Cases of Compression Molding
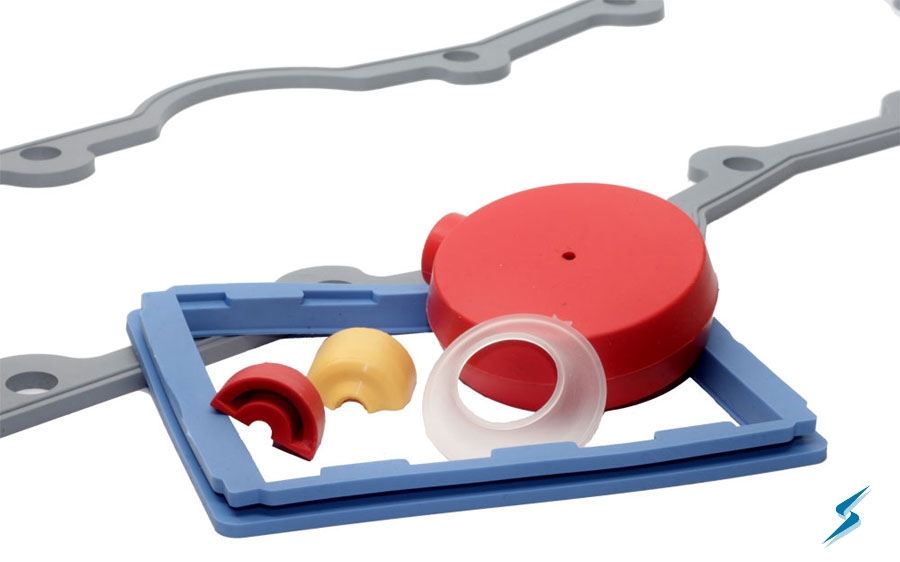
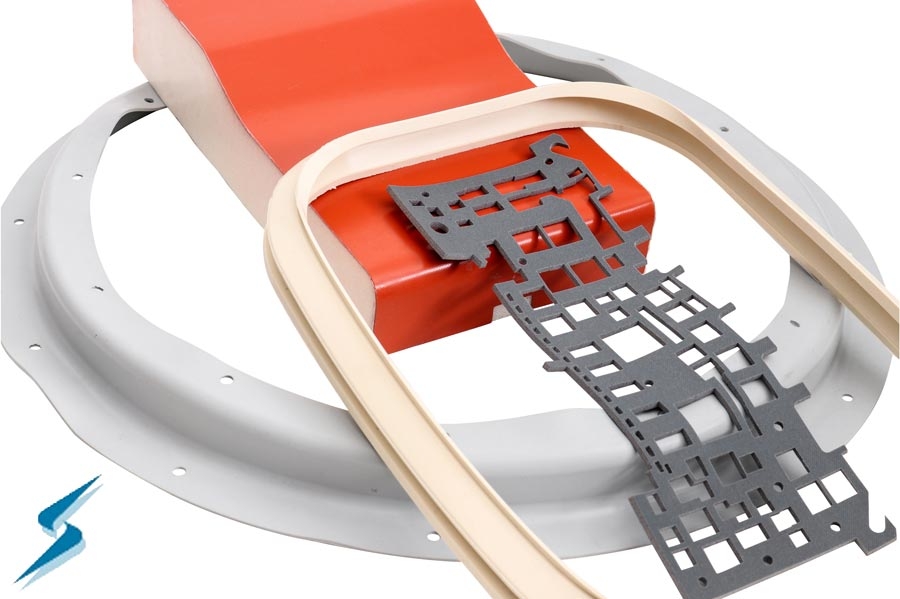
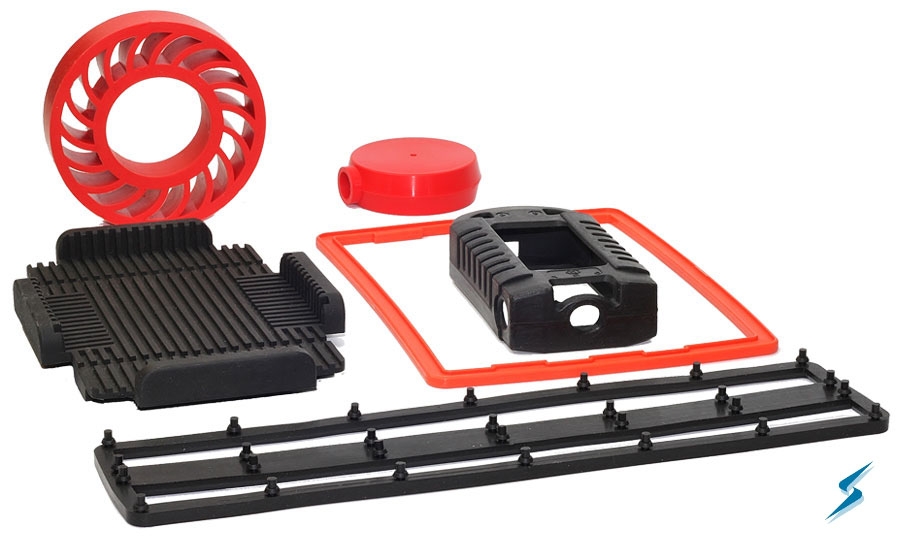
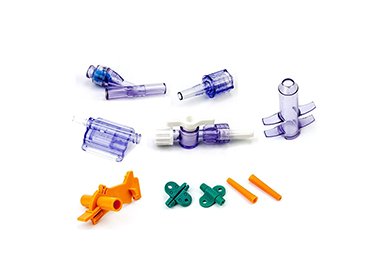
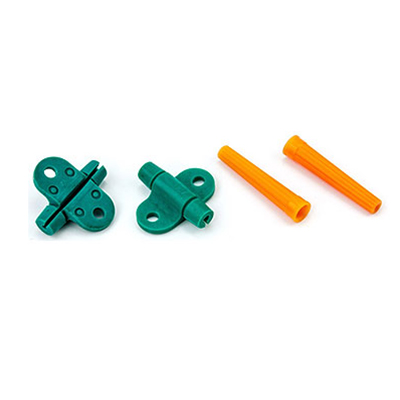
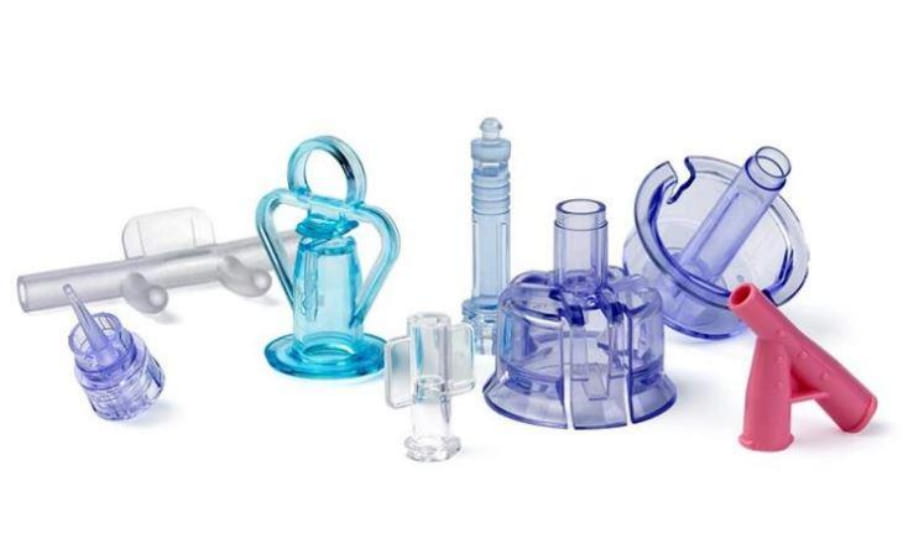
Silicone compression molding, known as Rubber Compression Molding, is widely used to produce different shapes of elastomer silicon rubber molded parts & products. It can produce simple design & structure seals, precision compression molded products, mainly depending on mold plate process controls, etc. This is one of the most cost-effective tools to make rubber seals or silicone rubber parts.
As a compression mold manufacturer & company, CS Mold provides professional compression molding services. we can run low volume production for customer with rapid tooling, the lead time is about 2-3 weeks.
The Process of Silicone Compression Molding
Compared to LSR injection molding, silicone transfer molding, or extrusion molding, the silicone compression molding process is simpler.
1. Compression molds are manufactured through CNC machining and polishing. For a simple silicone part design, a two plate mold is used, comprising the cavity side and core side. The template is then assembled and inserted into the compression molding machine.
2. Silicone materials like HCR (high consistency rubber) or LSR (liquid silicone rubber) are loaded into the template. The compressor sets the heat and pressure according to time, allowing the silicone material to spread throughout the entire mold cavity and cure.
3. The pressure is released from the press, the template is separated, and the silicone component is removed. This completes the normal compression molding cycle for simple silicone parts.
CS molds have different sizes of compression molding machines. This ensures our capabilities from small to large rubber parts, single cavity molds to multi cavity molds. We can configure our molding equipment to meet different production needs.
Advantages of compression molding
The following are many advantages of silicone compression molding :
- It is a simpler process.
- The loss of raw materials is minimal and will not cause significant losses.
- The mold cavity has a short lifespan and low maintenance costs.
- It is great for producing large items and thicker parts.
- It can be a good choice for insert molding and multi color molding.
- It is cost-effective for short production runs.
Applications
Silicone rubber is a key sealing material in various industries. Due to its many unique and optimal qualities, silicone rubber is often sought after in various applications.
WHY CHOOSE US
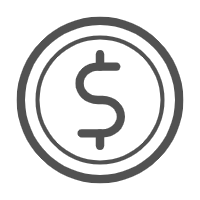
INSTANT QUOTING
Timely reply and provide the quote within 24 hours
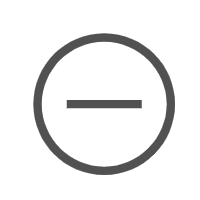
NO MOQ REQUIRED
Hord does not have minimum order quantity
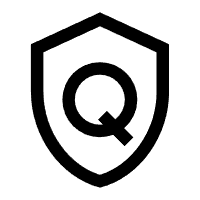
HIGH QUALITY
ISO 9001 & IATF 16949 certificated and inspect every step
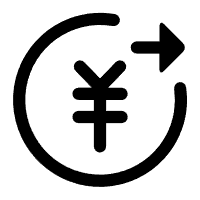
COST-EFFICIENT
+30% cost lower than western competitors
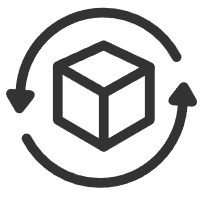
QUICK TUAROUND
Parts make in 7 days and delivery on time
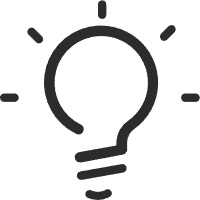
DFM ANALYSIS
Once receiving the inquiry, we will provide you with a preliminary DFM report
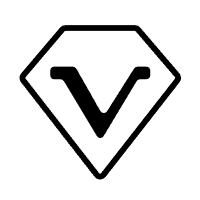
PROFESSIONAL SERVICES
More than 20 years of rapid tooling making
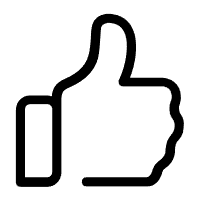
GOOD RAPUTATION FROM CUSTOMERS
Customers are satisfied with our services, products quality and delivery time.
OUR ADVANTAGE
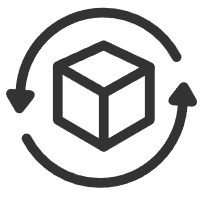
QUICK TUAROUND
Parts make in 5 days and delivery on time
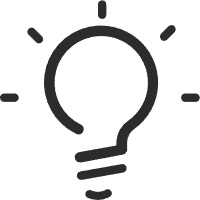
DFM ANALYSIS
Once receiving the inquiry, we will provide you with a preliminary DFM report
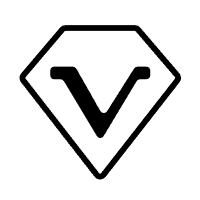
PROFESSIONAL SERVICES
More than 10 years of rapid tooling making
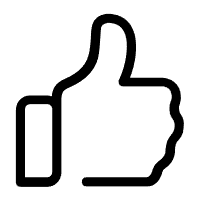
GOOD RAPUTATION FROM CUSTOMERS
Customers are satisfied with our services, products quality and delivery time.
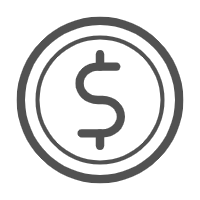
INSTANT QUOTING
Timely reply and provide the quote within 12 hours
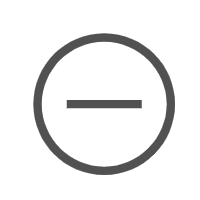
NO MOQ REQUIRED
CS Mold does not have minimum order quantity
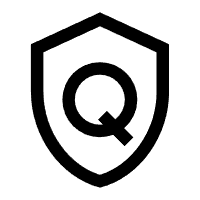
HIGH QUALITY
ISO 9001 & IATF 16949 certificated and inspect every step
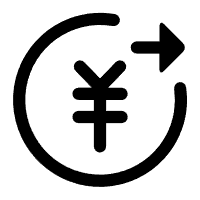
COST-EFFICIENT
+30% cost lower than western competitors
Compression molding finds applications in various industries, including automotive, aerospace, electrical insulation, consumer goods, and appliance manufacturing. It is particularly suitable for products that require high strength, resistance to heat and chemicals, and dimensional stability.
Compression molding differs from other molding processes, such as injection molding or blow molding, in terms of the material pre-form and the application of heat and pressure. In compression molding, the material is pre-formed and placed directly in the mold cavity, whereas in injection molding, molten material is injected into a mold cavity. Additionally, compression molding typically uses solid or pre-cut material, whereas other processes may use pellets or liquid resin.
Yes, compression molding is capable of producing complex parts, including parts with intricate shapes, undercuts, or varying wall thicknesses. The mold design and the use of auxiliary tools, such as inserts or ejector pins, can help achieve the desired complexity.
