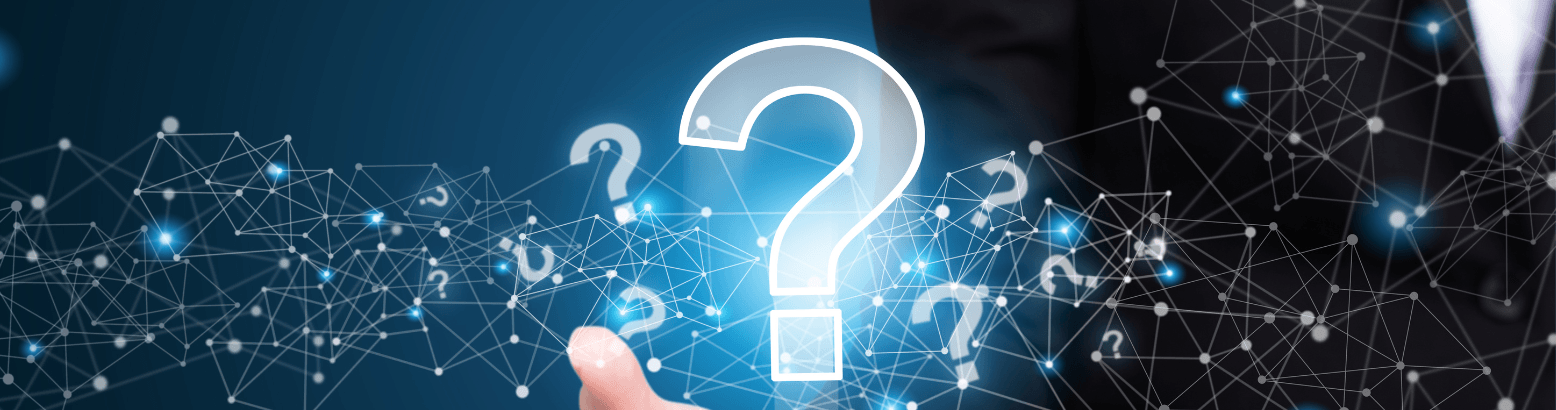
FREQUENTY ASKED QUESTIONS
Here are the answers to the frequently asked questions.Any further questions, please feel free to contact us.522621031@qqcom
Traditional machining is typically manual and requires human operators to control the machining tools. In contrast, CNC machining is automated, with computer programs controlling the machine’s movements. CNC machining offers higher precision, faster production times, and greater design flexibility compared to traditional methods.
Commonly used file formats for CNC machining include STEP, IGES, DXF, and STL. These formats contain the 3D CAD model or 2D vector data that guides the CNC machine in producing the desired part.
Tolerances refer to the allowable deviation from the desired dimensions of a part. The achievable tolerances in CNC machining depend on various factors, including the material, geometry, and machine capabilities. Generally, tolerances ranging from +/- 0.001″ to 0.005″ (or +/- 0.025mm to 0.127mm) are achievable with CNC machining.
CNC machining is versatile and can be used for both prototyping and production. It is particularly useful for prototyping due to its ability to produce high-quality parts quickly. For production runs, CNC machining offers cost-effective and efficient manufacturing processes, especially for small to medium batch sizes.
The time required for CNC machining depends on factors such as part complexity, material, quantity, and machine availability. Simple parts may be completed in hours, while more complex or larger production runs may take several days or weeks. Rapid prototyping services can often deliver parts within 1-5 days.
Compression molding finds applications in various industries, including automotive, aerospace, electrical insulation, consumer goods, and appliance manufacturing. It is particularly suitable for products that require high strength, resistance to heat and chemicals, and dimensional stability.
Compression molding differs from other molding processes, such as injection molding or blow molding, in terms of the material pre-form and the application of heat and pressure. In compression molding, the material is pre-formed and placed directly in the mold cavity, whereas in injection molding, molten material is injected into a mold cavity. Additionally, compression molding typically uses solid or pre-cut material, whereas other processes may use pellets or liquid resin.
Yes, compression molding is capable of producing complex parts, including parts with intricate shapes, undercuts, or varying wall thicknesses. The mold design and the use of auxiliary tools, such as inserts or ejector pins, can help achieve the desired complexity.
The geometry of the part, the amount of parts needed, your tooling budget and the application the part is being used for will all influence your decision to injection mold the part.
Most material is application specific. If you don’t have a material selected for your application, we can help and offer some guidance. Often several resins can be sampled but the customer has final approval before proceeding.
We will evaluate your part design and modify it to be efficiently injection molded. Then, we will build the mold for the part. Next, your mold will be put into an injection molding press to make production parts. On average the entire process takes 8-10 weeks.
8-10 weeks on average, depending on the complexity and cavitations of the mold.