At CS Mold, we specialize in providing professional compression molding services, offering a cost-effective solution for producing elastomer silicone rubber molded parts and products. Our expertise lies in manufacturing precision compression molded products, catering to a wide range of industrial needs with rapid tooling capabilities that ensure efficient low-volume production within a short lead time. In this article, we will delve into what is the difference between injection molding and compression molding.
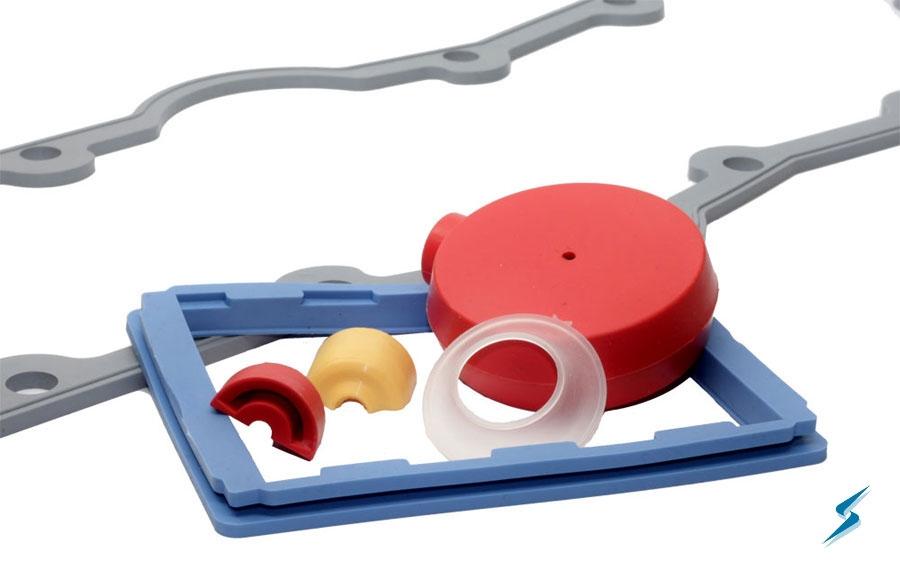
Understanding Injection Molding and Compression Molding
When it comes to manufacturing silicone rubber parts, two prominent techniques stand out-injection molding and compression molding. While injection molding involves injecting molten material into a mold cavity under high pressure, compression molding relies on loading solid material into a mold and applying heat and pressure to shape the final product. Understanding the differences between these processes is crucial for determining the most suitable method for your specific project requirements.
The Process Variations Between Injection Molding and Compression Molding
In injection molding, the material is forced into the mold through a nozzle and runner system, ensuring consistent filling and precise control over part dimensions. On the other hand, compression molding utilizes the application of pressure to distribute the material evenly within the mold cavity without the need for complex channels or runners. This difference in material distribution and pressure application impacts the structural integrity and surface finish of the final product.
In the intricate process of injection molding, the material is propelled into the mold under pressure through a meticulously designed nozzle and runner system, enabling a uniform filling process and meticulous control over the dimensions of each part produced. Conversely, compression molding intricately applies pressure to evenly distribute the material within the mold cavity, eliminating the necessity for intricate channels or runners.
Advantages and Applications of Injection Molding Versus Compression Molding
Injection molding is favored for its high production efficiency, intricate part design capabilities, and tight tolerances, making it ideal for mass production of complex geometries. In contrast, compression molding offers greater flexibility in material selection, lower tooling costs, and better control over material waste, making it a preferred choice for small to medium production runs where customization and material properties are paramount.
Conclusion
Understanding the key distinctions between injection molding and compression molding is essential for selecting the most appropriate manufacturing process for your silicone rubber parts. While injection molding excels in high-volume production and intricate designs, compression molding offers versatility, cost-effectiveness, and control over material properties. At CS Mold, we leverage our expertise in compression molding to deliver customized solutions that meet your specific requirements efficiently and affordably, ensuring optimal quality and performance for your silicone rubber molded products.Ready to transform your vision into reality? Contact us today for a free quote! Fill out the form below or shoot us an email, and let’s craft a future of possibilities, together.