Insert Molding Service
Insert molding is a type of injection molding process where inserts, usually made of metal, are added to an injection-molded part. The inserts are placed inside the mold cavity before injecting molten plastic. As the plastic cools and solidifies, the inserts become an integral part of the plastic component.
Insert molding enables the production of robust, long-lasting, and lightweight parts, which is why many industries have embraced this technique. Additionally, the metal inserts enhance the mechanical properties of the plastics or thermoplastics used in the insert molding process.
The Advantages of Insert Molding
Insert molding allows for complex and integrated designs that would be difficult or impossible to achieve with traditional assembly methods. It enables the precise placement of inserts, accommodating unique shapes, and optimizing product functionality.
With insert molding, the production process is streamlined, reducing handling and assembly steps. This results in improved production efficiency and faster turnaround times.
By integrating multiple components into a single molding process, insert molding eliminates the need for separate assembly steps, reducing labor costs and assembly time. It also minimizes the risk of errors and ensures consistent quality.
Inserts can provide additional functionalities or properties to the molded part, such as electrical conductivity, thermal insulation, or vibration dampening. This enhances the overall performance and versatility of the product.
Insert molding creates a strong bond between the insert material (typically metal) and the molded plastic, resulting in improved structural integrity and durability of the final product.
Insert molding ensures a secure and reliable bond between the insert and the plastic, reducing the risk of component loosening or detachment during product use. This leads to consistent quality and reliability of the final product.
Insert molding can be applied in a wide range of industries and products where the integration of multiple components is required for improved performance, strength, and efficiency.
Insert molding is used in automotive applications for producing components such as electrical connectors, sensor housings, dashboard panels, and interior trim pieces.
It is employed in the electronics industry for manufacturing items like circuit boards, connectors, switches, and sensor enclosures, providing enhanced functionality and durability.
Many consumer goods incorporate insert molding, including household appliances, electrical connectors, power tool components, knobs, handles, and electronic enclosures.
The deferrence beweent Over-molding & Insert Molding
Overmolding and insert molding are two common techniques used in the manufacturing of plastic parts. While they are similar in that they both involve combining multiple materials into a single finished product, there are some key differences between them.
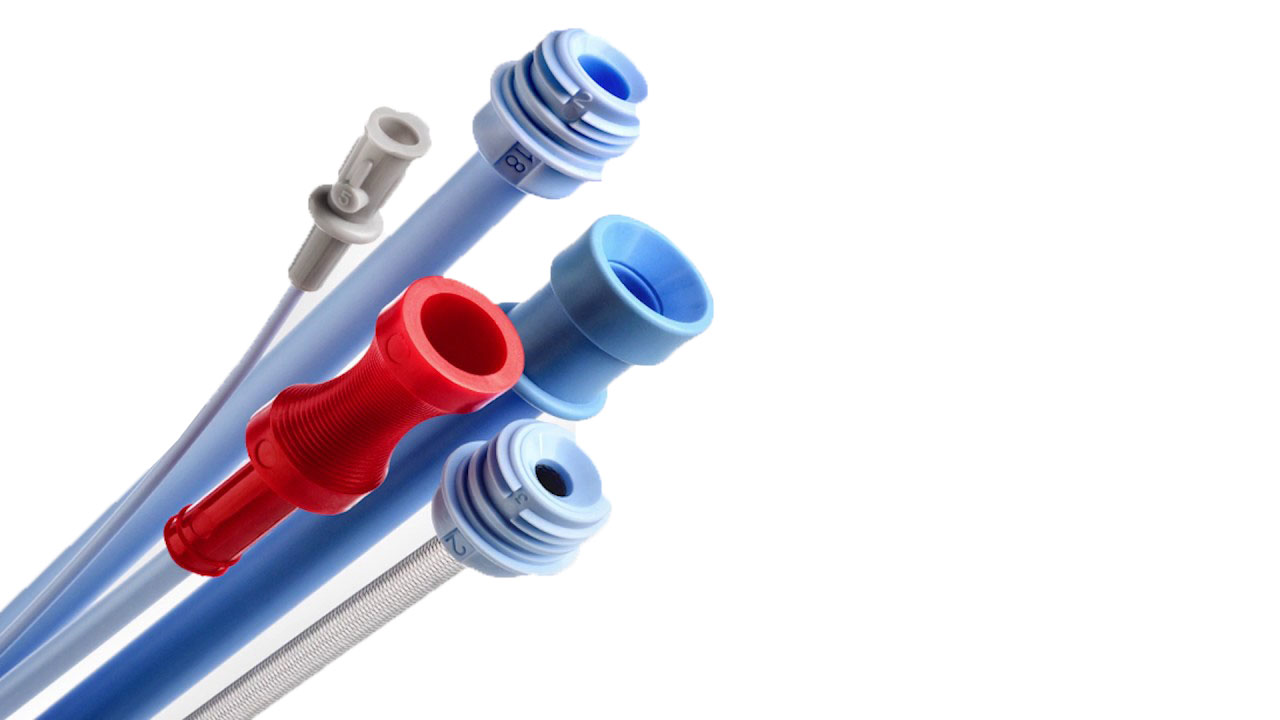
Over-molding
Overmolding is a type of custom plastic injection molding where a part is created using multiple materials. This process involves applying an injection molded layer of material onto an existing injection molded workpiece, resulting in chemically bonded parts made from different materials. It can be used to manufacture layered parts from the ground up or to add a durable outer layer to existing plastic components and tools, enhancing their ruggedness. A typical example of an over-molded product is a toothbrush, which combines a solid plastic body with a rubberized grip for improved handling and comfort.
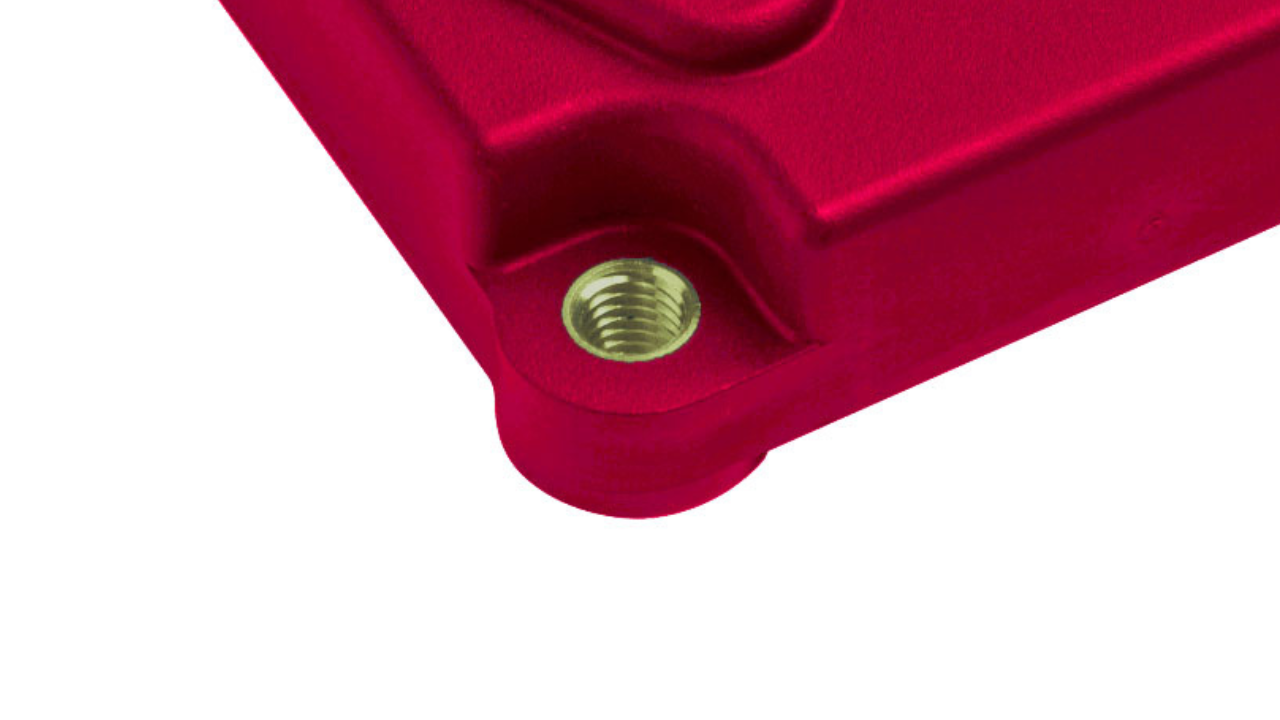
Insert Molding
Insert molding, also referred to as metal insert molding or plastic insert molding, is a widely adopted technique for incorporating metal components into injection molded parts during the molding process, eliminating the need for additional manufacturing or assembly steps after curing. The inserts, which can be inserted manually or automatically, are positioned onto mold cores integrated within the molds. Subsequently, when the mold halves are sealed, plastic pellets are melted in the injector barrel and injected into the mold, causing the molten plastic material to envelop the inserted components.
Insert Molding FAQs
Inserts can be made of various materials, such as metal, plastic, ceramics, or even electronic components. The choice of material depends on the specific requirements of the application.
By integrating metal or specialized inserts into plastic parts, insert molding can enhance product performance in various ways. It can provide electrical conductivity, thermal management, reinforcement, or vibration dampening, depending on the specific needs of the application.
Design considerations for insert molding include proper draft angles for easy part ejection, insert compatibility with the chosen plastic material, appropriate material selection for both the insert and plastic, and opportunities for part consolidation.
While insert molding offers numerous advantages, it does have some limitations. Design complexity, the availability of suitable inserts, and the cost of tooling can impact the feasibility and cost-effectiveness of the process.
Quality control measures during insert molding include stringent material testing, dimensional and functional checks during production, and adherence to industry standards and certifications to ensure consistent and high-quality results.
Other Articles You Might Enjoy
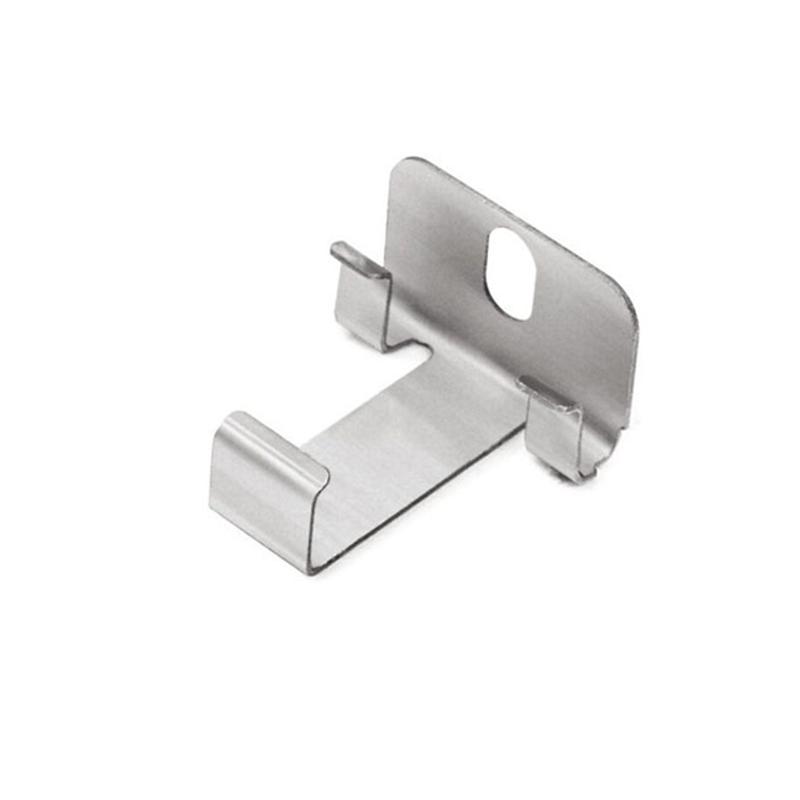
Elevate Your Projects with CS Mold’s Custom Sheet Metal Fabrication
At CS Mold, we take pride in our expertise in custom sheet metal fabrication, offering tailored solutions to meet your unique project requirements. With a
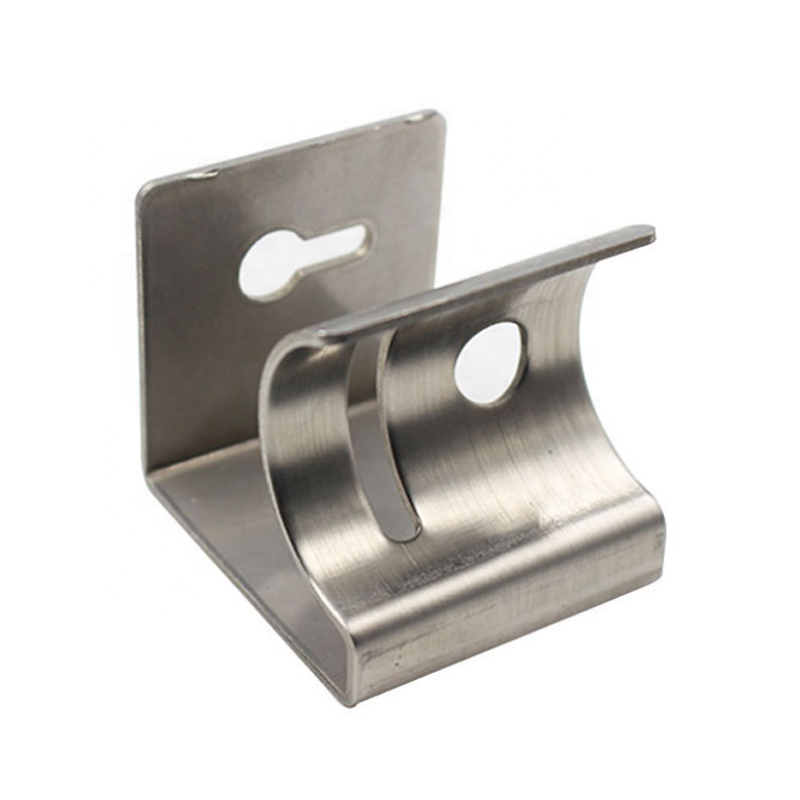
Unveiling What Sheet Metal Is Made Of with CS Mold
At CS Mold, we specialize in precision sheet metal fabrication services that cater to a multitude of industries. With our expertise and commitment to excellence,
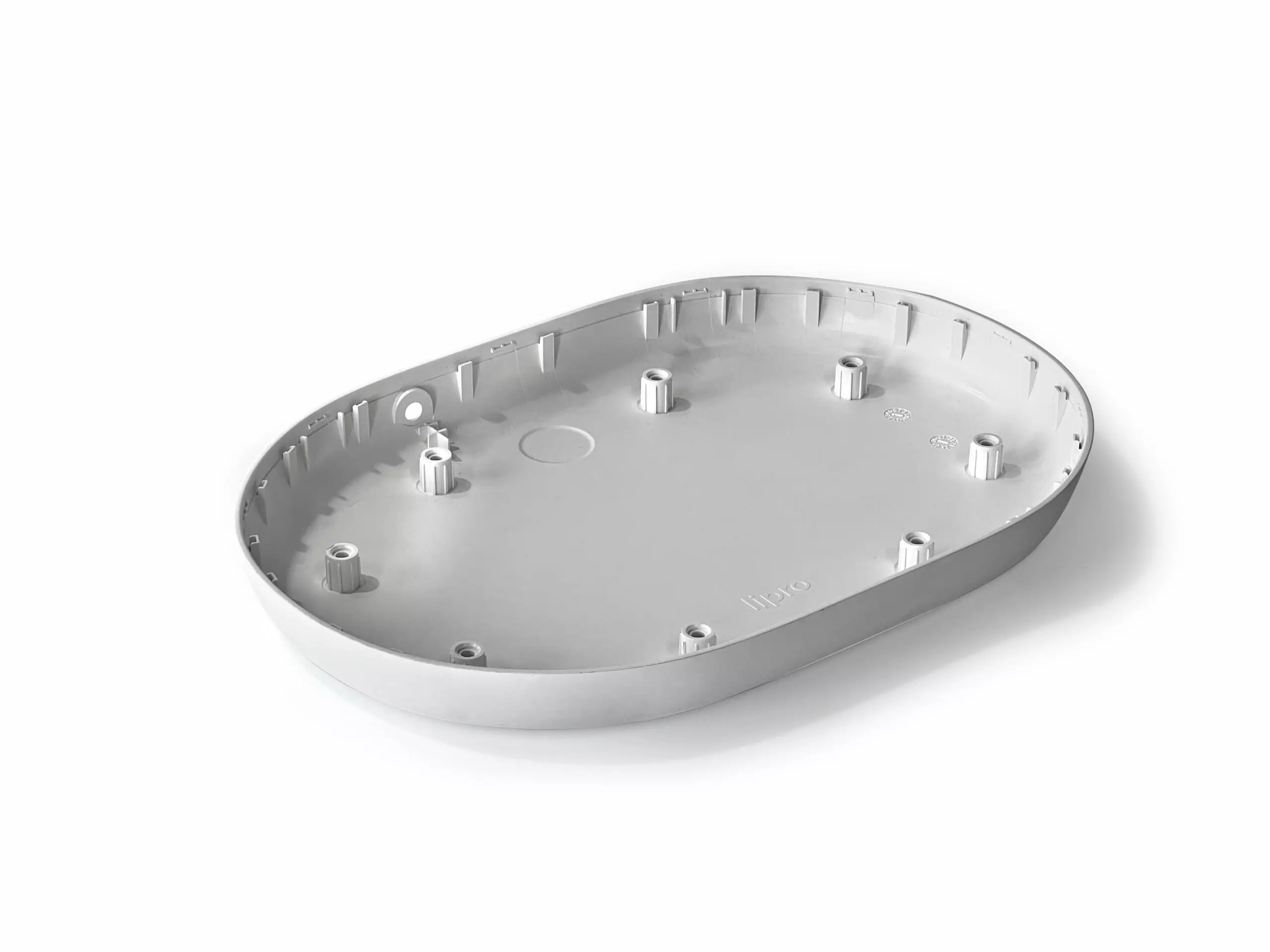
CS Mold – Unveiling the Battle: 3D Print vs Injection Molding
At CS Mold, we delve into the realm of manufacturing methods to compare two stalwarts: 3D printing and injection molding. With a focus on efficiency,