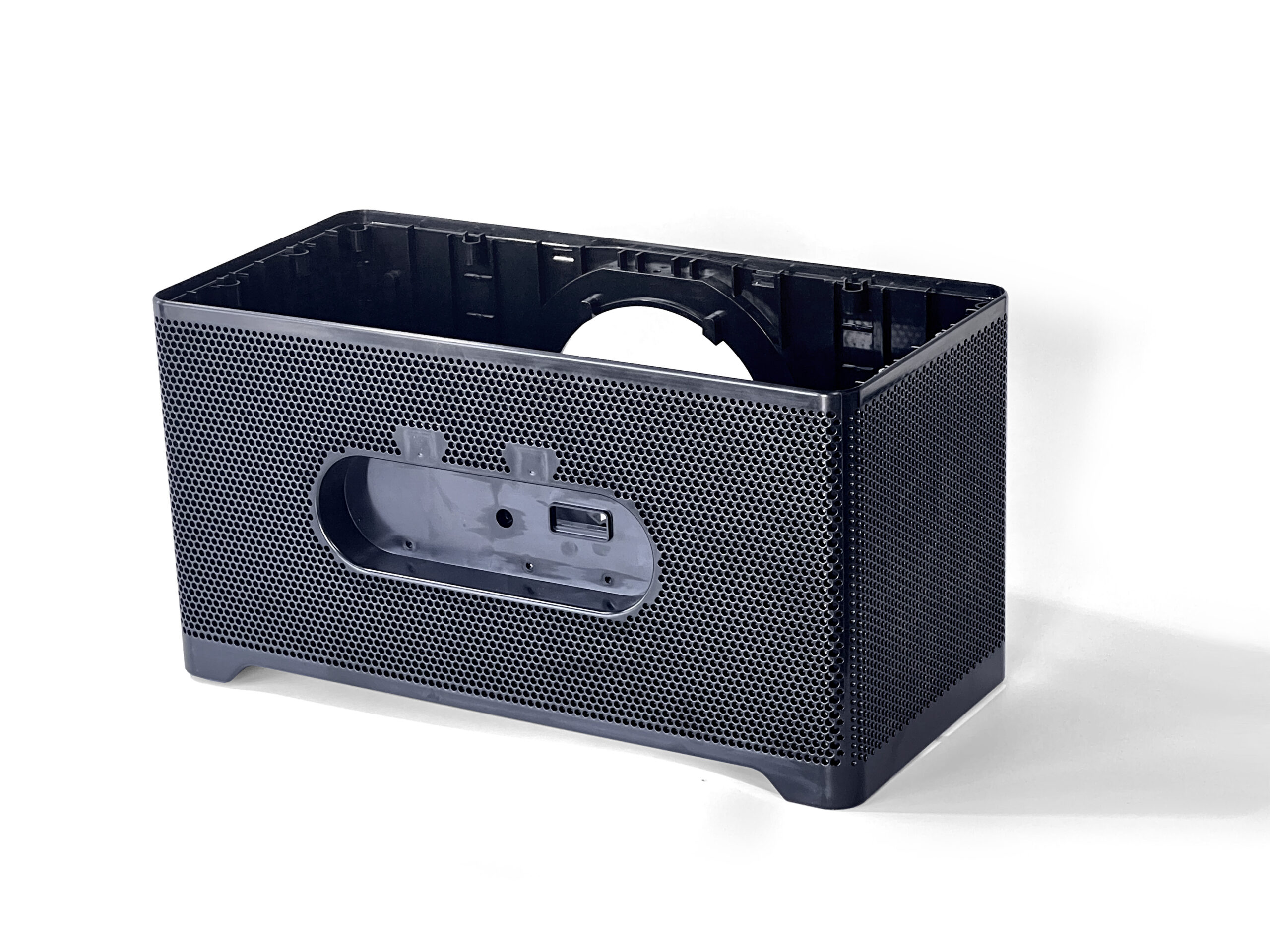
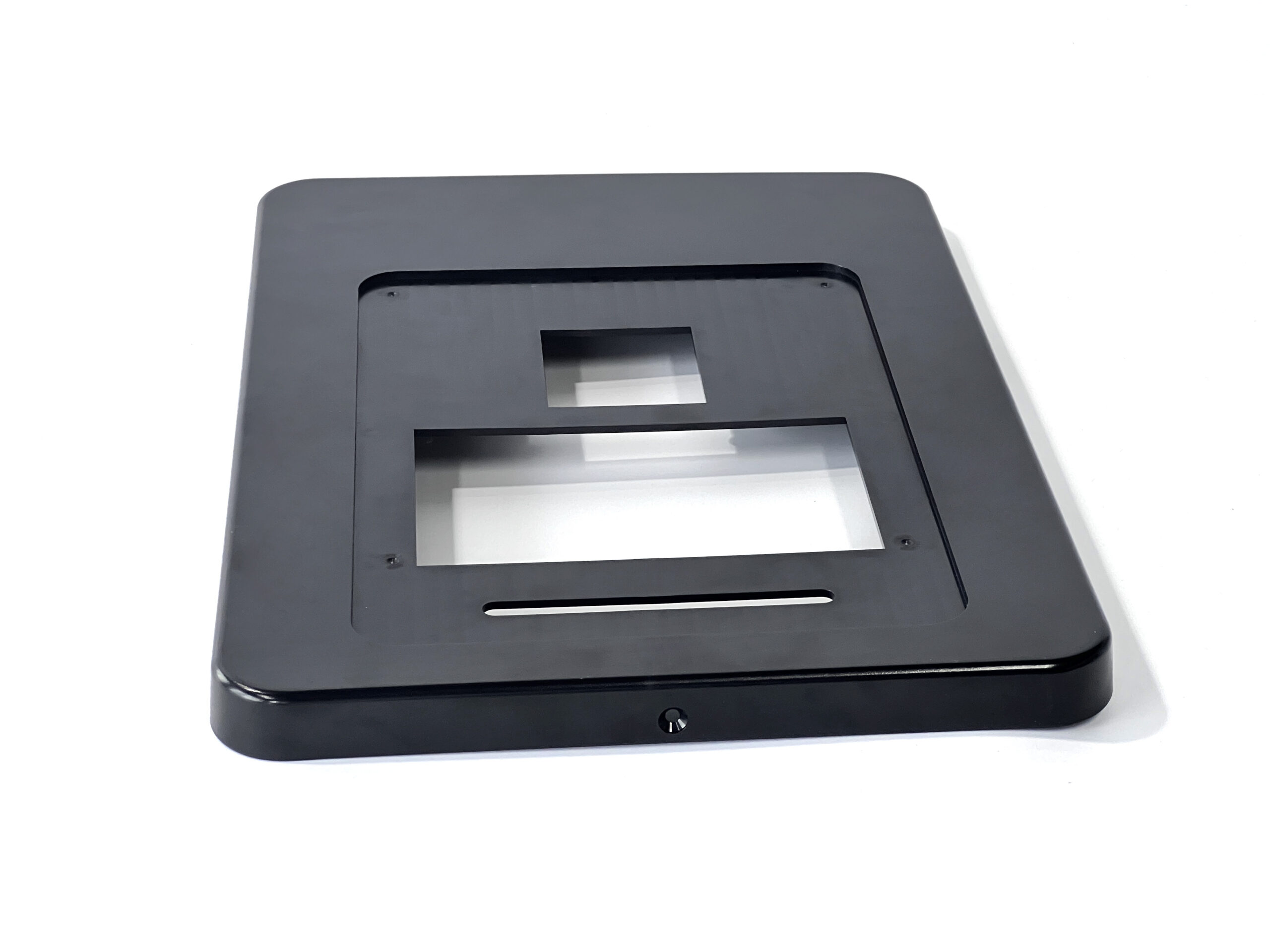
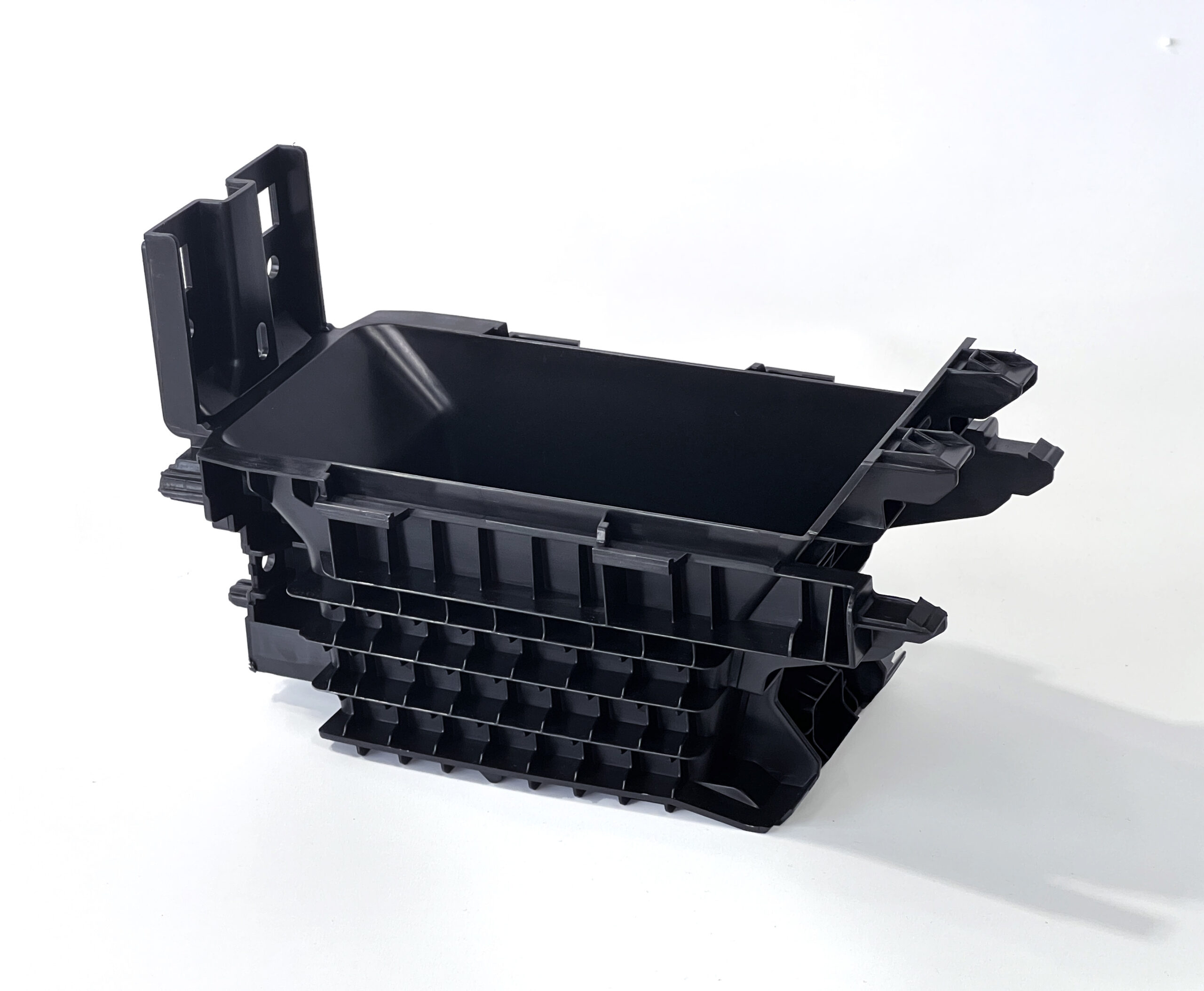
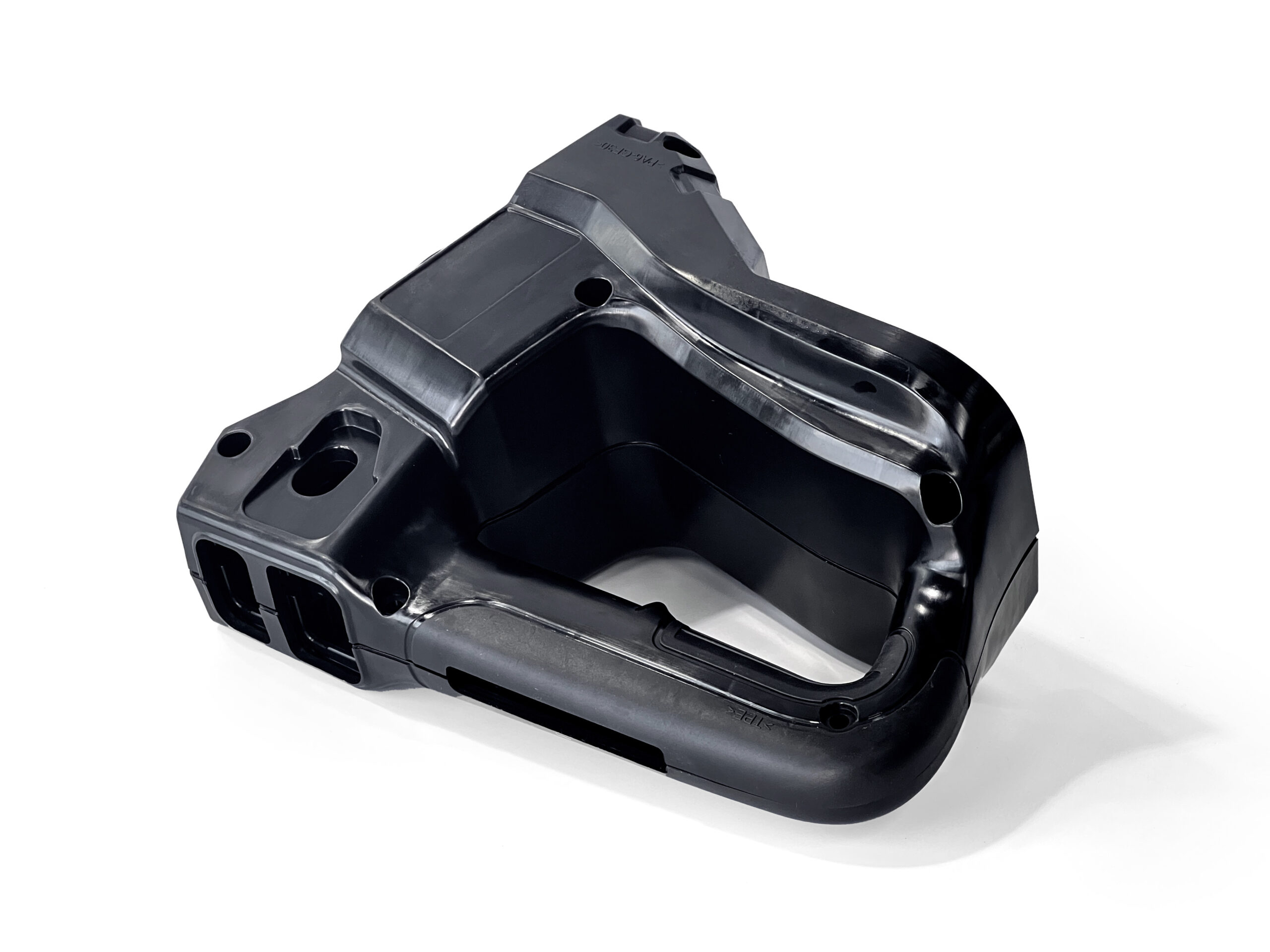
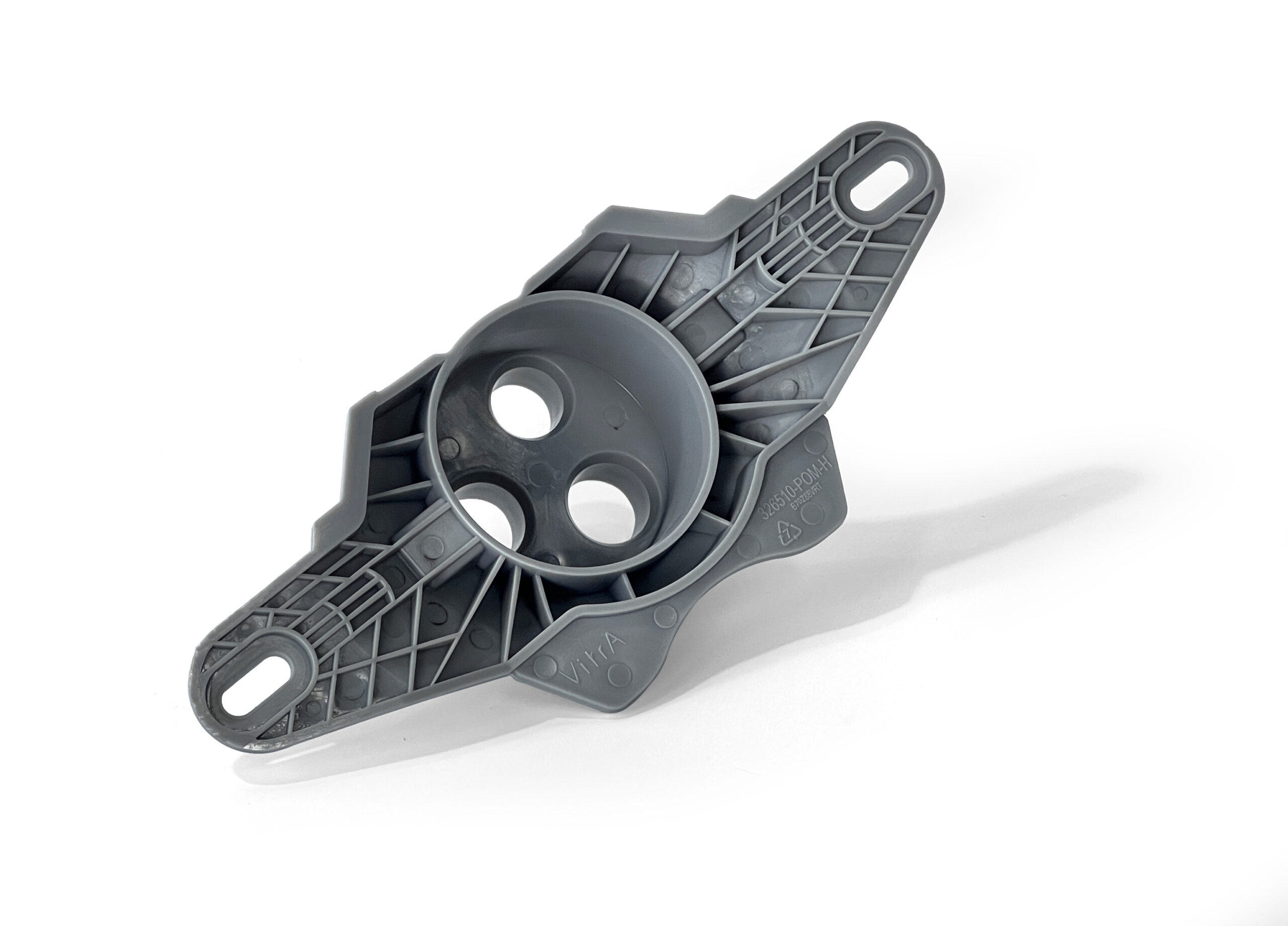
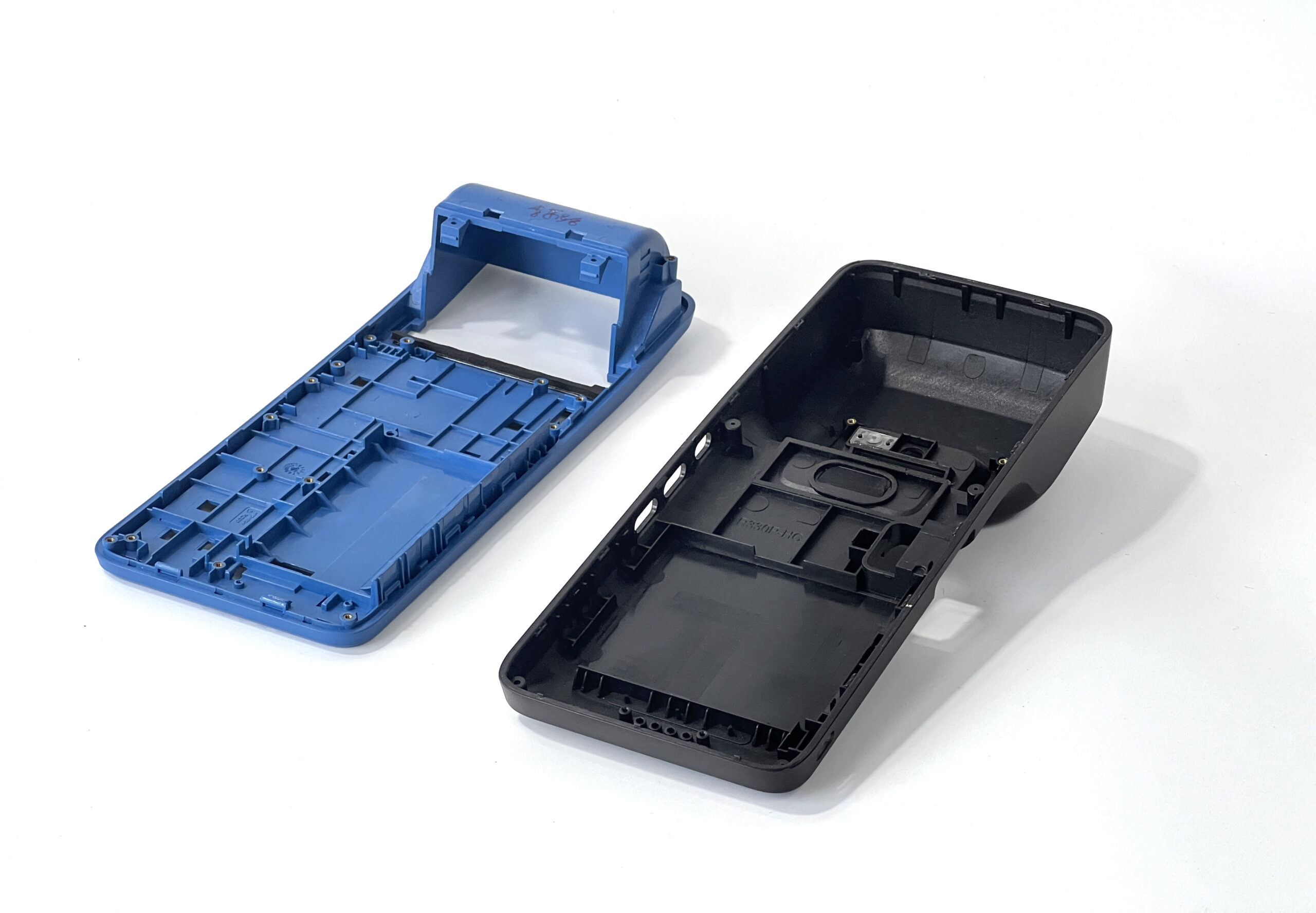
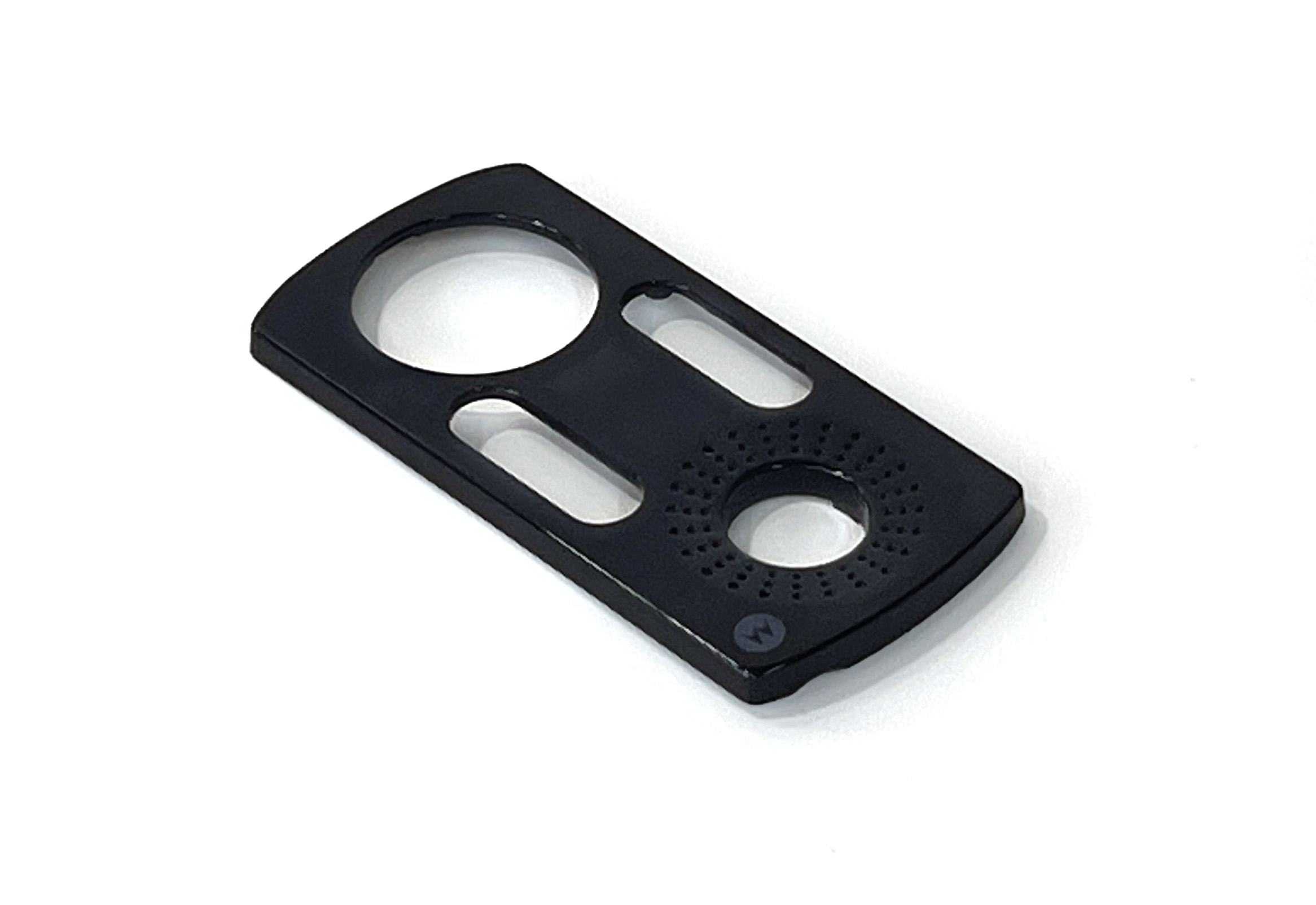
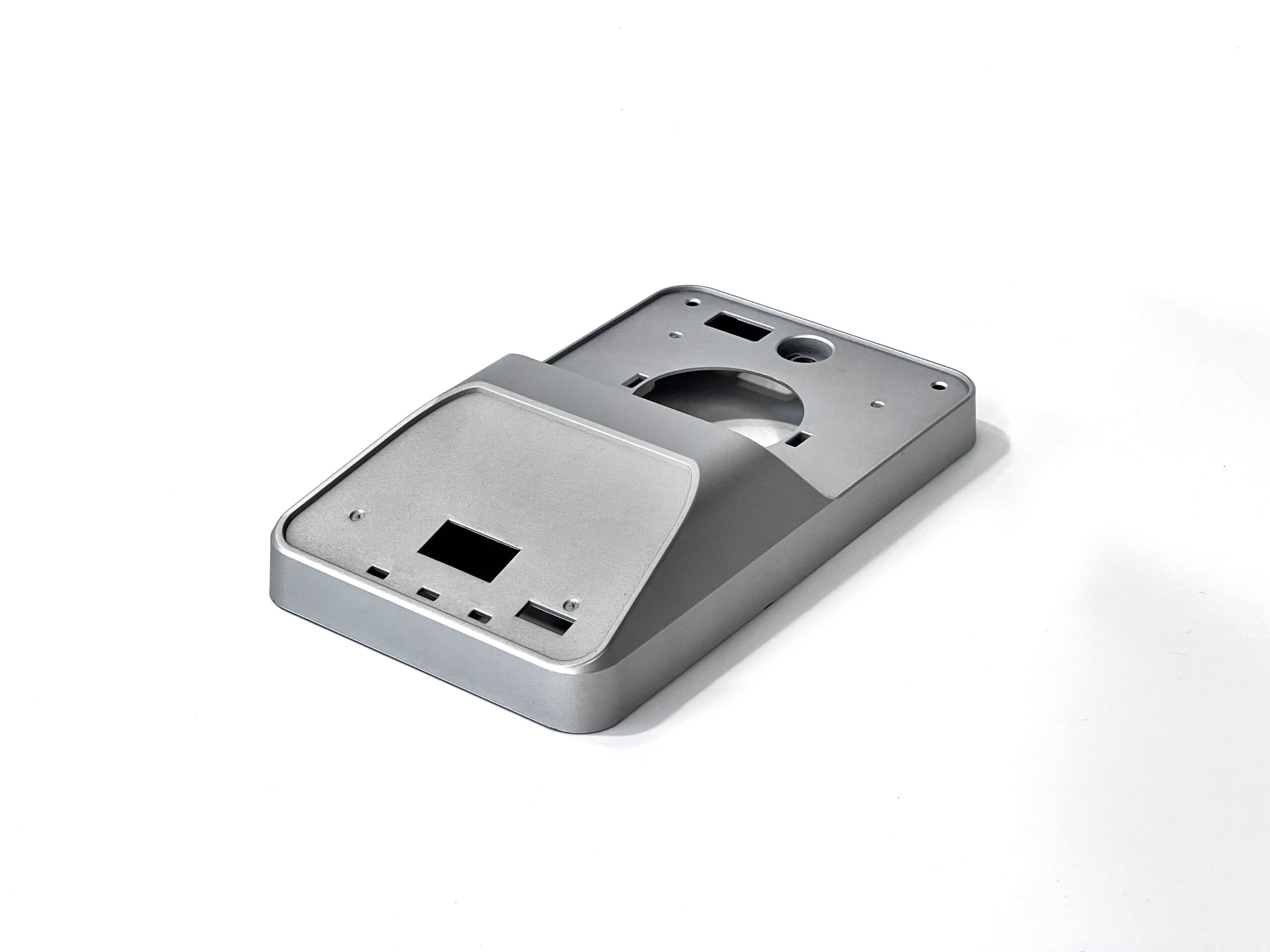
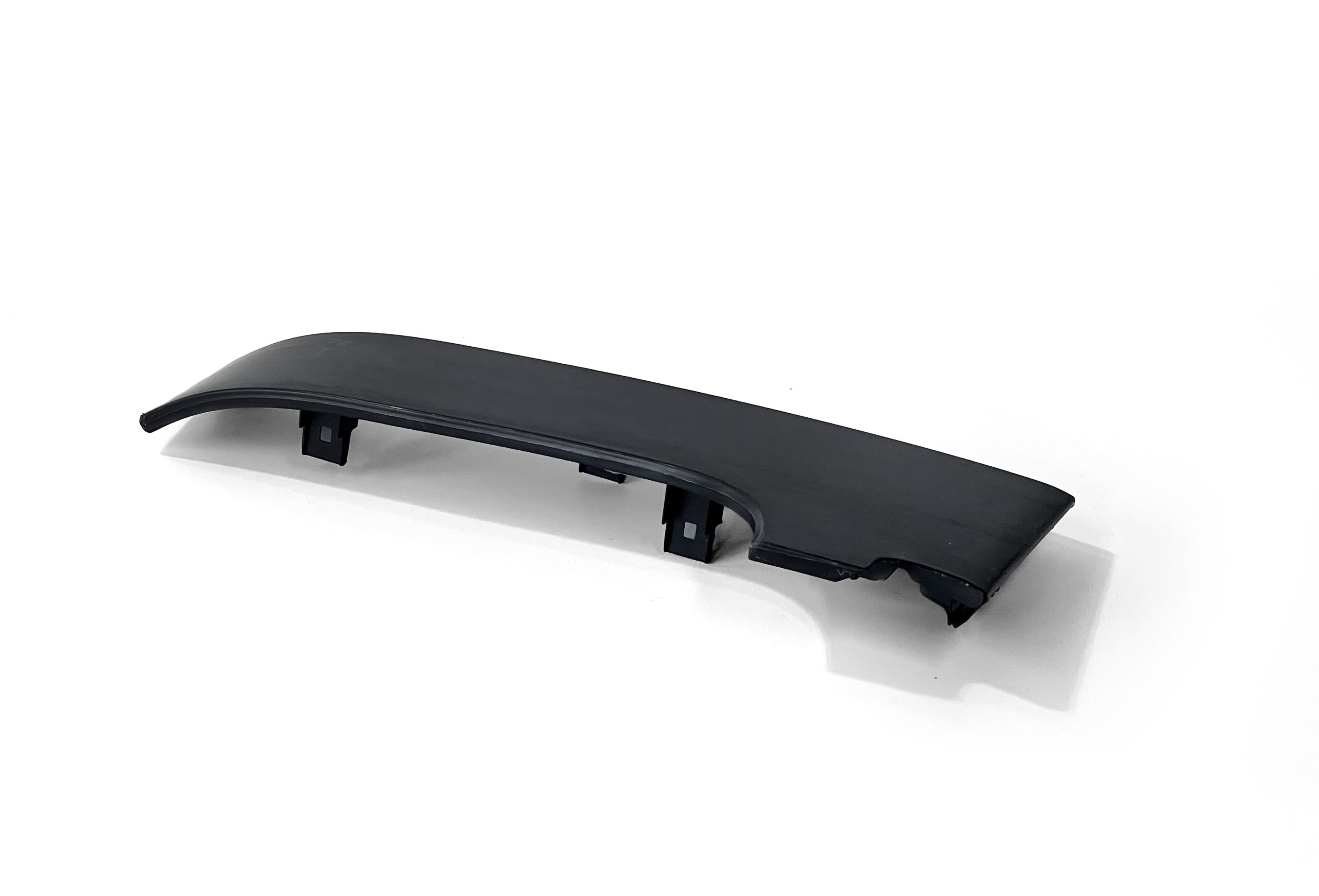
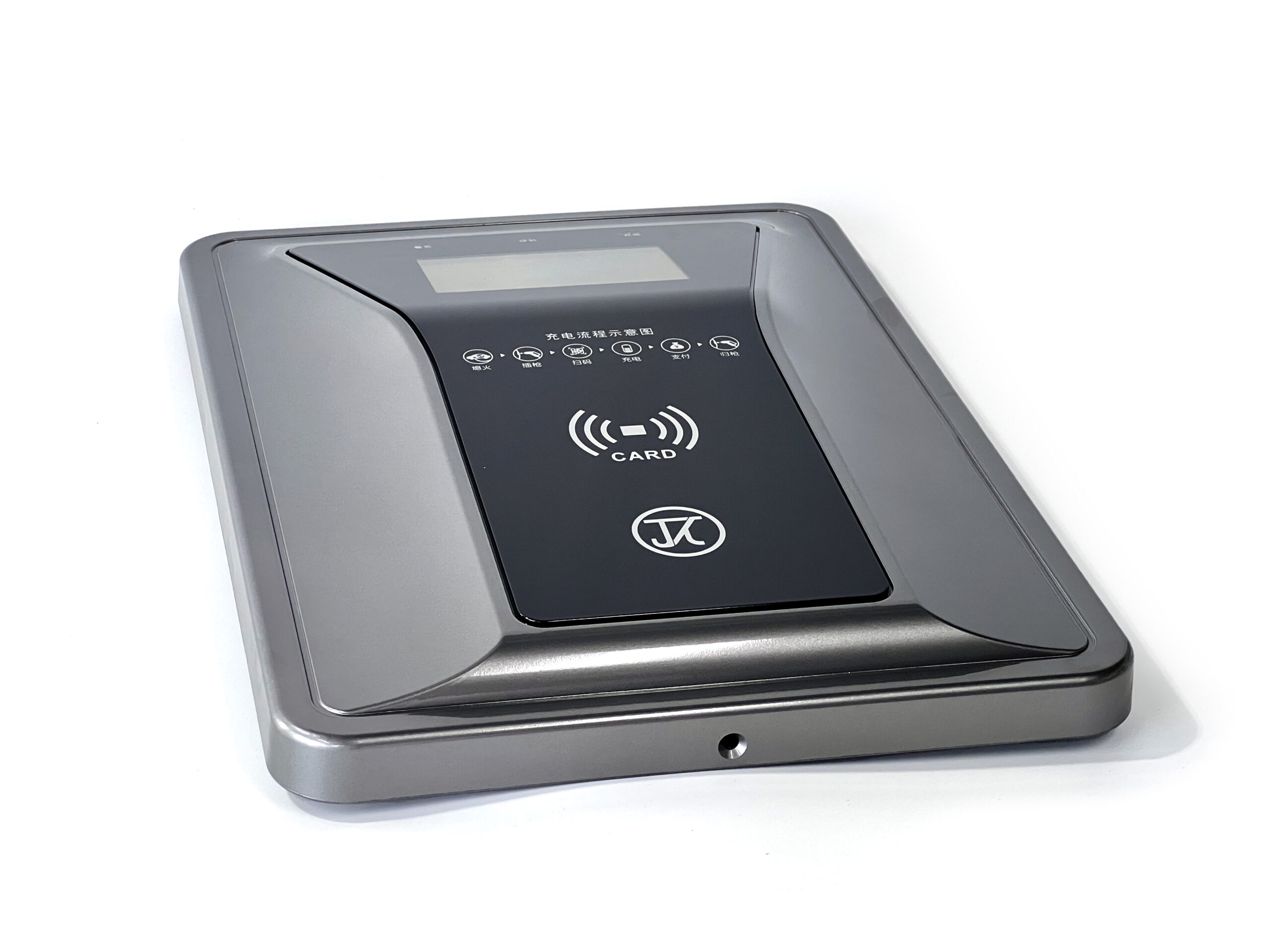
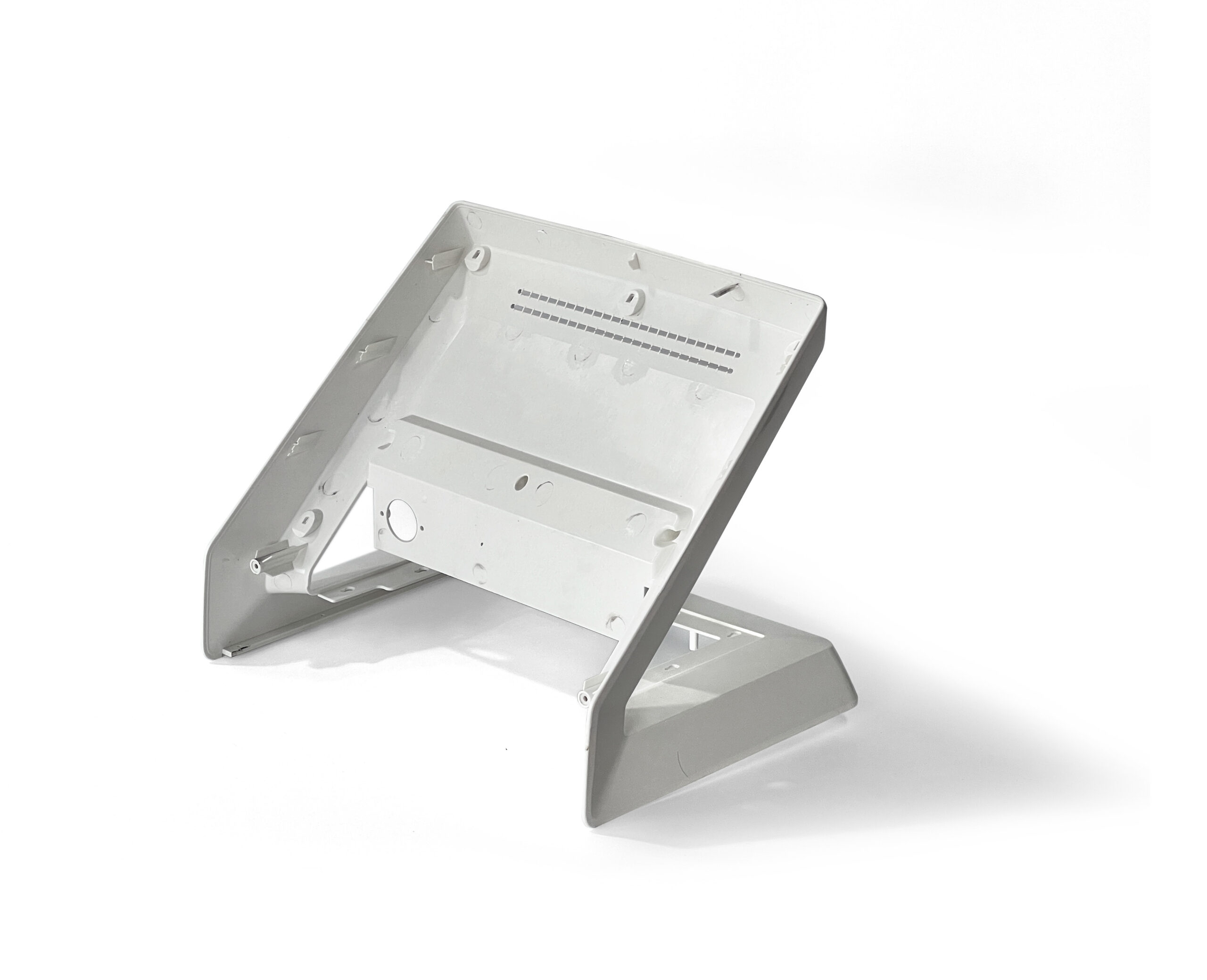
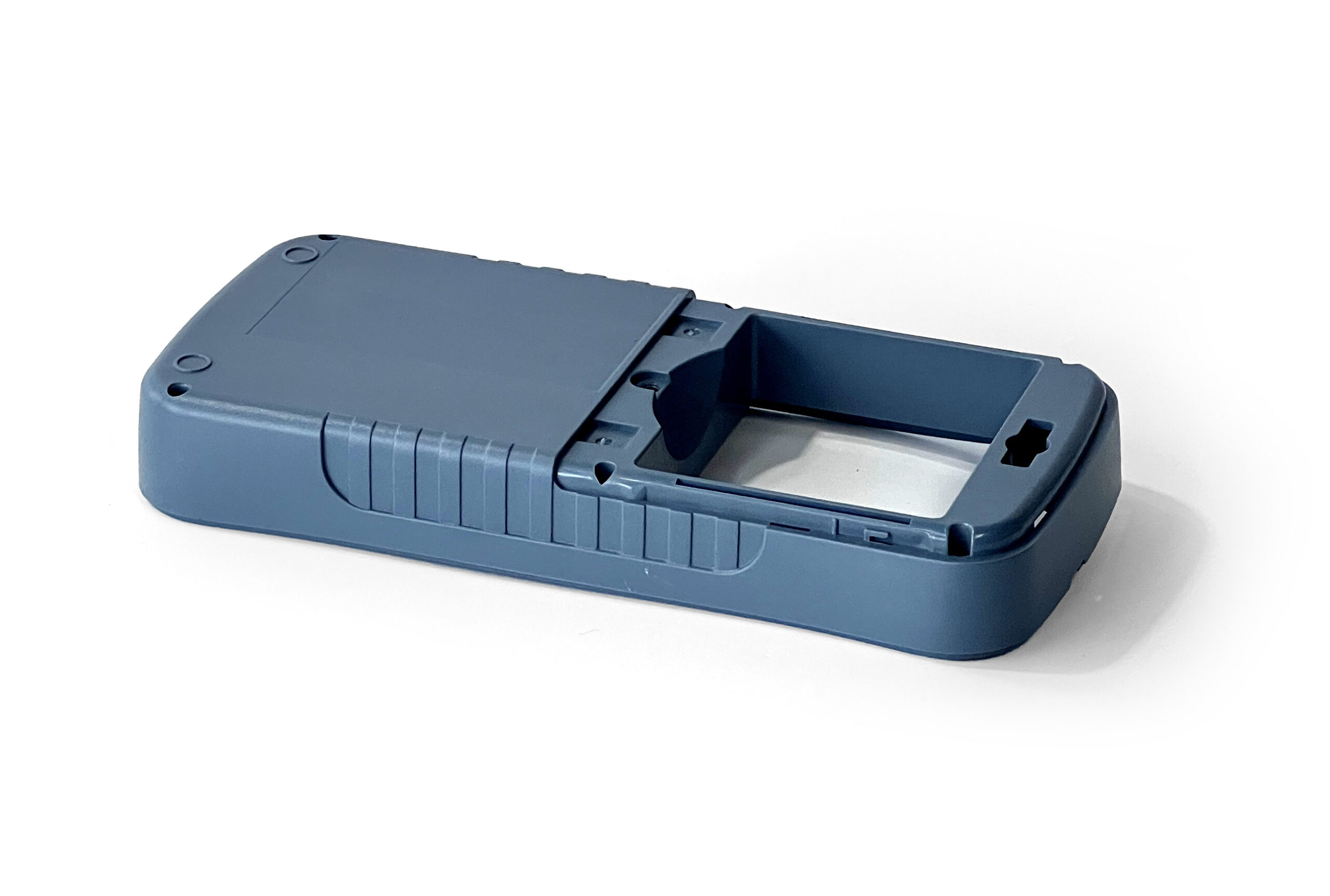
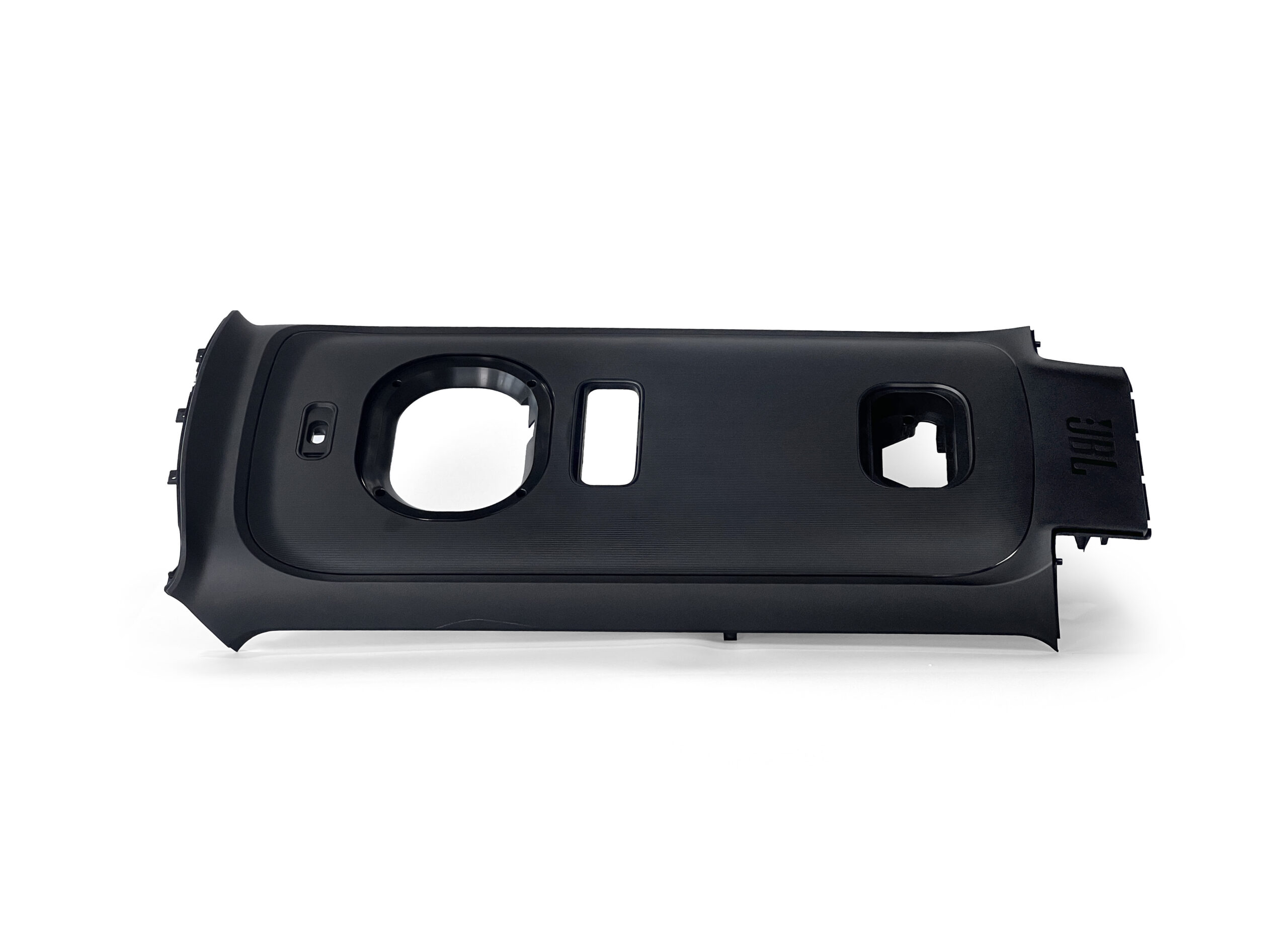
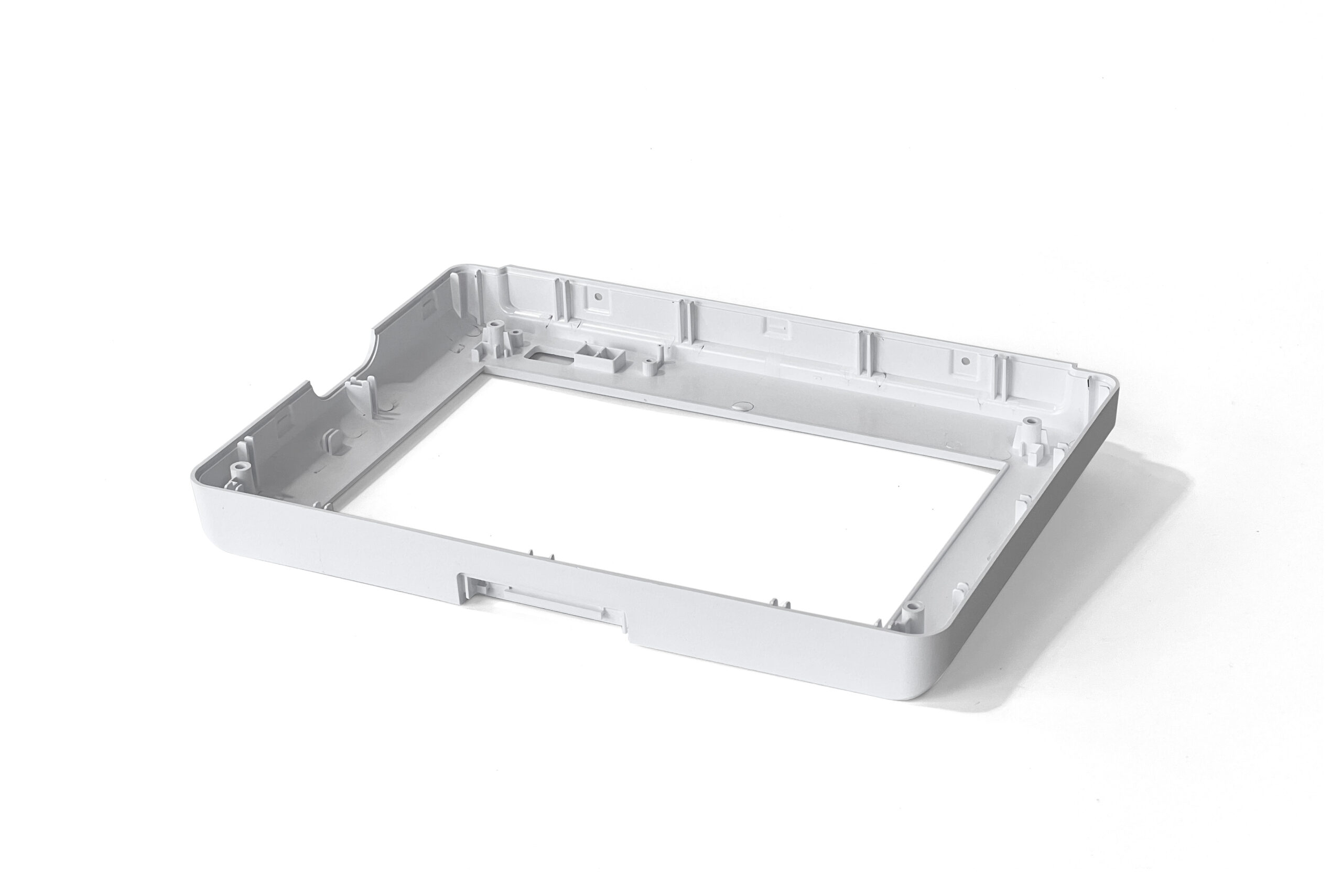
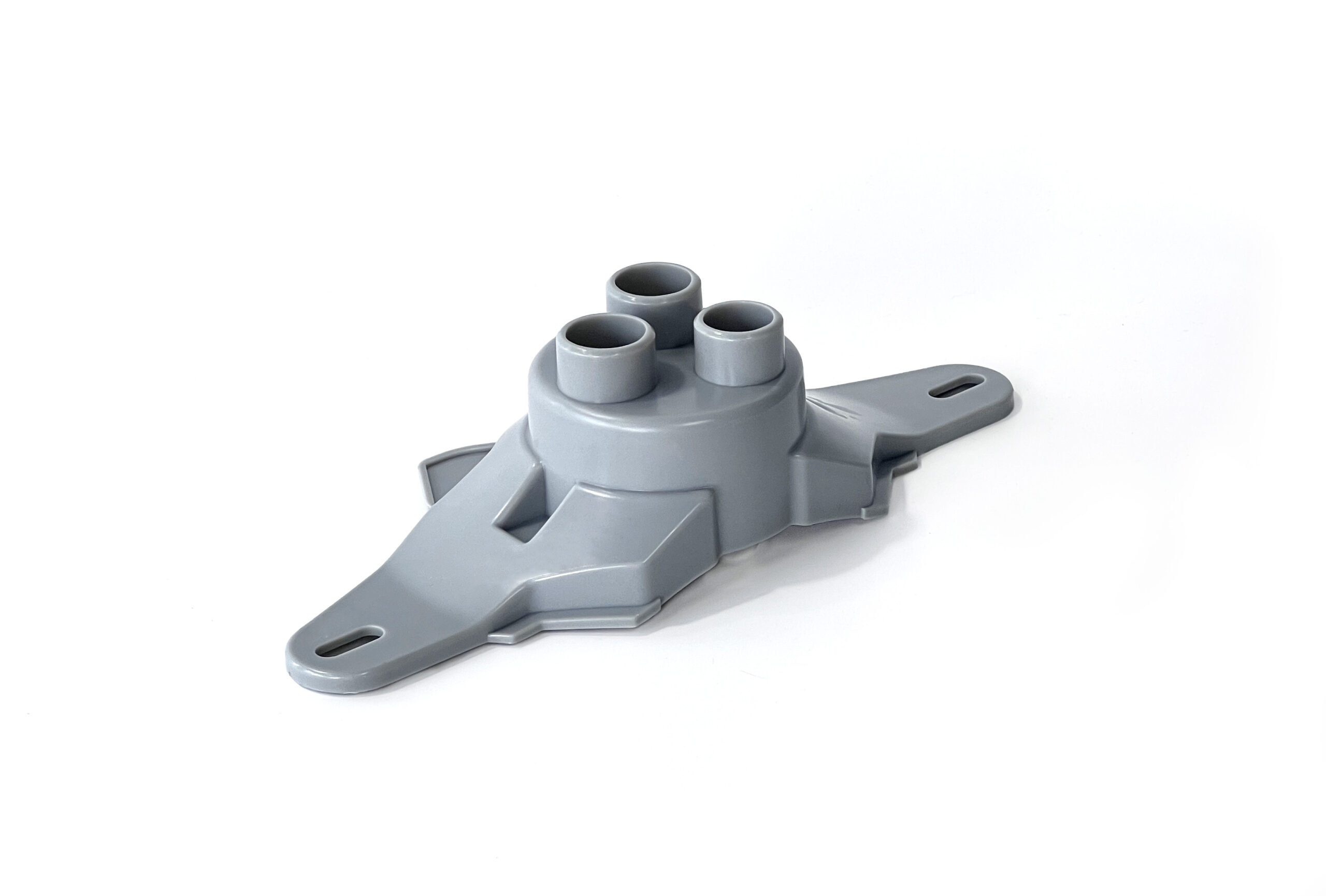
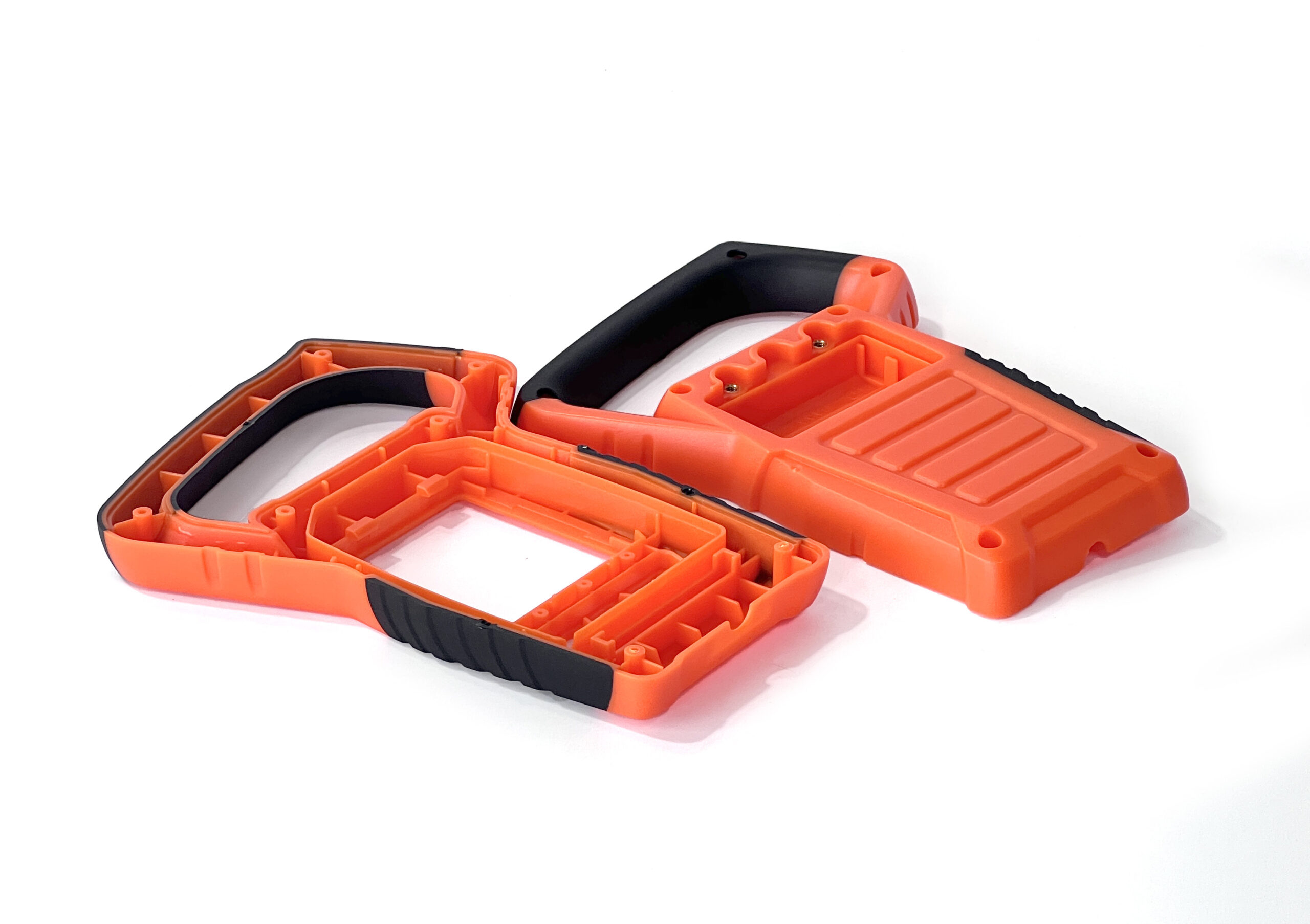
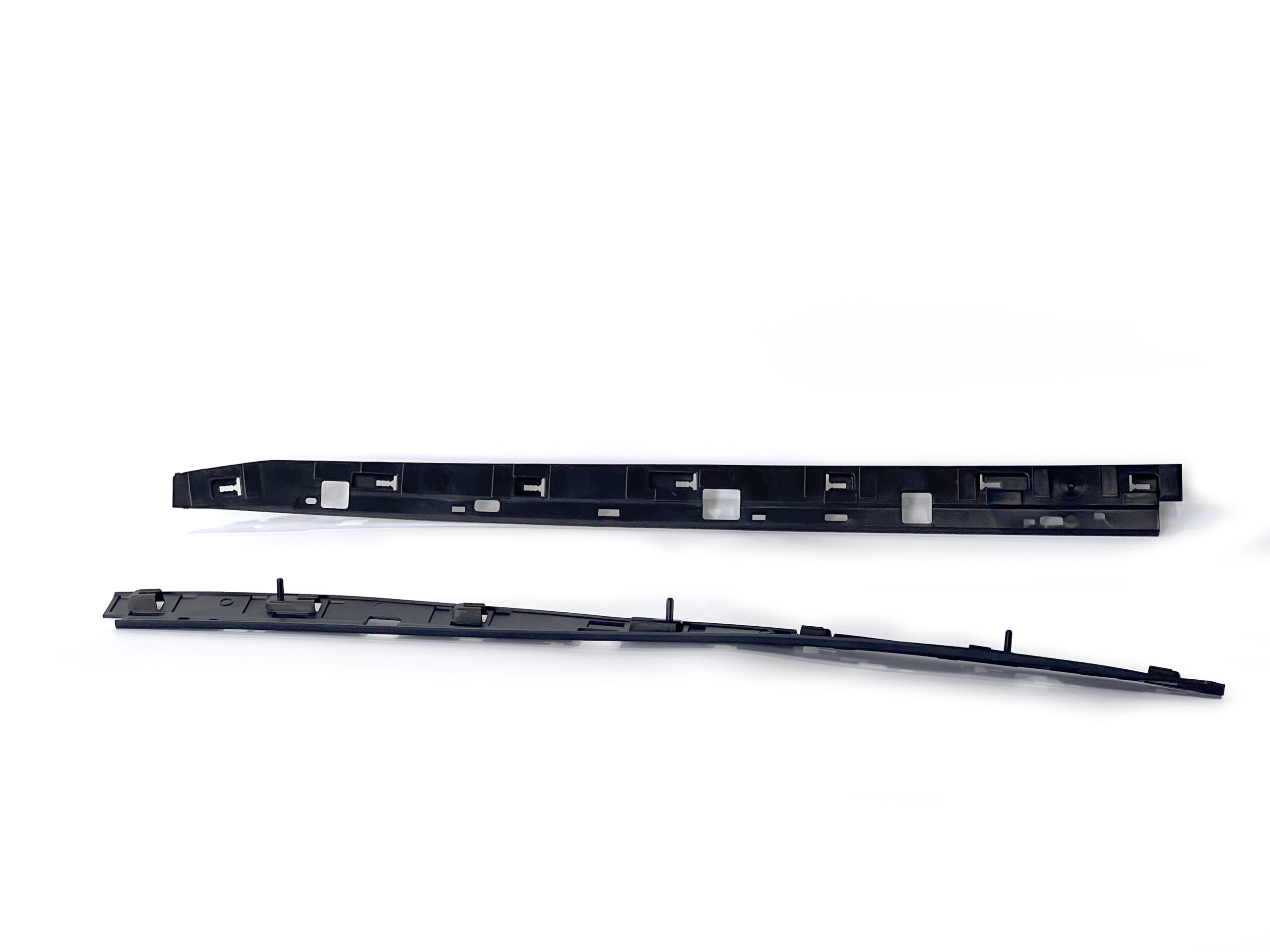
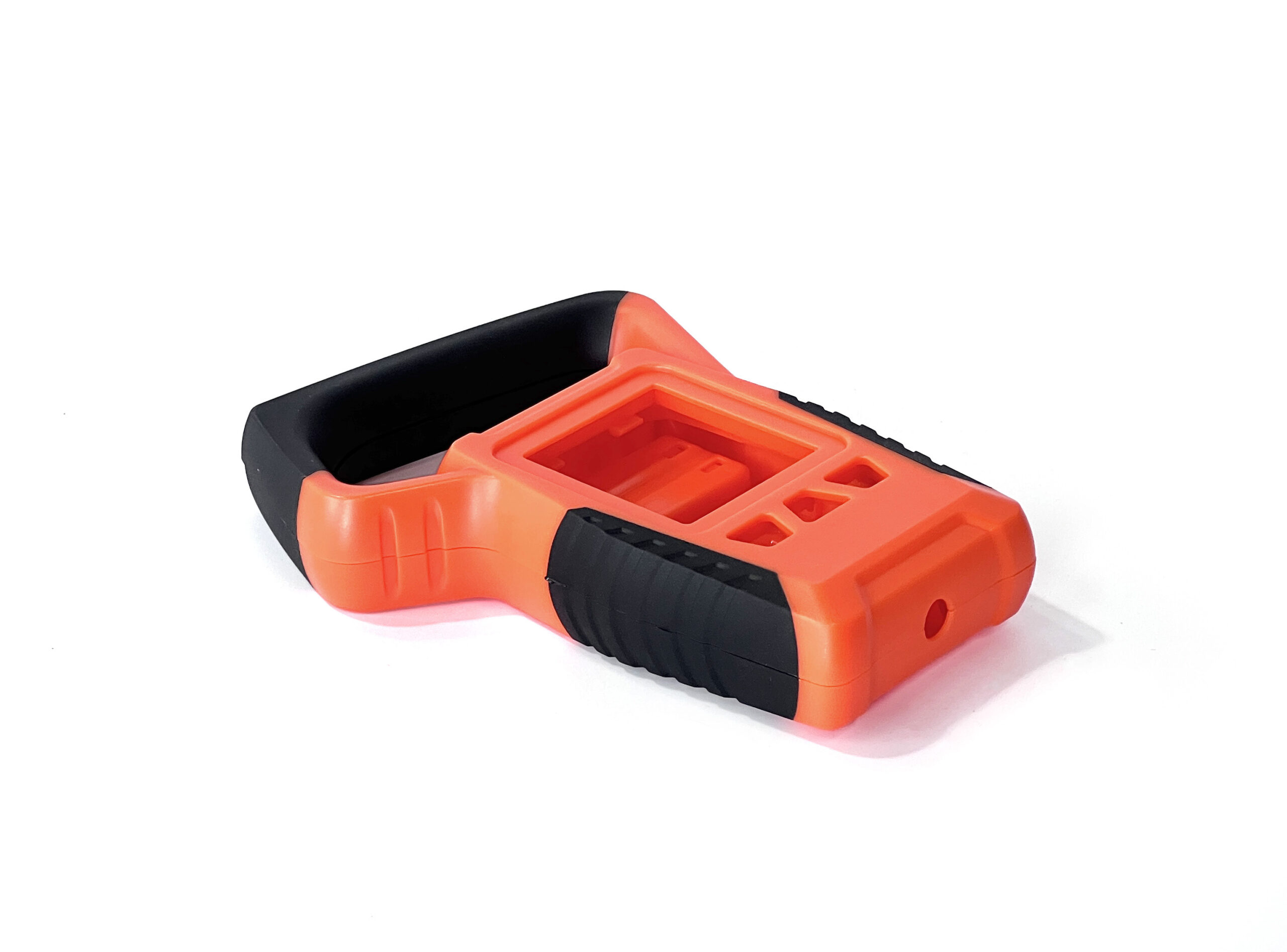
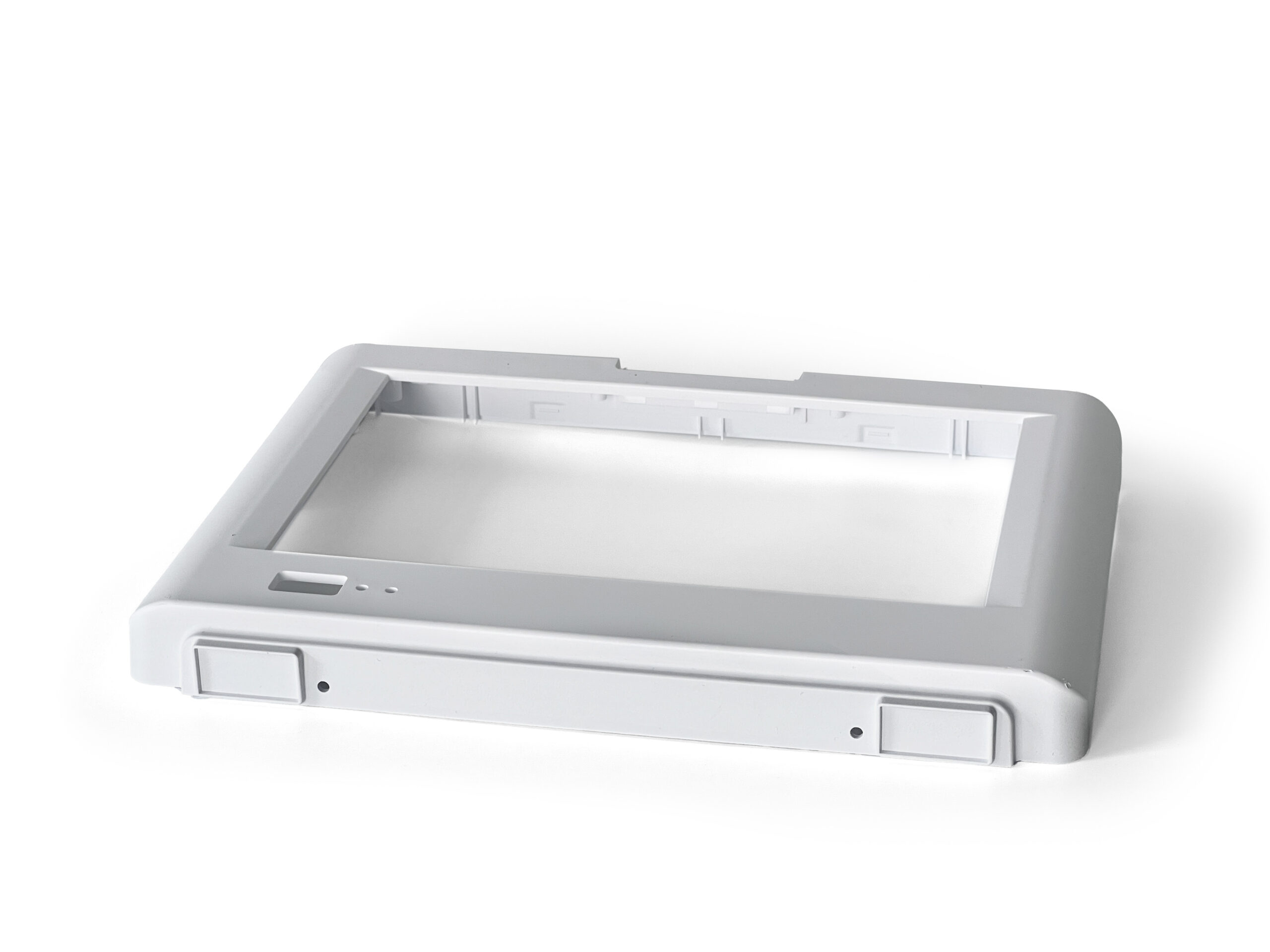
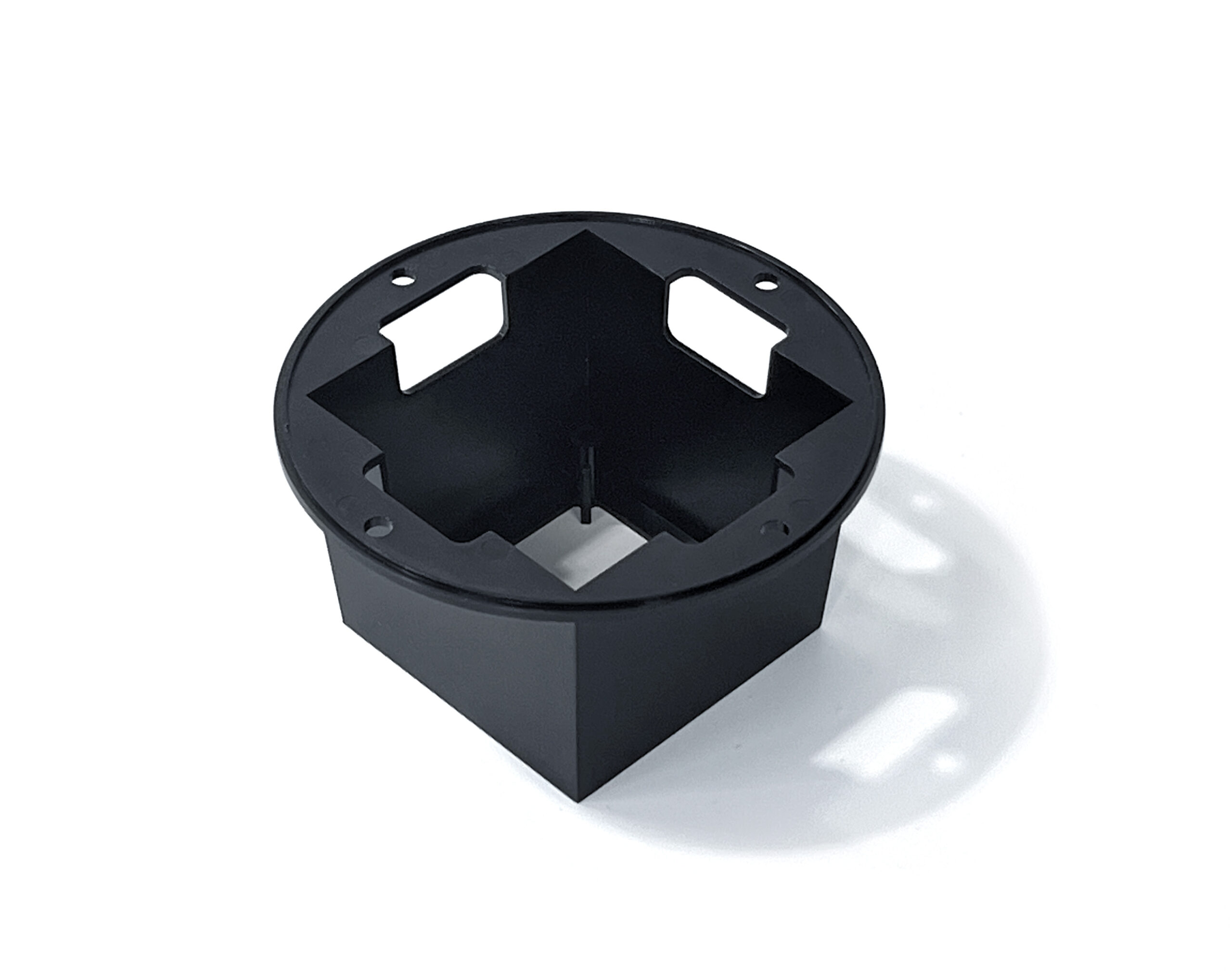
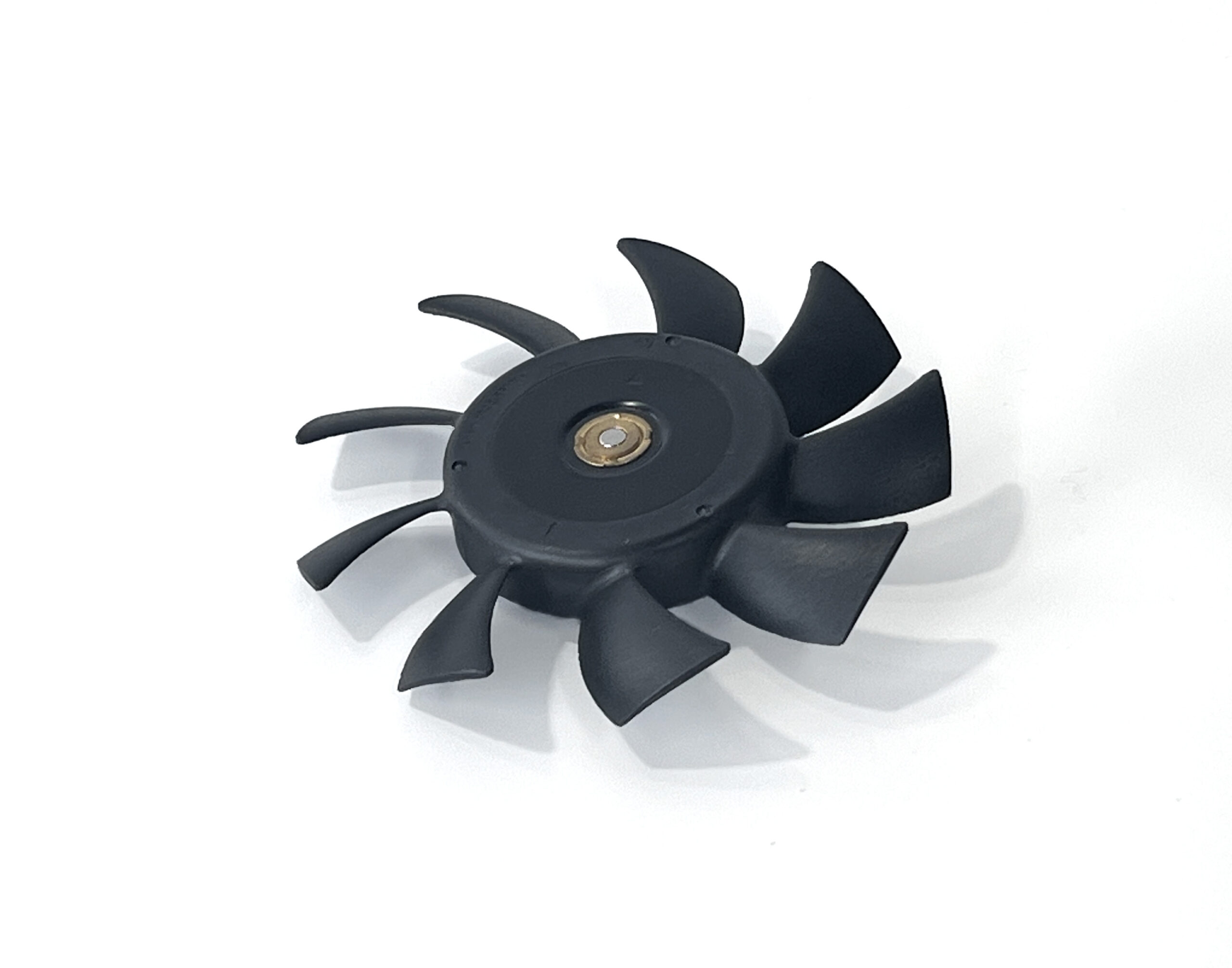
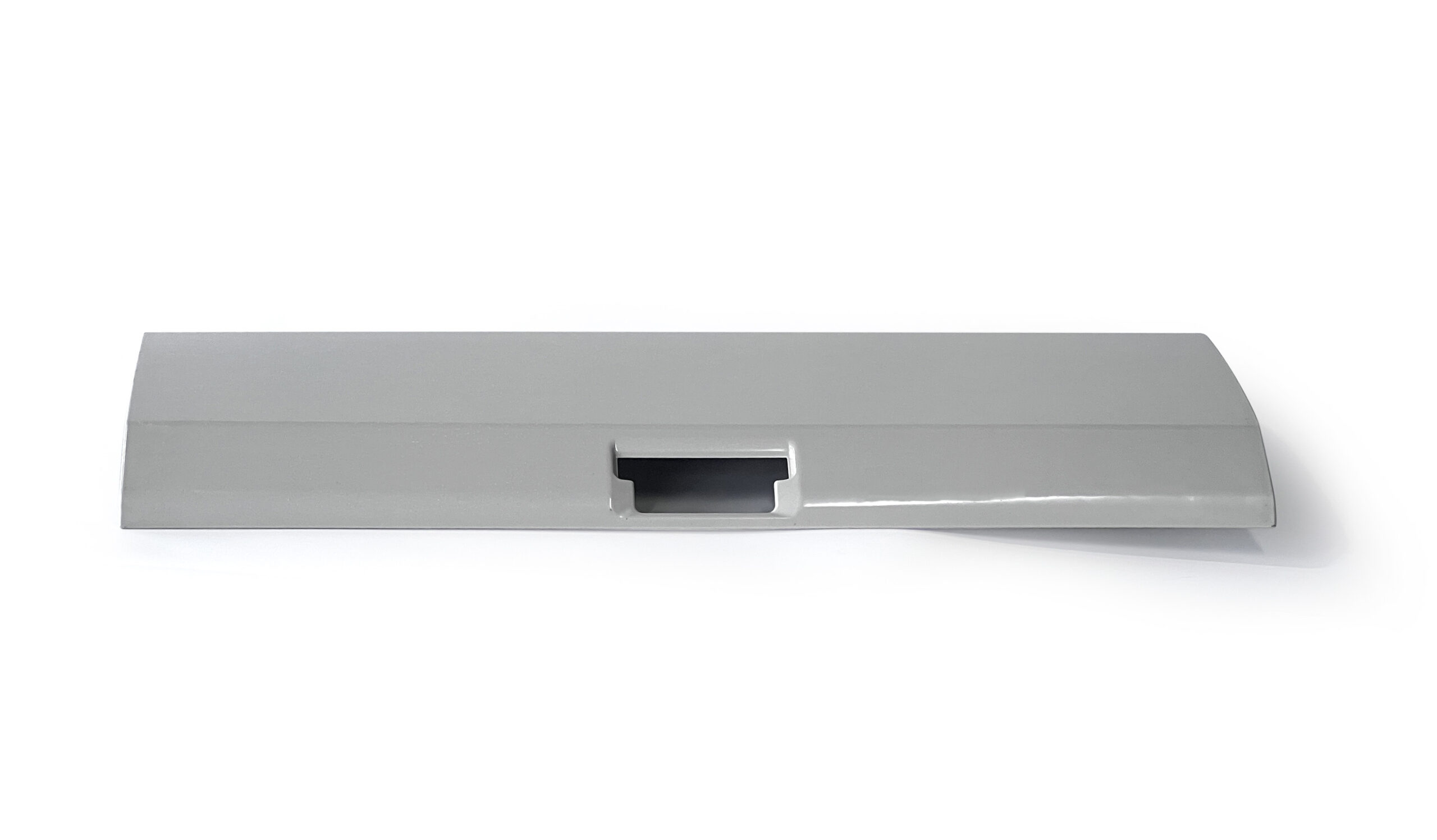
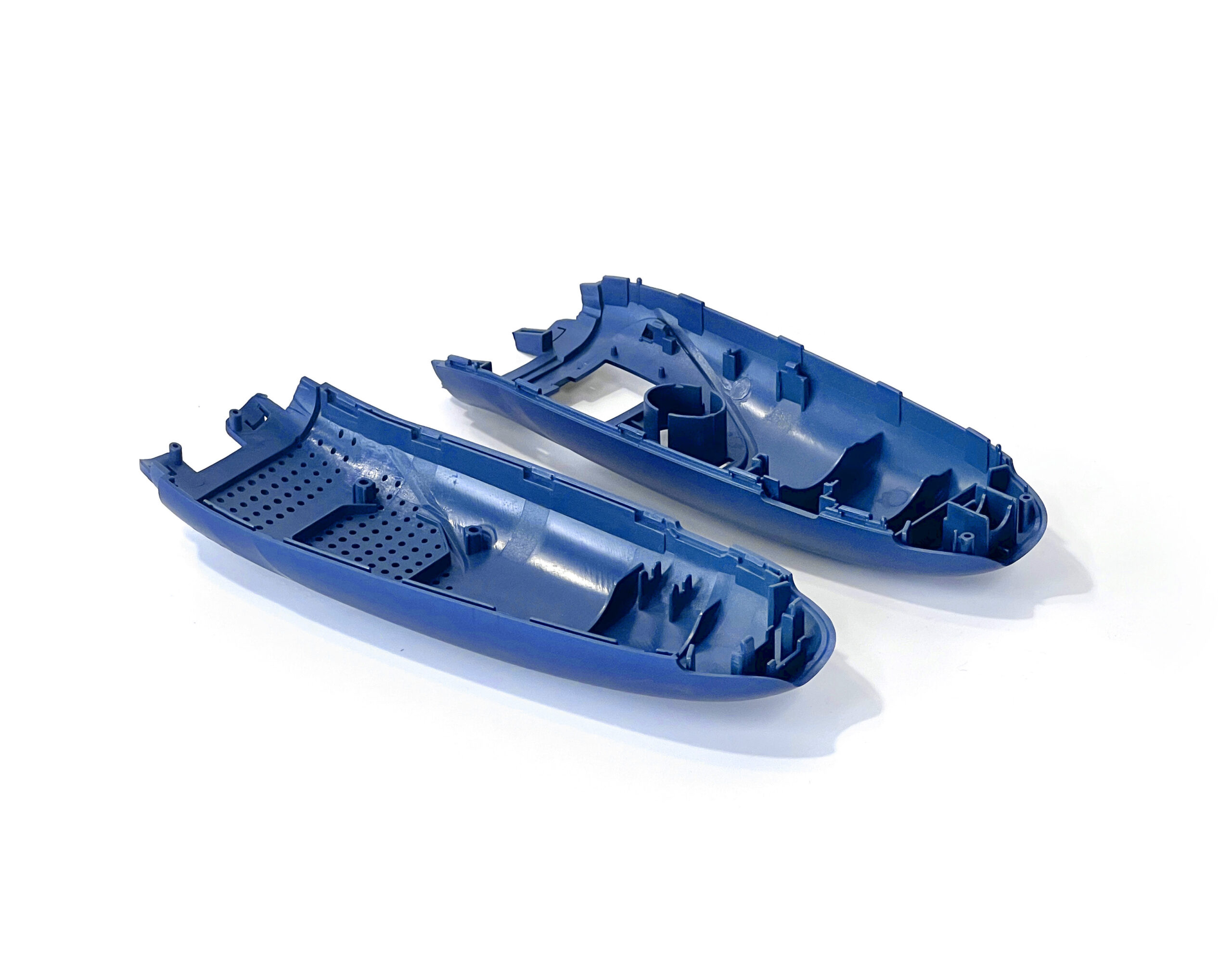
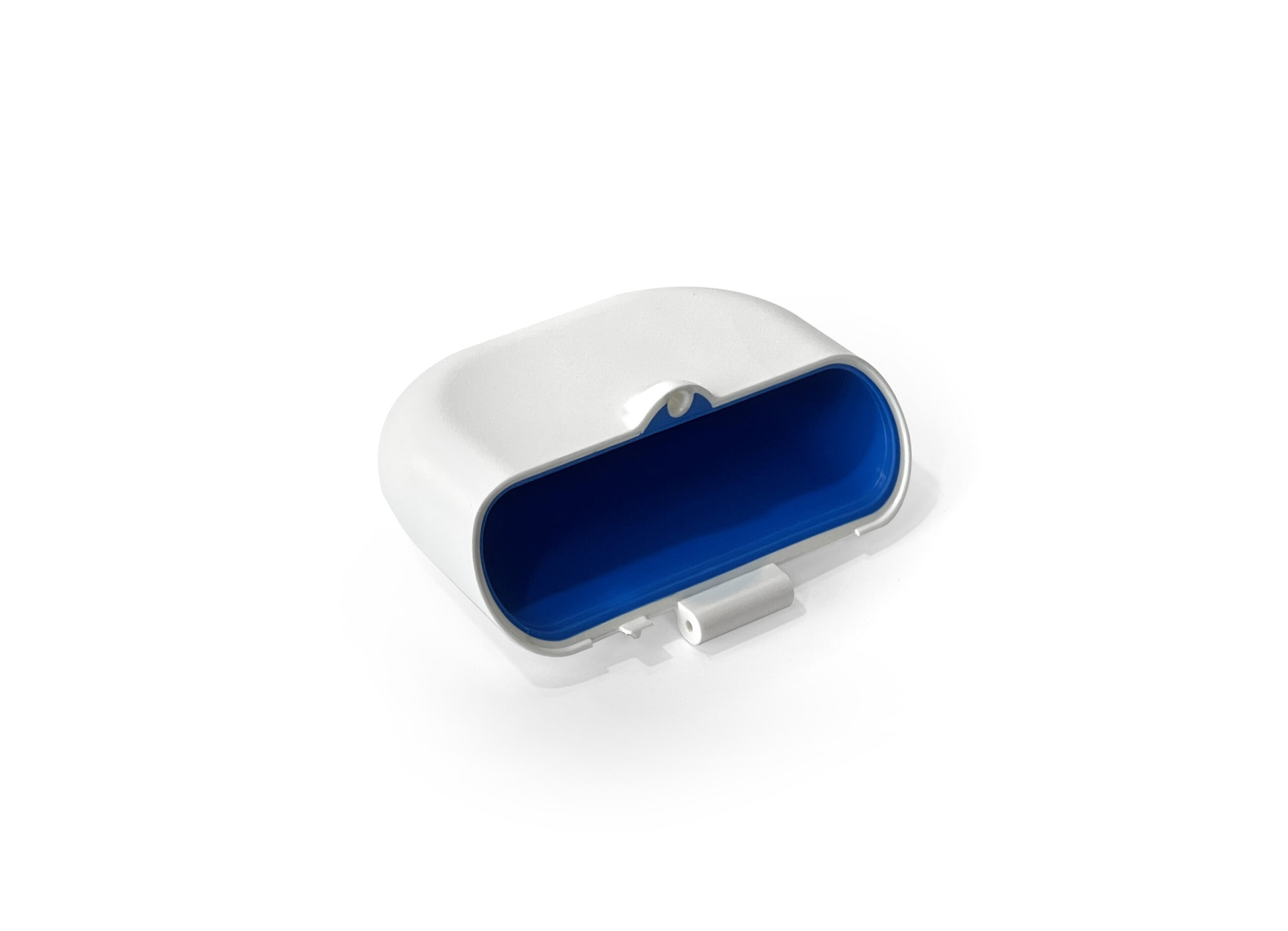
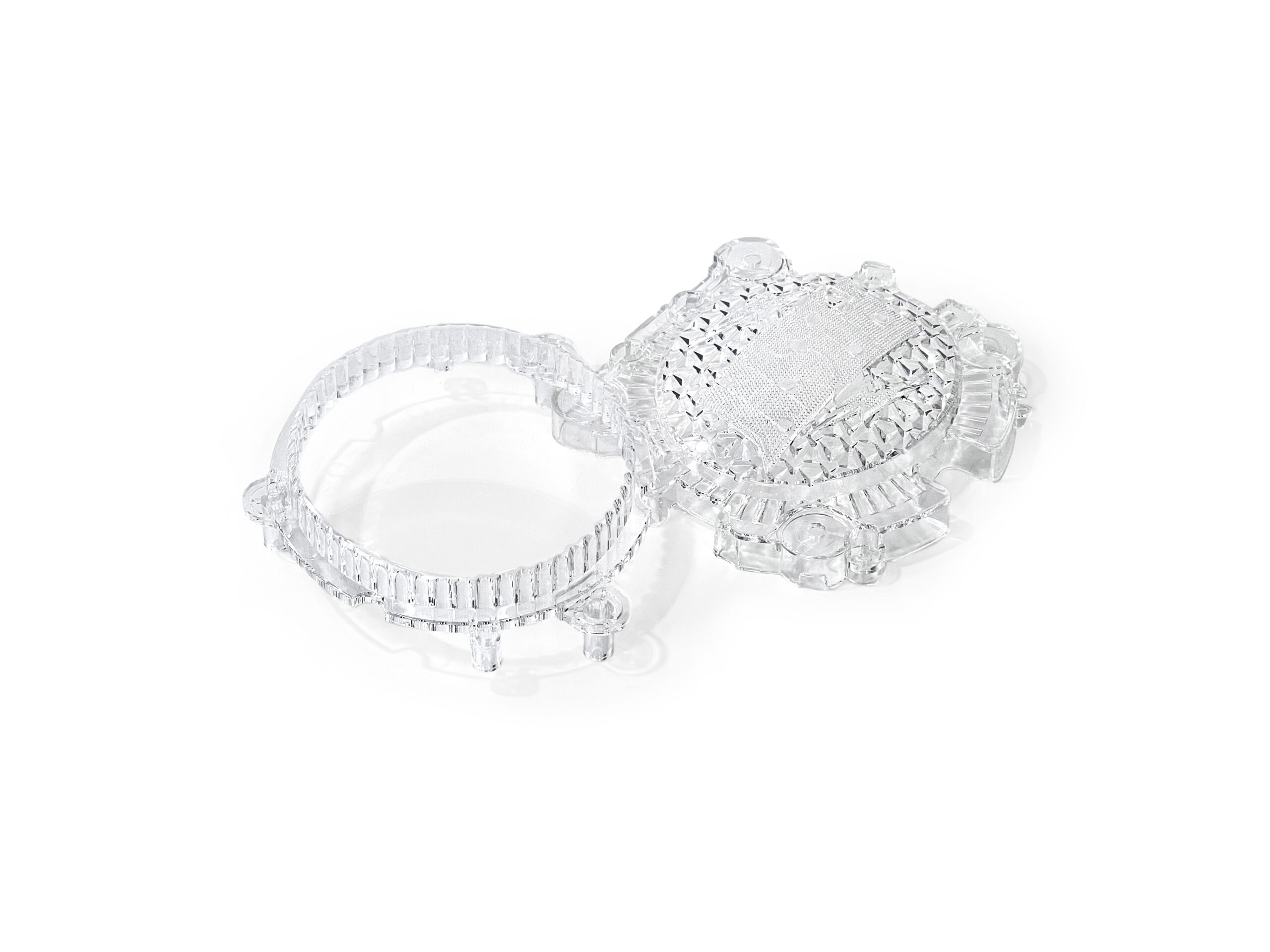
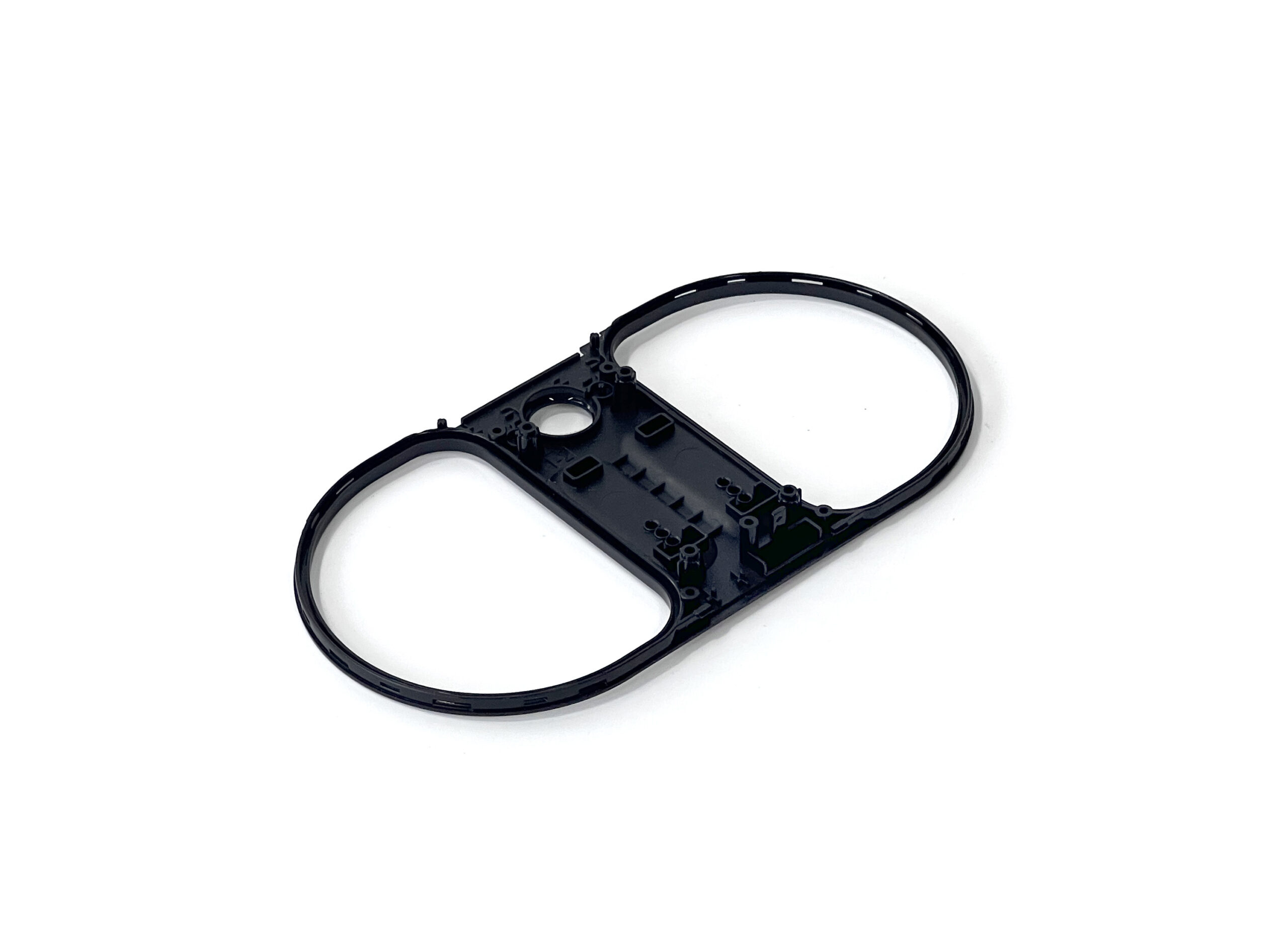
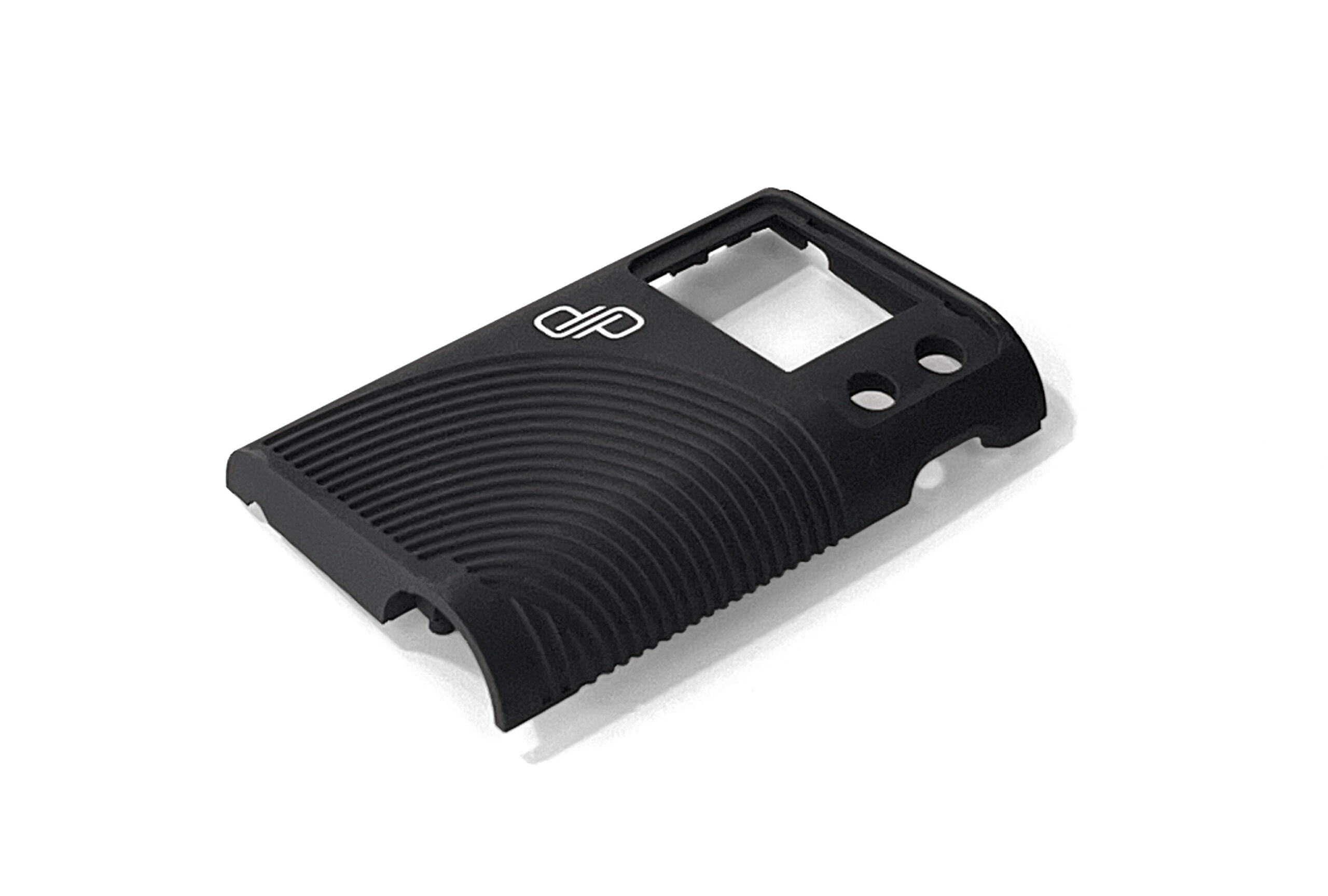
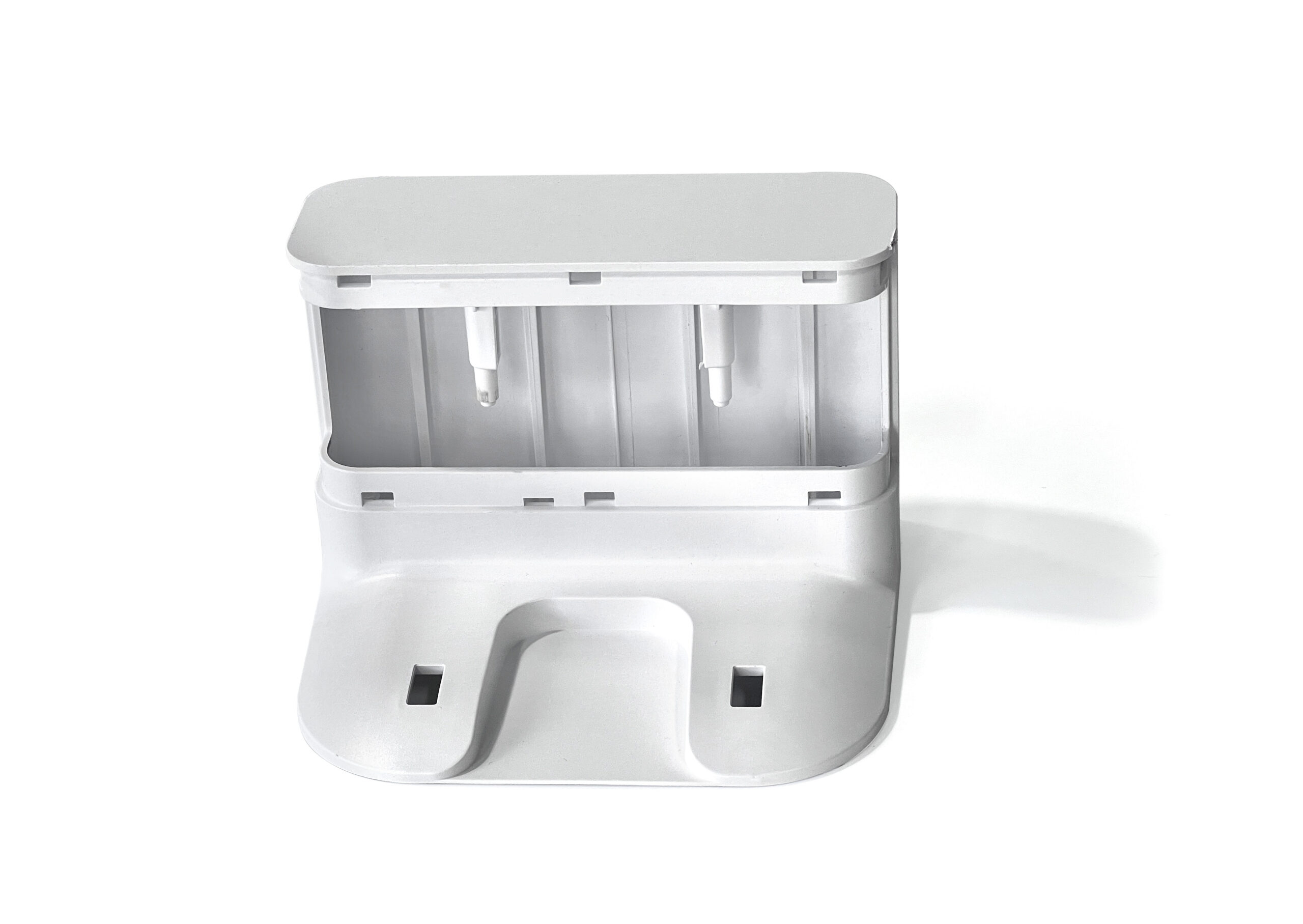

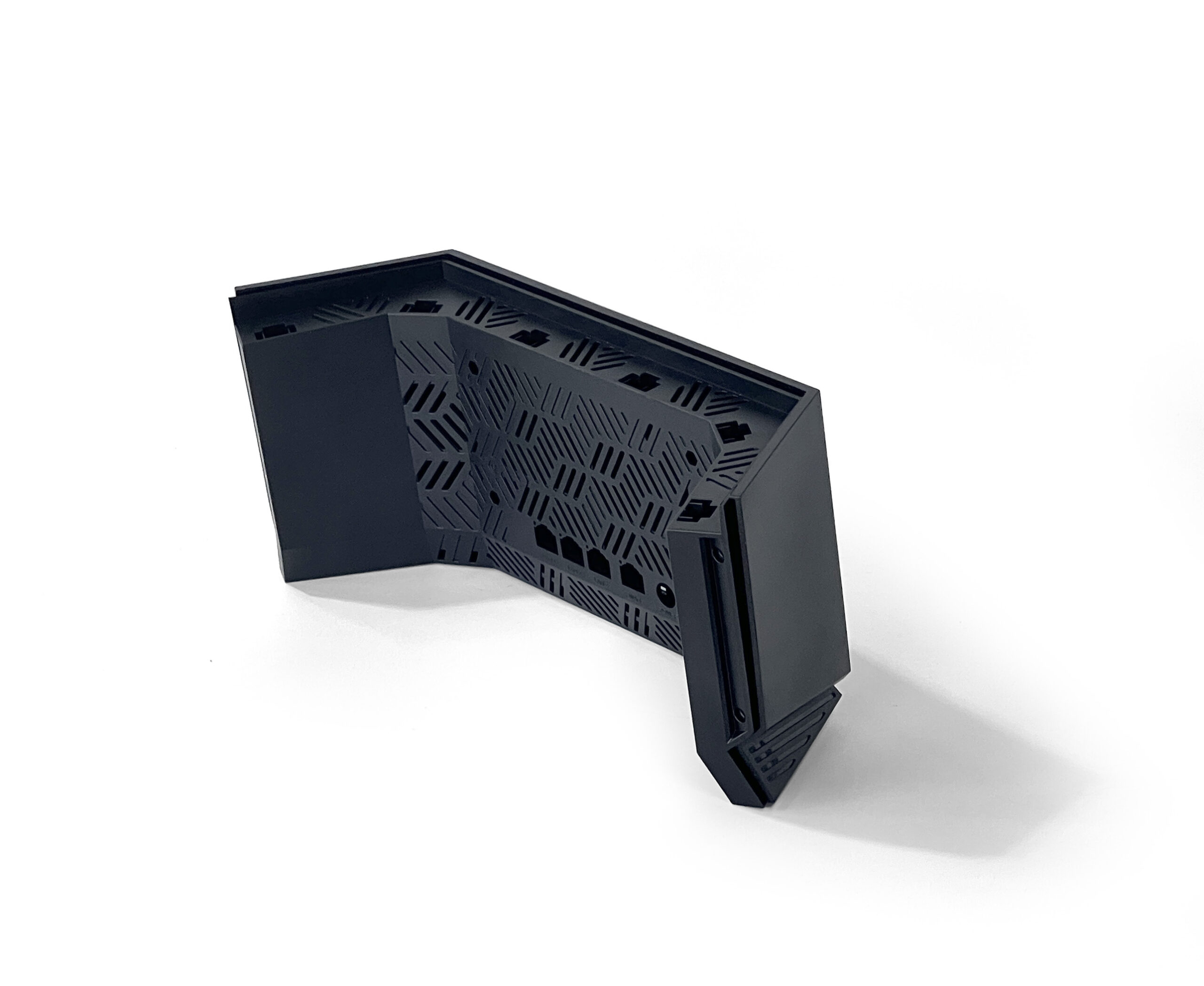
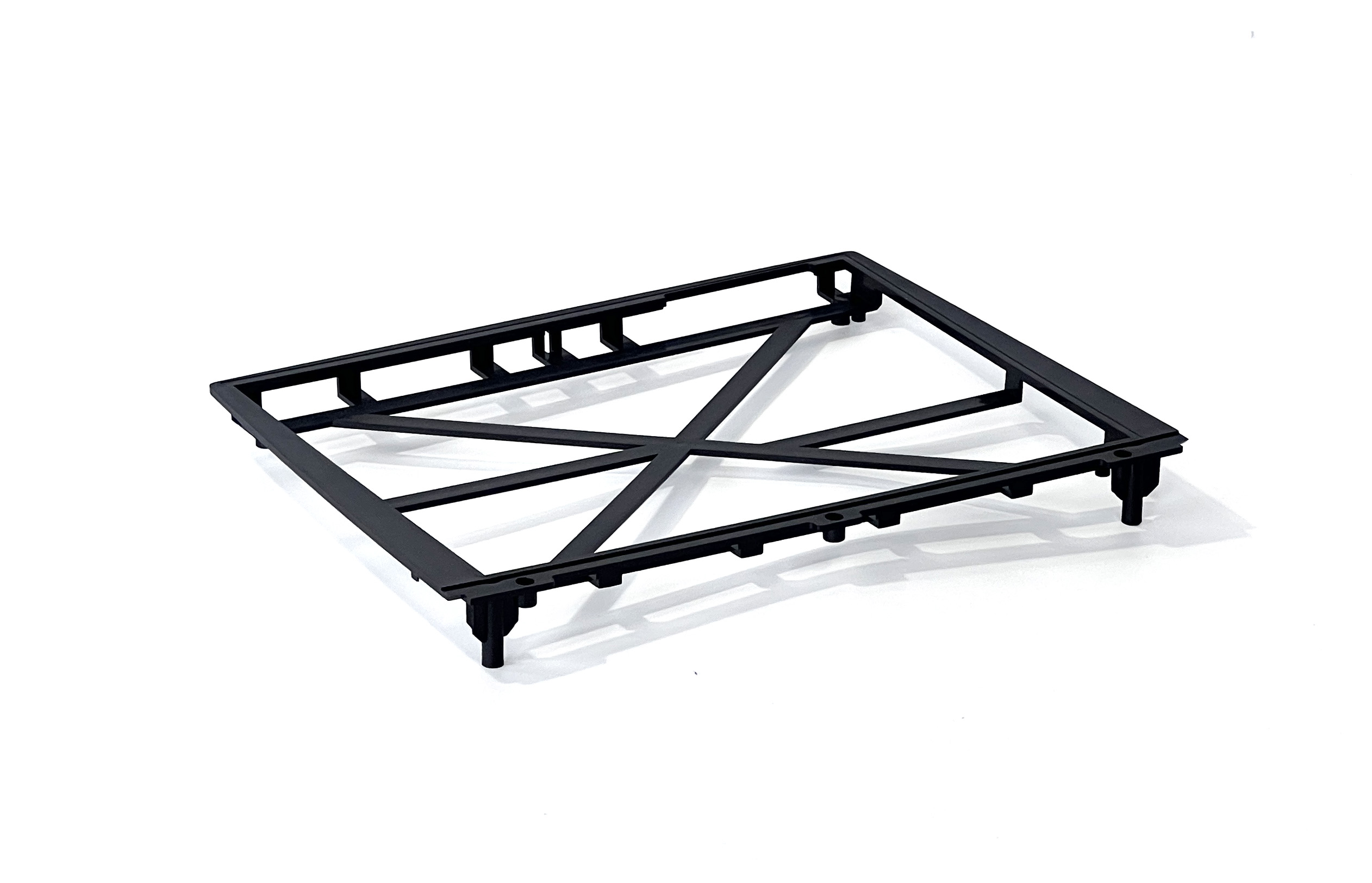
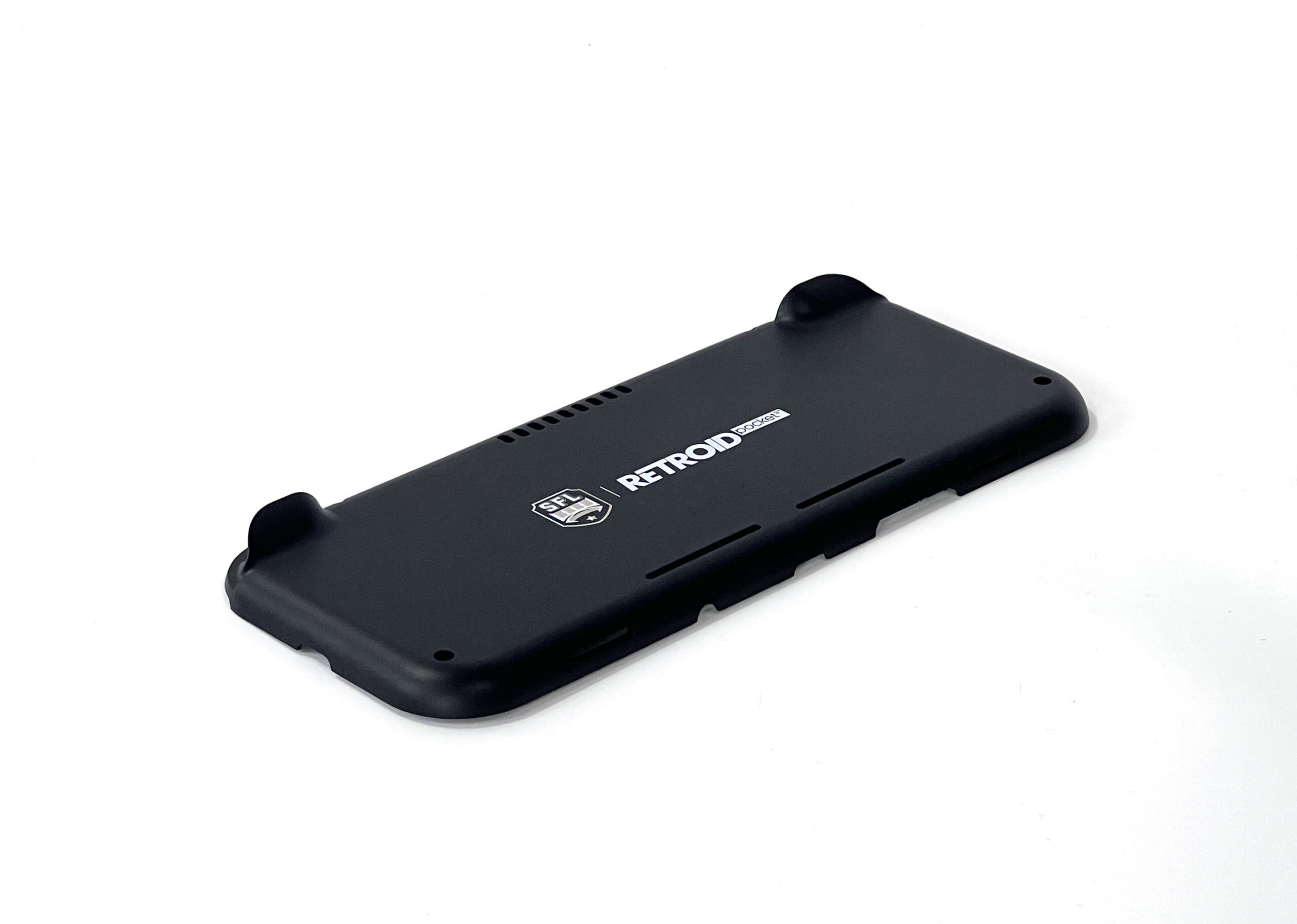
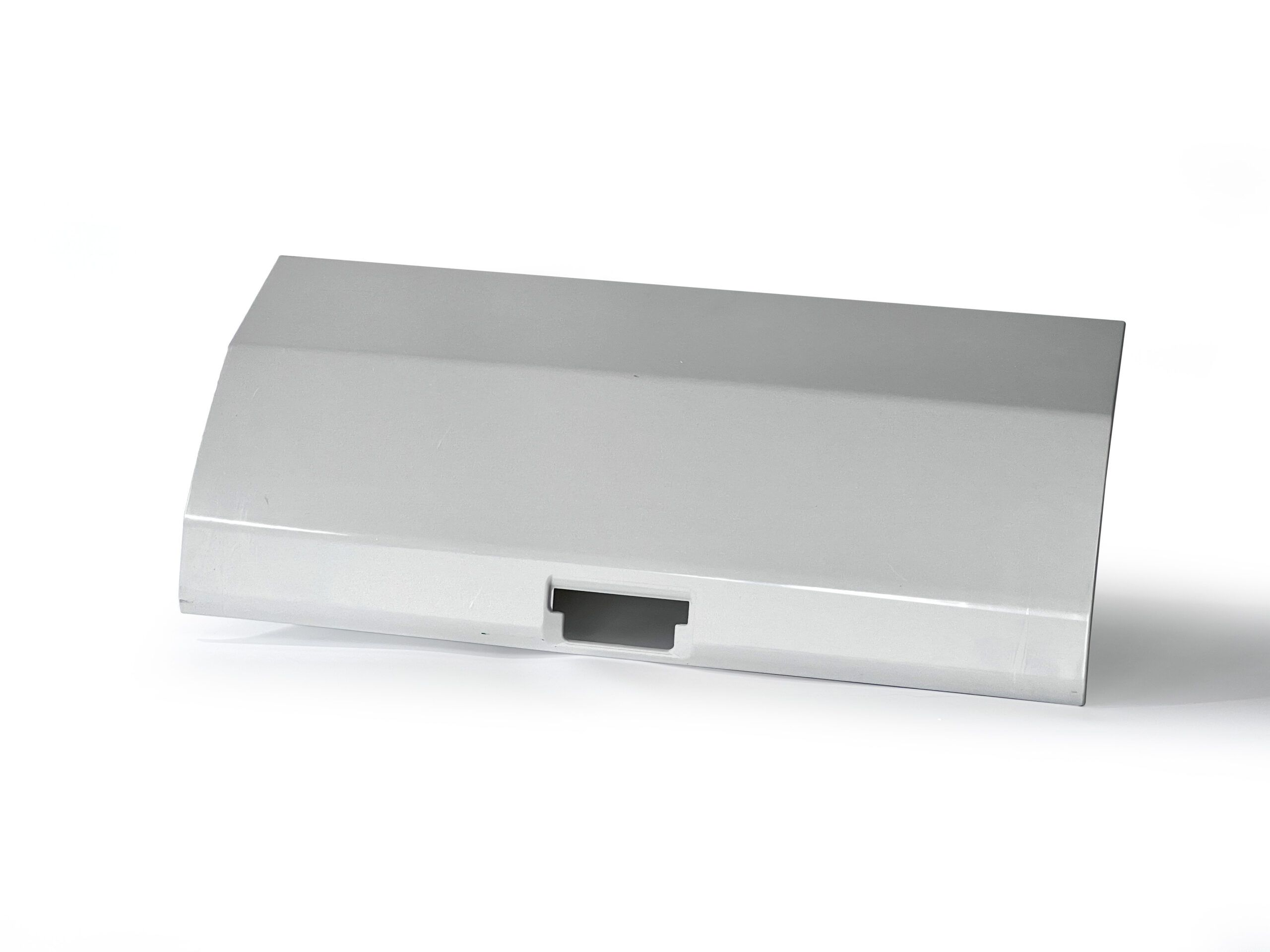
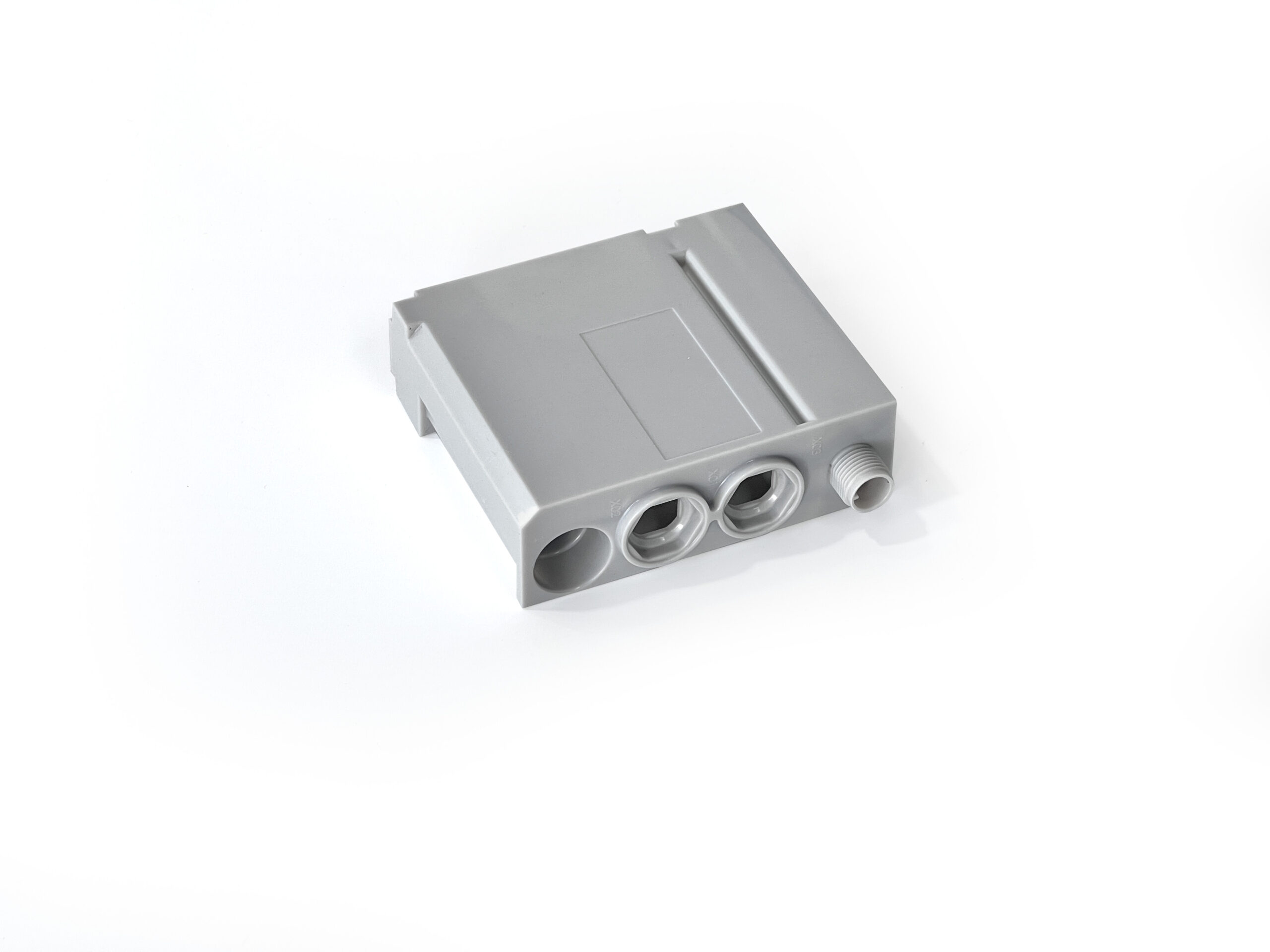
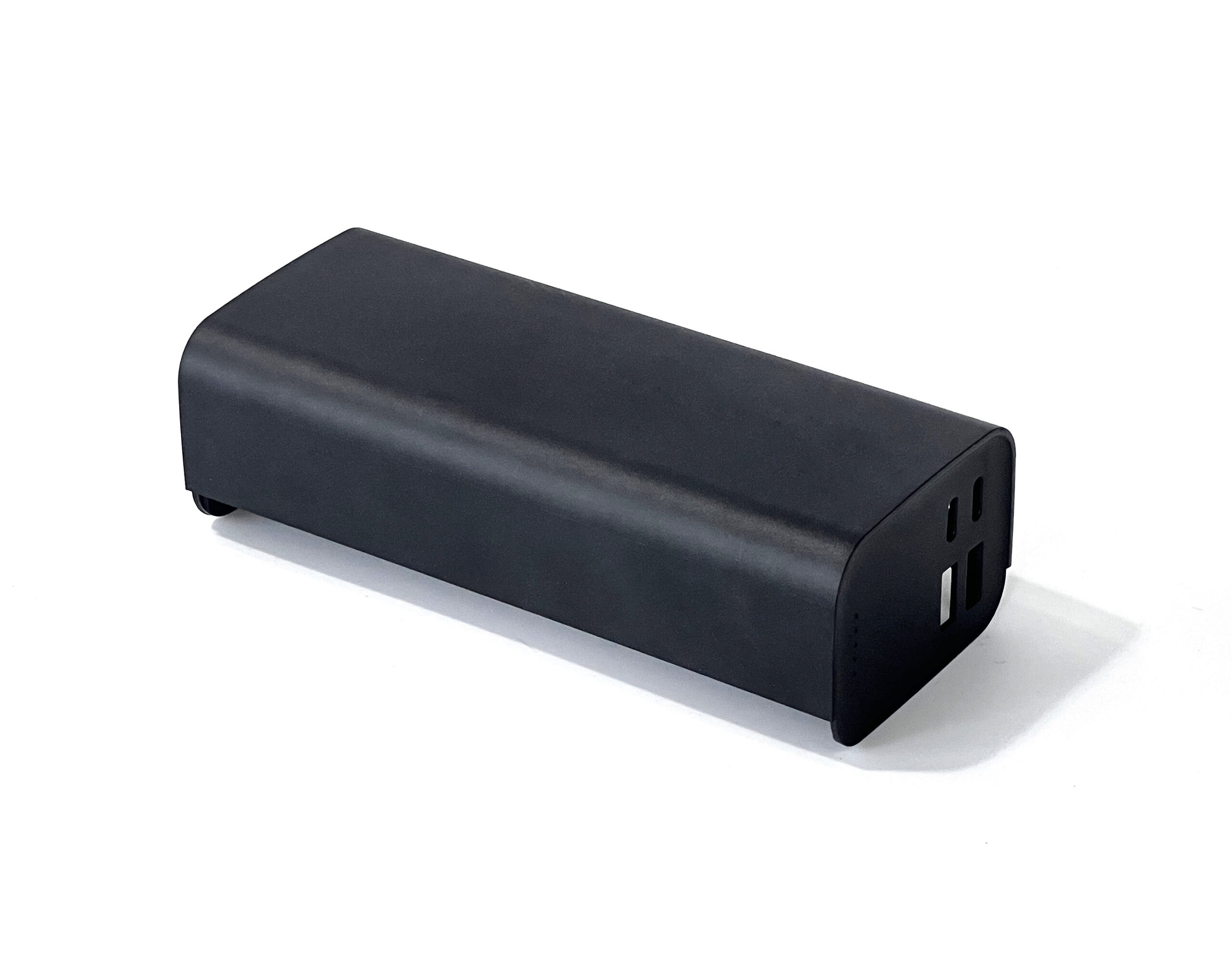
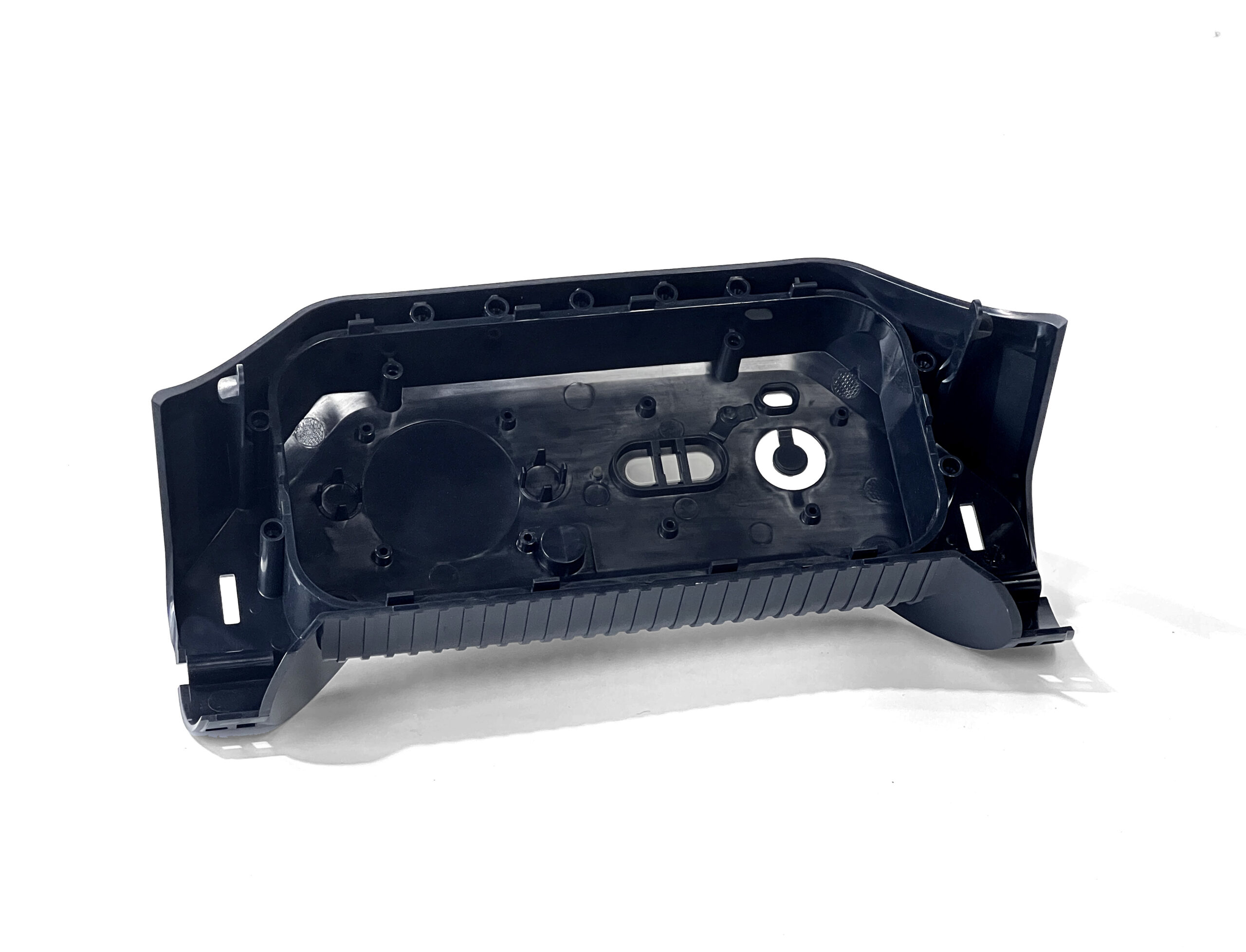
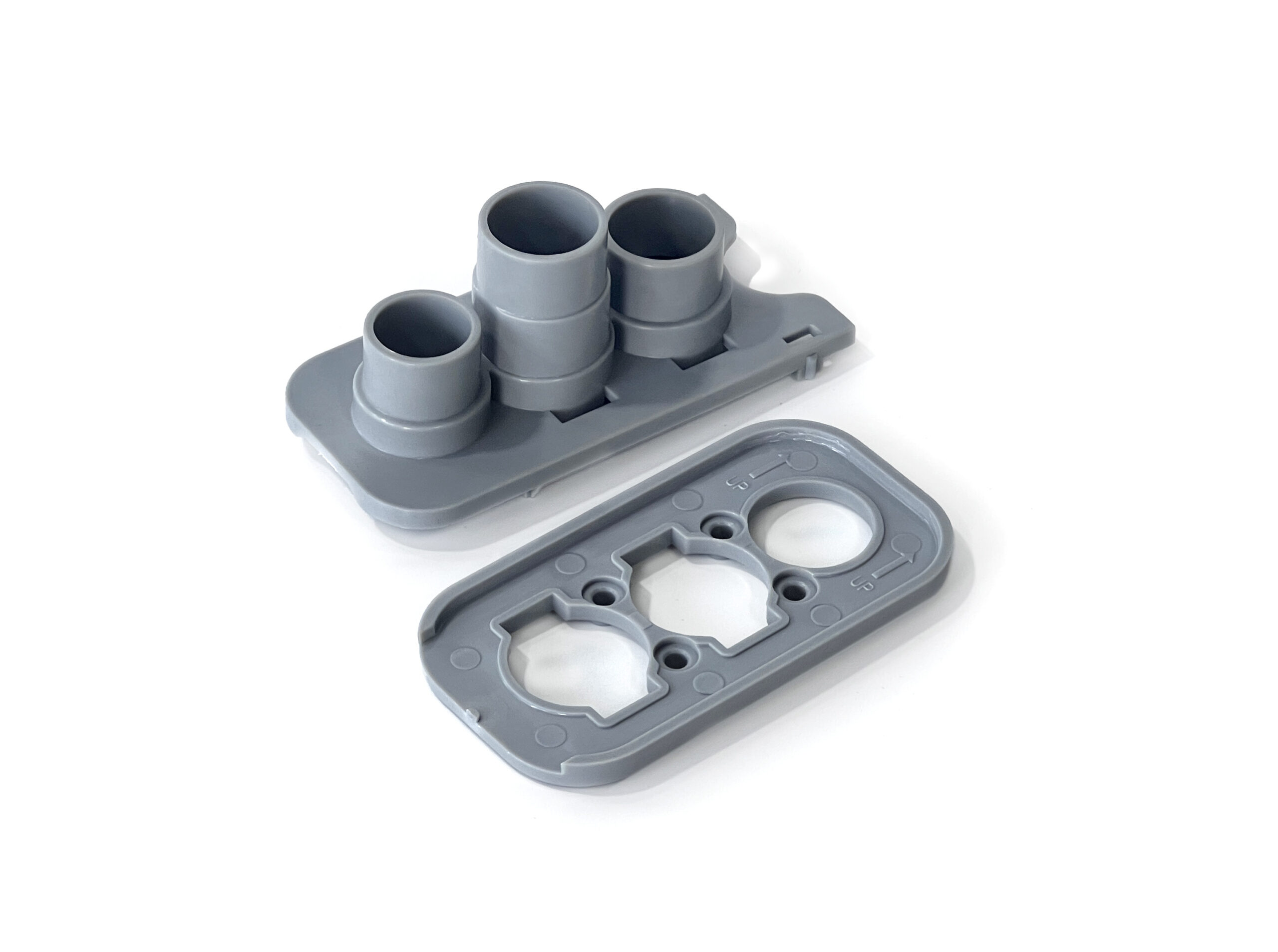
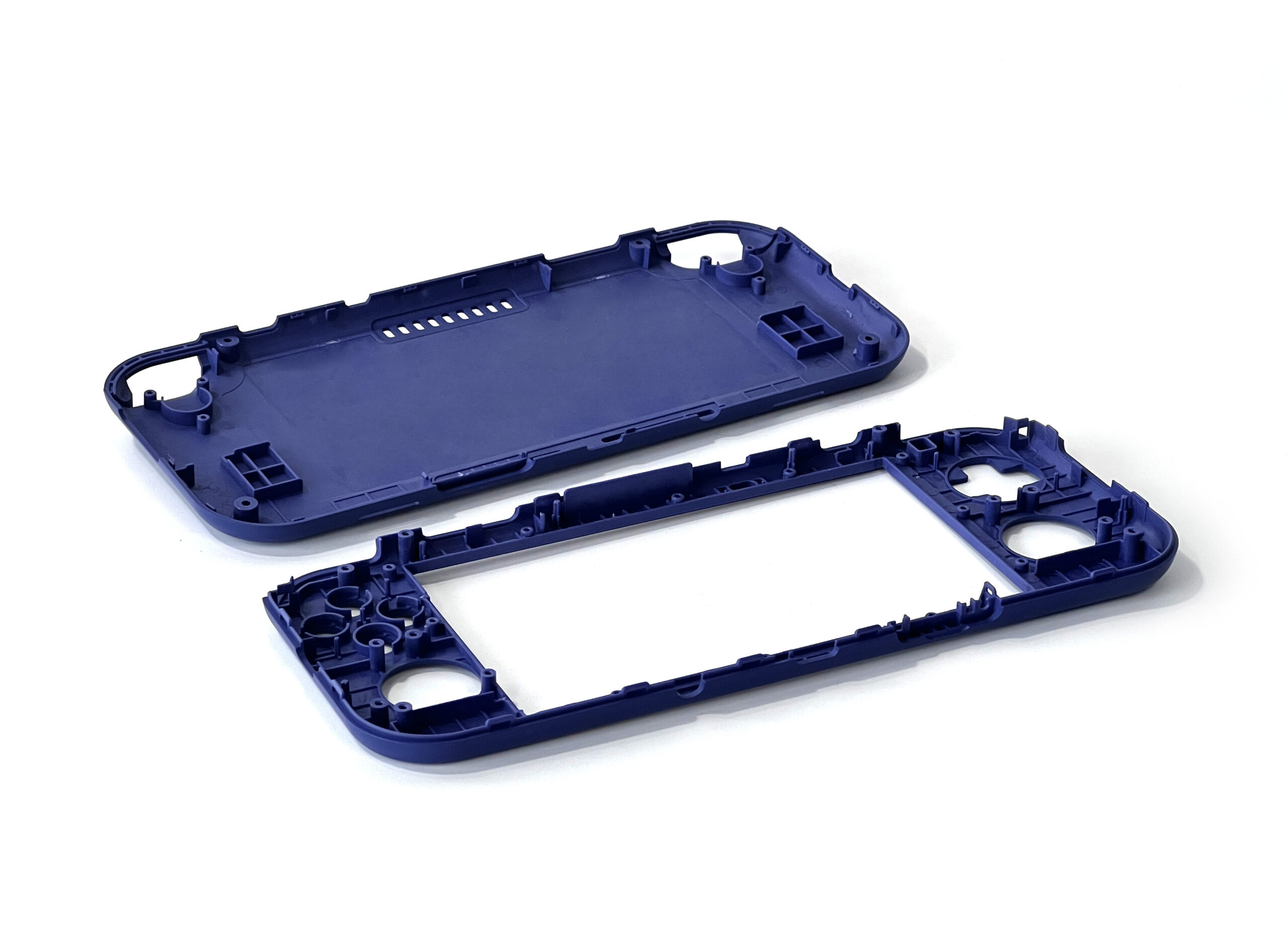
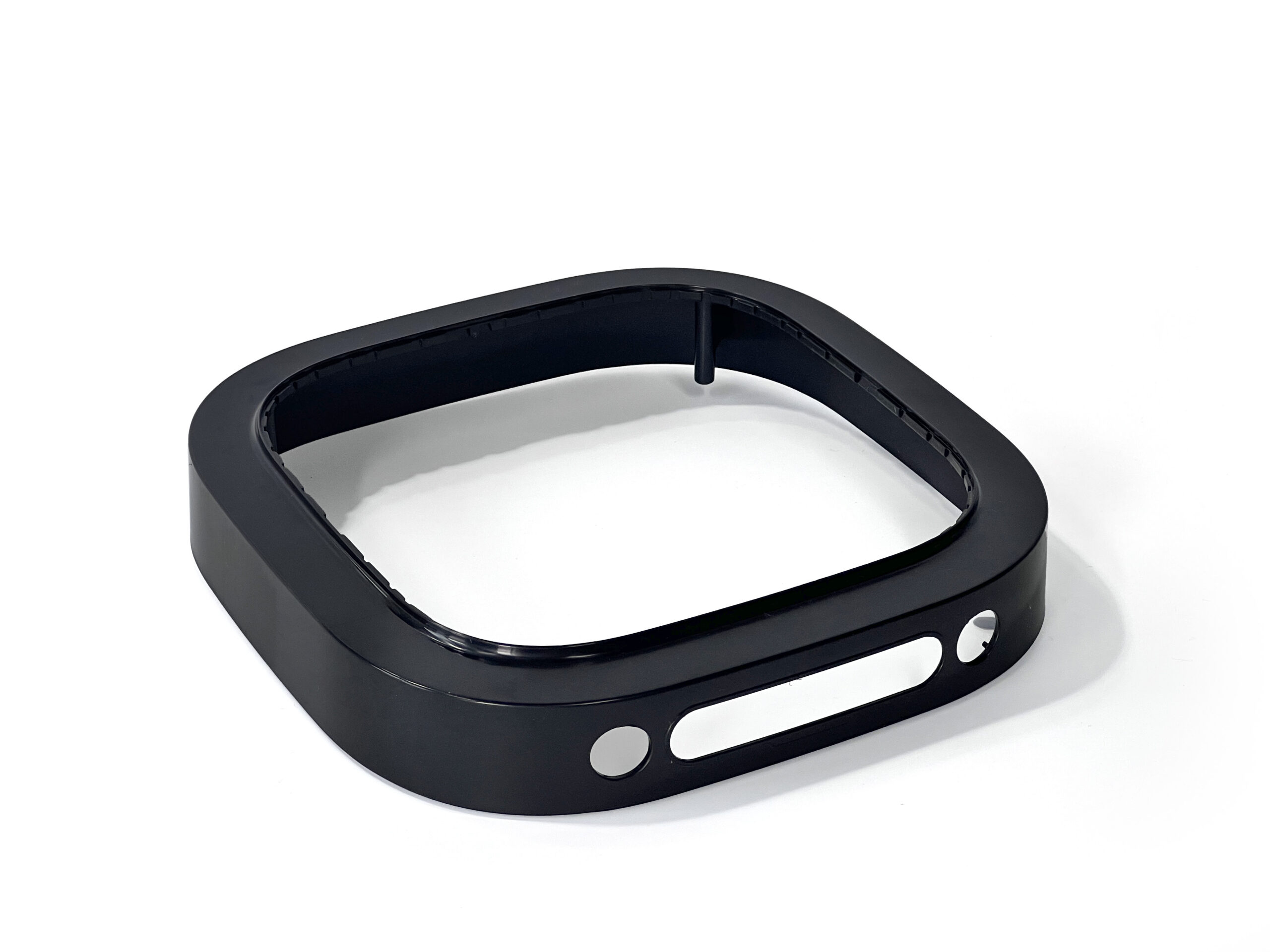
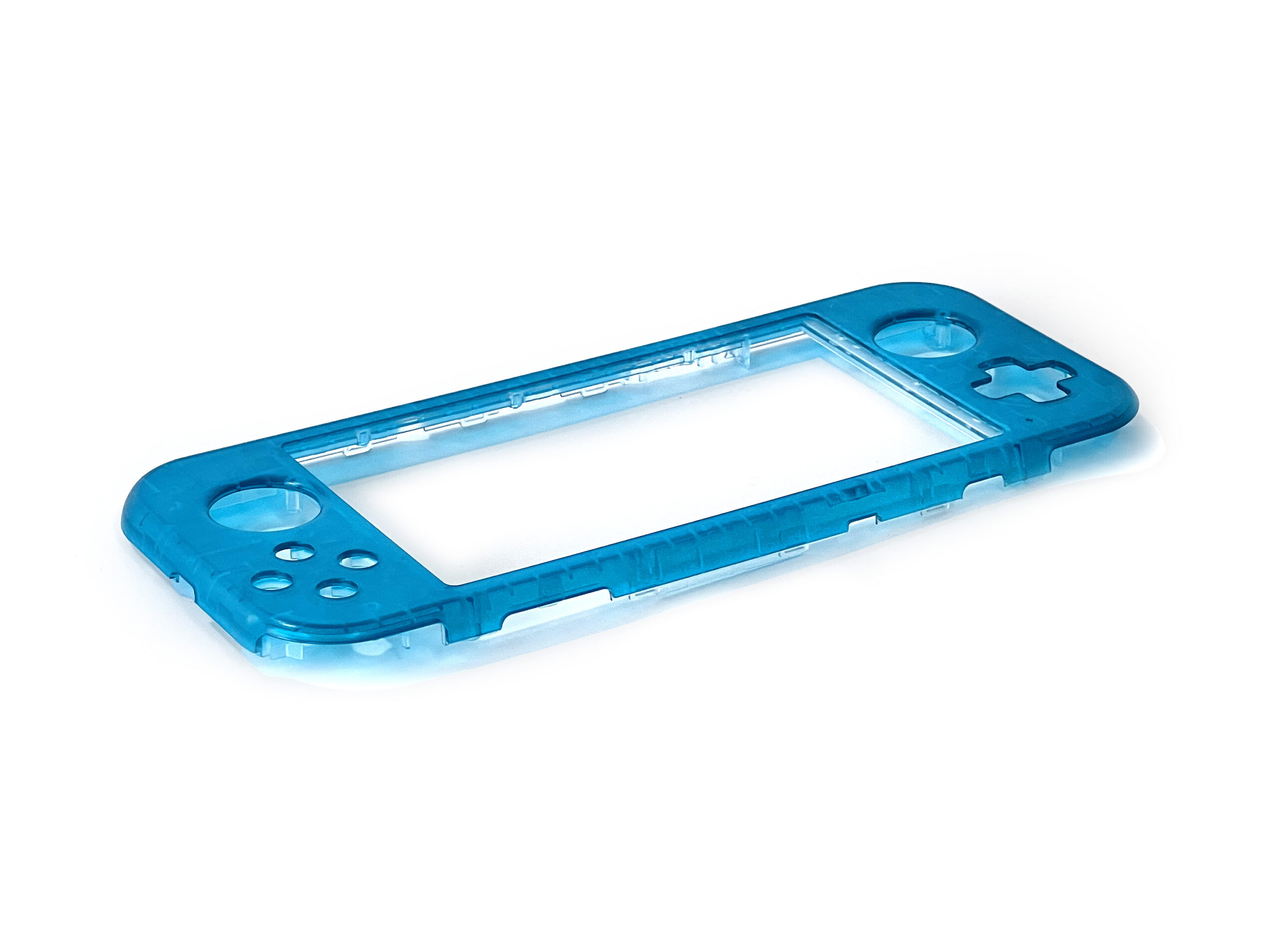
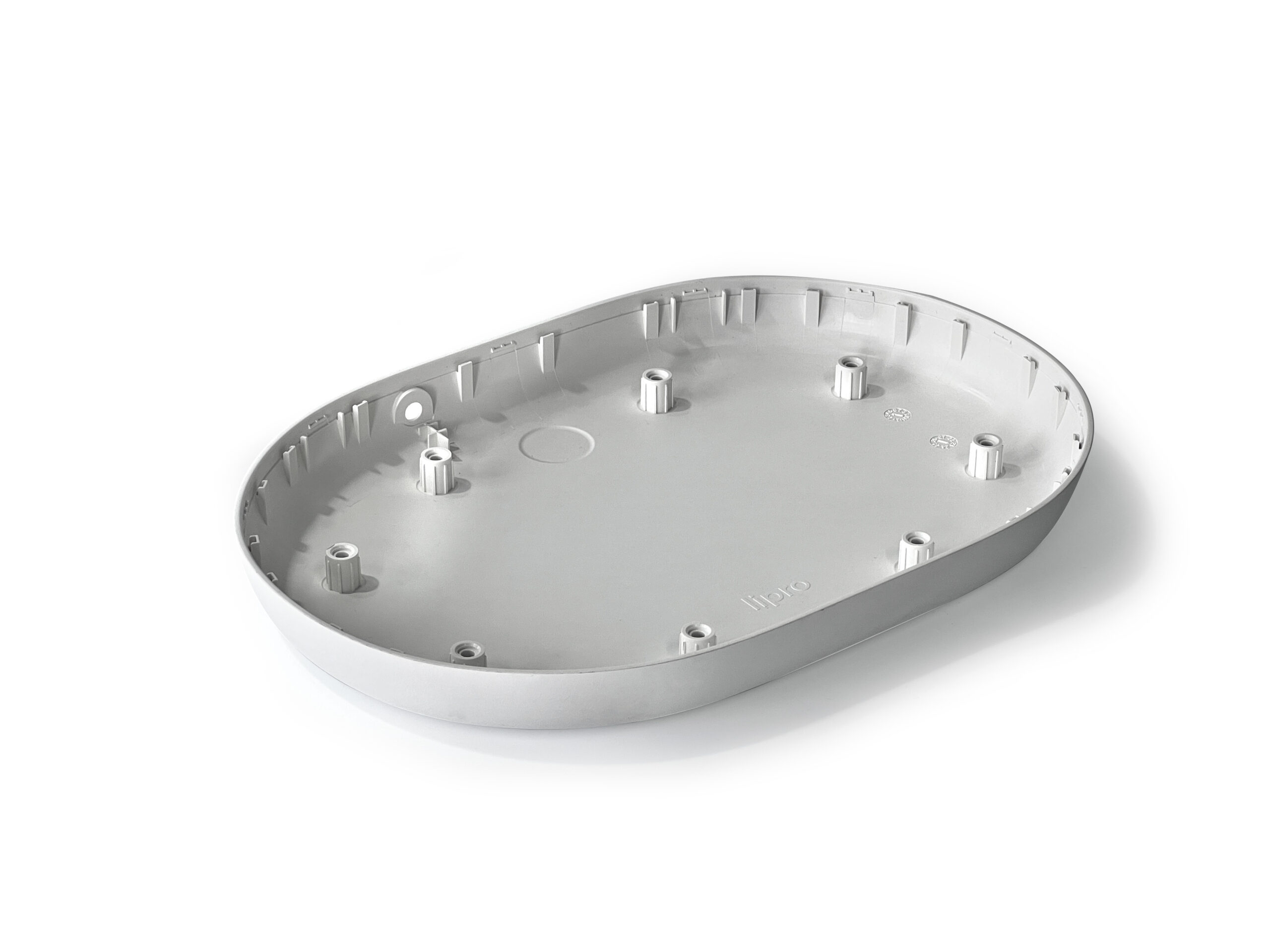
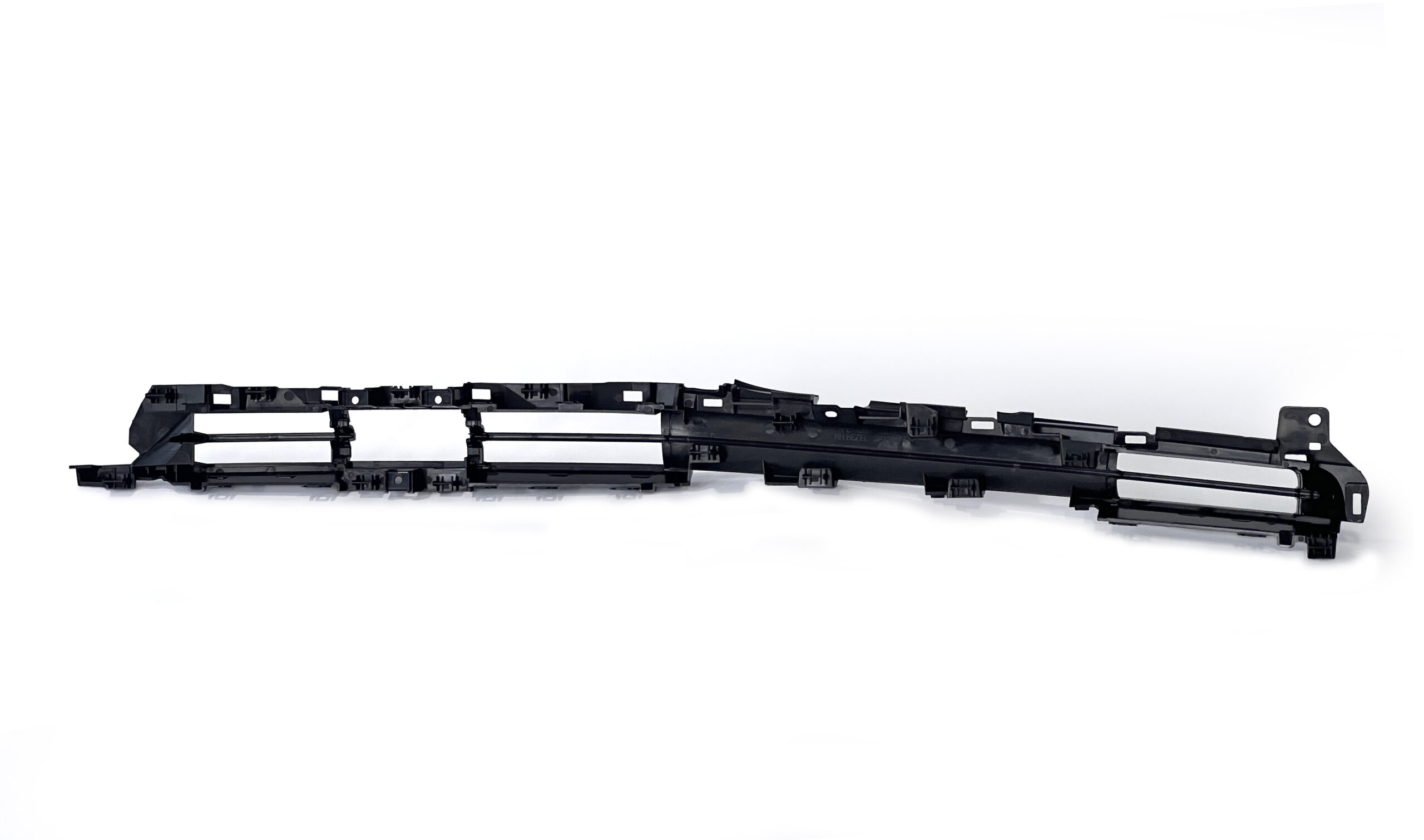
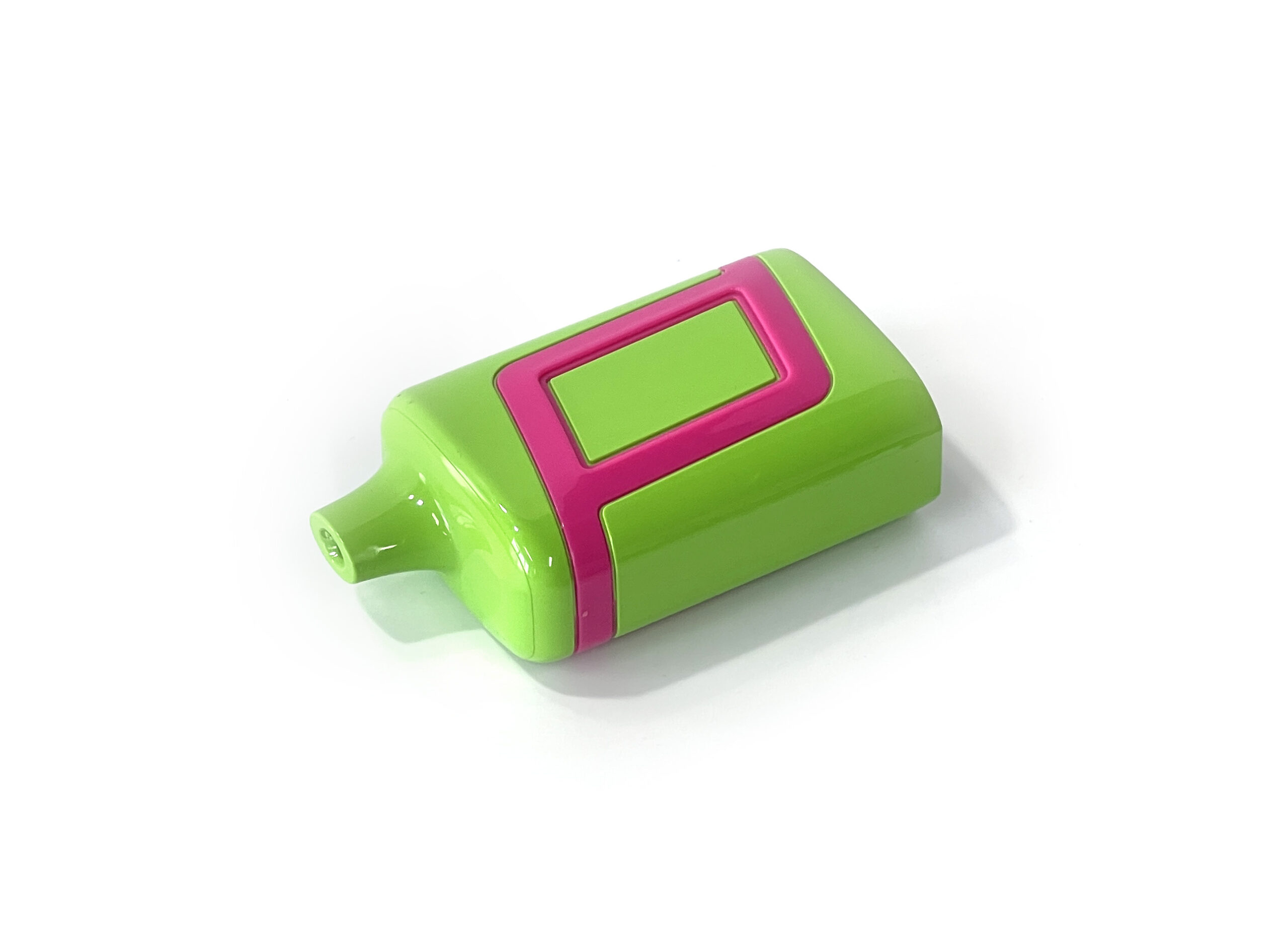
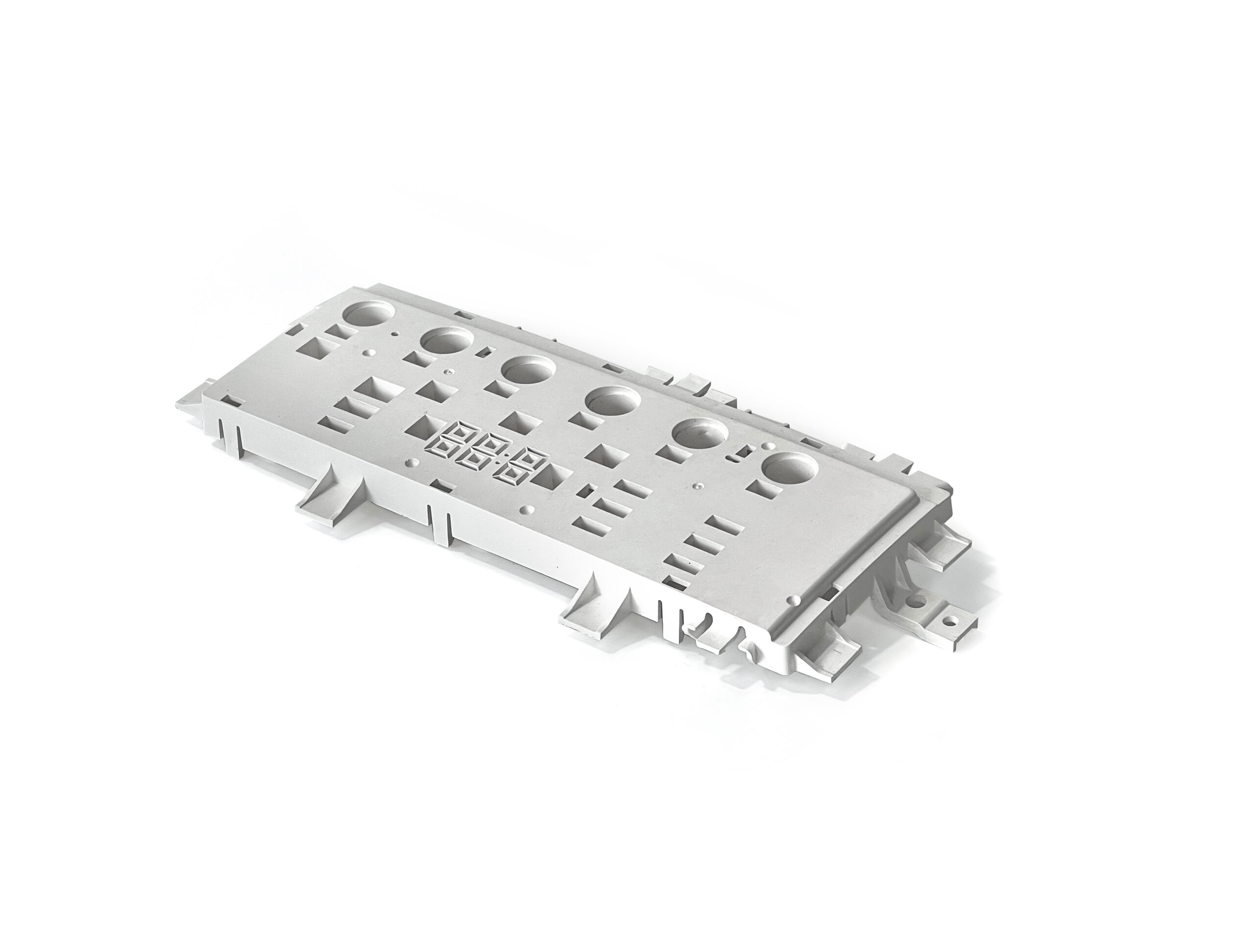
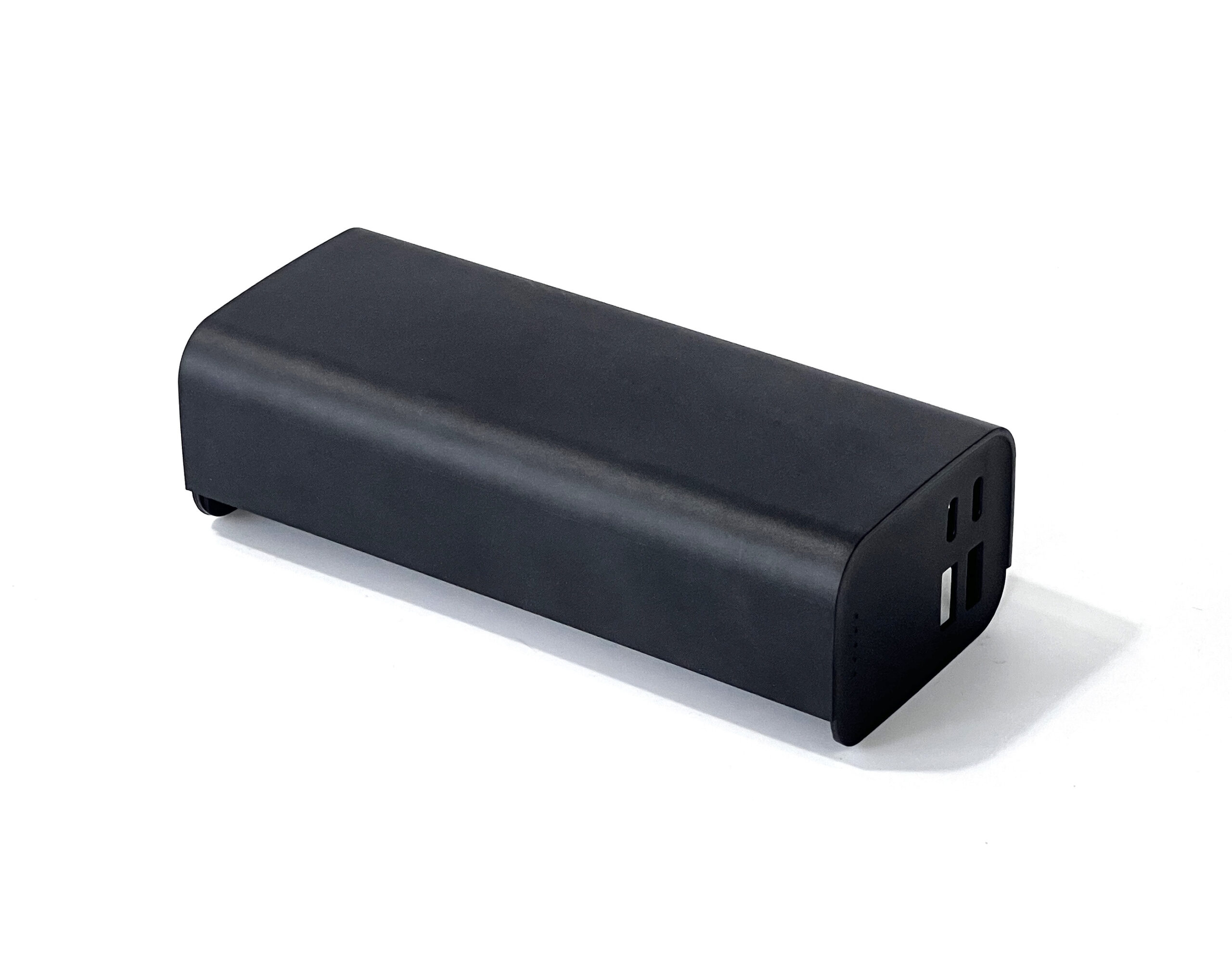
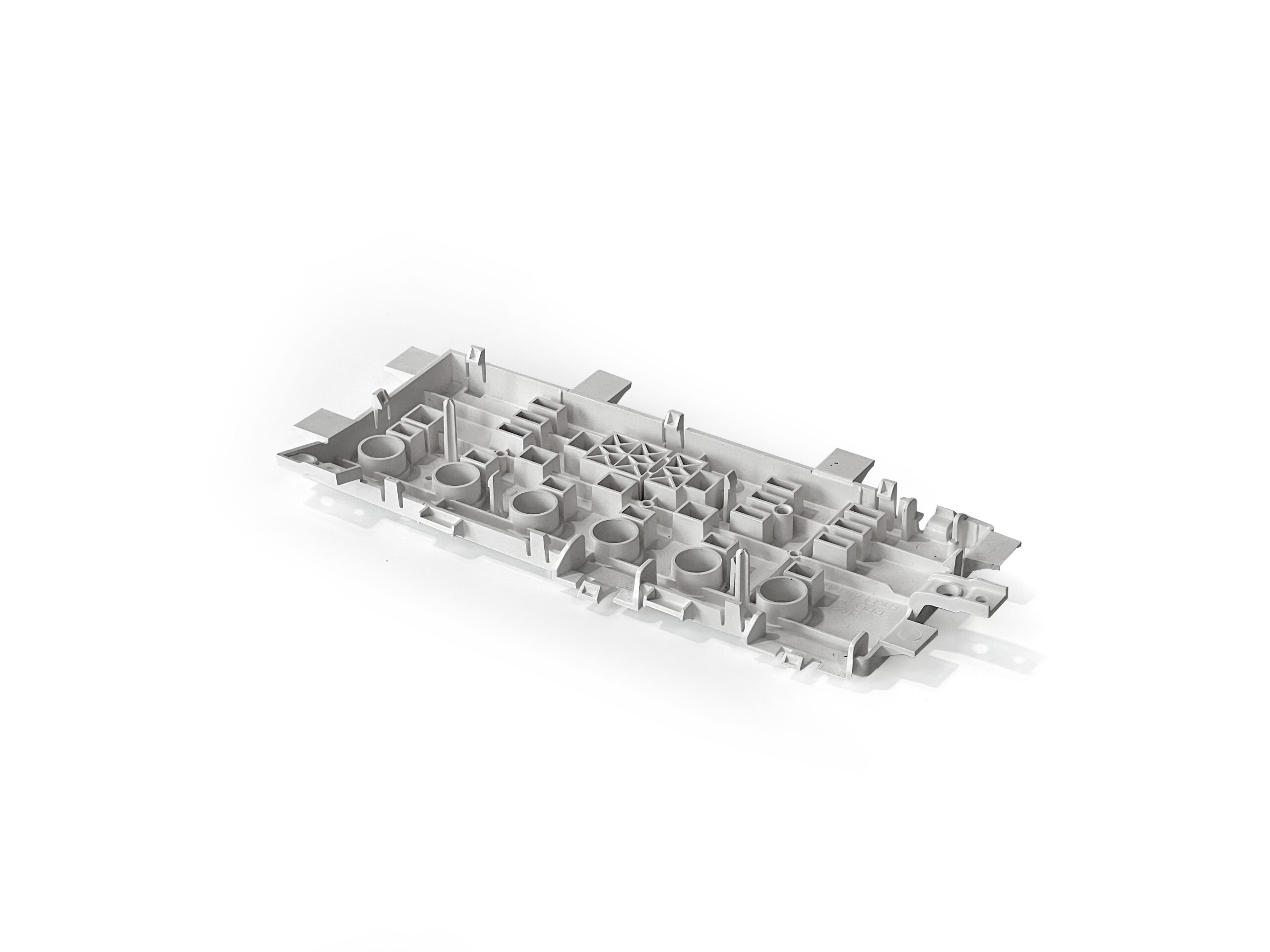
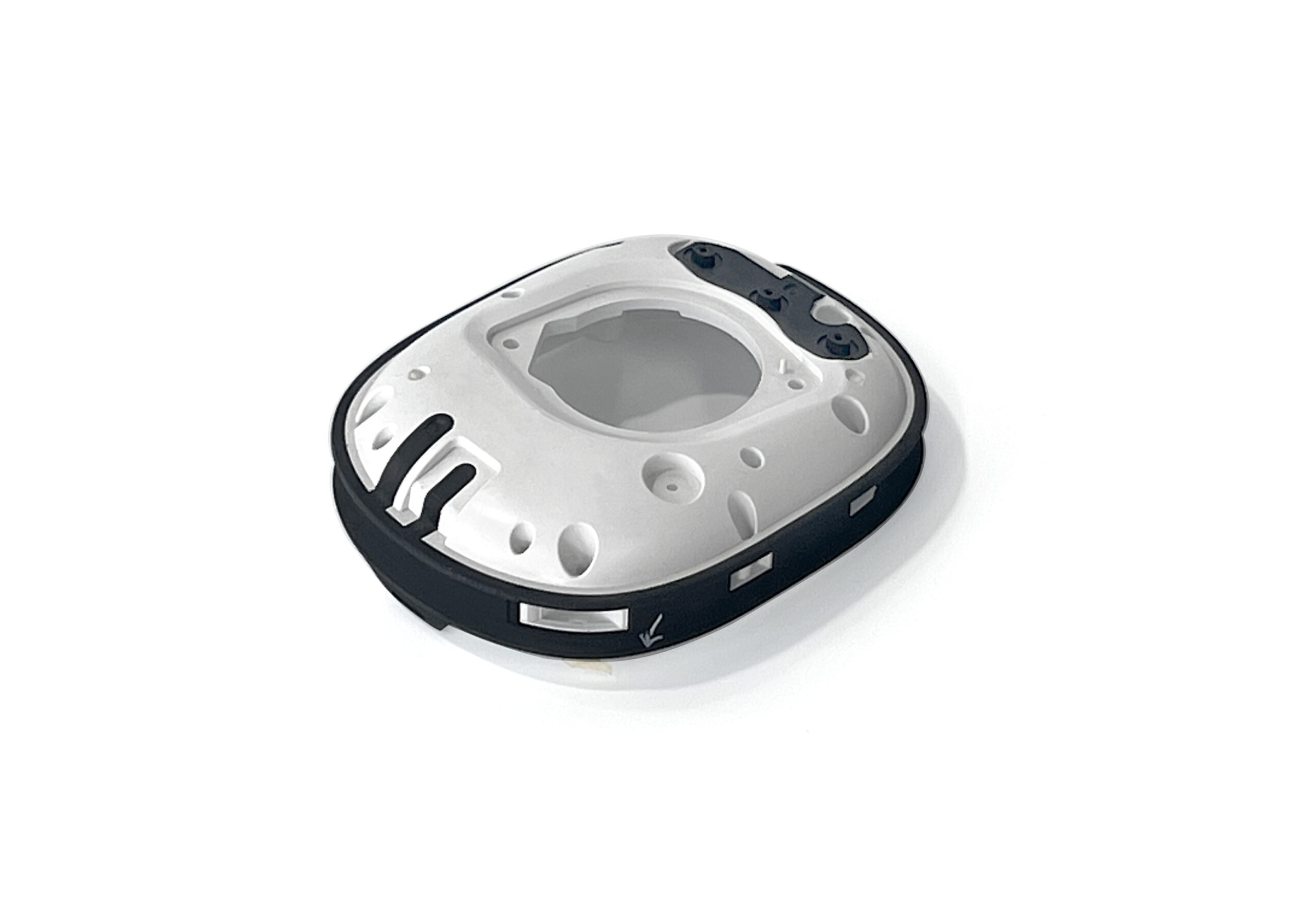
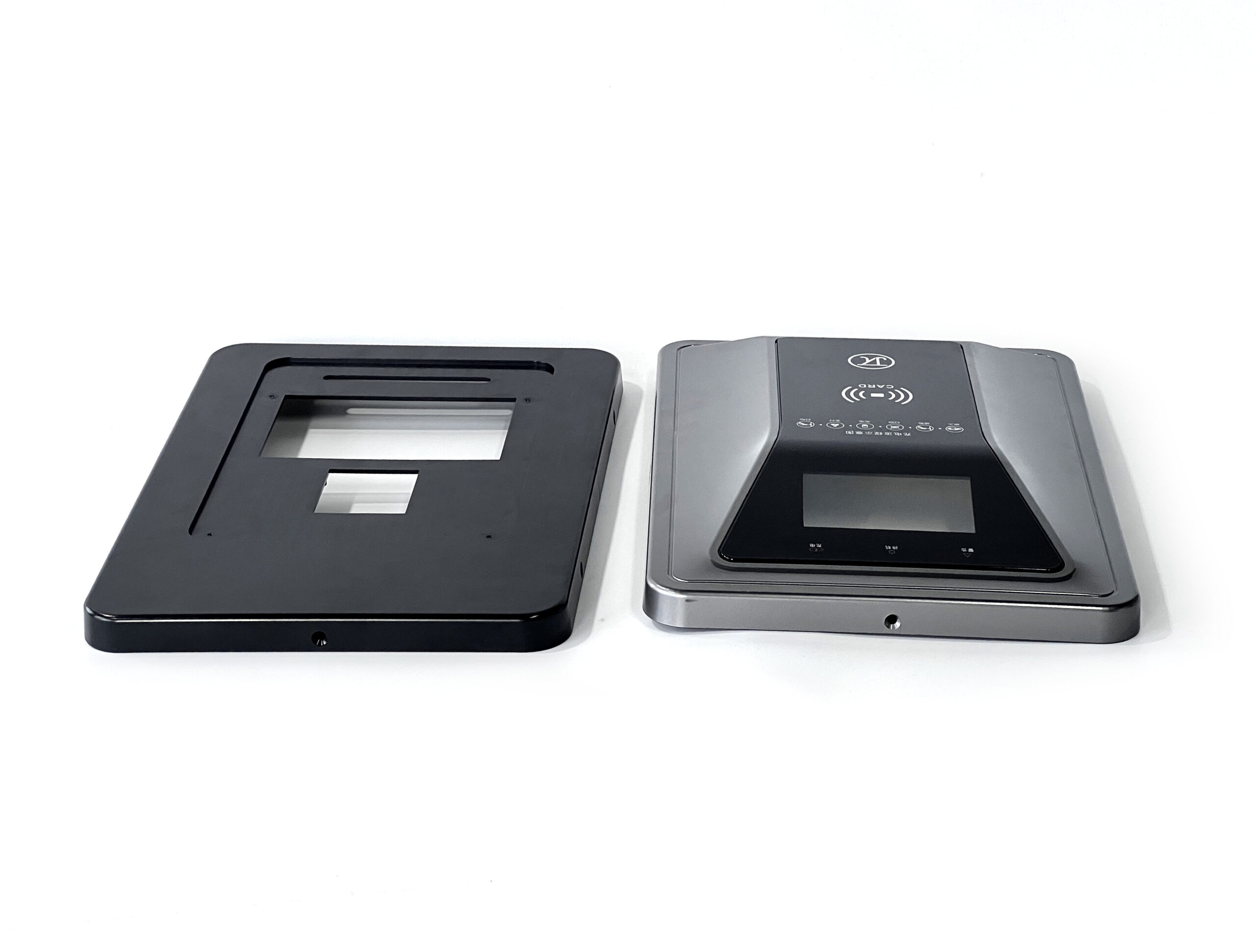
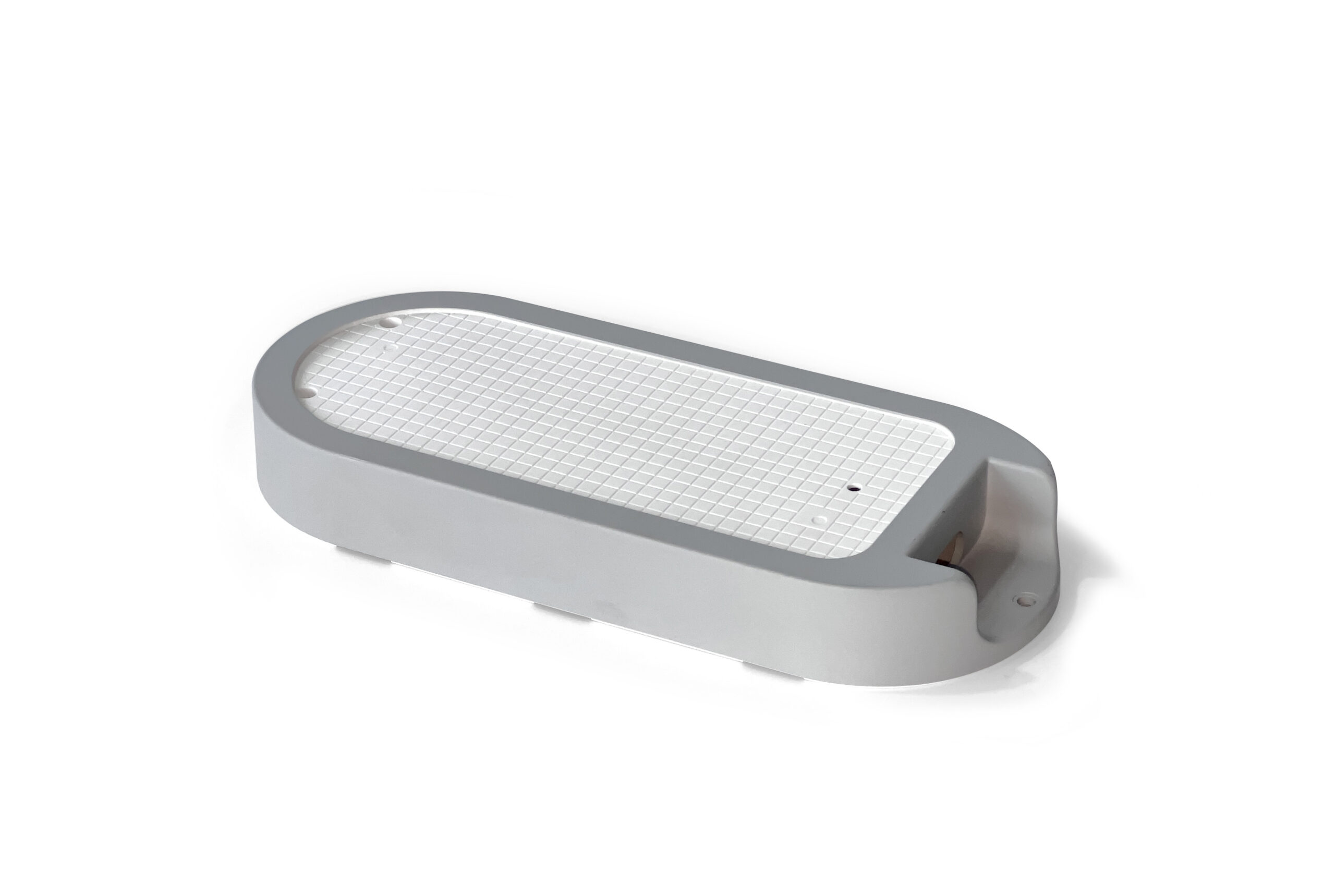
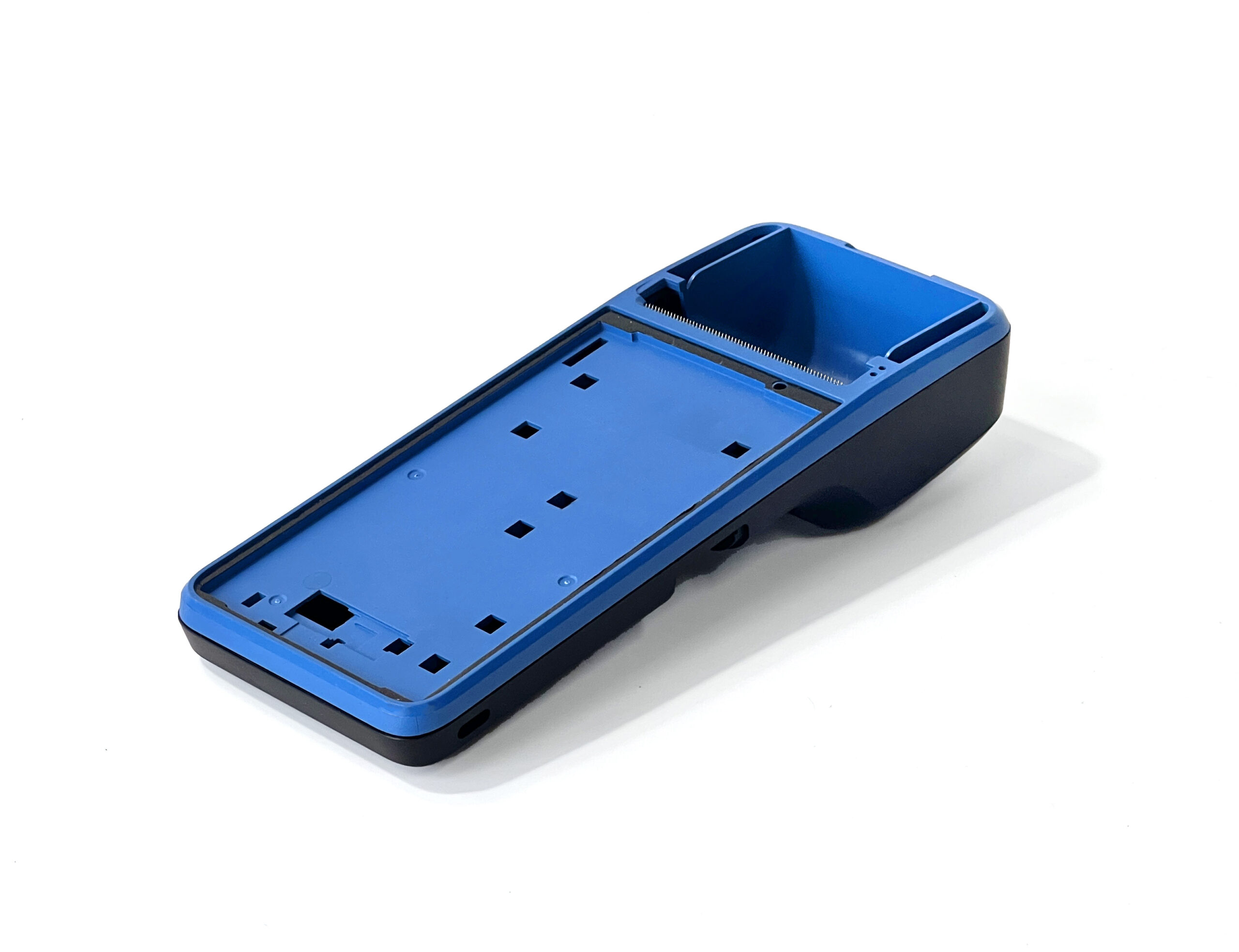
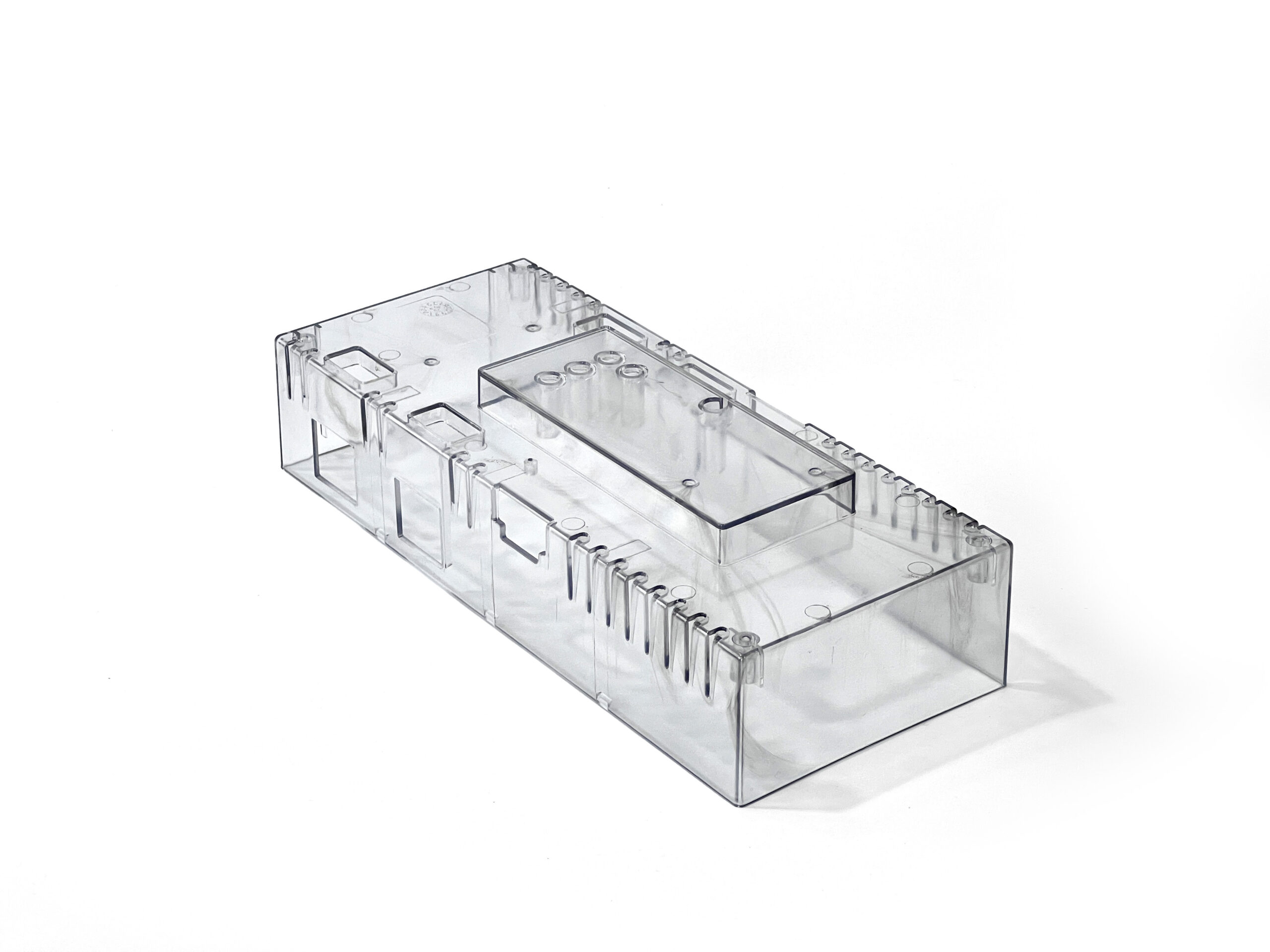
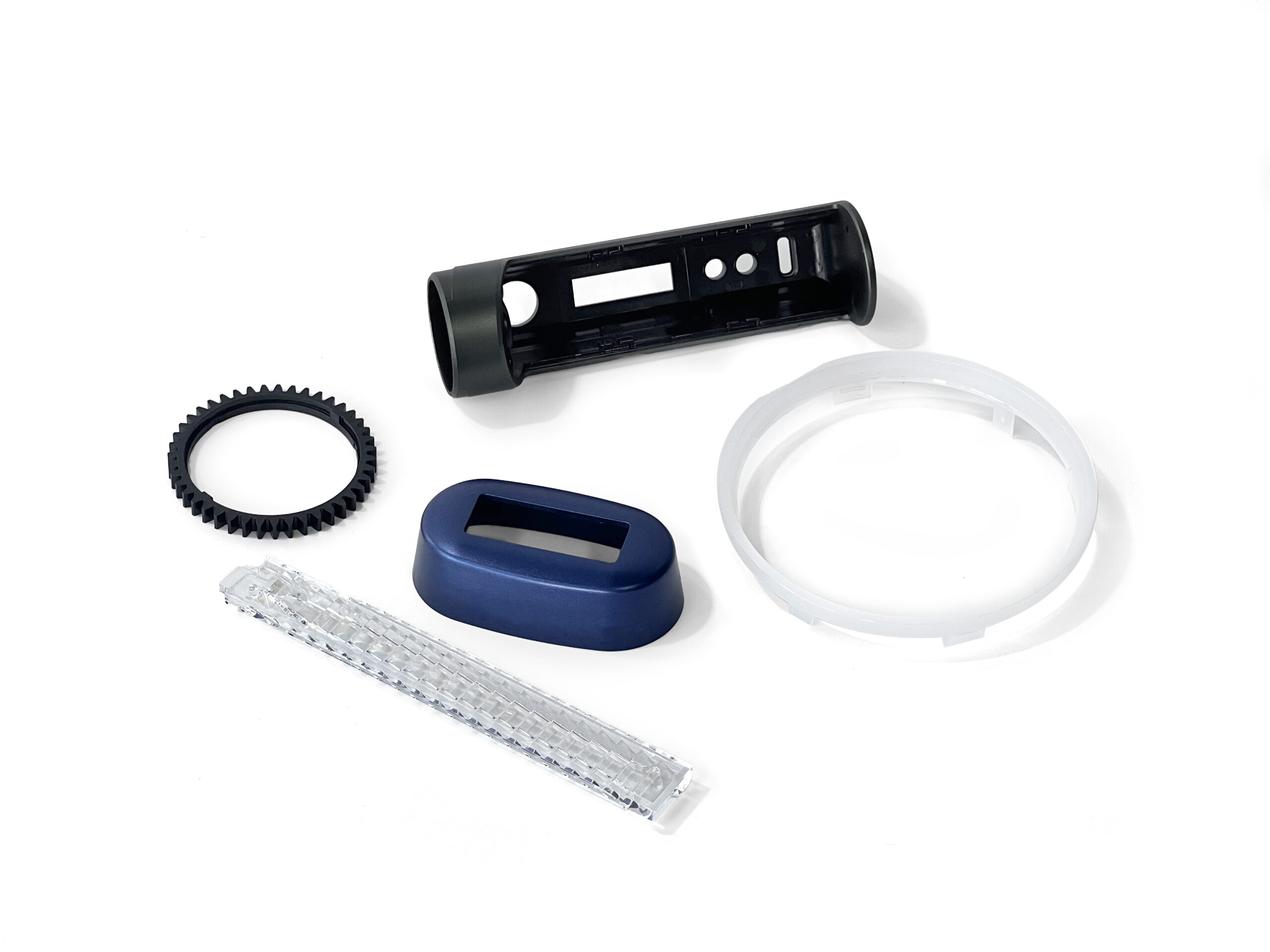
Plastic Injection Molding
CS Mold provides professional injection molding service, a highly efficient and cost-effective method for producing a wide range of plastic products. With over 10 years of experience, CS Mold is a experienced plastic injection molding manufacturer in China, catering to projects of any size or complexity. With our commitment to excellence and customer satisfaction, CS Mold is dedicated to delivering top-notch injection molding services that meet the highest industry standards.
Our state-of-the-art injection molding capabilities enable us to deliver high-quality parts with competitive pricing and quick lead times. Whether you need prototypes for testing or full-scale production, we have the expertise and capacity to meet your requirements. From chairs to toys, consumer electronics cases to disposable cutlery, and even car body panels, we have the versatility to manufacture various products using diverse materials and molding techniques.
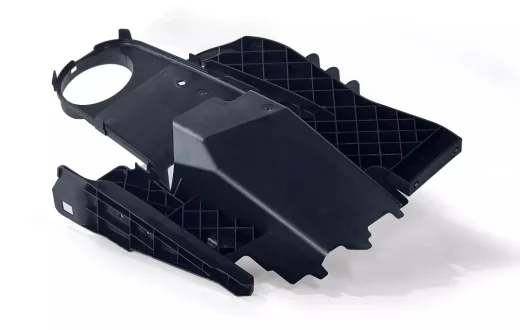
With our commitment to excellence and customer satisfaction, we are dedicated to delivering top-notch injection molding services that meet the highest industry standards
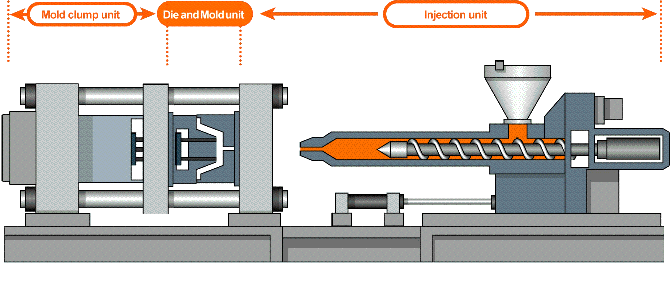
Plastic injection molding is the most commonly used method for mass manufacturing plastic products. Here is an overview of how the process works:
- Mold Setup: The mold is prepared and mounted onto the injection molding machine.
- Material Feeding and Melting: Thermoplastic material, in the form of pellets or granules, is fed into the machine’s hopper.
- Injection: The molten plastic is injected into the mold cavity under high pressure using a screw or plunger.
- Holding and Cooling: After the molten plastic is injected, it is held under pressure for a specific time to ensure complete filling and to allow for proper cooling and solidification. Cooling channels within the mold help expedite this process.
Ejecting and Finishing: Once the plastic has cooled and solidified, the mold is opened, and the finished part is ejected from the mold using ejector pins or a robotic system.
The injection molding process is highly efficient and capable of producing large quantities of parts quickly and consistently. By using molds with single or multiple cavities, manufacturers like CS Mold can produce a vast number of parts economically. The manufacturing cycle time varies depending on factors such as material, part size, and complexity.
We have a robust supply chain that ensures access to top-quality materials for your project. All our injection molding materials are sourced directly from manufacturers or authorized agents, guaranteeing their authenticity and reliability. We can provide the technical datasheet for each material, ensuring transparency and avoiding potential issues related to material quality.
In most cases, if there are no specific material requirements, we recommend using our recommended stock materials. These materials are readily available, enabling faster production and cost-effectiveness. However, if you have special material preferences or specific project requirements, we can accommodate those needs and utilize the appropriate materials for manufacturing.
The following materials are commonly used in plastic injection molding:
ABS
TPV
PCTG
PCTG
PSU
TPU
PC
PSU
POM
PP
PA66
HDPE
PBT
PPE
Nylon
PPA
This list represents our available injection molding materials. If your desired material is not listed, please consult with our project manager who can assist you in confirming its availability and suitability for your project.
Available Surface Finishes
- As Molded
- SPI Finishes
- Polishing
- Silk screening
- Pad printing
- Glossy
- Matte
- Painting
- Etching
- Laser Engraving
- CustomFinishing
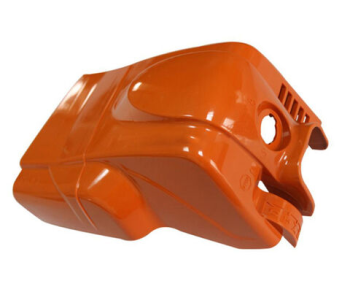
Advantage of Rapid Injection Molding:
Rapid injection molding provides a competitive advantage by enabling fast production, material versatility, scalability, repeatability, and cost-effectiveness. It is a popular and efficient method for manufacturing large quantities of finished plastic parts.

Fast Production and High Efficiency:
Rapid injection molding is known for its exceptional production speed and efficiency. The process can produce a significant number of parts per hour, allowing for quick turnaround times.

Wide Range of Available Materials:
Rapid injection molding offers a wide selection of materials to choose from. This includes the ability to use multiple plastic materials simultaneously. Commonly used materials include ABS, PE, PS, and PP.

Scalability and Repeatability
Plastic injection molding offers high repeatability, ensuring consistent and accurate reproduction of parts. Aluminum molds can last between 5,000 and 10,000 cycles, while full-scale steel production molds can last for over 100,000 cycles.

Cost-Effectiveness
Rapid injection molding proves to be cost-effective due to its ability to repeat the process hundreds or thousands of times rapidly. This allows for the amortization of tooling costs and reduces the cost per unit to a few dollars or less.
Applications
Plastic injection molding finds applications in diverse industries. Our team of experts specializes in delivering production solutions that expedite your product’s time to market.
In addition to our standard injection molding services, we offer specialized processes such as Over-molding and Insert Molding.
Over-molding, known as two-shot or 2k molding, is a unique custom plastic injection molding technique that allows multiple materials seamlessly combine into a single part or product. This process typically involves overlaying a rigid plastic-base component with a thin, pliable thermoplastic elastomer (TPE) exterior layer or other materials. It can be achieved through single-shot (insert molding) or two-shot (multiple-shot molding) techniques.
Partnering with us for your over-molding needs ensures access to our expertise, state-of-the-art equipment, and commitment to delivering high-quality, custom-molded products.
Insert Molding
Insert Molding also referred to as metal or plastic insert molding, is a widely adopted technique for incorporating metal components into injection molded parts during the molding process itself, instead of being added afterwards. This approach significantly reduces the need for subsequent manufacturing and assembly operations, streamlining the overall production process.
Insert Molding
OUR ADVANTAGE
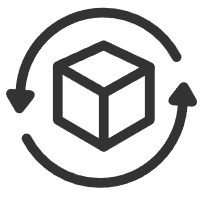
QUICK TUAROUND
Parts make in 5 days and delivery on time
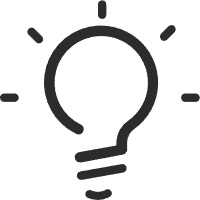
DFM ANALYSIS
Once receiving the inquiry, we will provide you with a preliminary DFM report
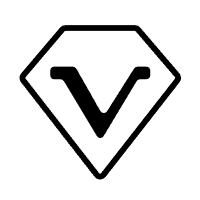
PROFESSIONAL SERVICES
More than 10 years of rapid tooling making
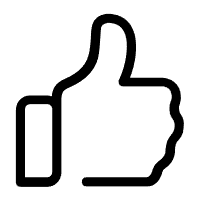
GOOD RAPUTATION FROM CUSTOMERS
Customers are satisfied with our services, products quality and delivery time.
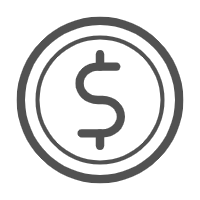
INSTANT QUOTING
Timely reply and provide the quote within 12 hours
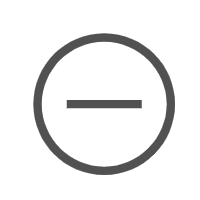
NO MOQ REQUIRED
CS Mold does not have minimum order quantity
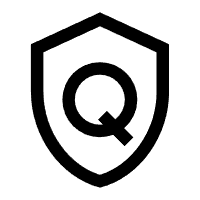
HIGH QUALITY
ISO 9001 & IATF 16949 certificated and inspect every step
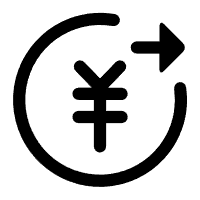
COST-EFFICIENT
+30% cost lower than western competitors
WHY CHOOSE US
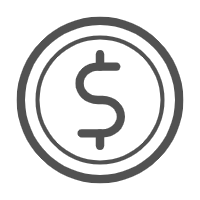
INSTANT QUOTING
Timely reply and provide the quote within 24 hours
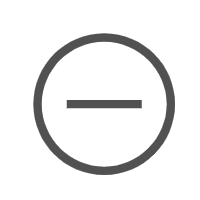
NO MOQ REQUIRED
Hord does not have minimum order quantity
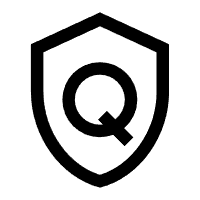
HIGH QUALITY
ISO 9001 & IATF 16949 certificated and inspect every step
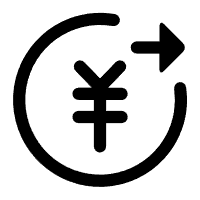
COST-EFFICIENT
+30% cost lower than western competitors
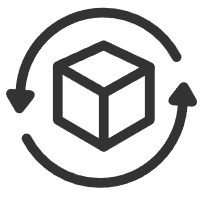
QUICK TUAROUND
Parts make in 7 days and delivery on time
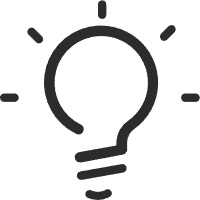
DFM ANALYSIS
Once receiving the inquiry, we will provide you with a preliminary DFM report
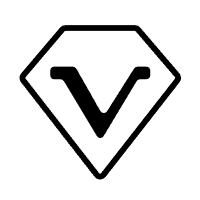
PROFESSIONAL SERVICES
More than 20 years of rapid tooling making
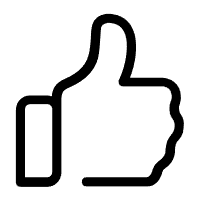
GOOD RAPUTATION FROM CUSTOMERS
Customers are satisfied with our services, products quality and delivery time.
WORK WITH US
Step 1
Share the 2D/3D files and project specifications with us for a precise quotation
Step 2
Once the order is confirmed, we will provide a detailed design and manufacturing analysis report. Our engineers will review all tolerances and appearance specifications, identifying any issues that may affect the quality of the parts.
Step 3
Upon DFM approval, we will initiate production. Our project engineers will conduct thorough inspections of the parts’ dimensions, tolerances, and appearance during manufacturing, ensuring they meet your expectations.
Step 4
After the quality inspection, the parts will be shipped to your location.
The geometry of the part, the amount of parts needed, your tooling budget and the application the part is being used for will all influence your decision to injection mold the part.
Most material is application specific. If you don’t have a material selected for your application, we can help and offer some guidance. Often several resins can be sampled but the customer has final approval before proceeding.
We will evaluate your part design and modify it to be efficiently injection molded. Then, we will build the mold for the part. Next, your mold will be put into an injection molding press to make production parts. On average the entire process takes 8-10 weeks.
We offer some packaging at the press, but do not offer custom packaging, decorating or assembly at the press. Additional secondary operations can be performed by approved 3rd party vendors with whom we work.
8-10 weeks on average, depending on the complexity and cavitations of the mold.
