What is Overmolding?
Overmolding is a manufacturing process in which a substrate or base component is covered or encapsulated with a second material, usually a thermoplastic elastomer (TPE), to create a composite product. It involves injecting the second material onto or around the first component, bonding them together to form a single integrated part. Skilled professionals like those at CS Mold offer swift and precise over-molding services to assist you in designing your project
The Over-molding Process
- First, the substrate material is prepared and placed into a mold.
- Then, the overmolding material is injected or molded over the substrate material.
- The two materials are bonded during the molding process, creating a strong and durable bond between them.
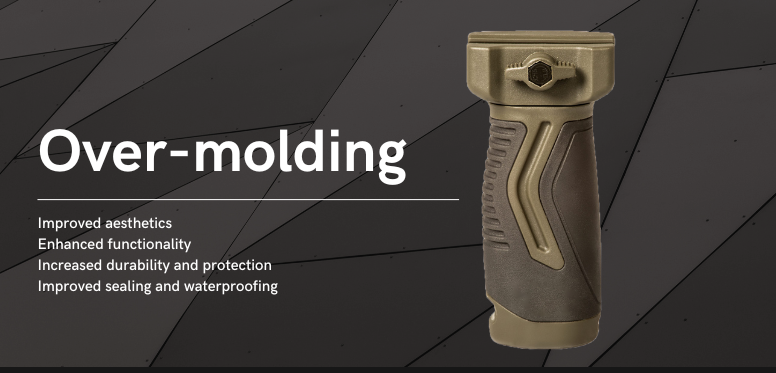
Rules of Overmolding Design and Production
Rules of Overmolding Design and Production

- The best bonding is generally achieved when wall thicknesses are within the range of 0.060″ to 0.120″ (1.5 mm-3 mm).
- To minimize localized stresses, it is recommended to maintain radii of at least 0.020″ or 0.5mm in corners.

- If thick thermoplastic elastomer sections are necessary for the part, it is advisable to core them out to minimize shrinkage problems, reduce part weight, and lower cycle time.
- It is recommended to avoid deep and blind pockets or ribs in your design.
- To prevent flow issues such as backfills and gas traps, gradual transitions between wall thickness should be used.

- To avoid warpage, especially for flat or long parts, the thermoplastic elastomer/thermoplastics vulcanizates should be less thick than the substrate.
- Overmolding requires mechanical or chemical bonding to the substrate. Therefore, the choice of overmolding materials should allow for this.
Applications of Overmolding
Applications of Overmolding
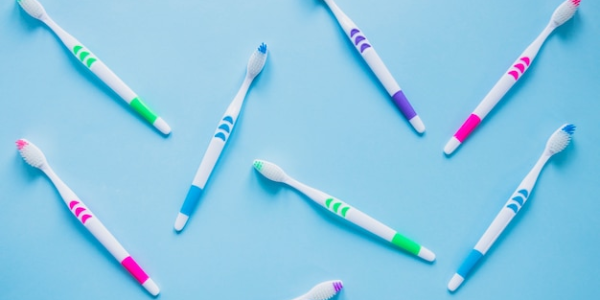
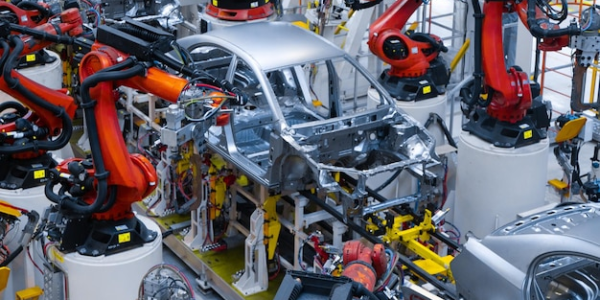
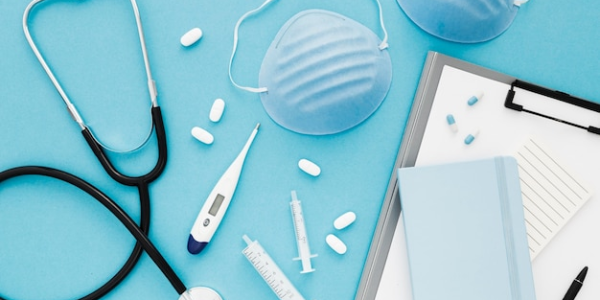
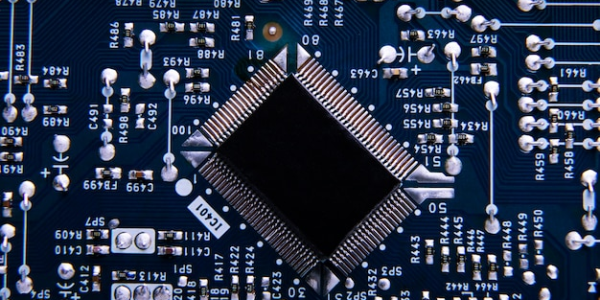
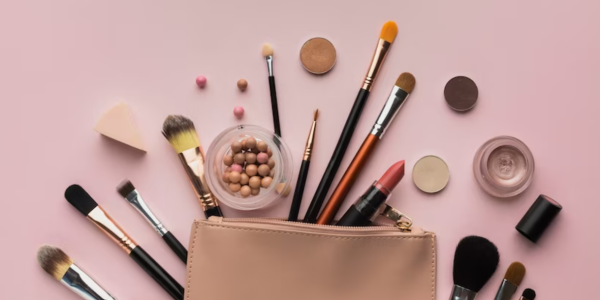
Get the Perfect Parts with CS Mold Overmolding Services
Work with a professional overmolding manufacturer like CS Mold.
Get the Perfect Parts with CS Mold Overmolding Services
Work with a professional overmolding manufacturer like CS Mold .
- 20+ years of experience
- 24 hours Instant Quoting
- NO MOQ required
- ISO9001 & IATF 16949 certificated quality
- Quick turnaround
- DFM analysis
Over-molding FAQs
The benefits of overmolding include enhanced functionality, improved aesthetics, increased durability, improved ergonomics, better sealing and waterproofing, simplified assembly, and customization opportunities.
Common materials used in overmolding include rigid plastics (such as ABS or polycarbonate) as the base material and flexible or elastomeric materials (such as TPE or silicone) as the overmolded material.
Design considerations for overmolding include material compatibility, part geometry, bonding between materials, proper gating and venting, and the specific requirements of the end-use application.
The cost implications of overmolding can vary depending on factors such as material selection, part complexity, tooling requirements, and production volume. Generally, overmolding can add complexity and cost to the manufacturing process compared to traditional molding techniques.