CNC Machining Services
Rapid Prototypes In As Fast As 2 Days
20K+ CNC Parts Produced Every Month
Tolerance Accuracy From +/- 0.001” to 0.003”
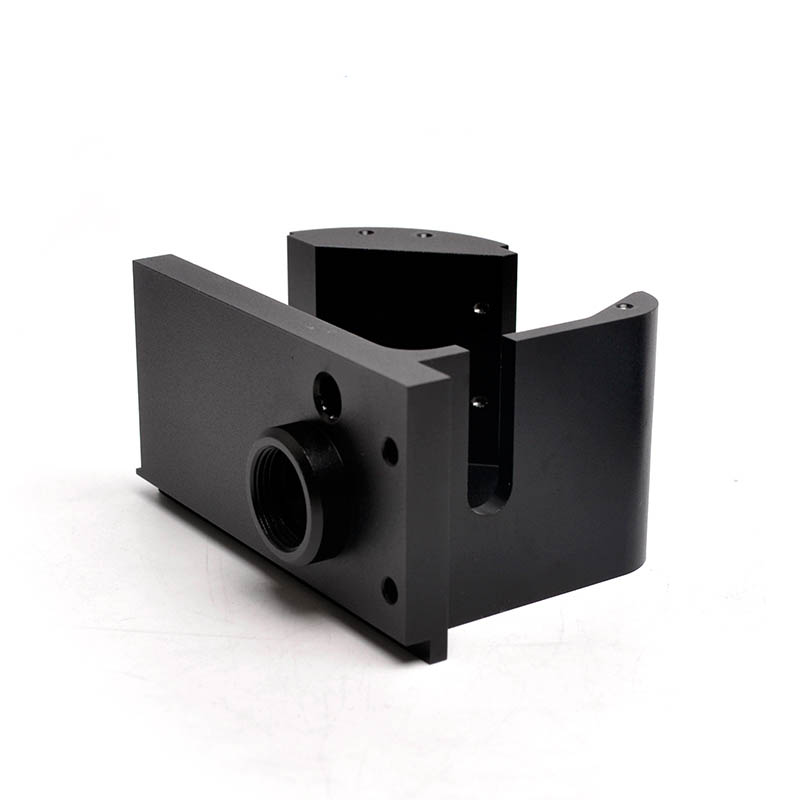
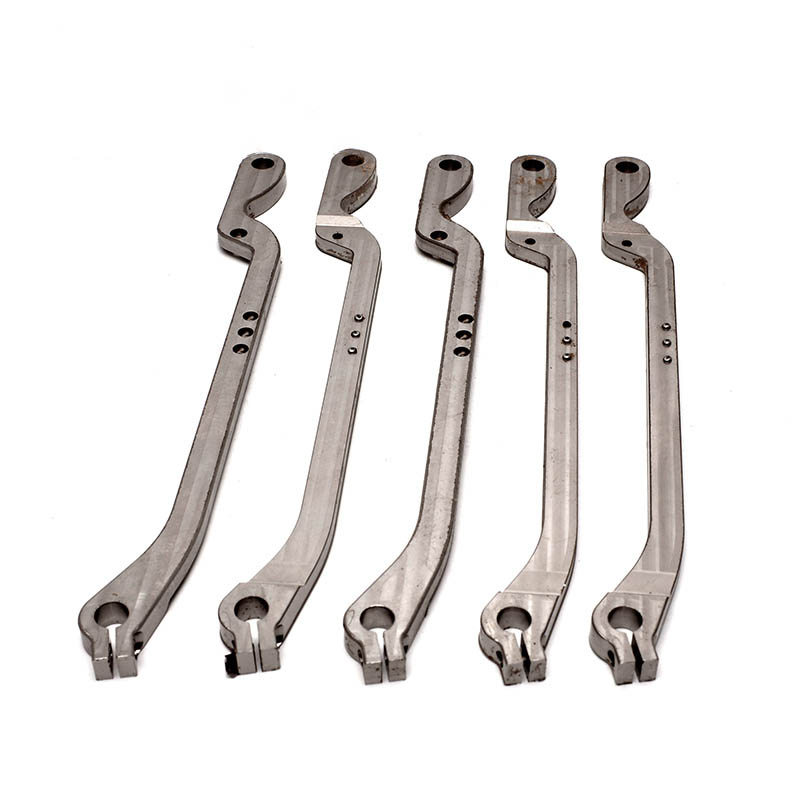
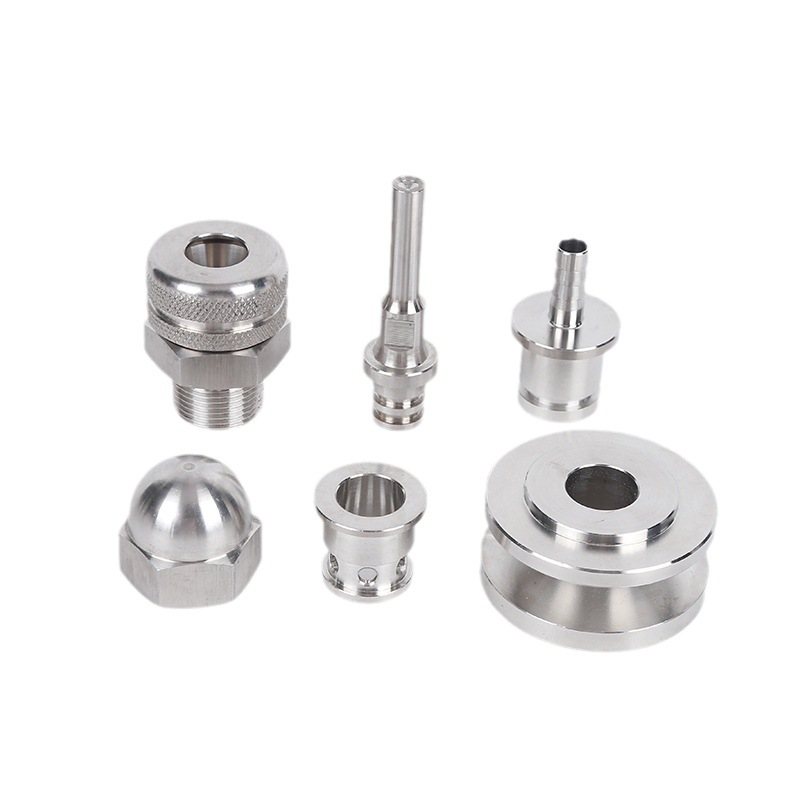
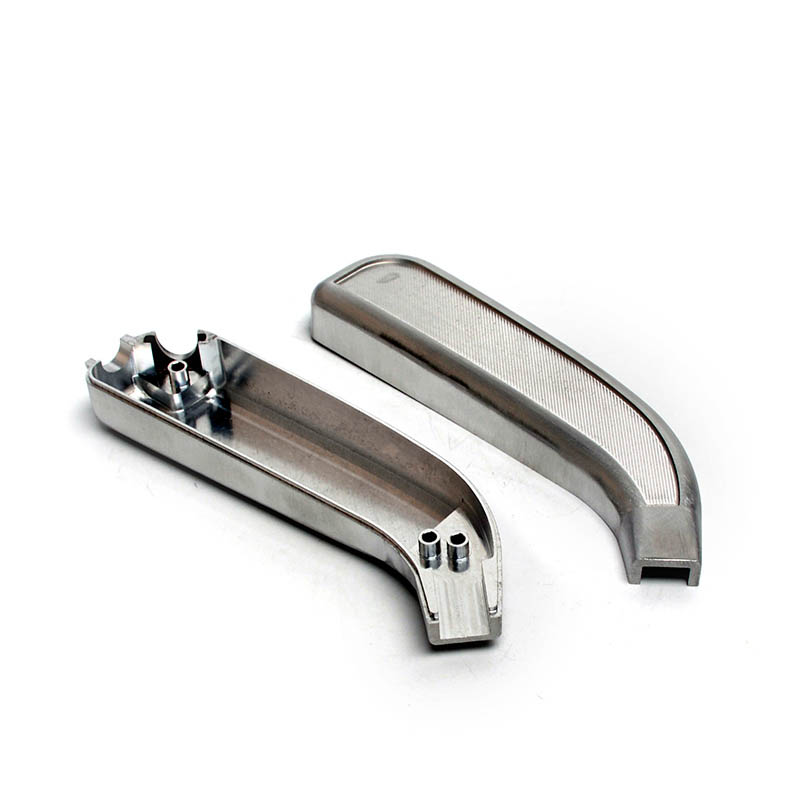
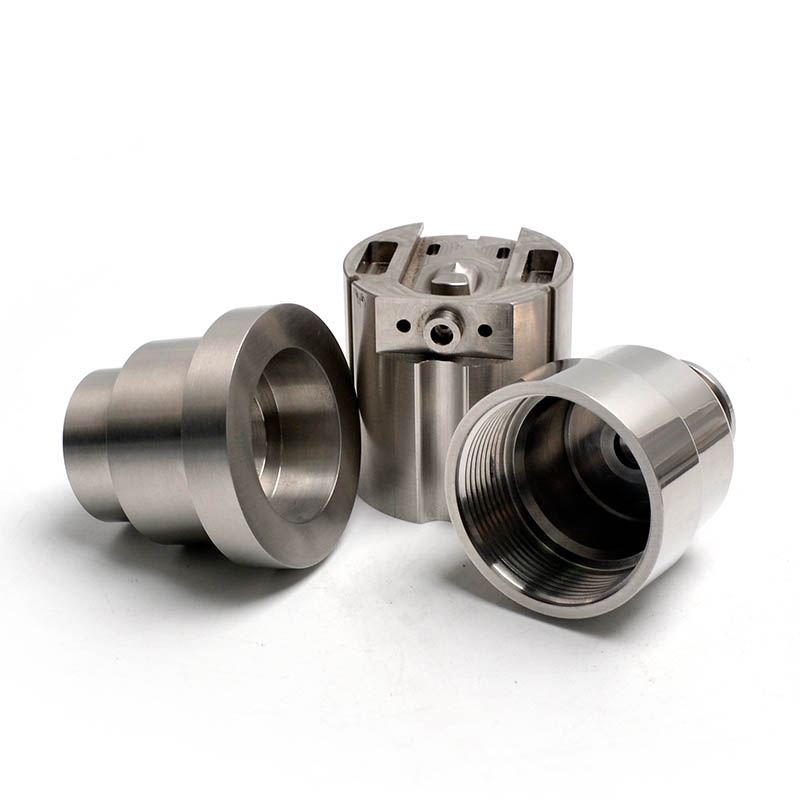

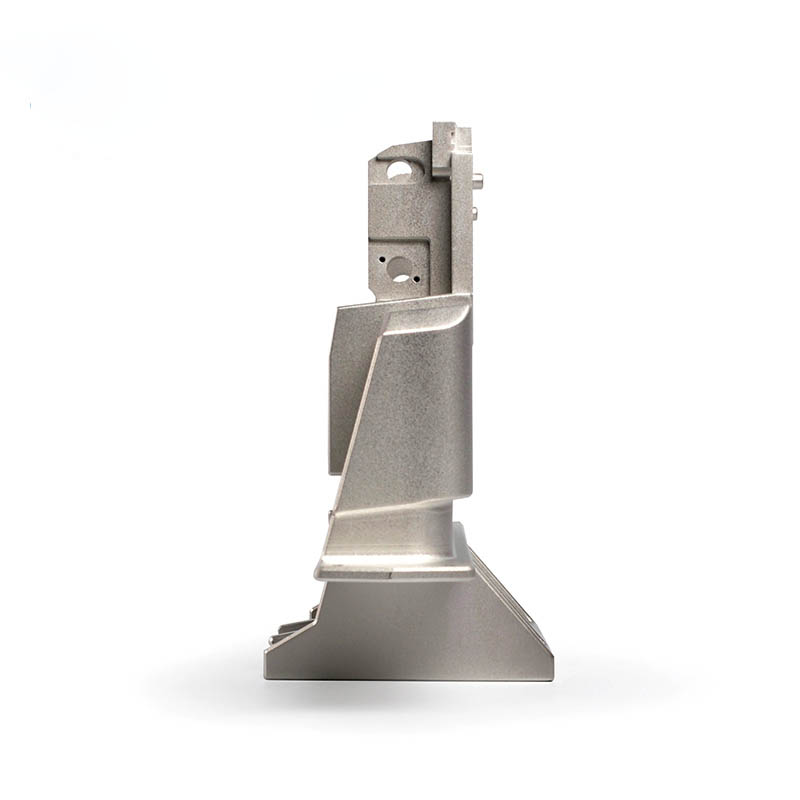
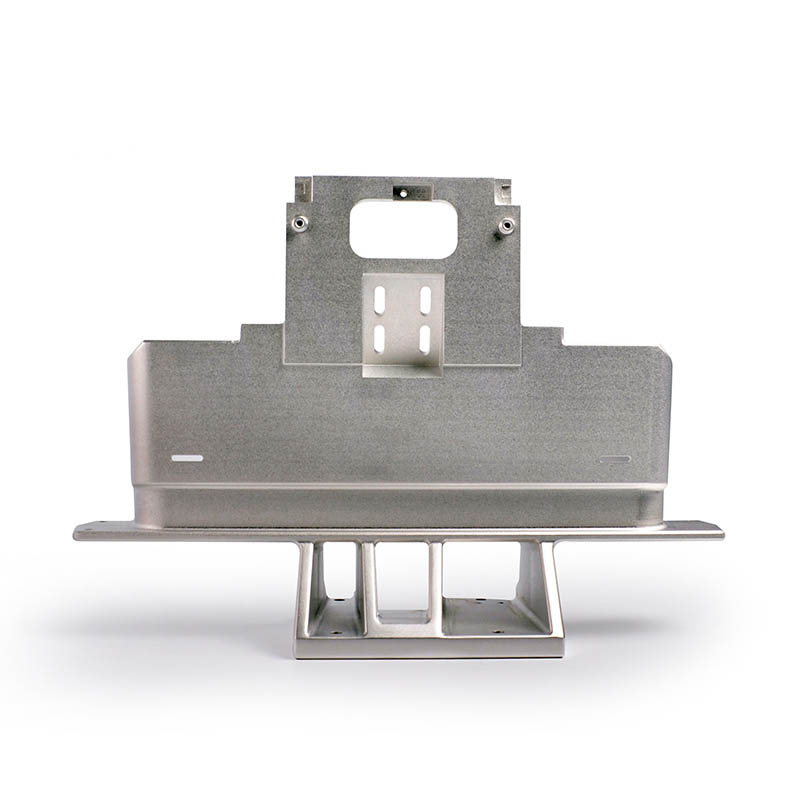
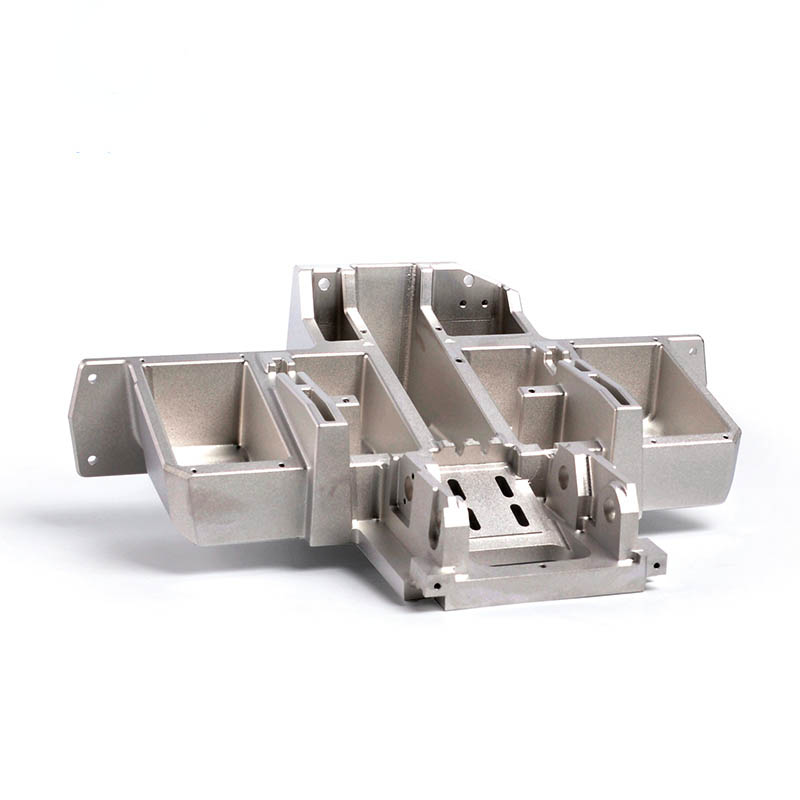
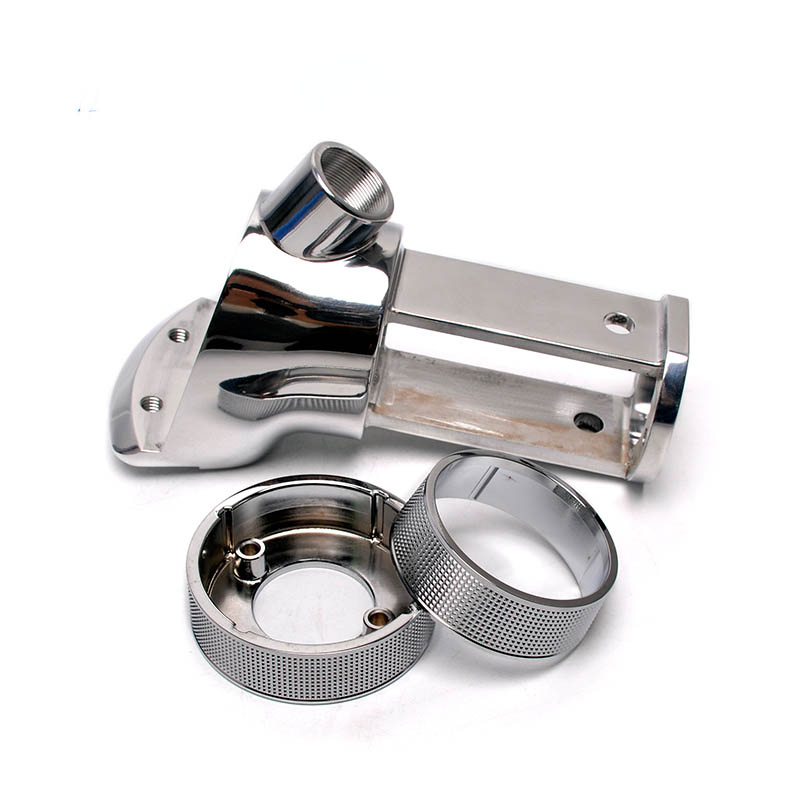
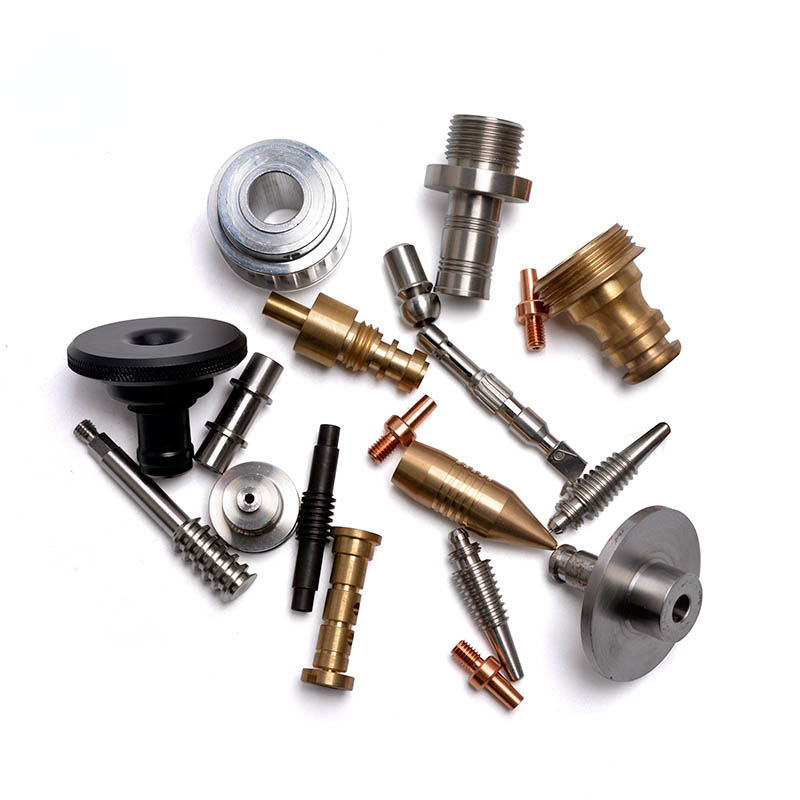
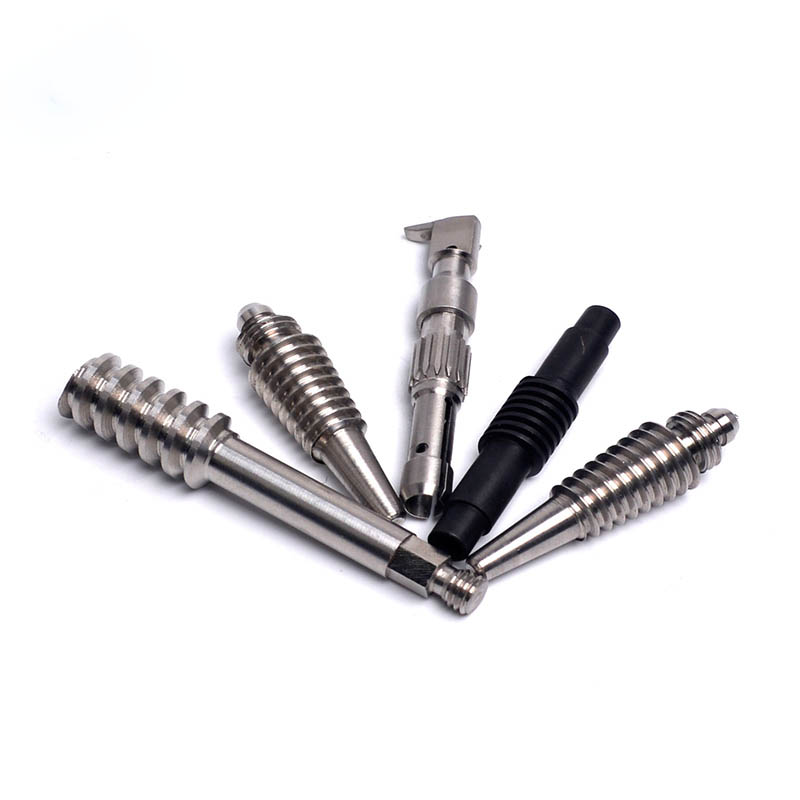
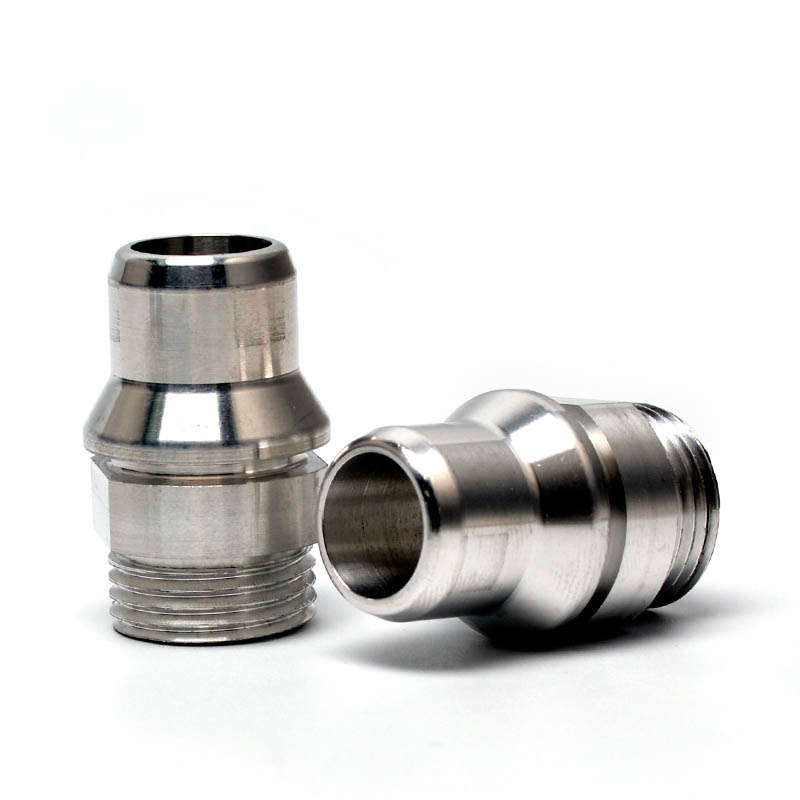
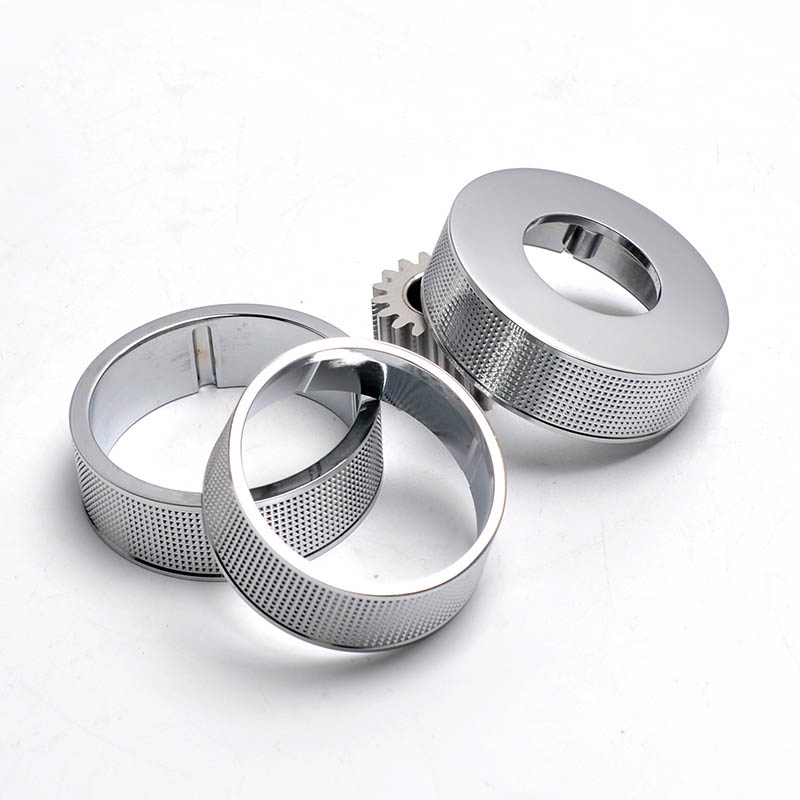
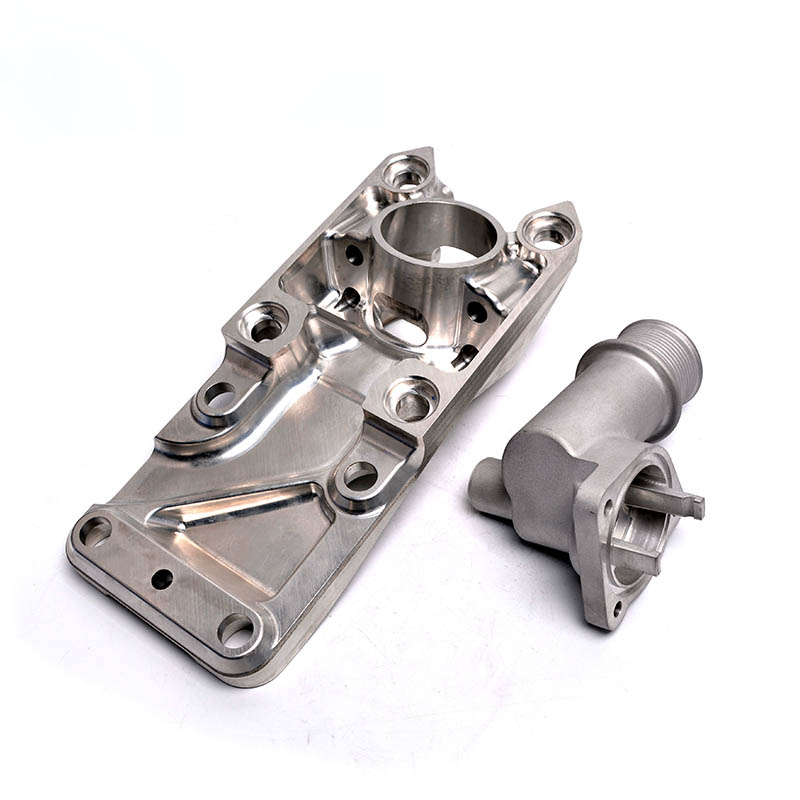
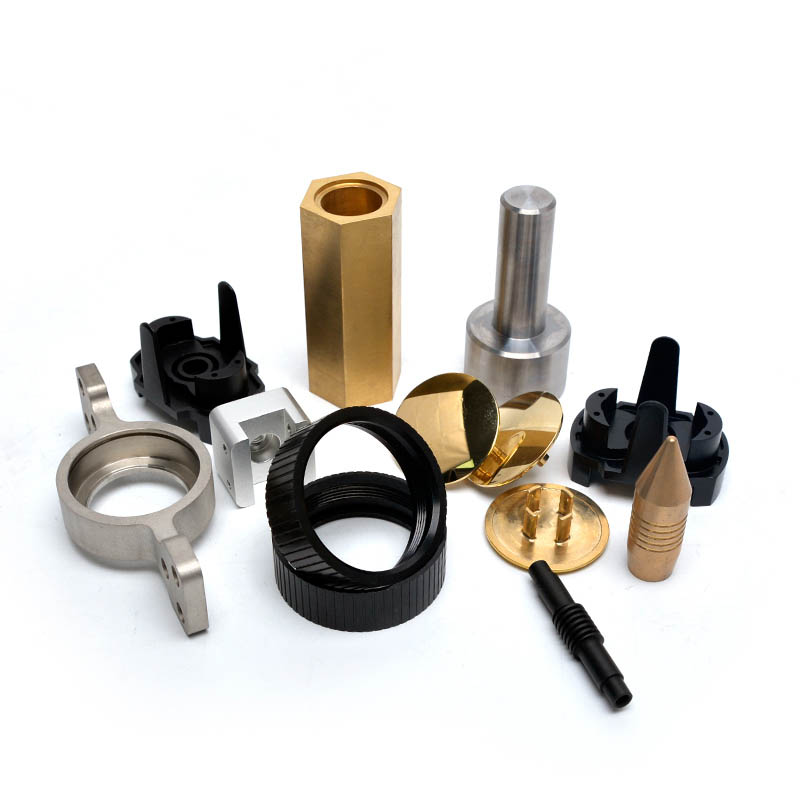
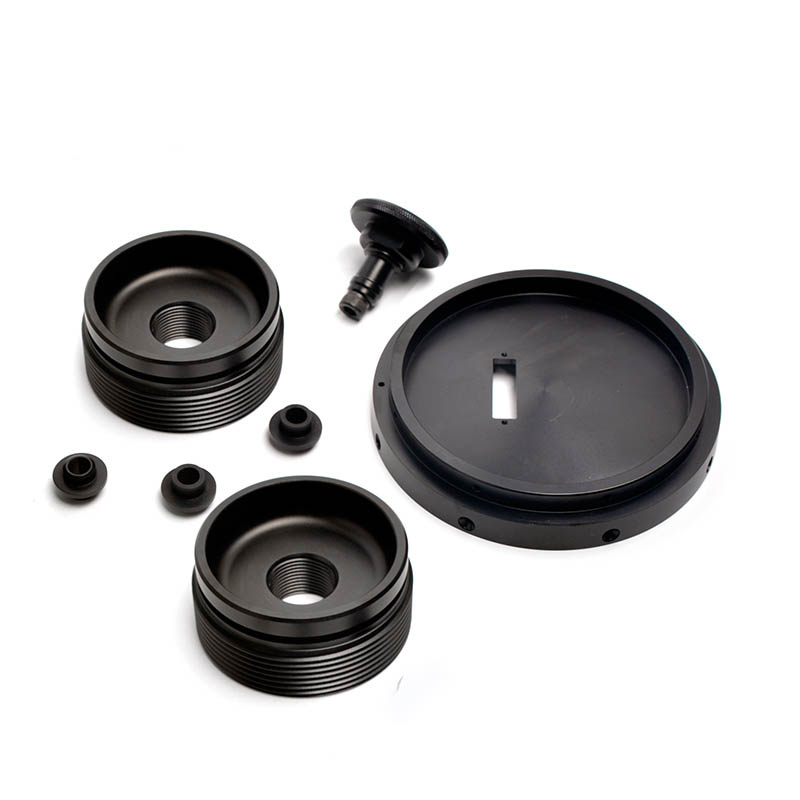
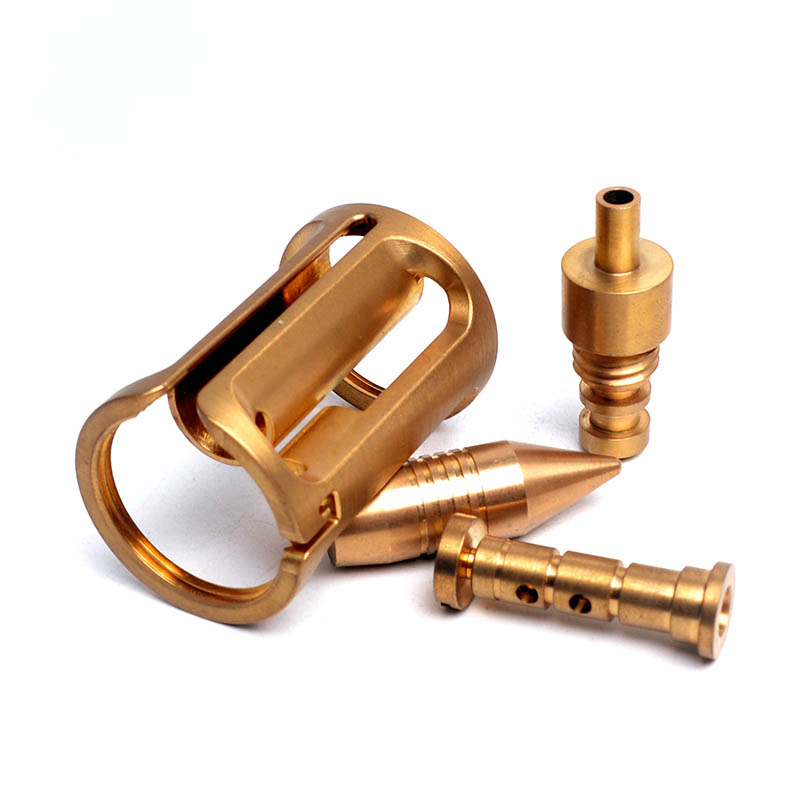
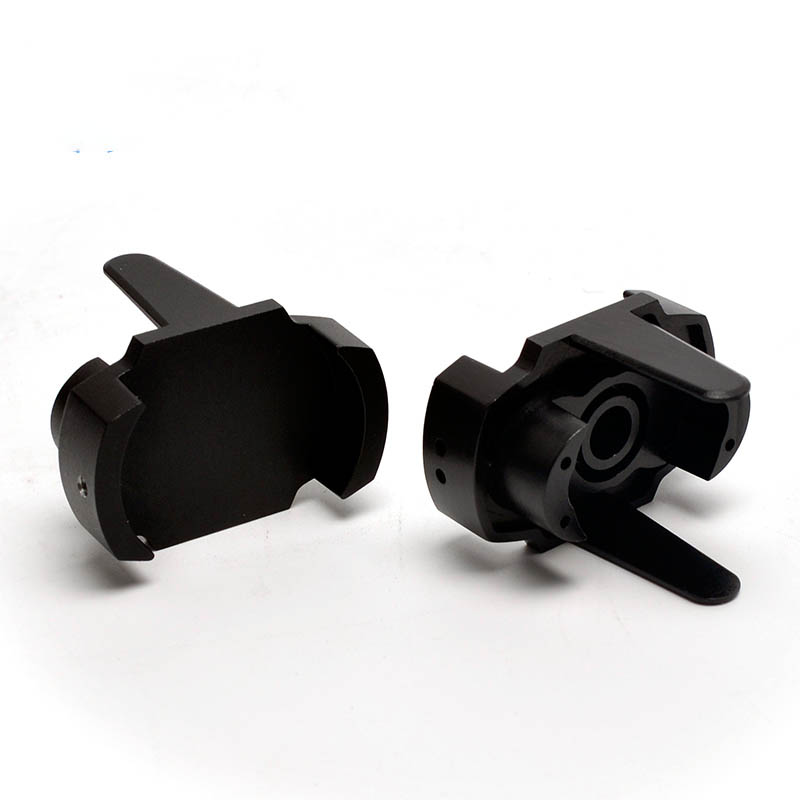

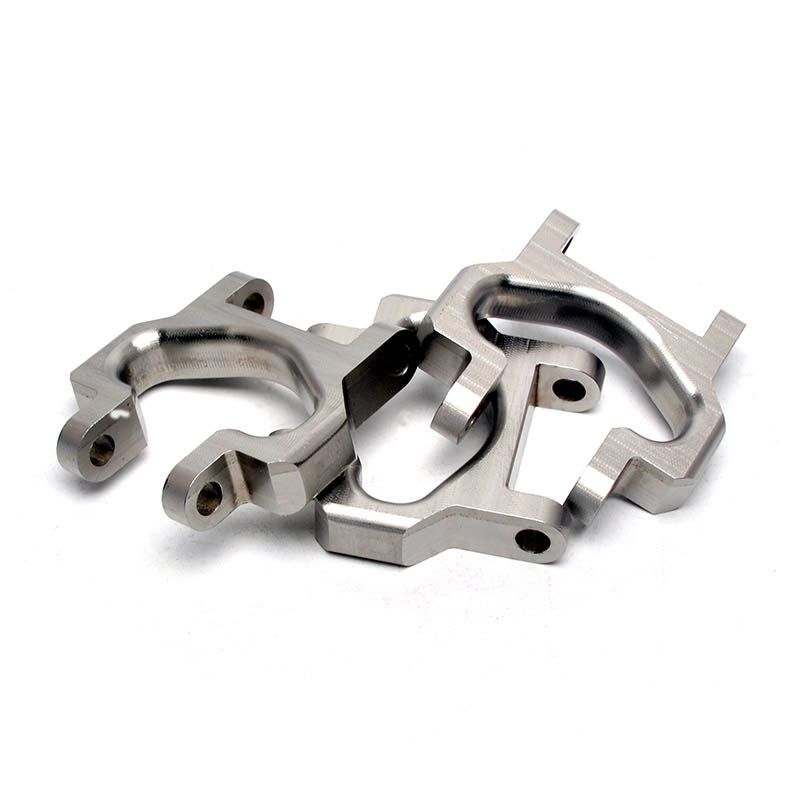
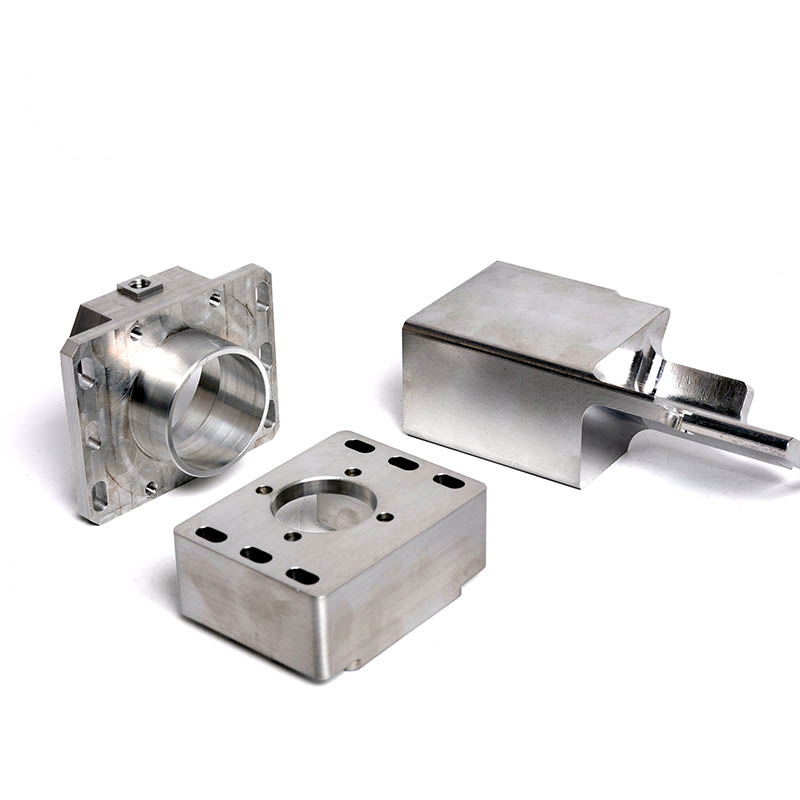
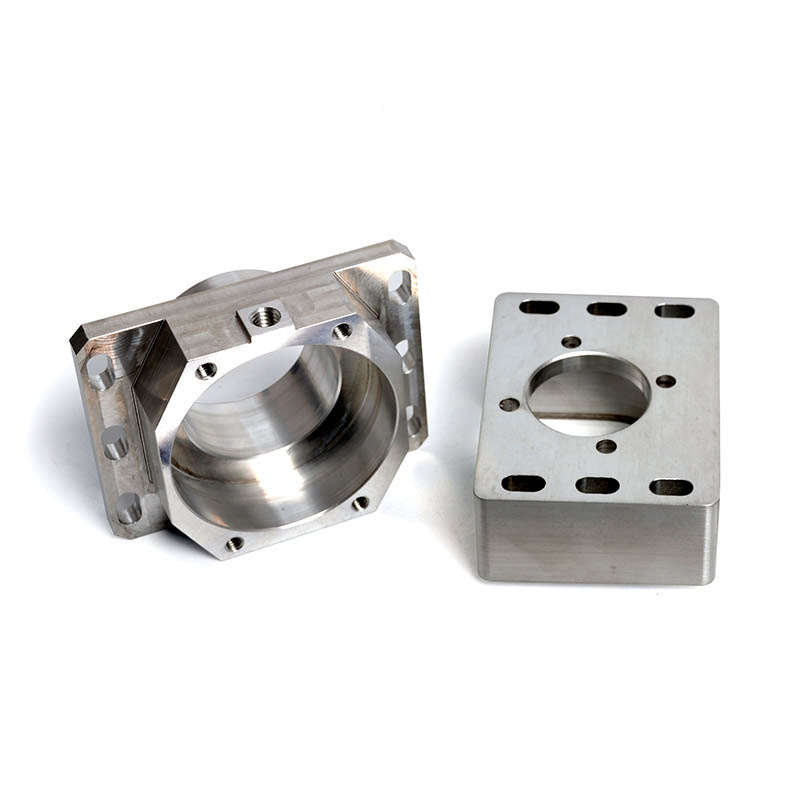
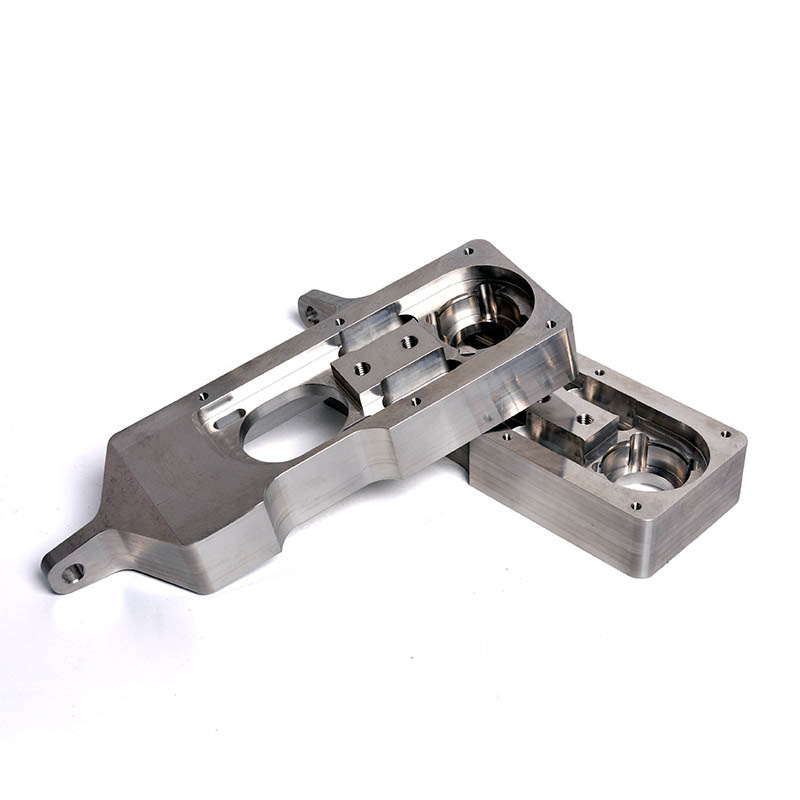
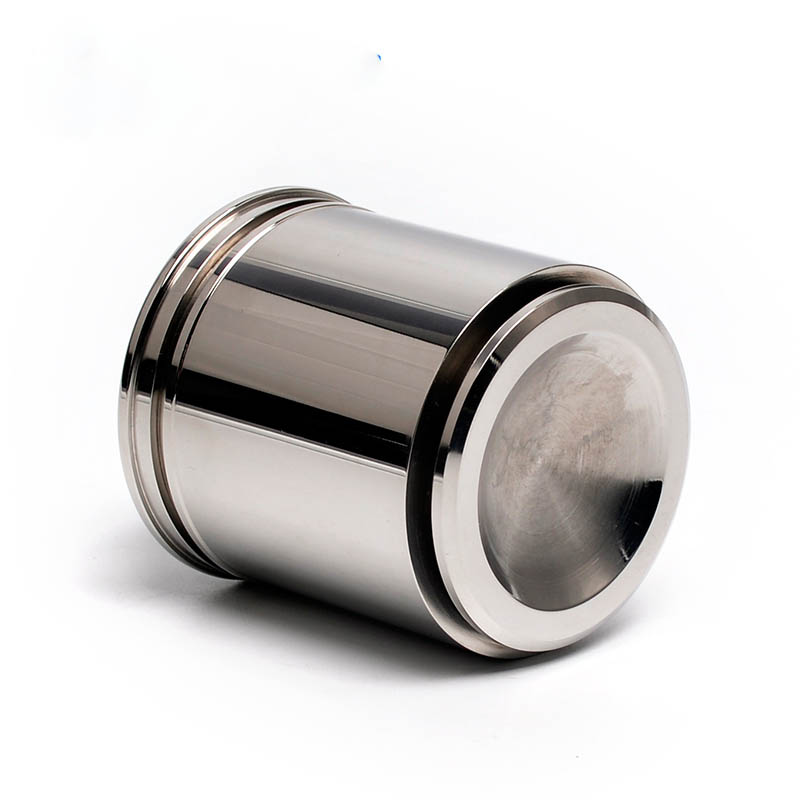
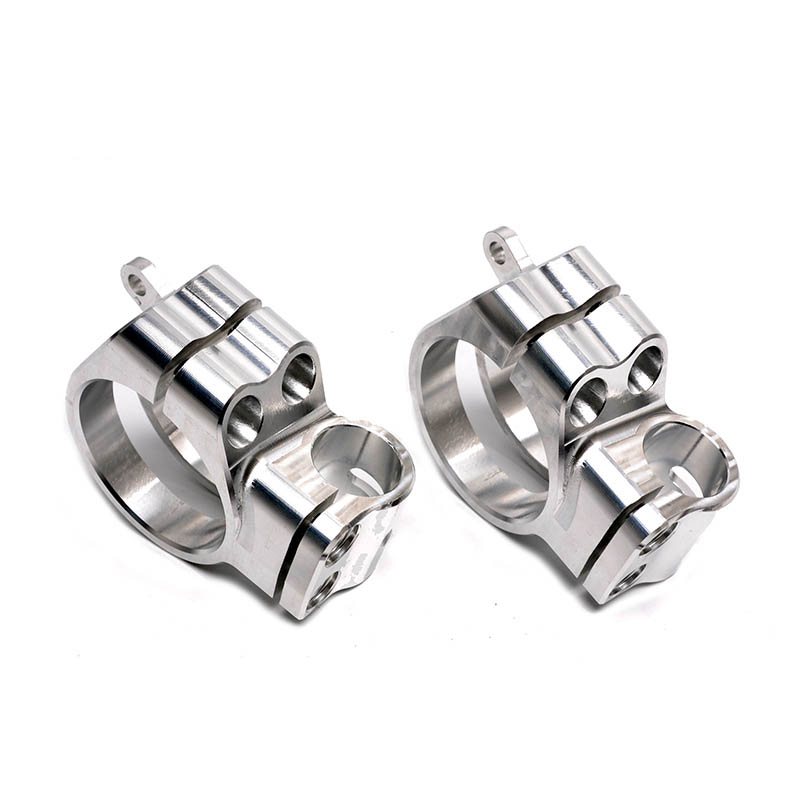
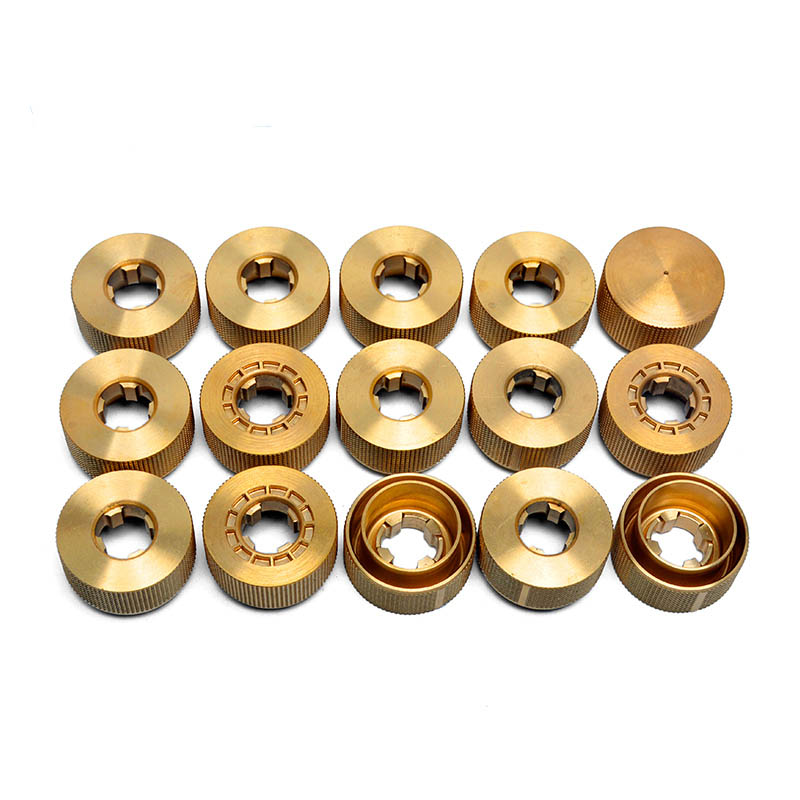
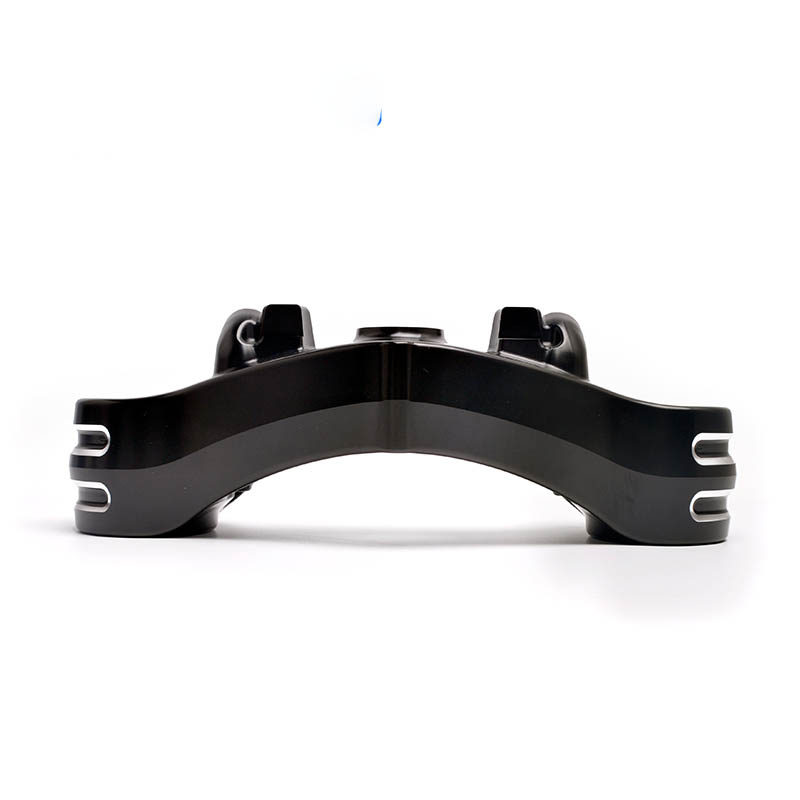
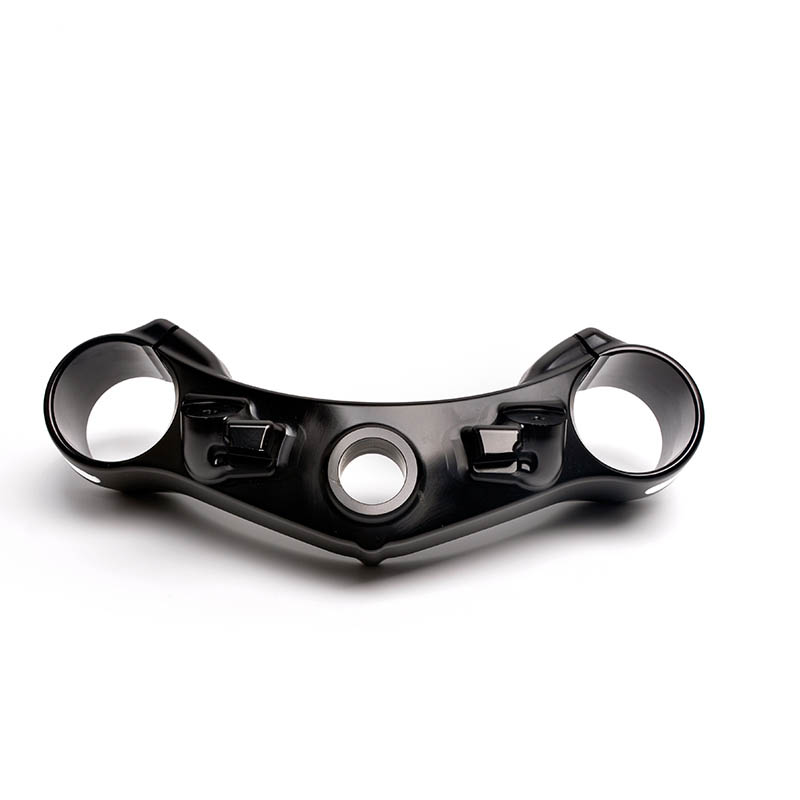

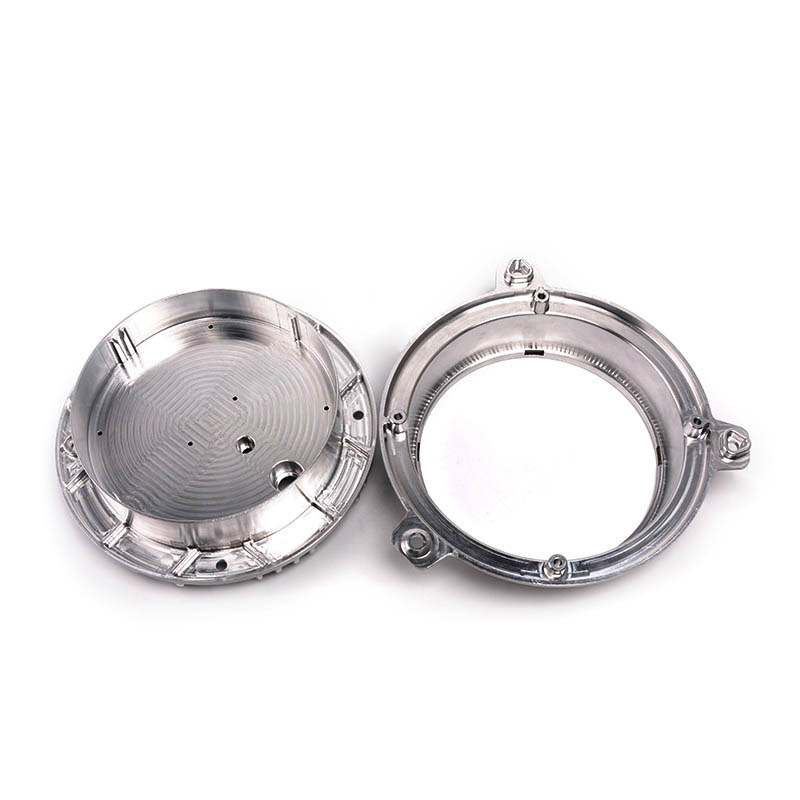
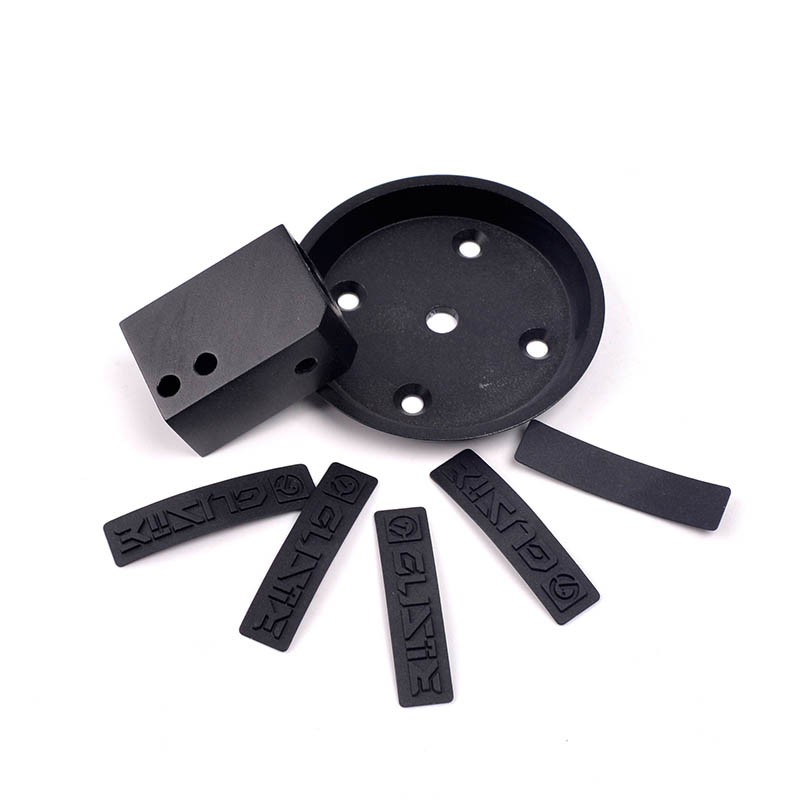
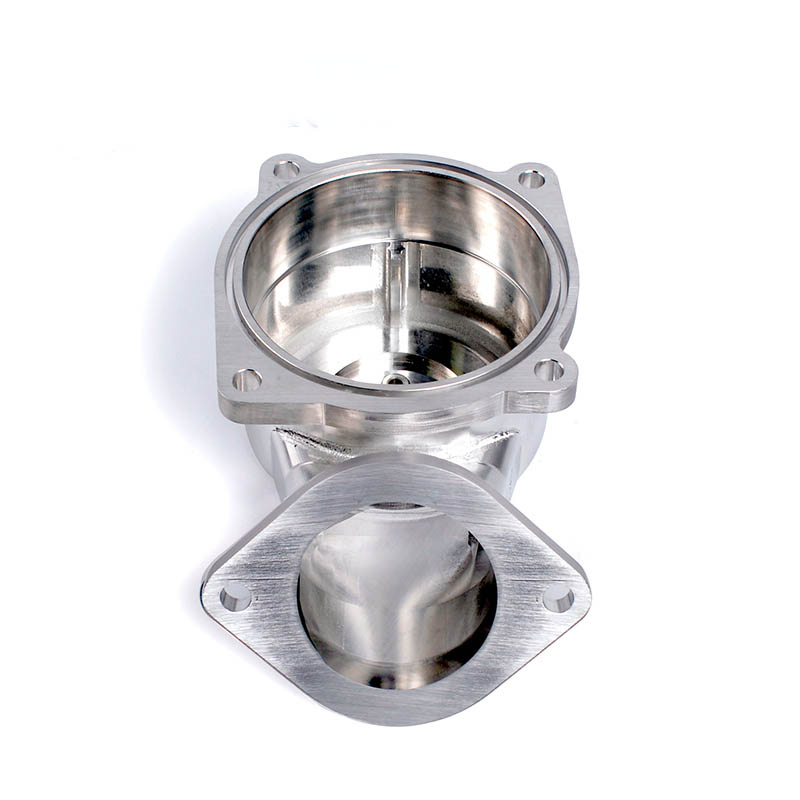
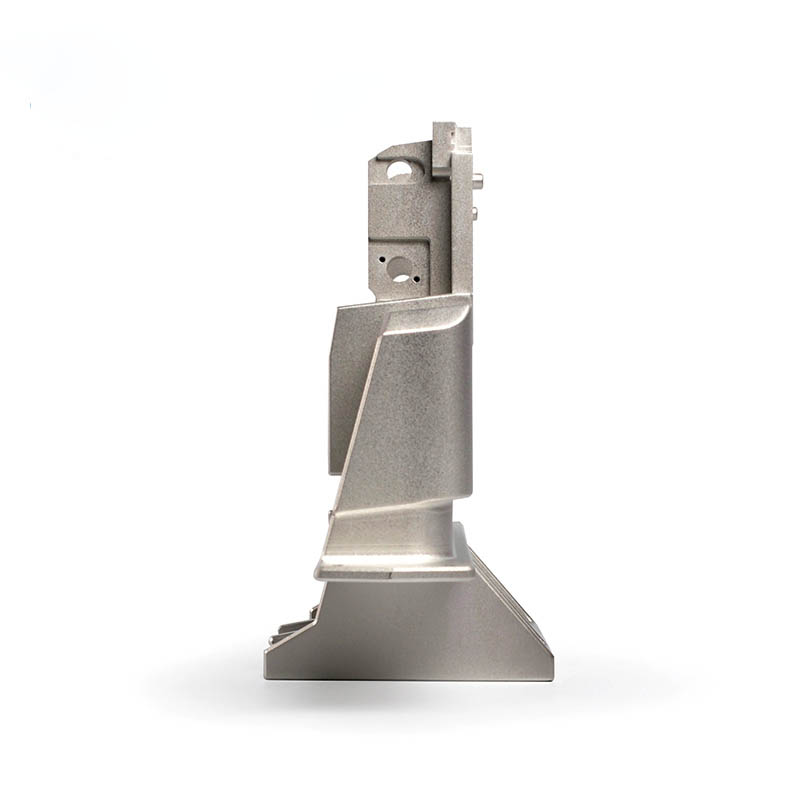
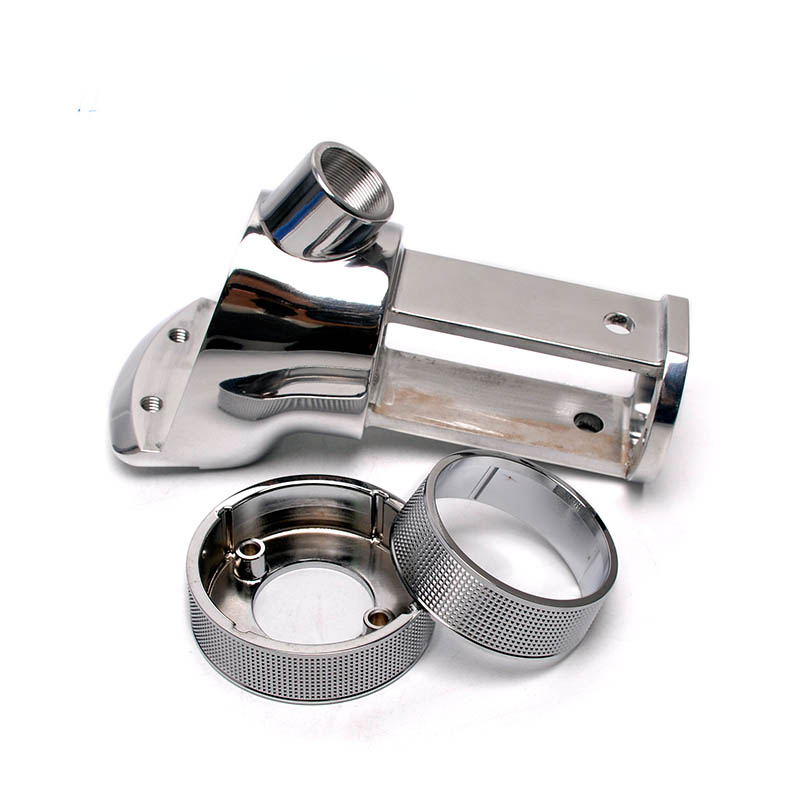
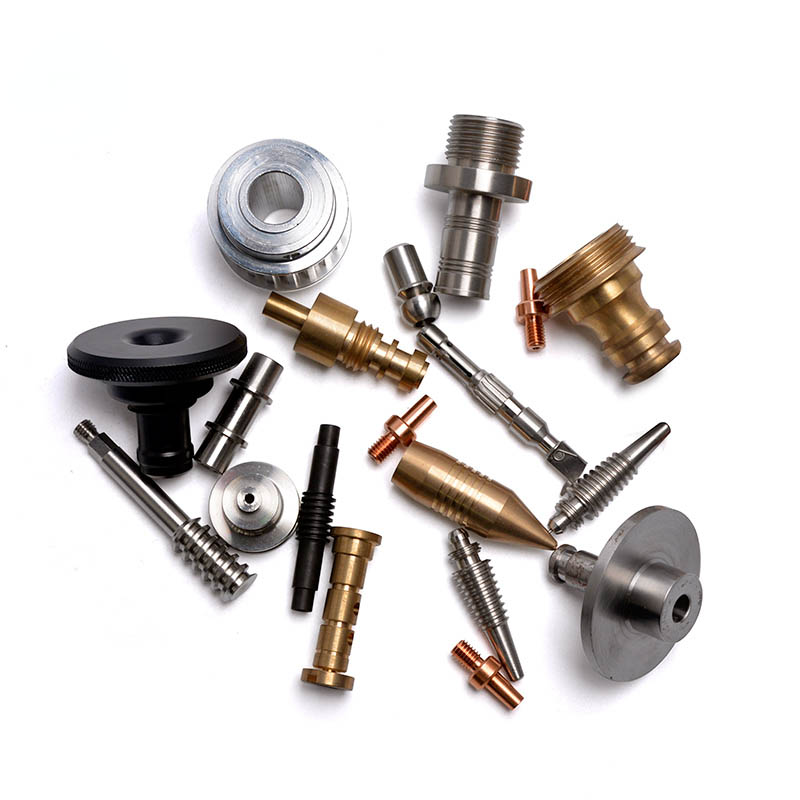
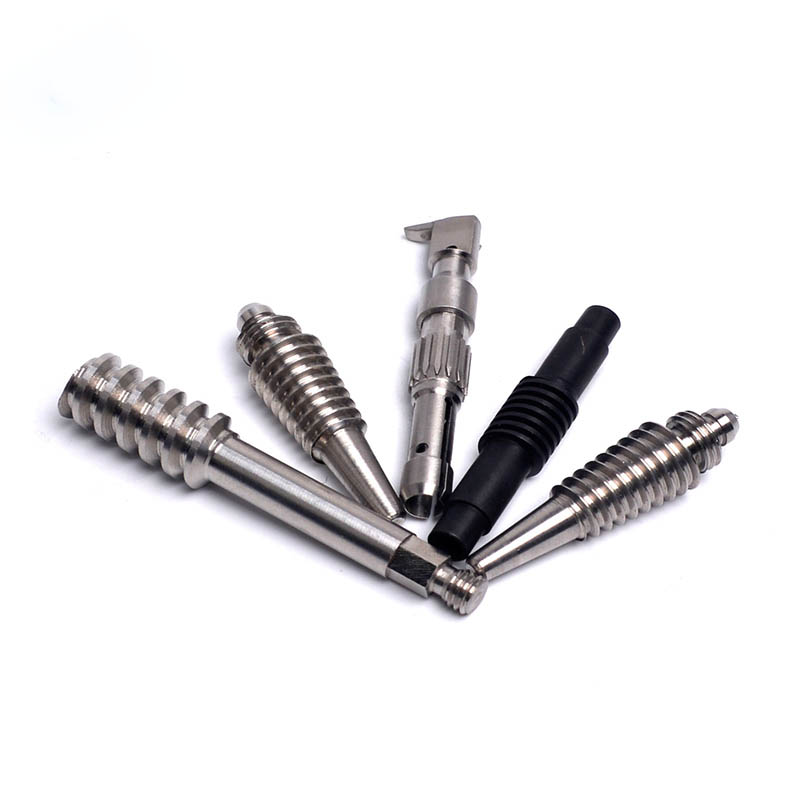
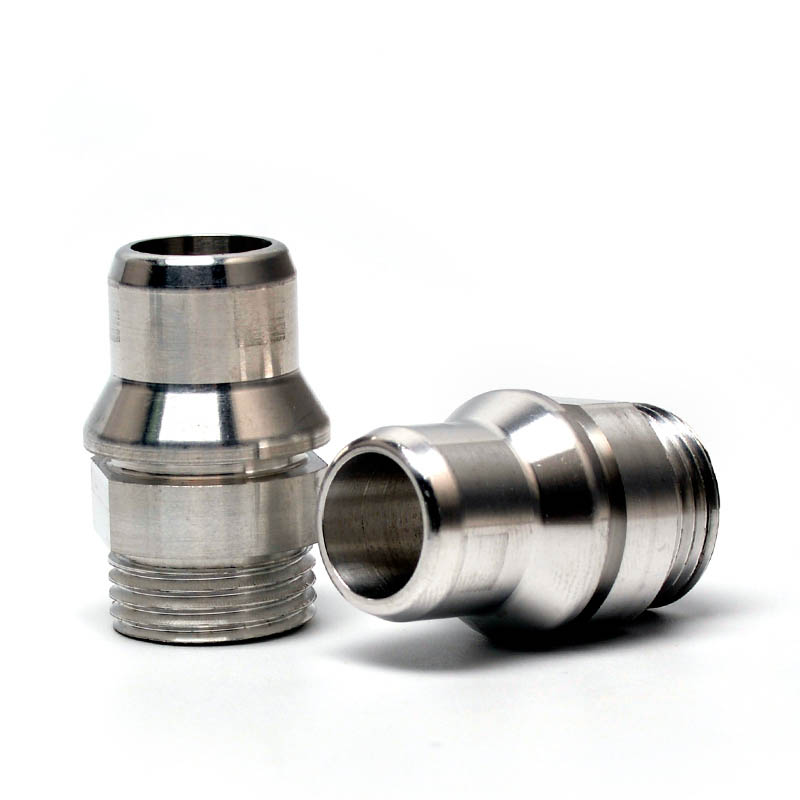
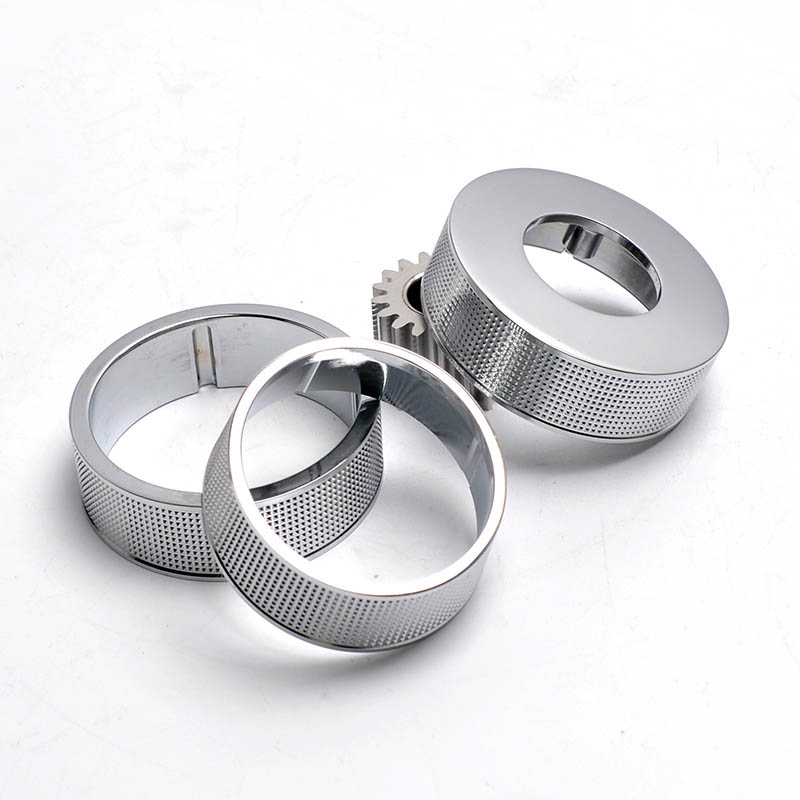
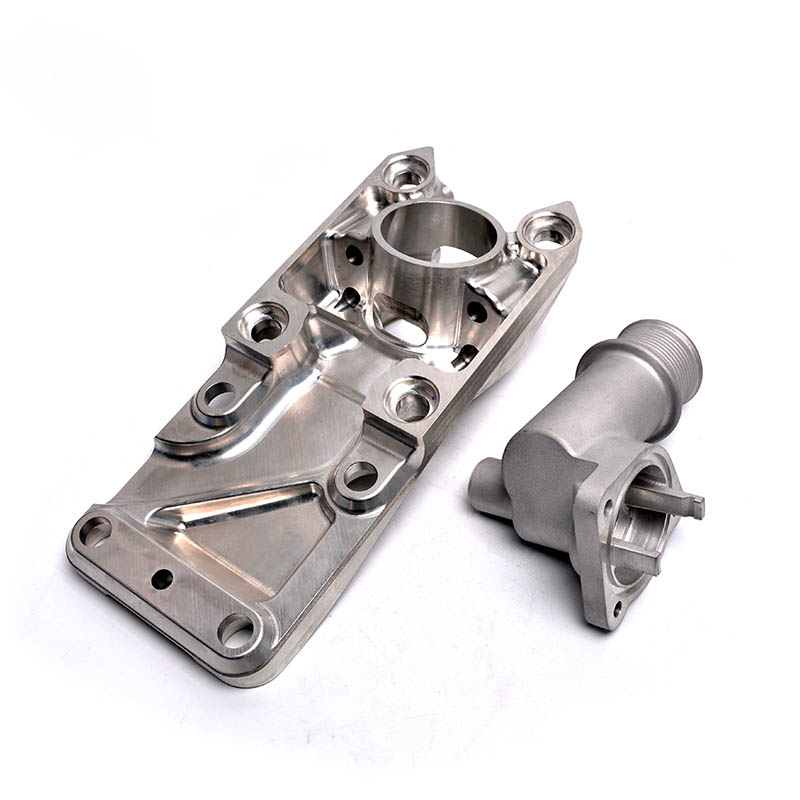
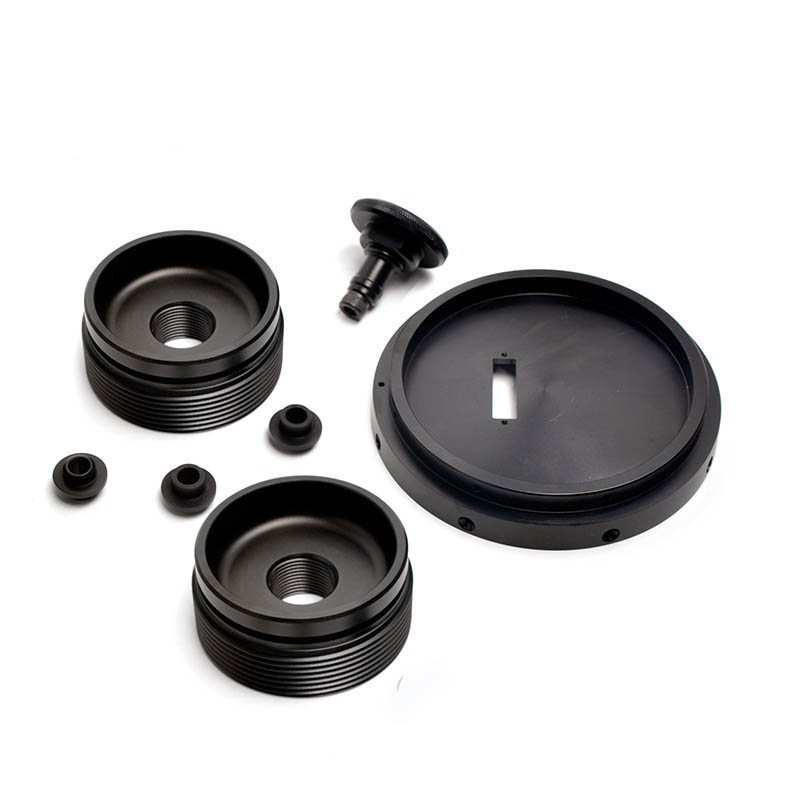
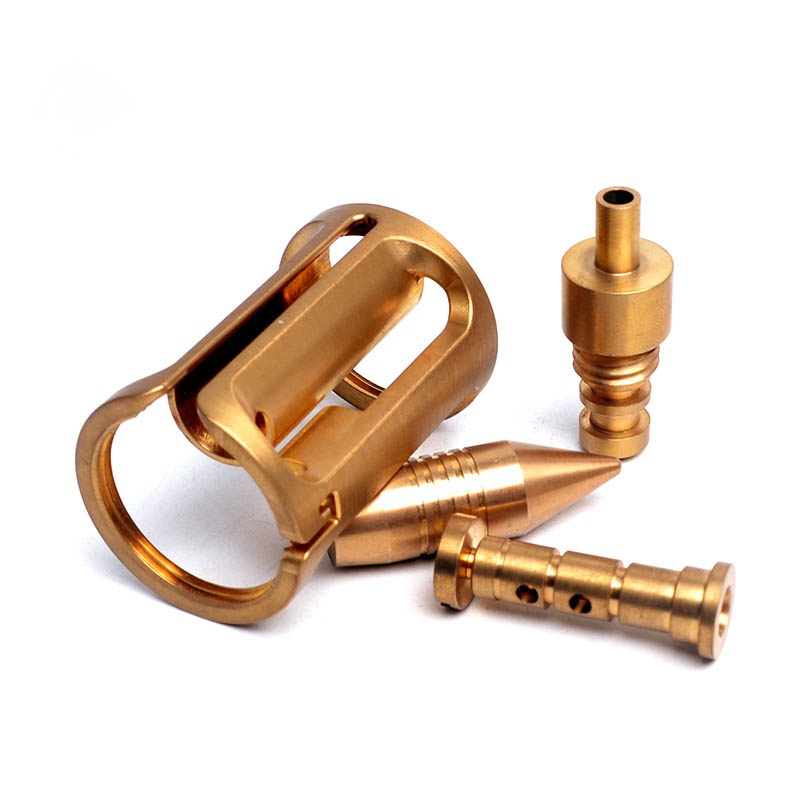
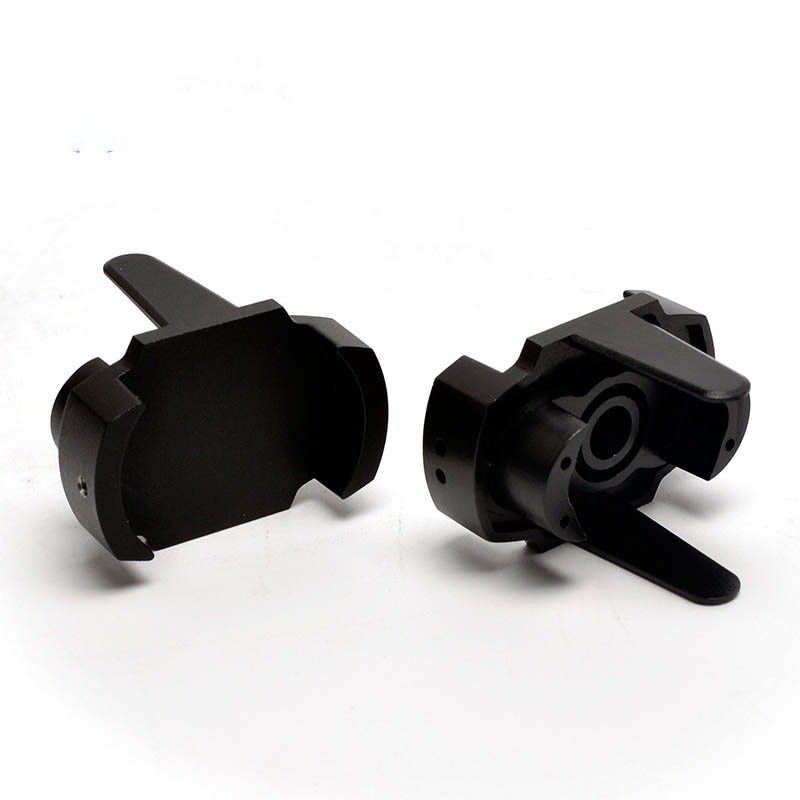
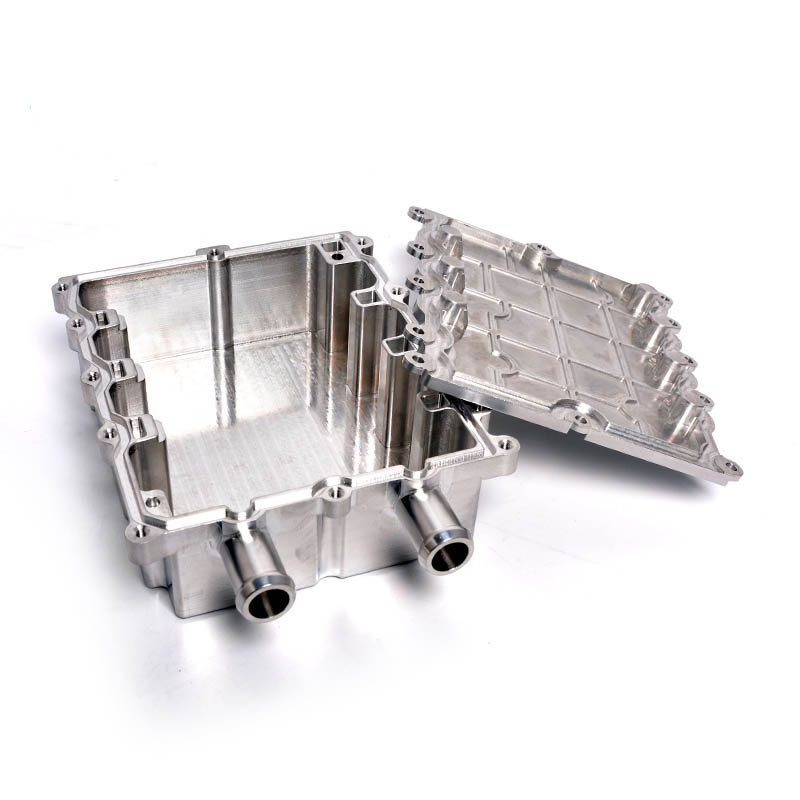
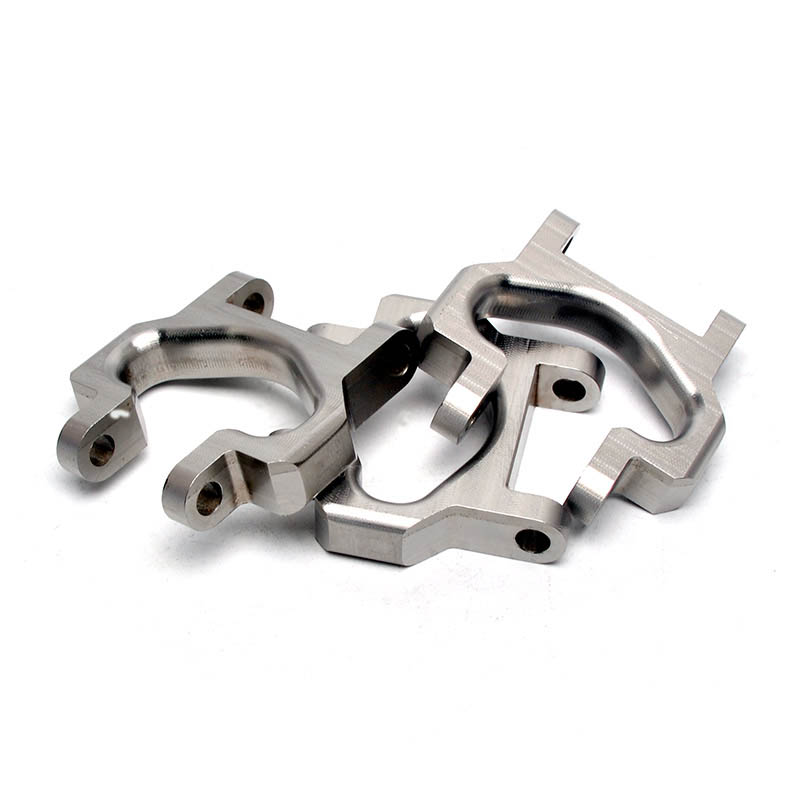
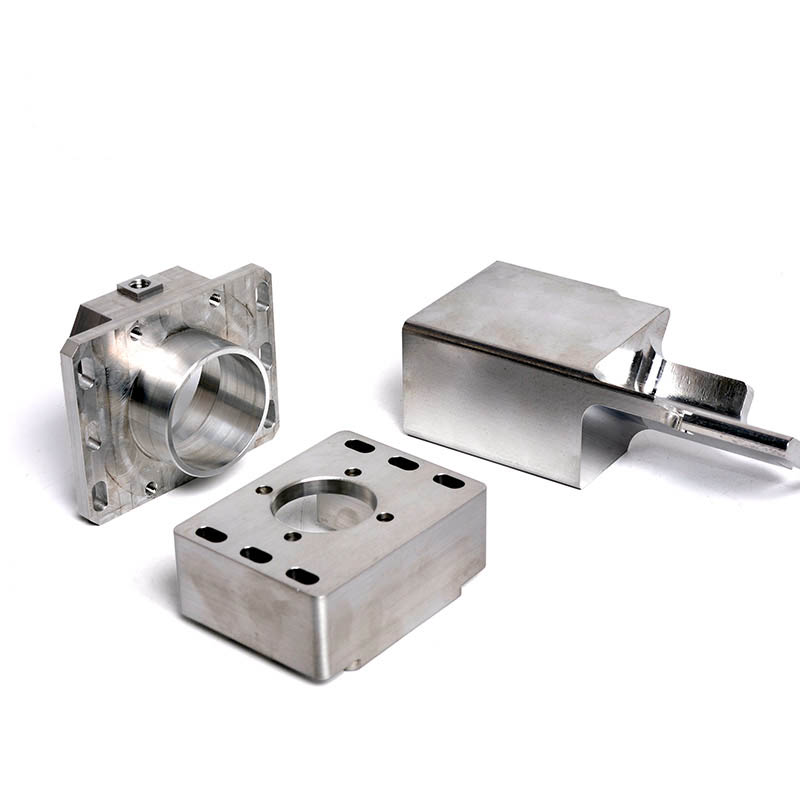
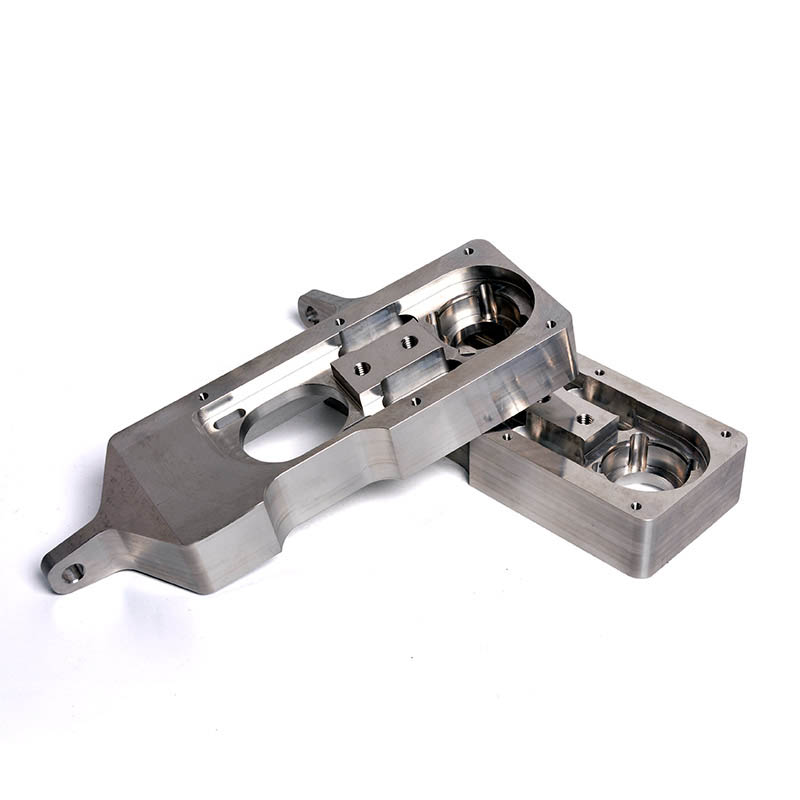
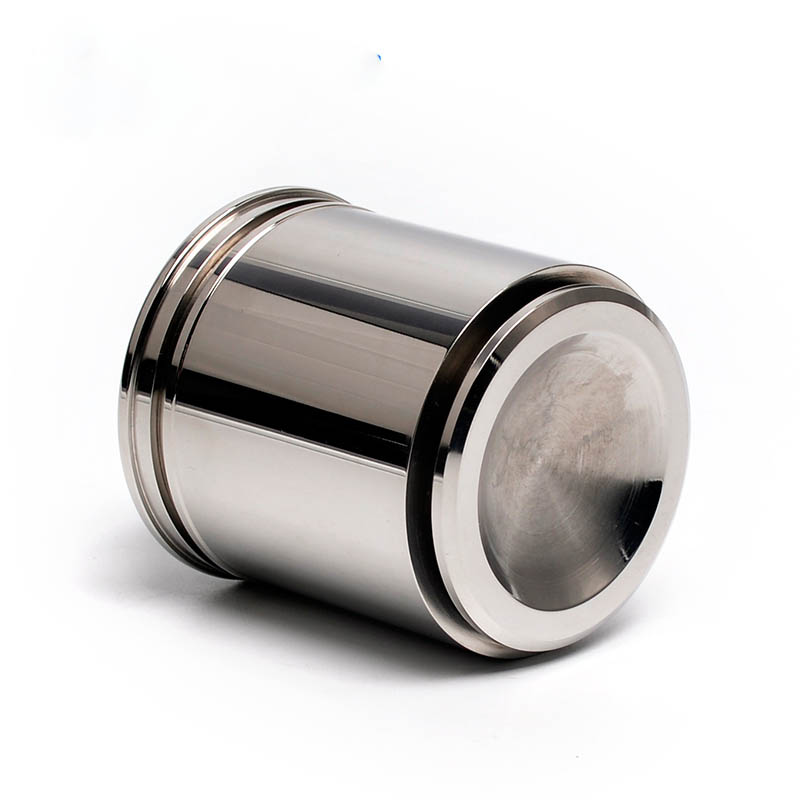
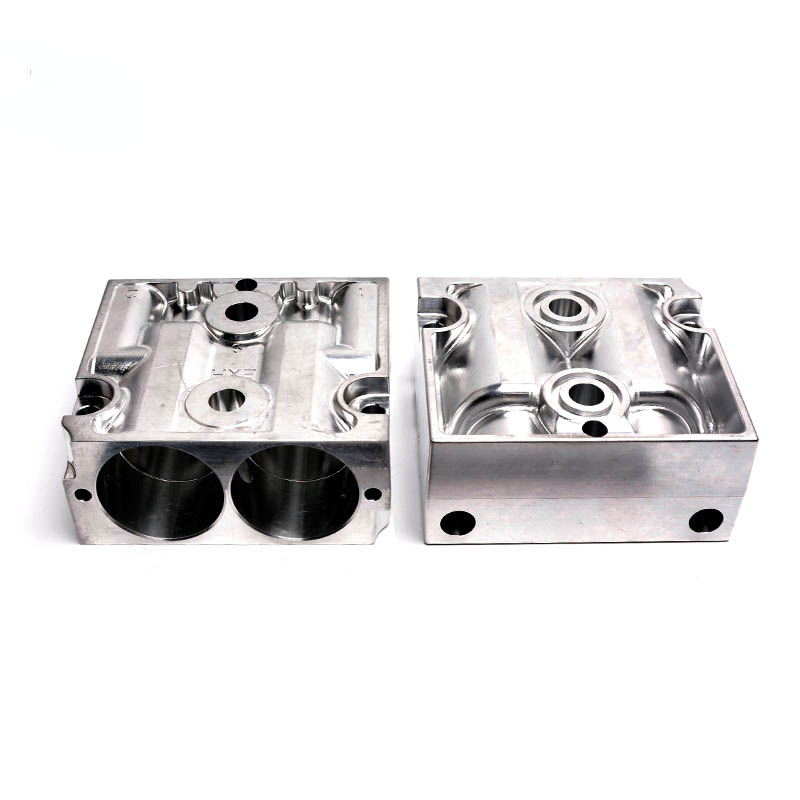
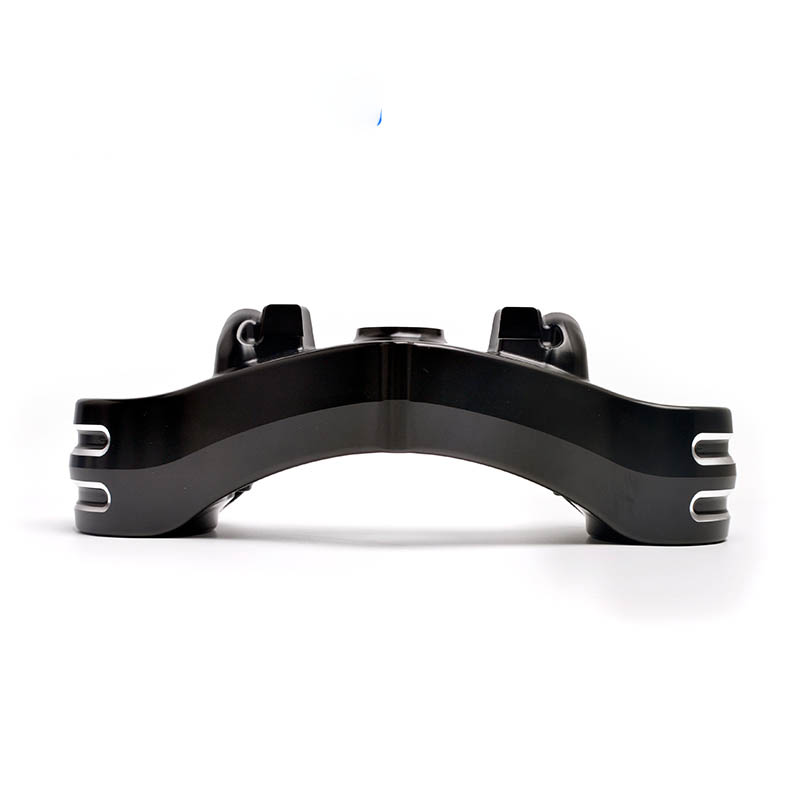
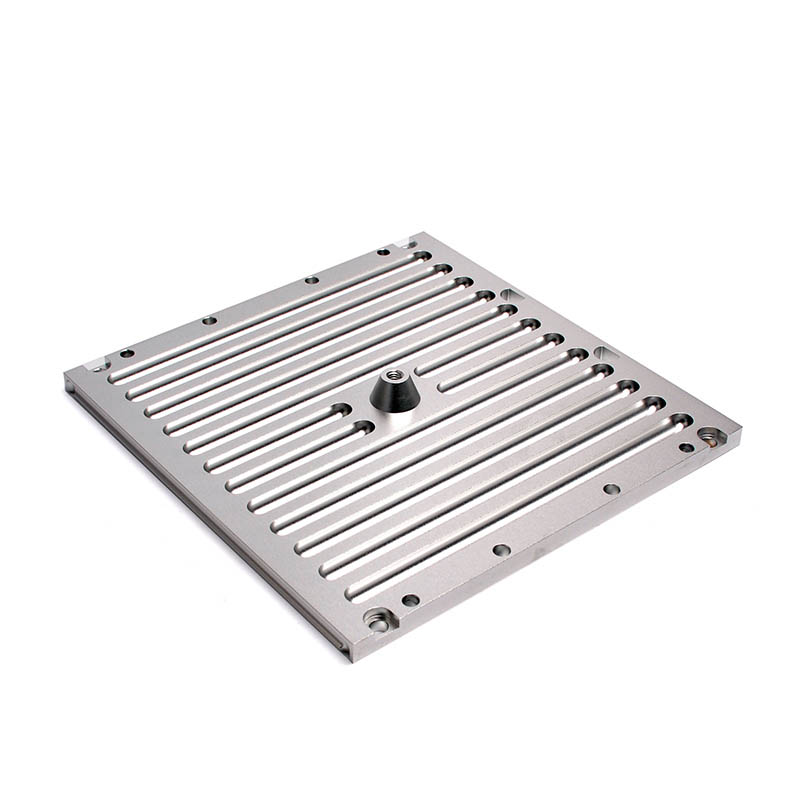
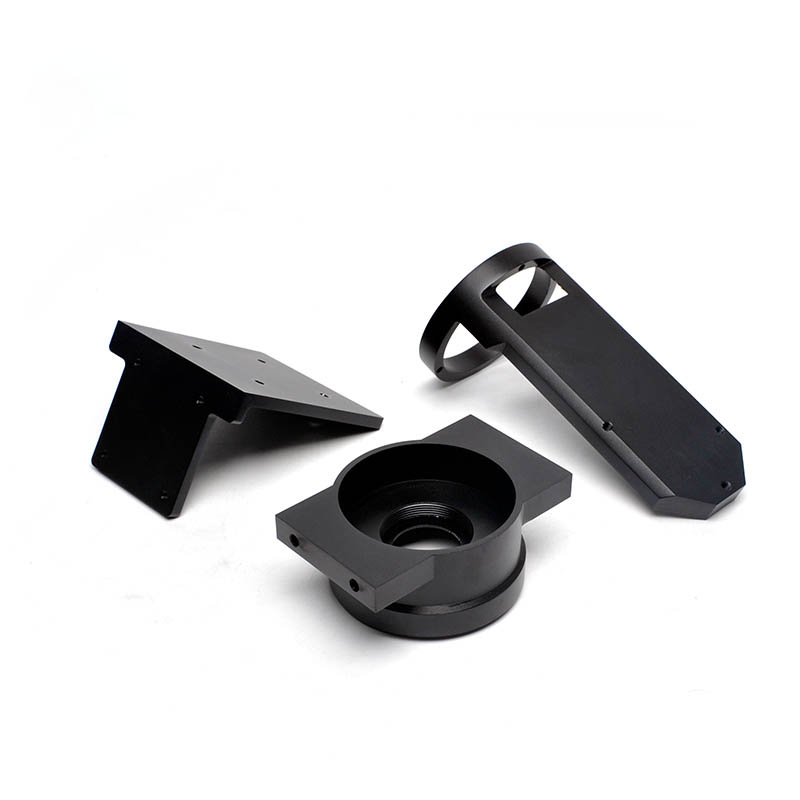
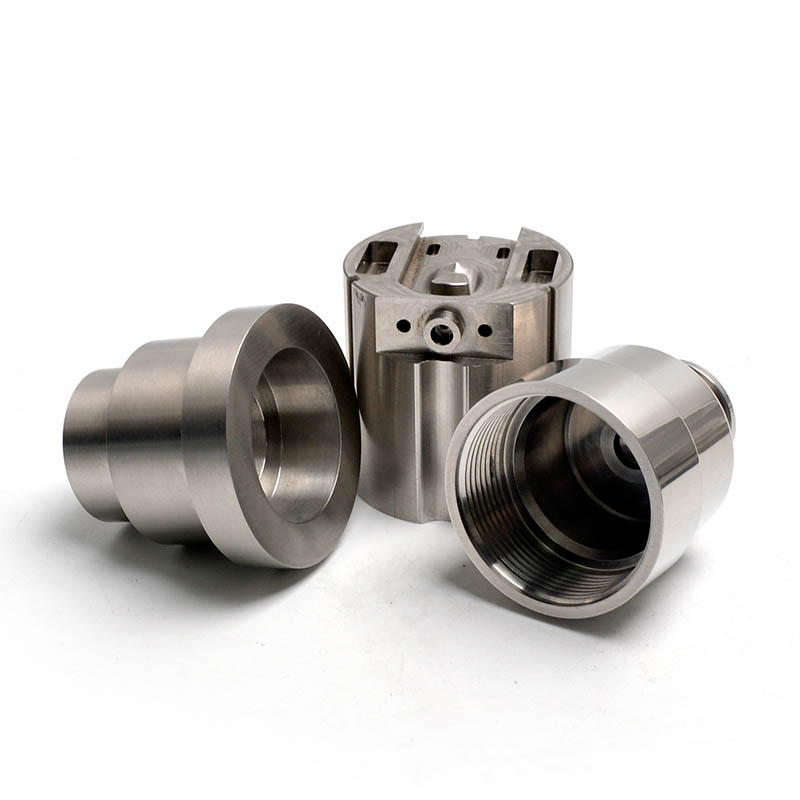
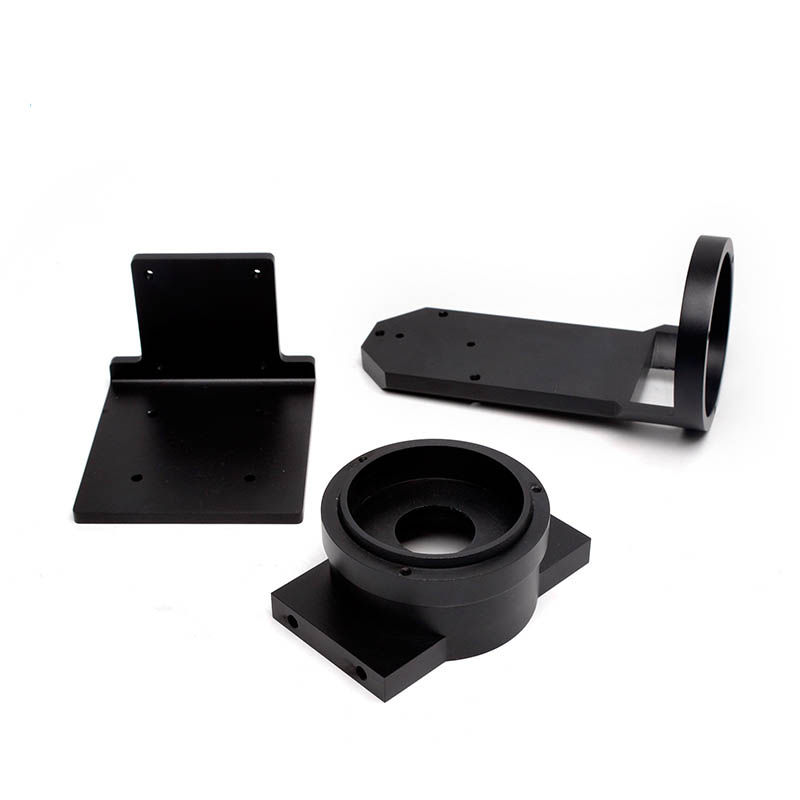
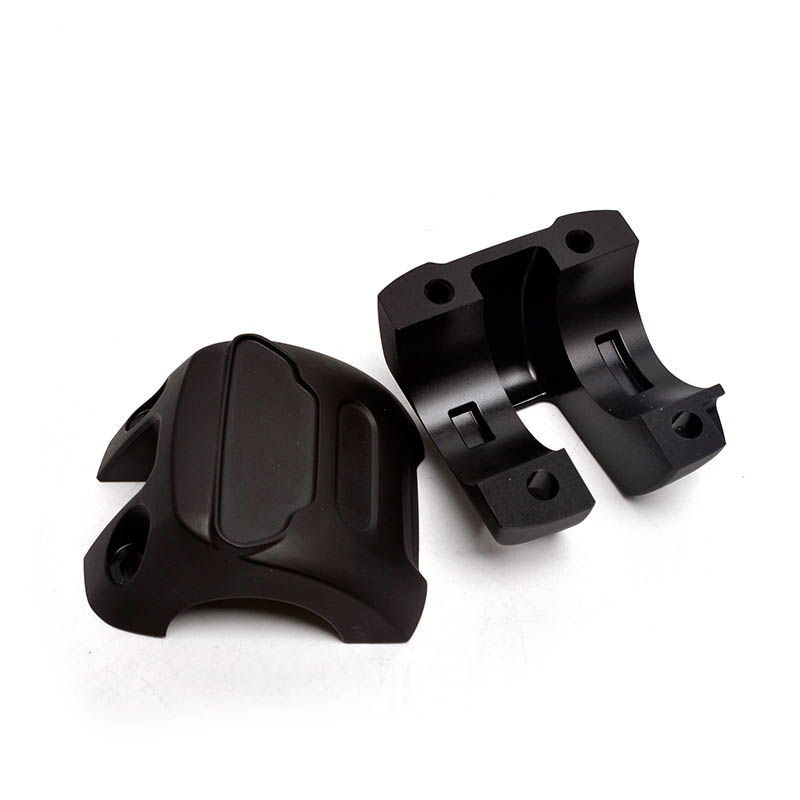
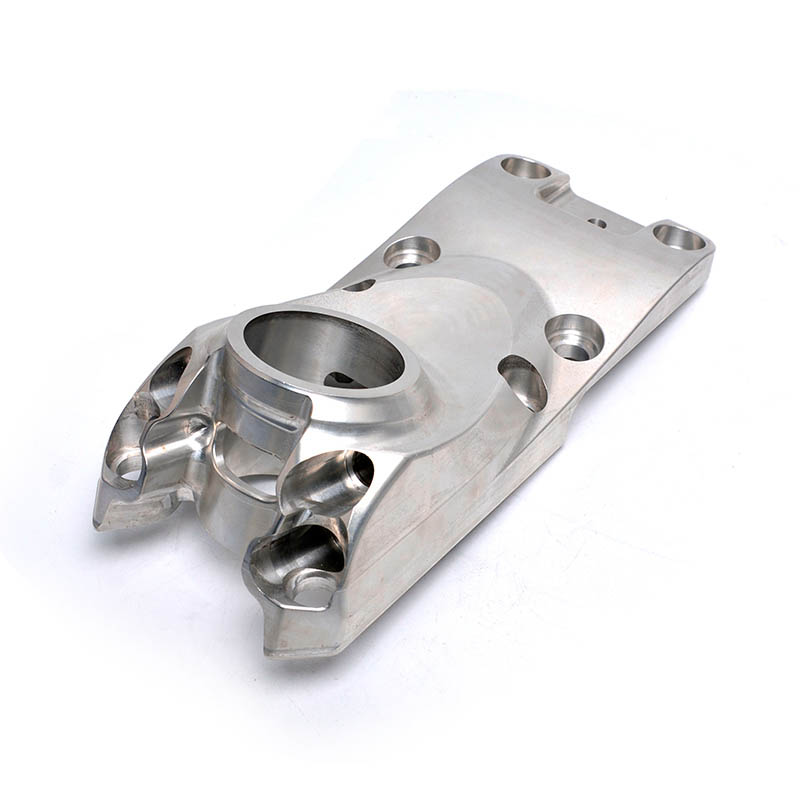
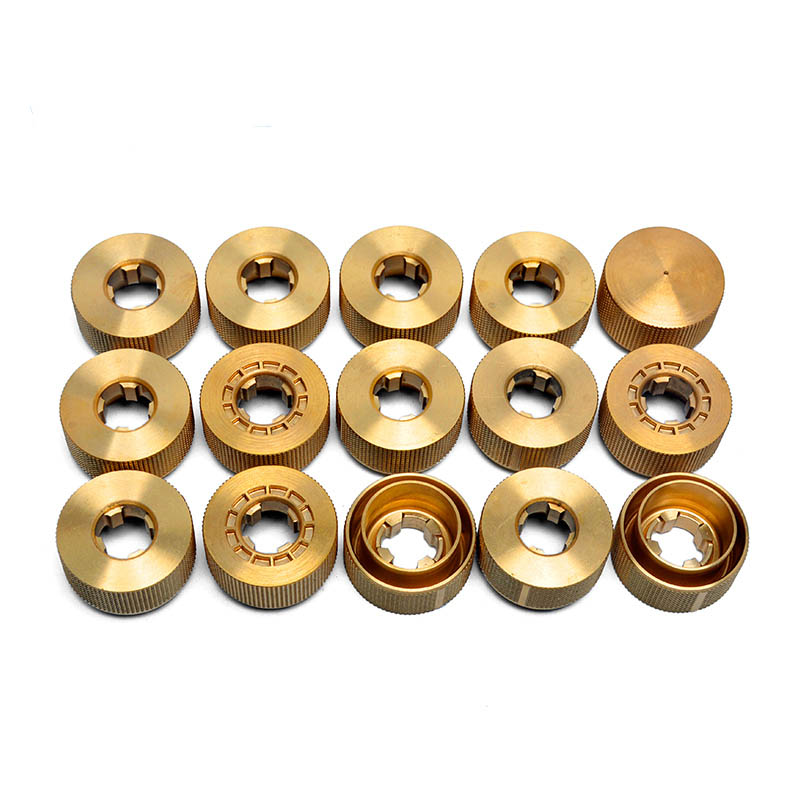
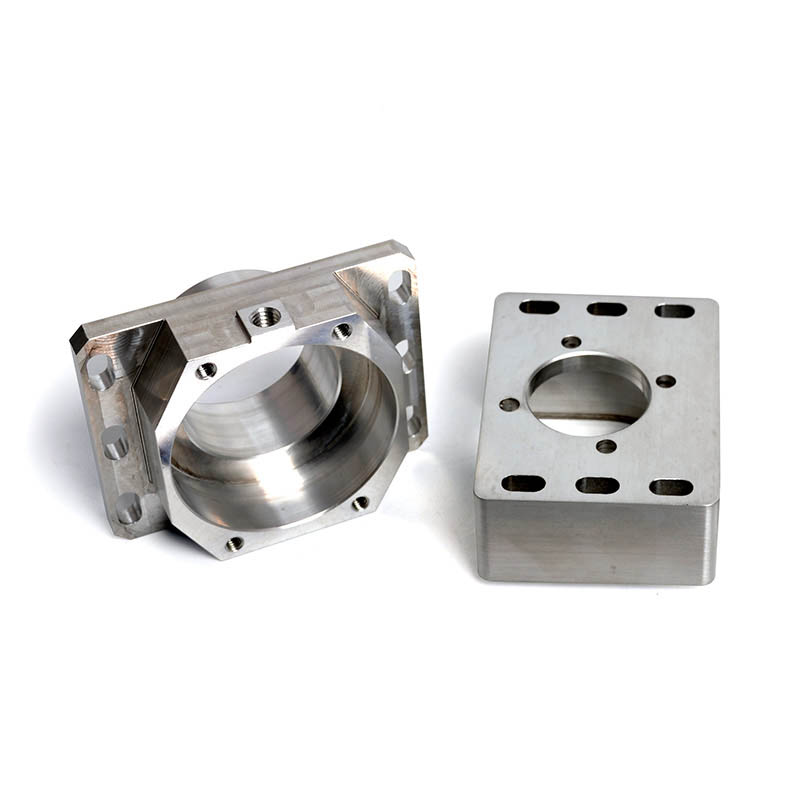
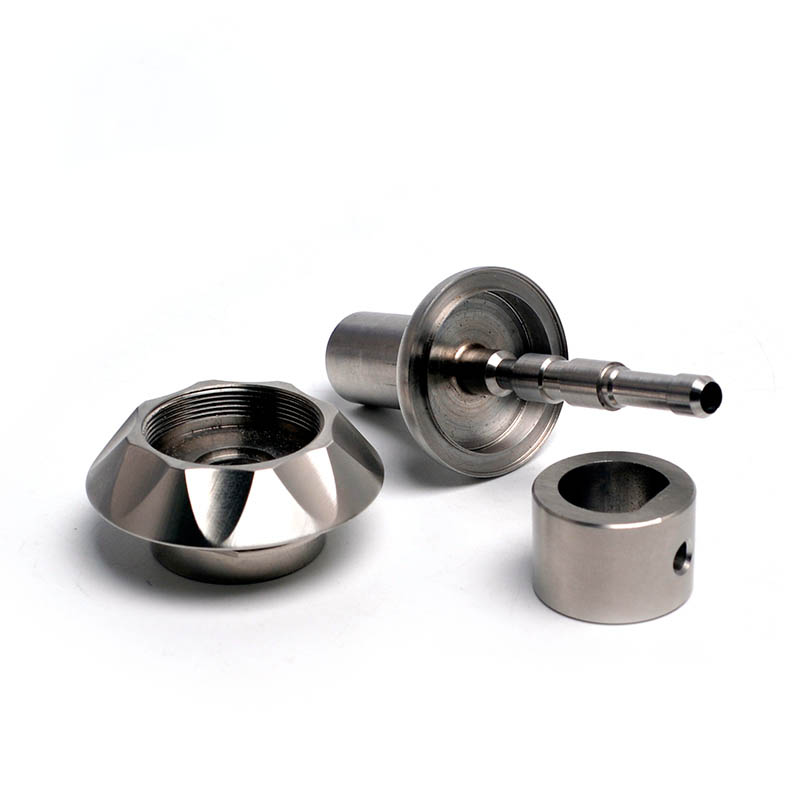
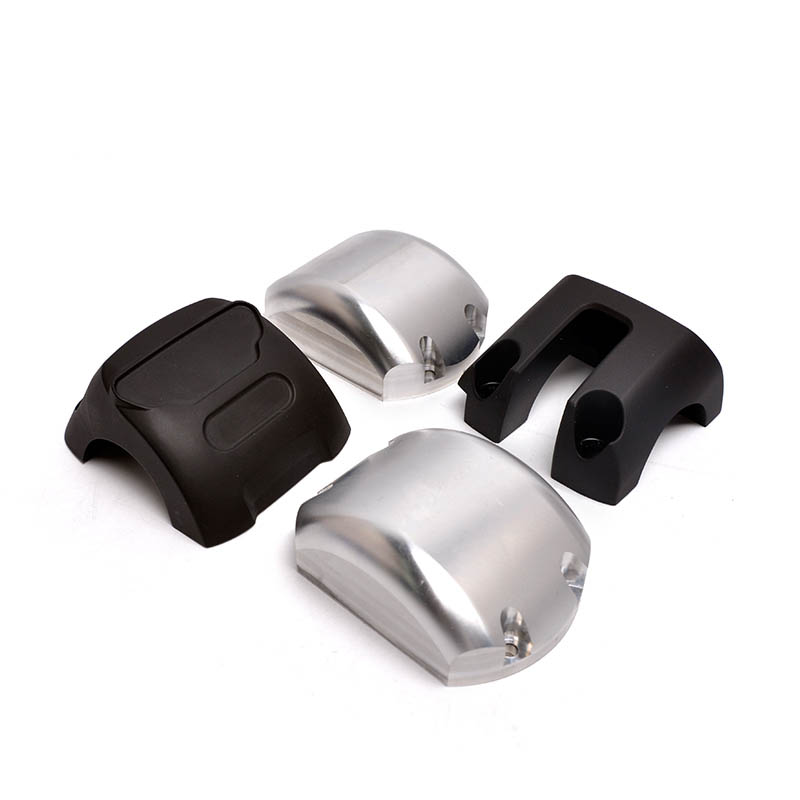
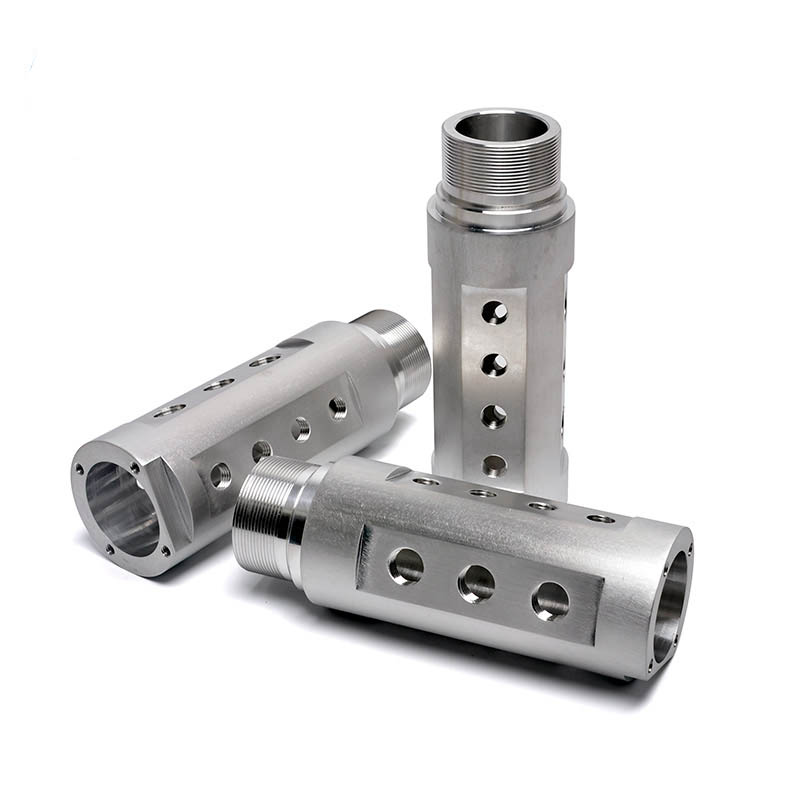
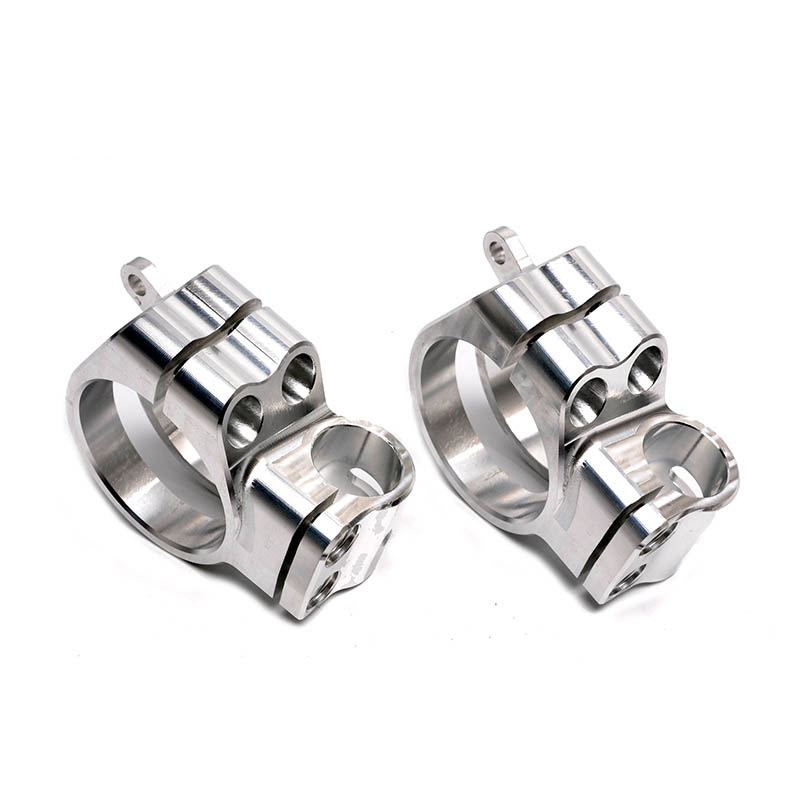
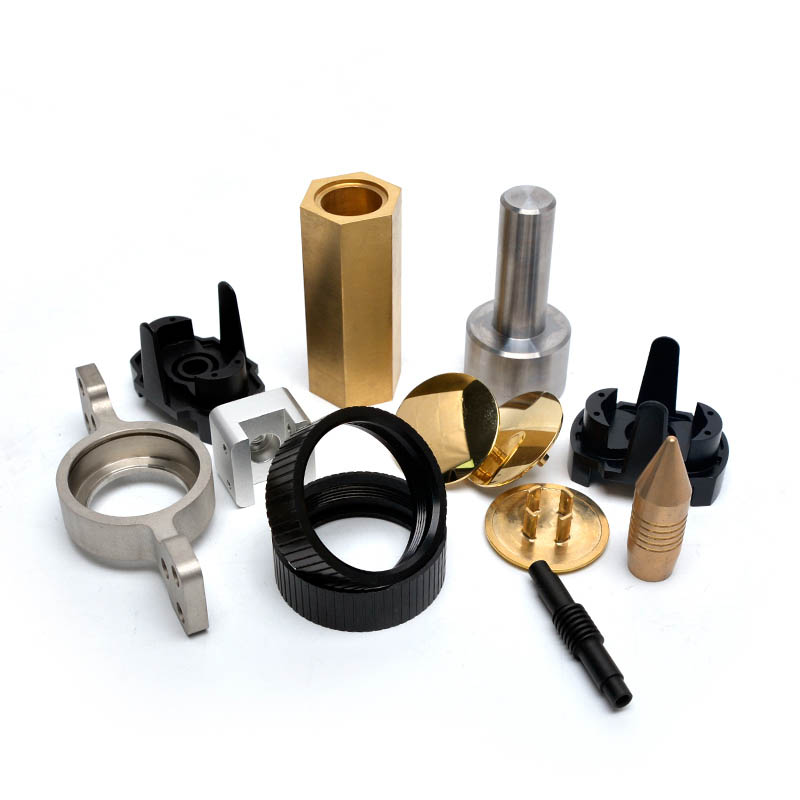
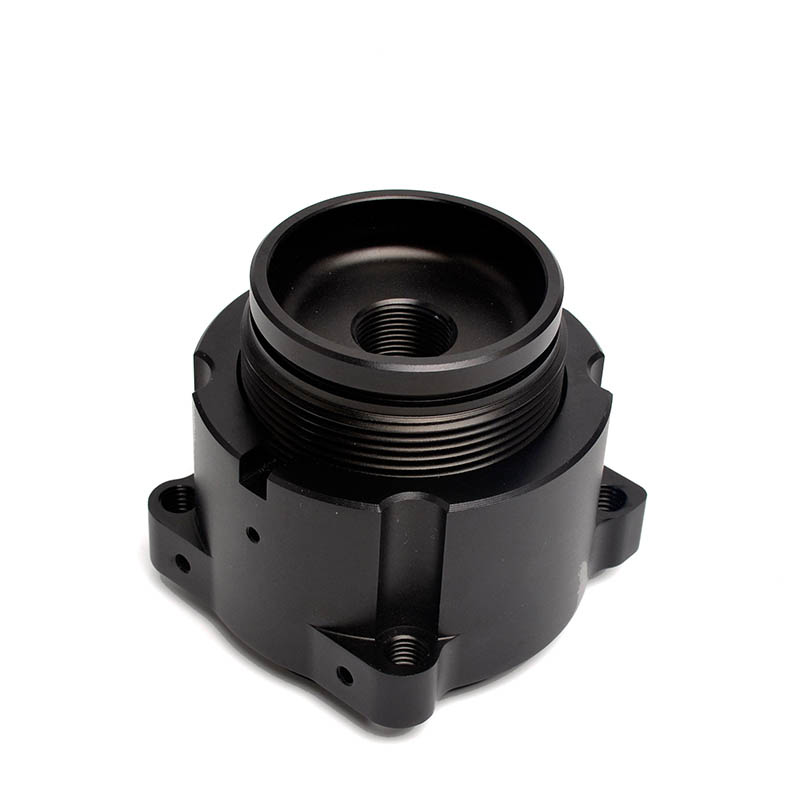
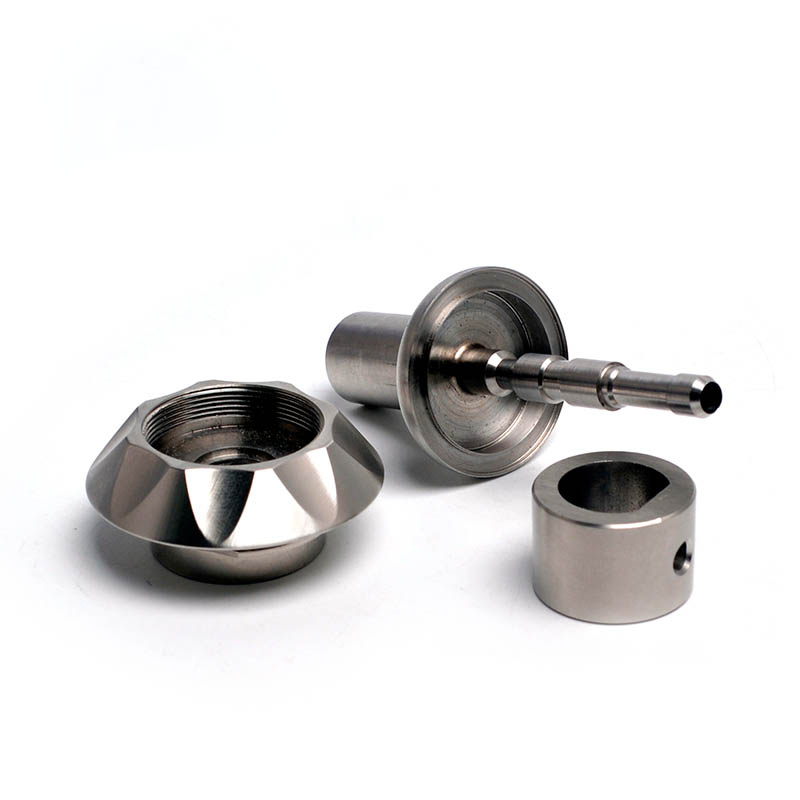
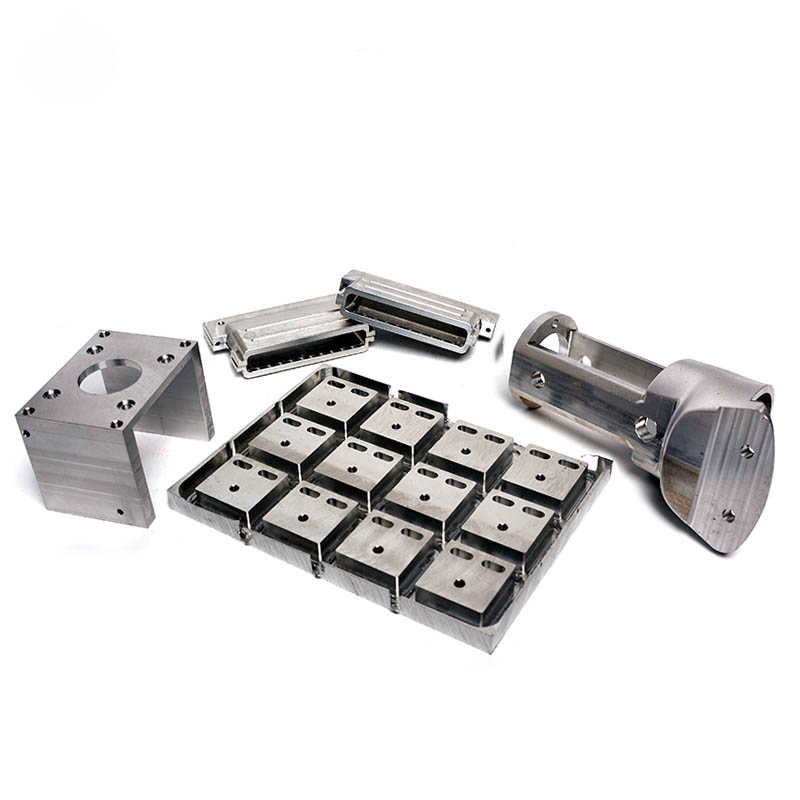
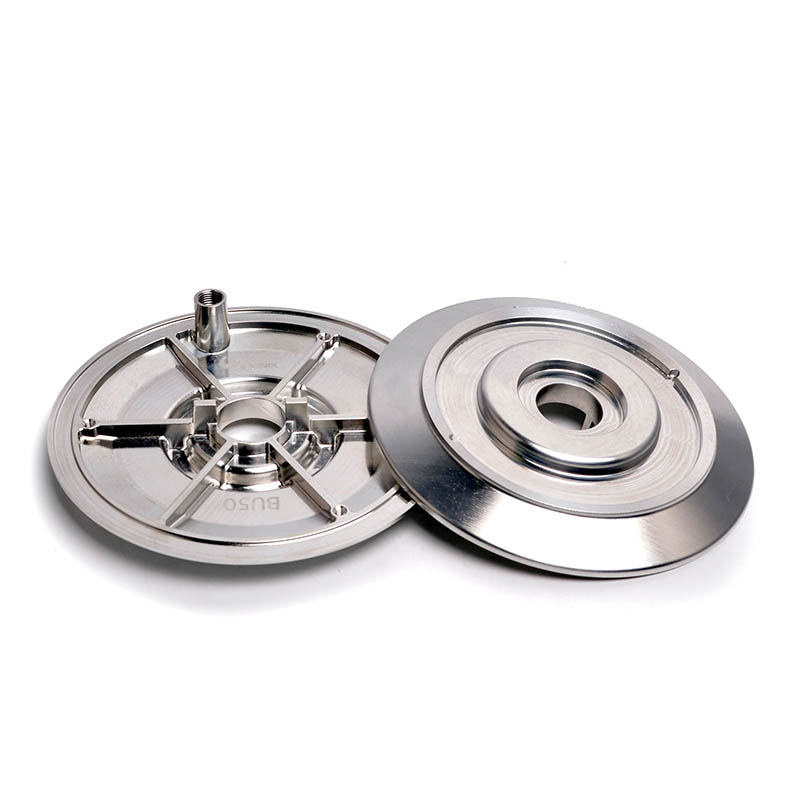
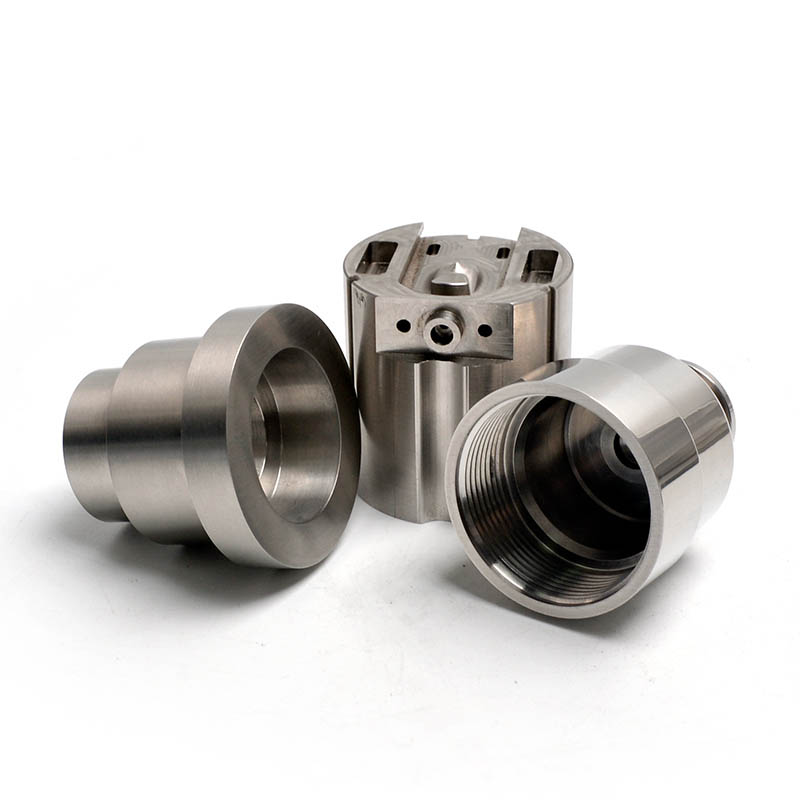
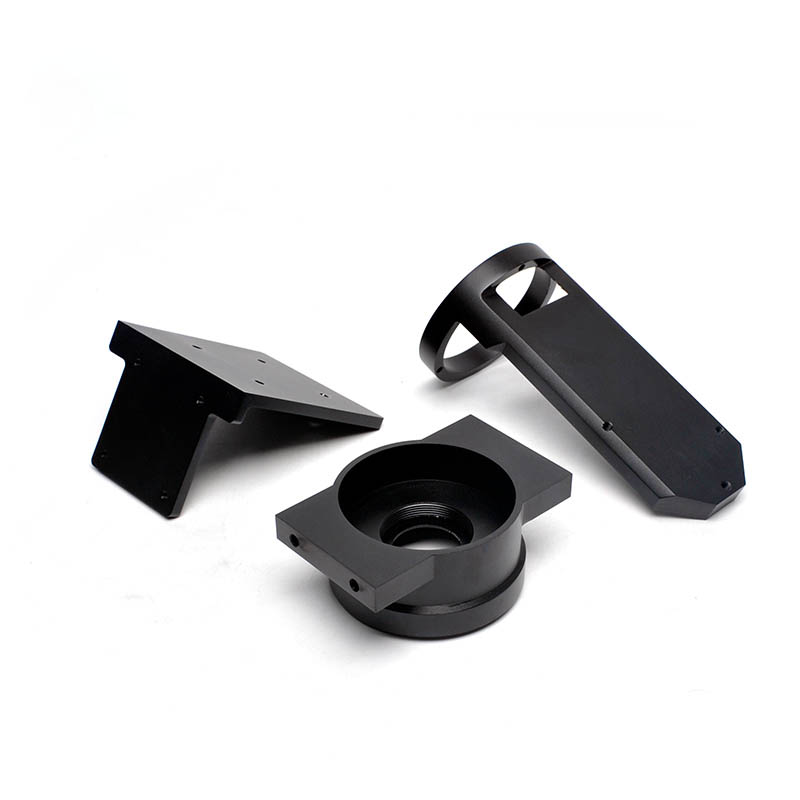
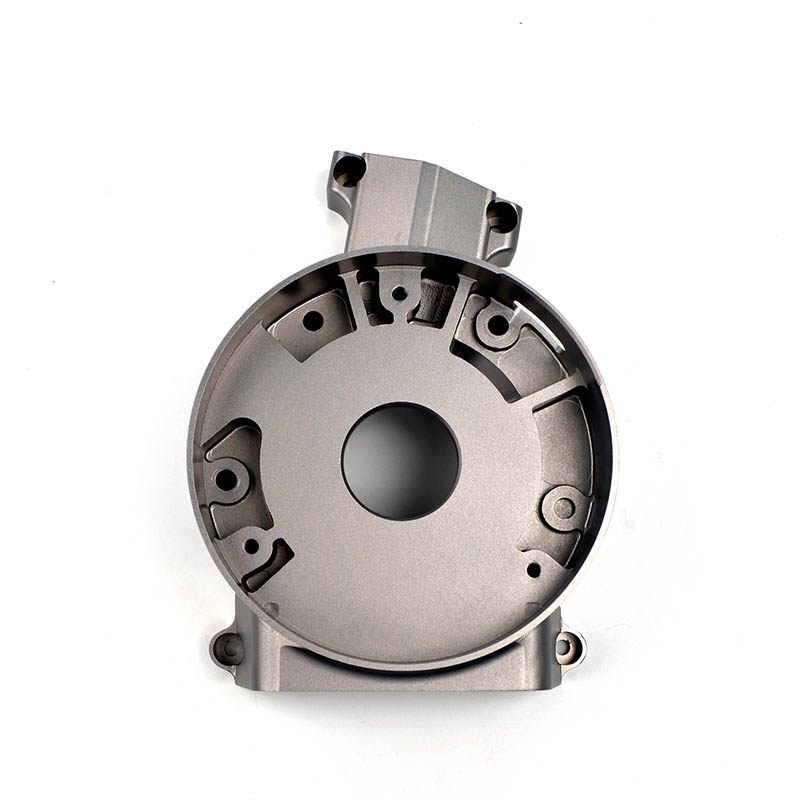
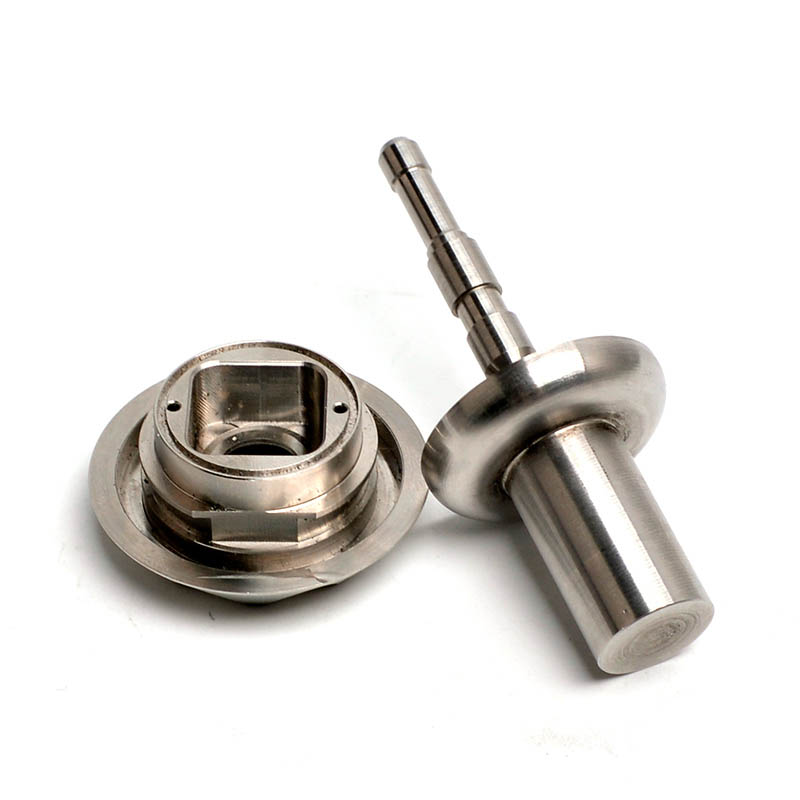
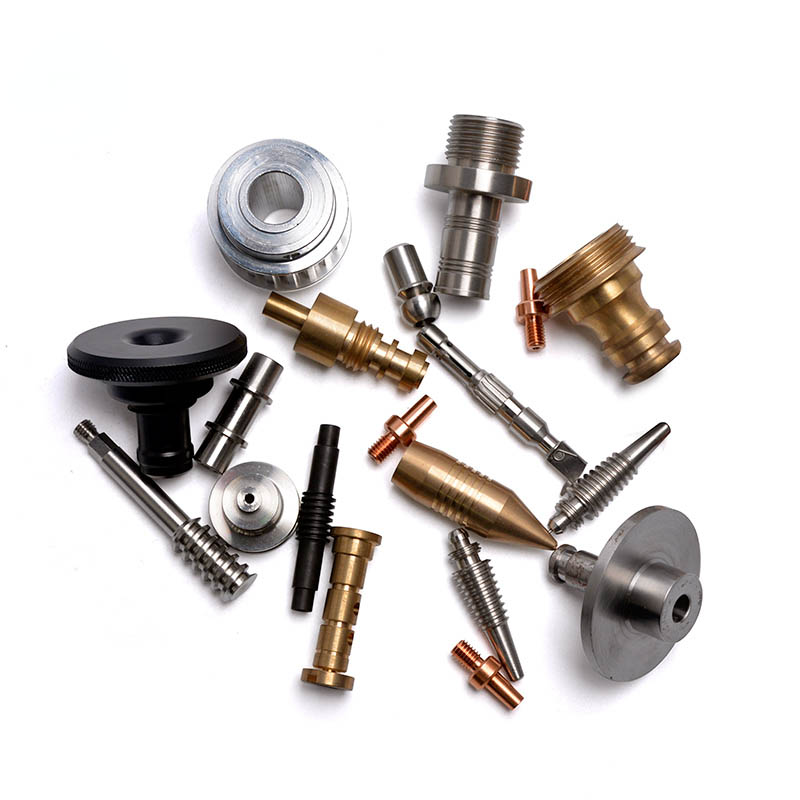
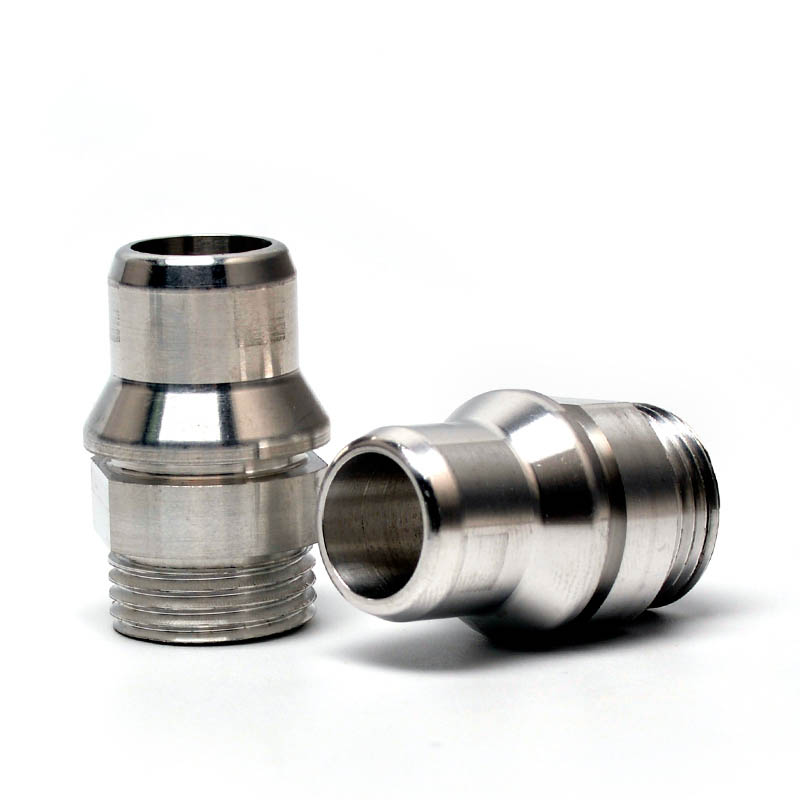
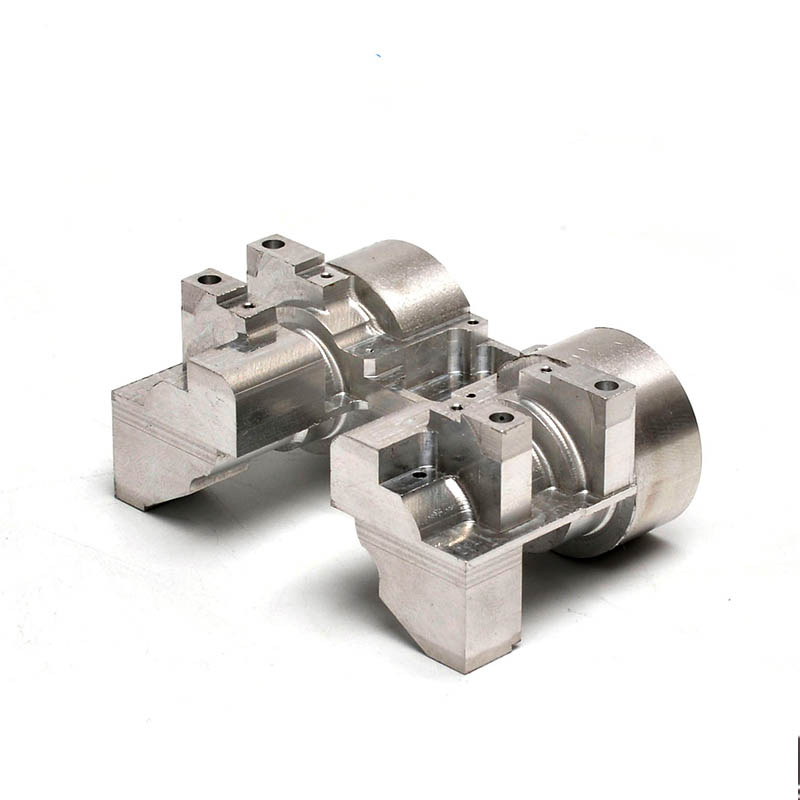
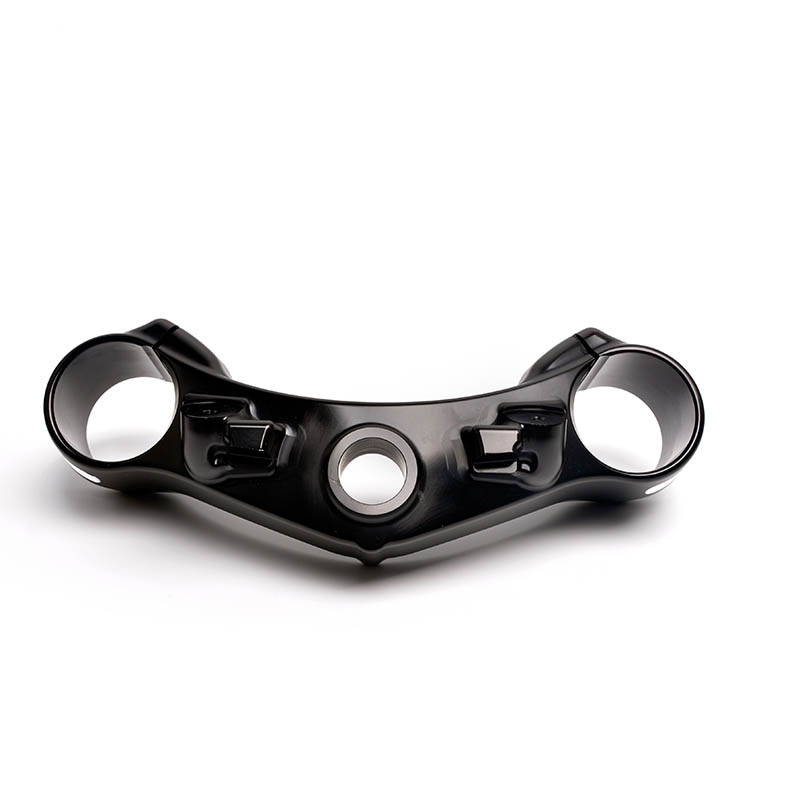
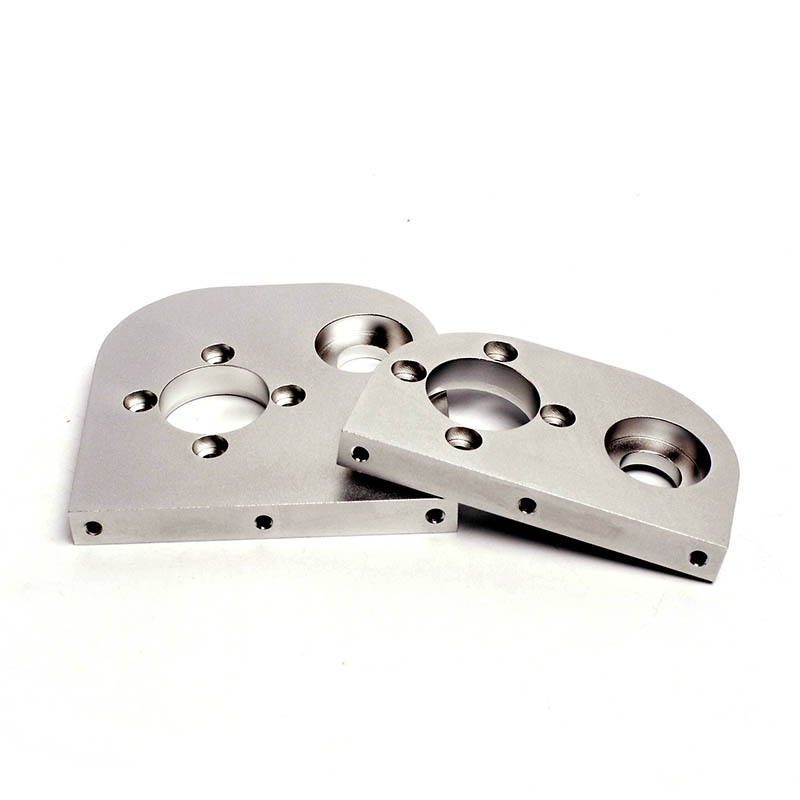
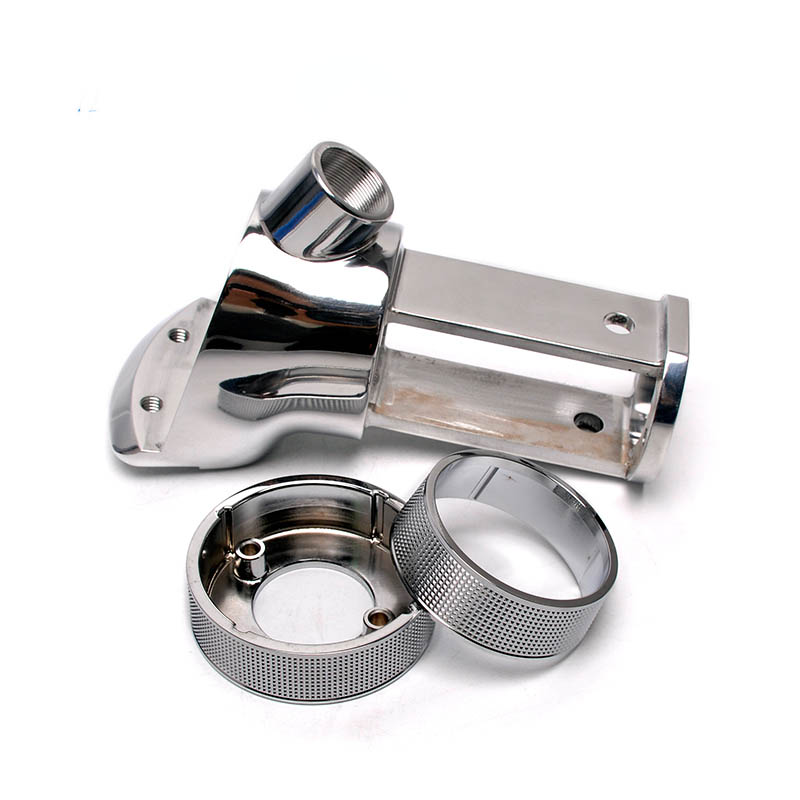
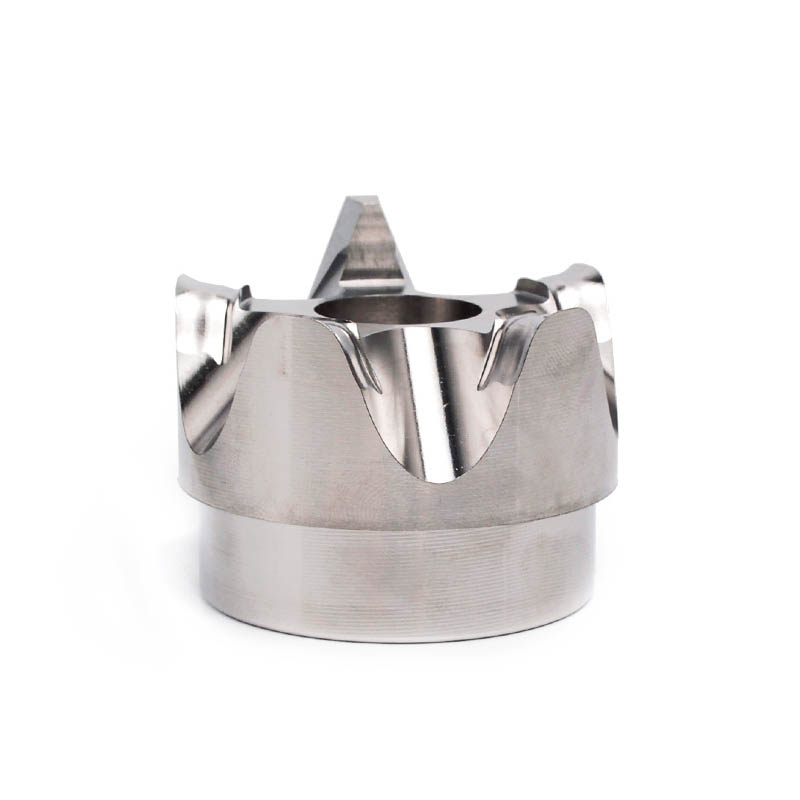
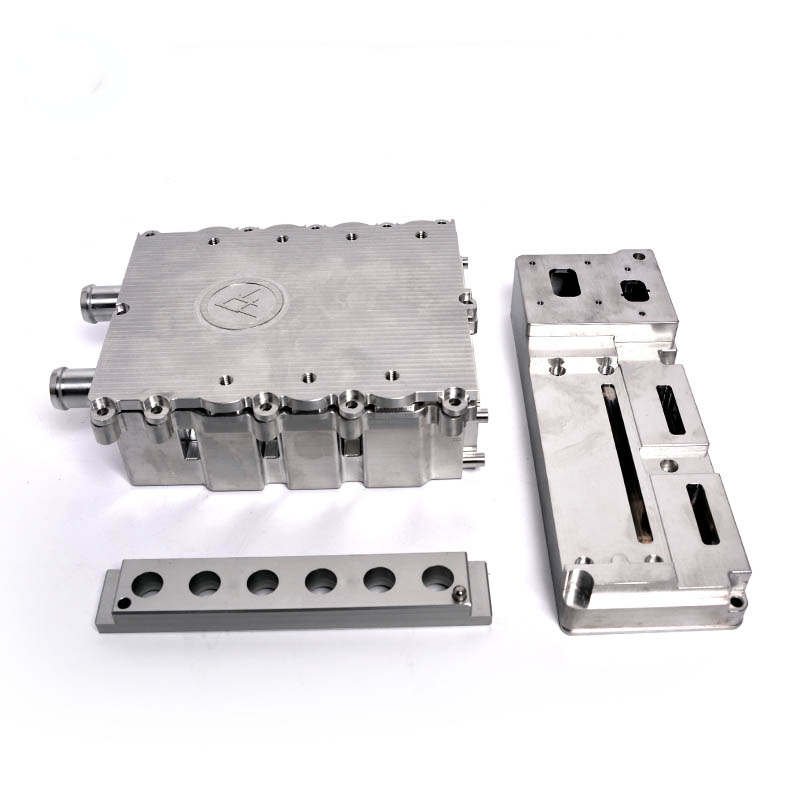
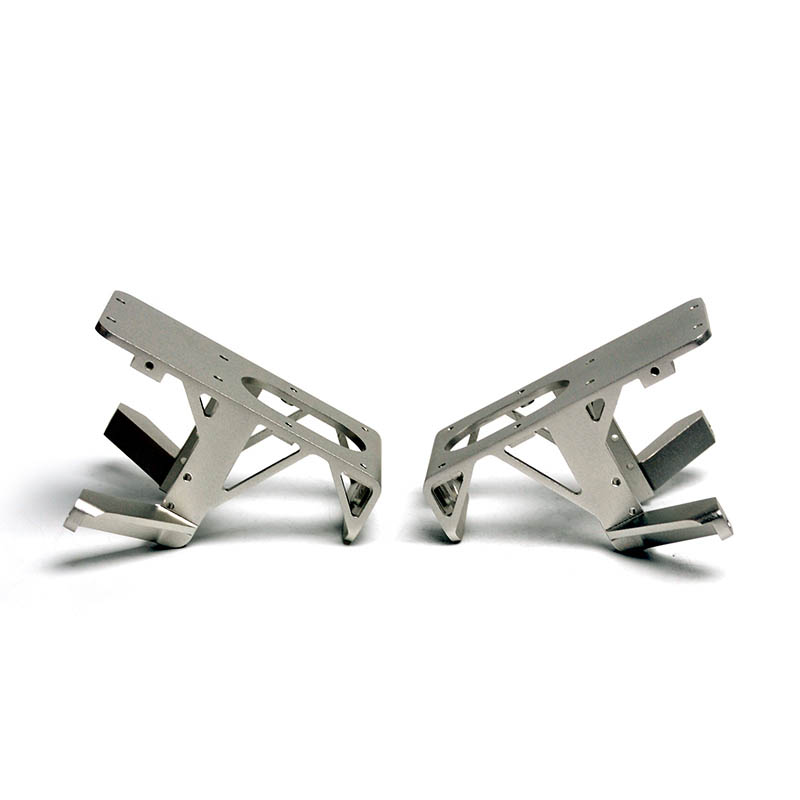
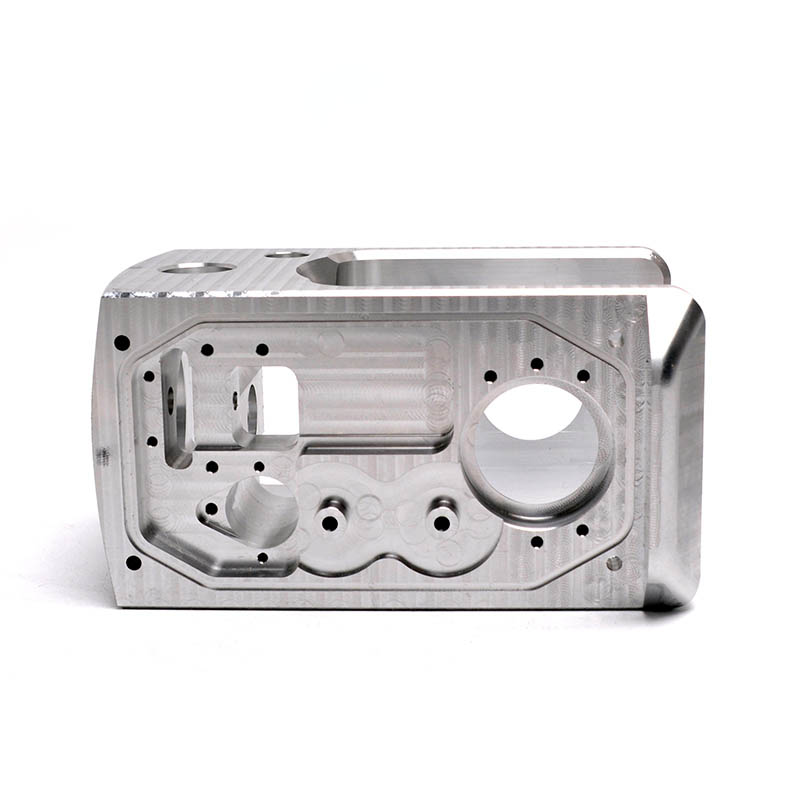
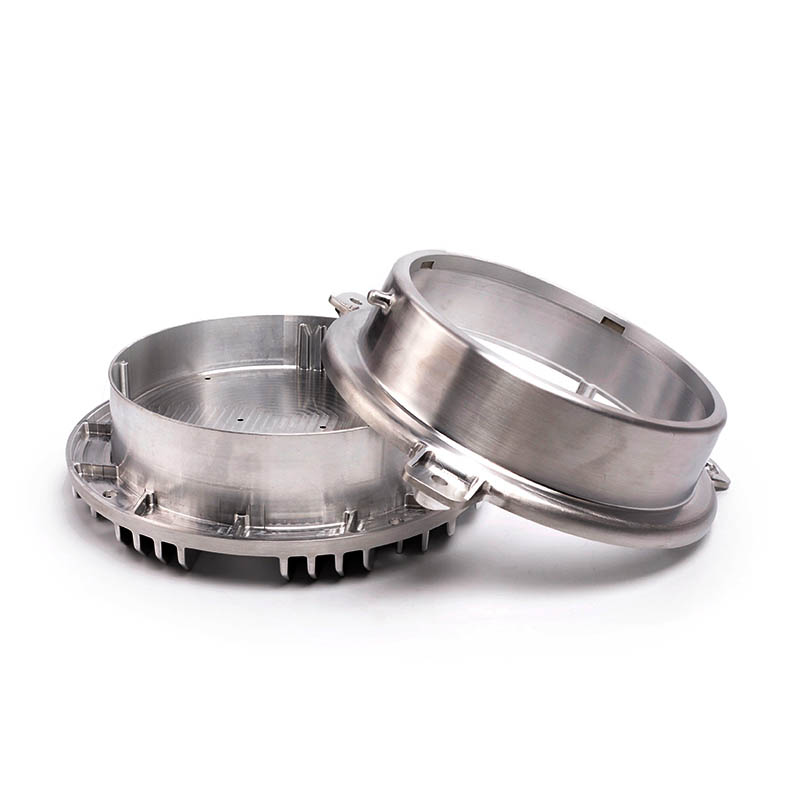
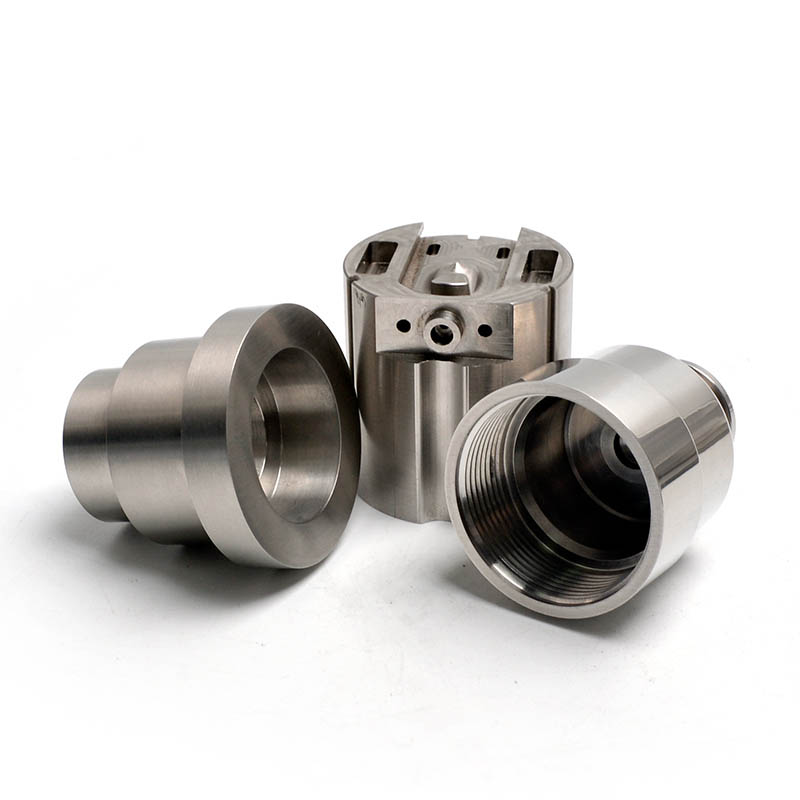
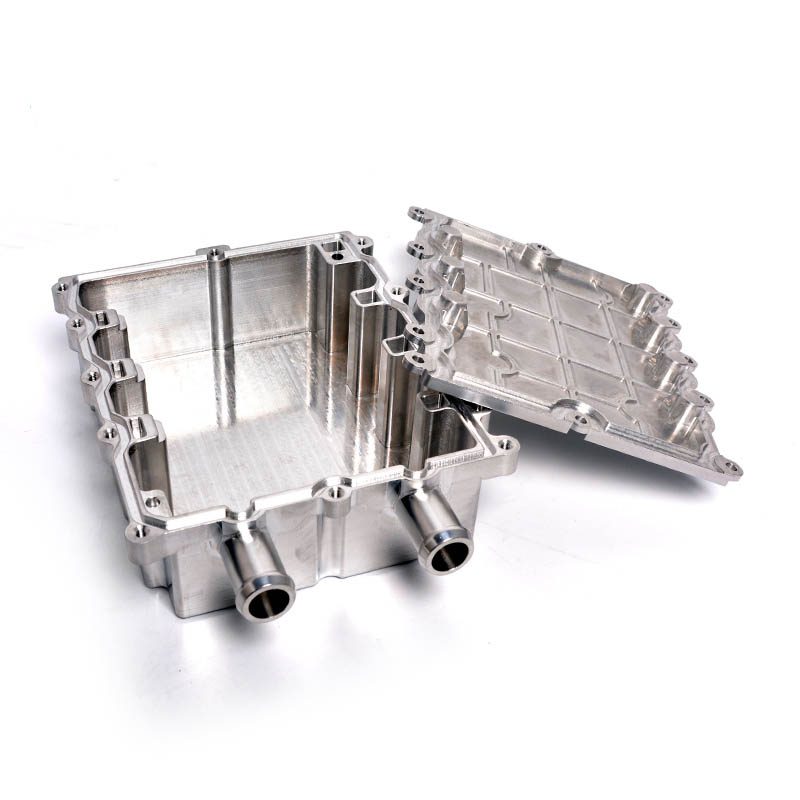
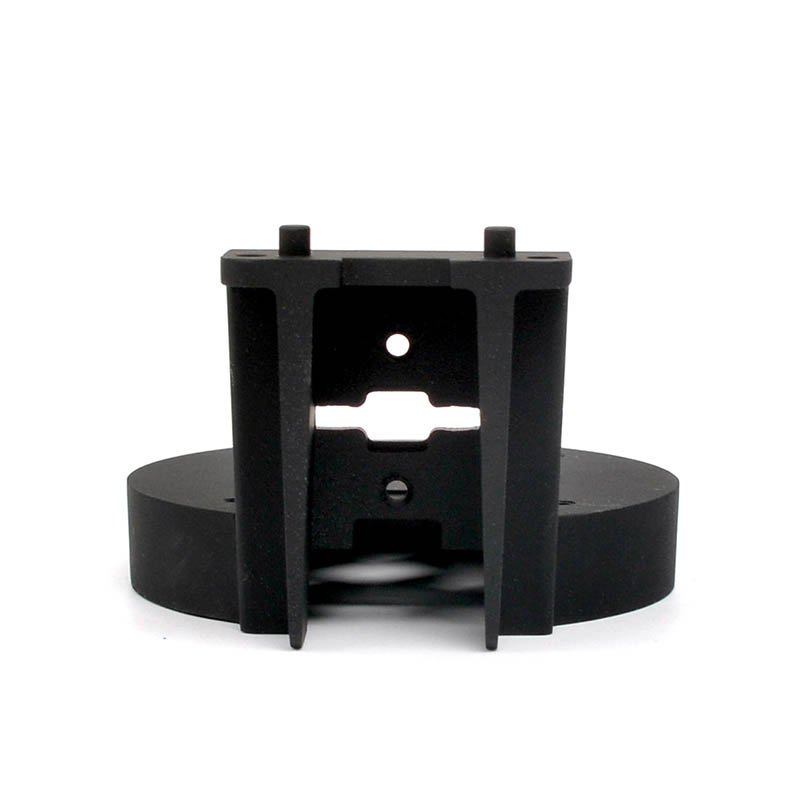
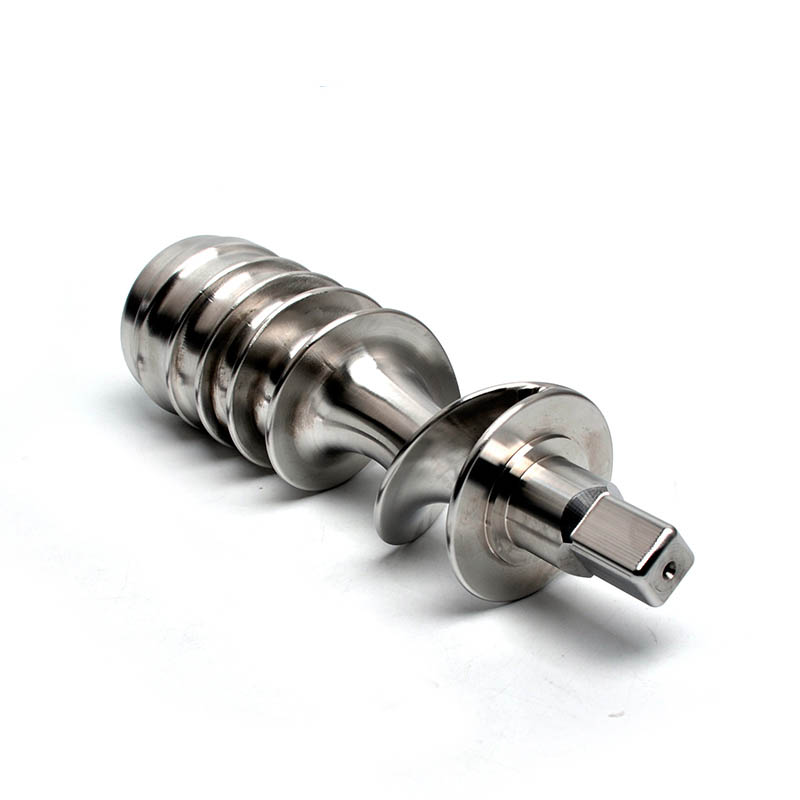
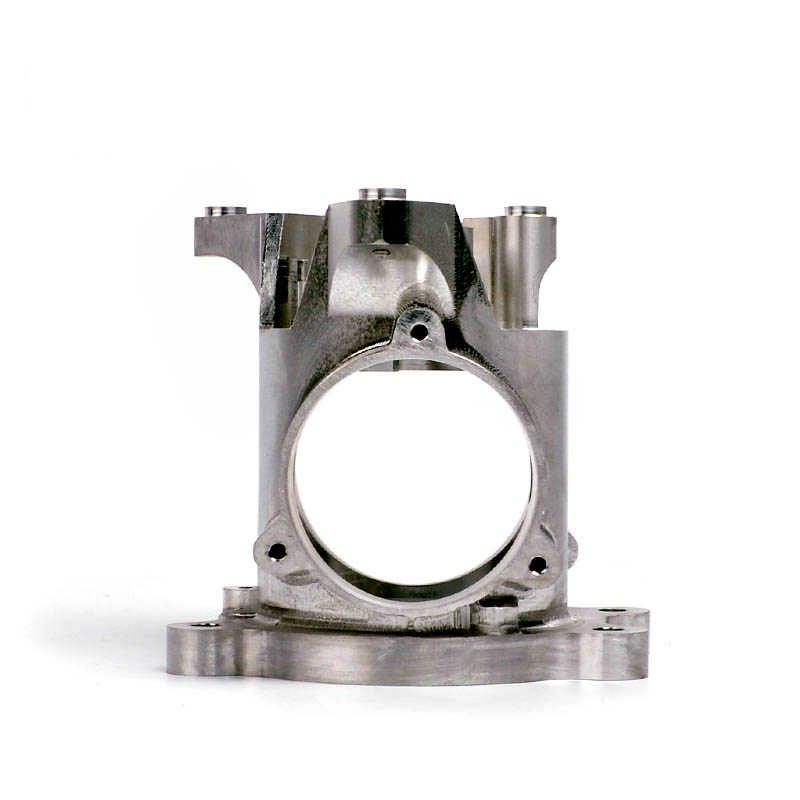
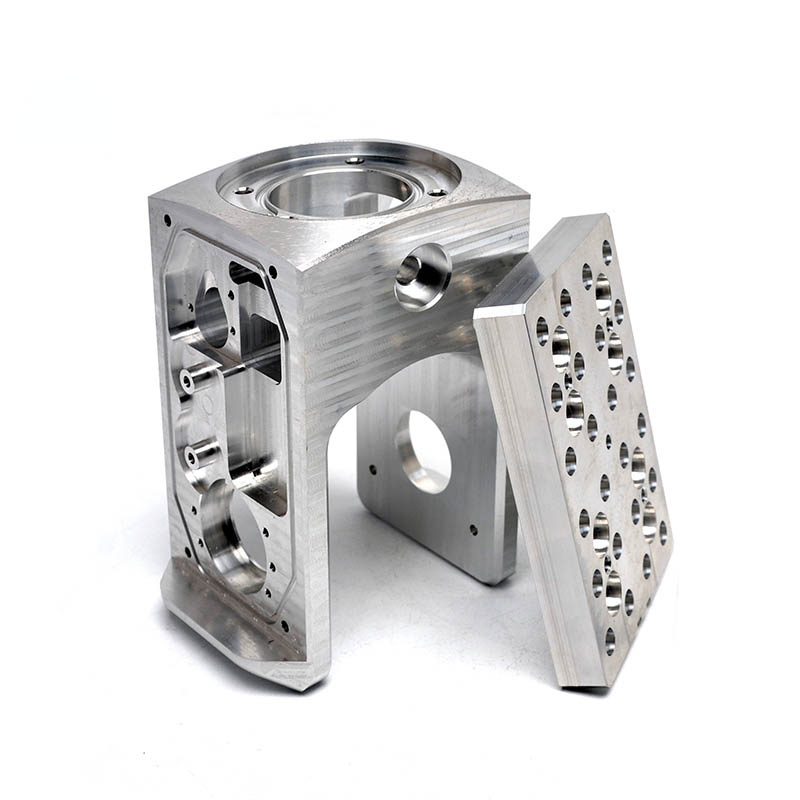
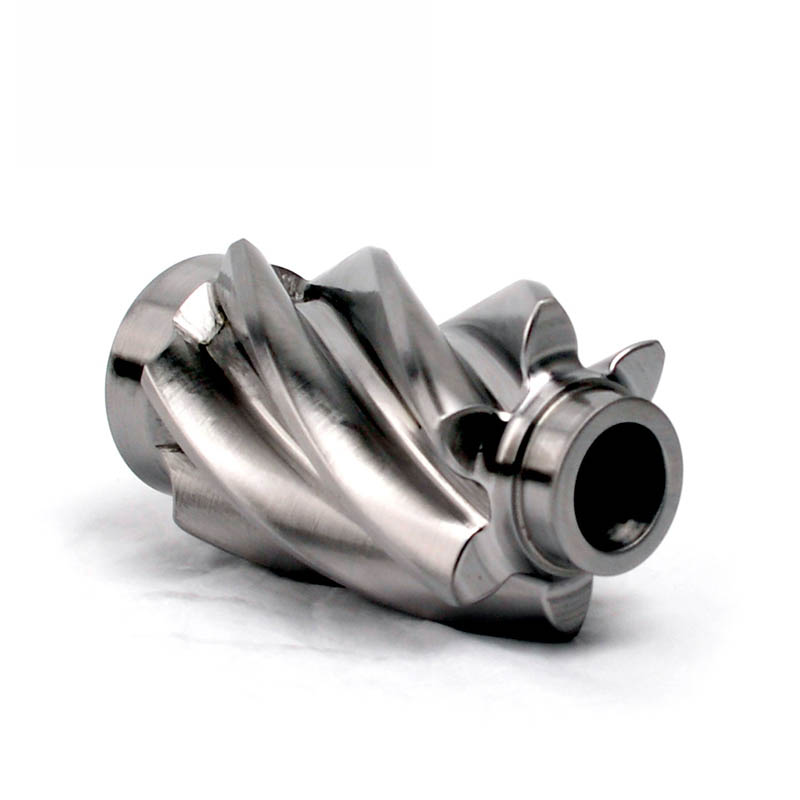
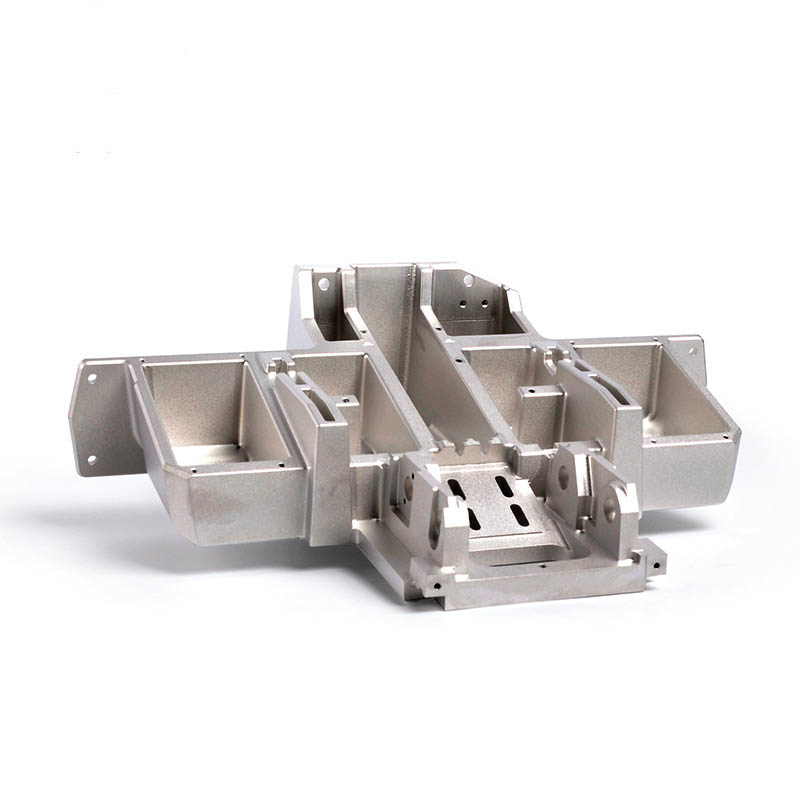
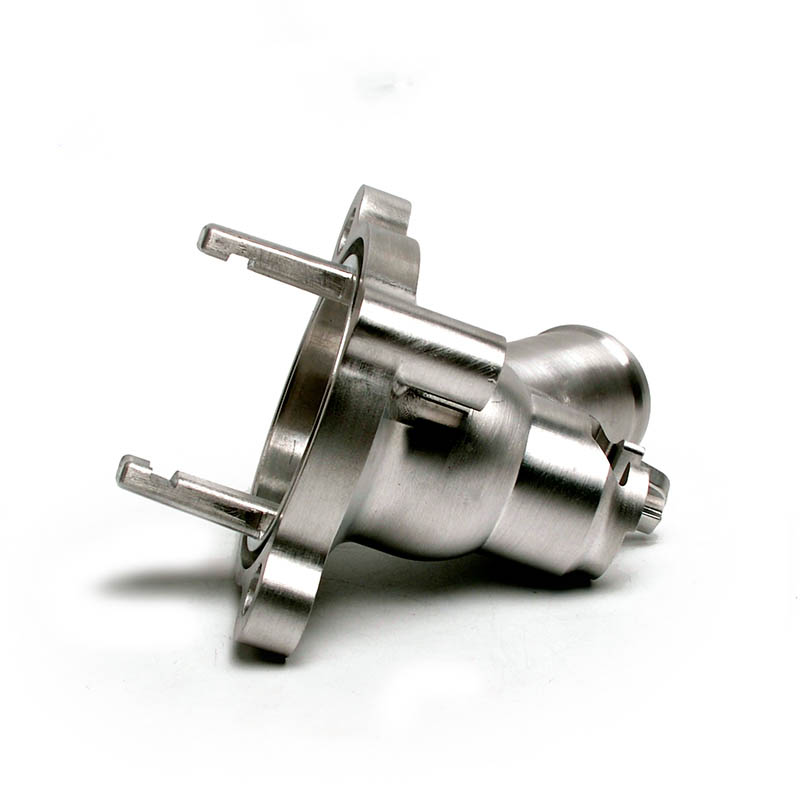

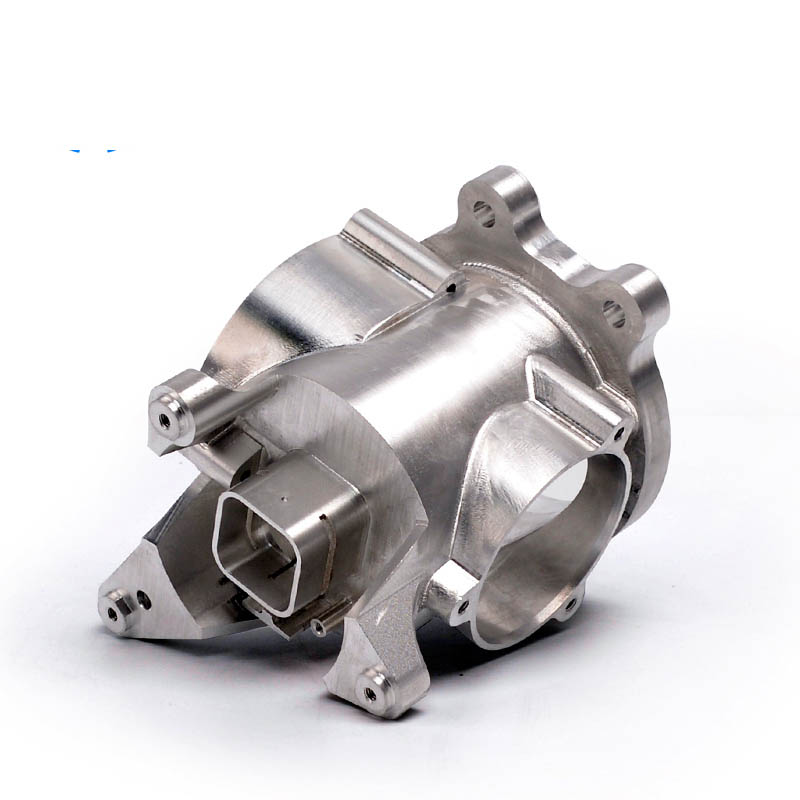
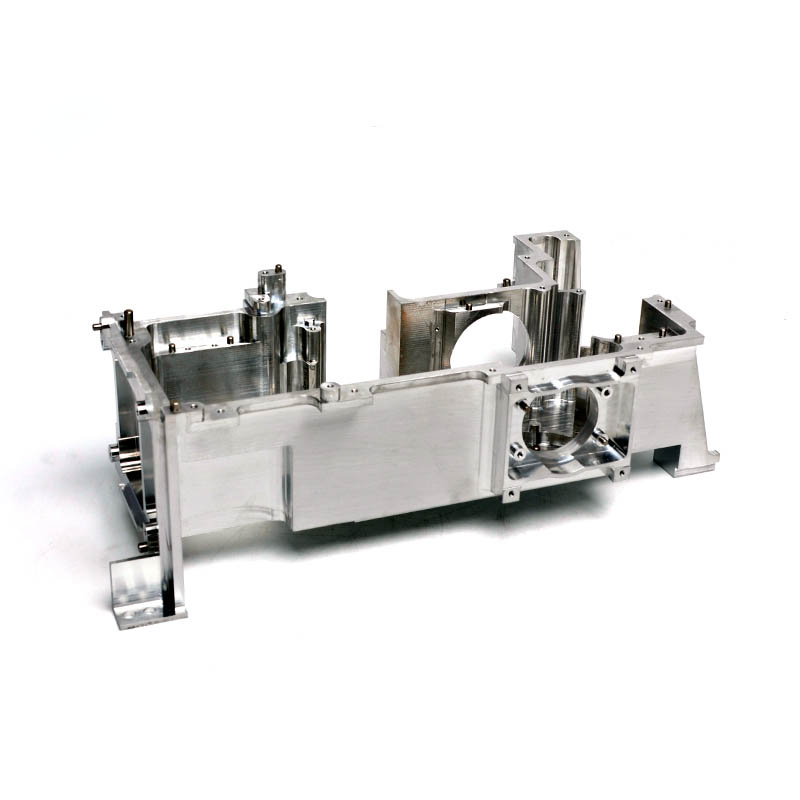
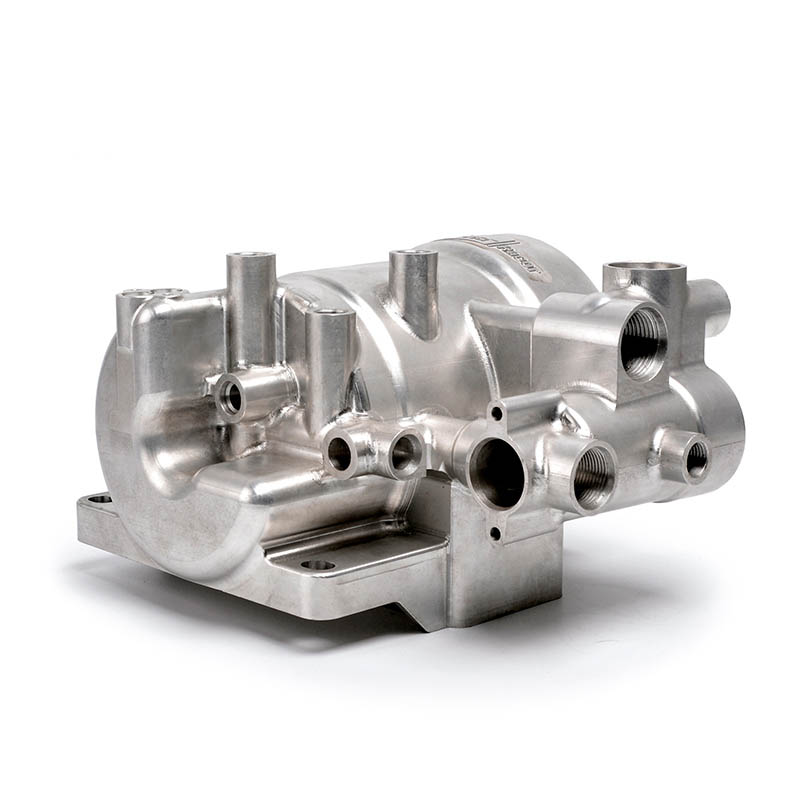
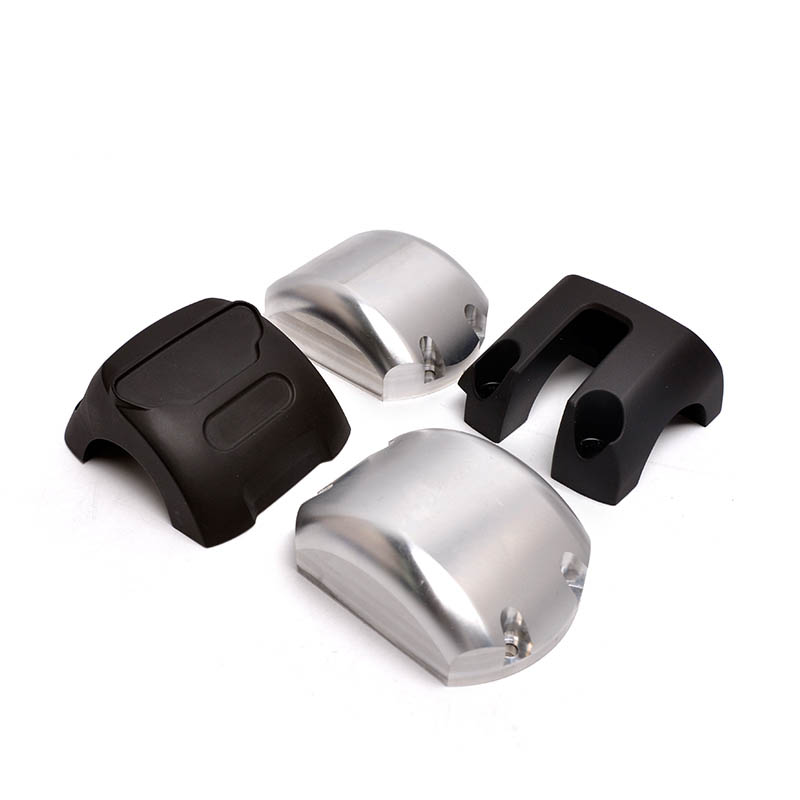
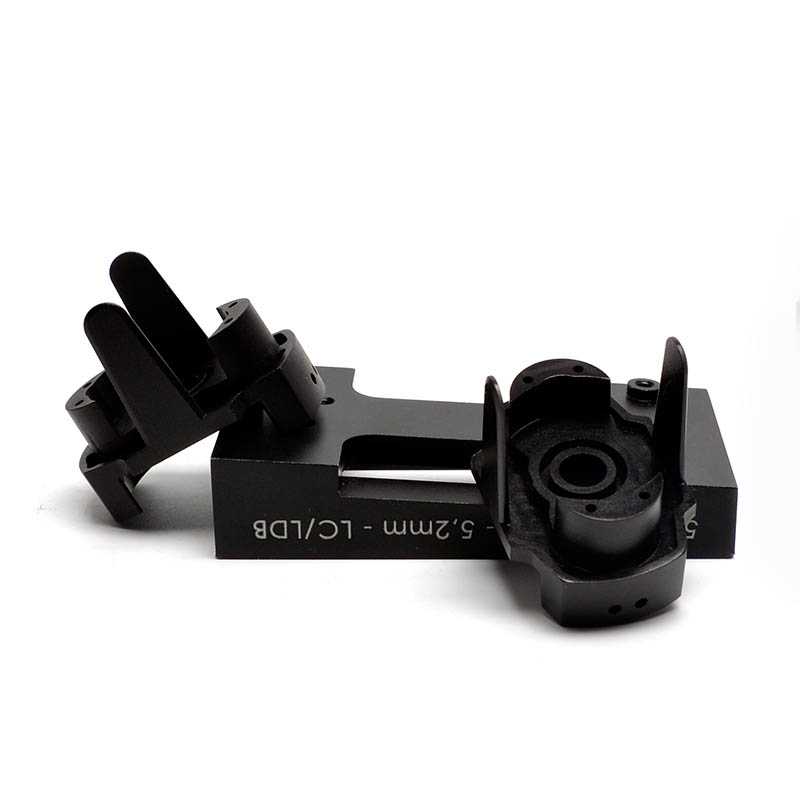

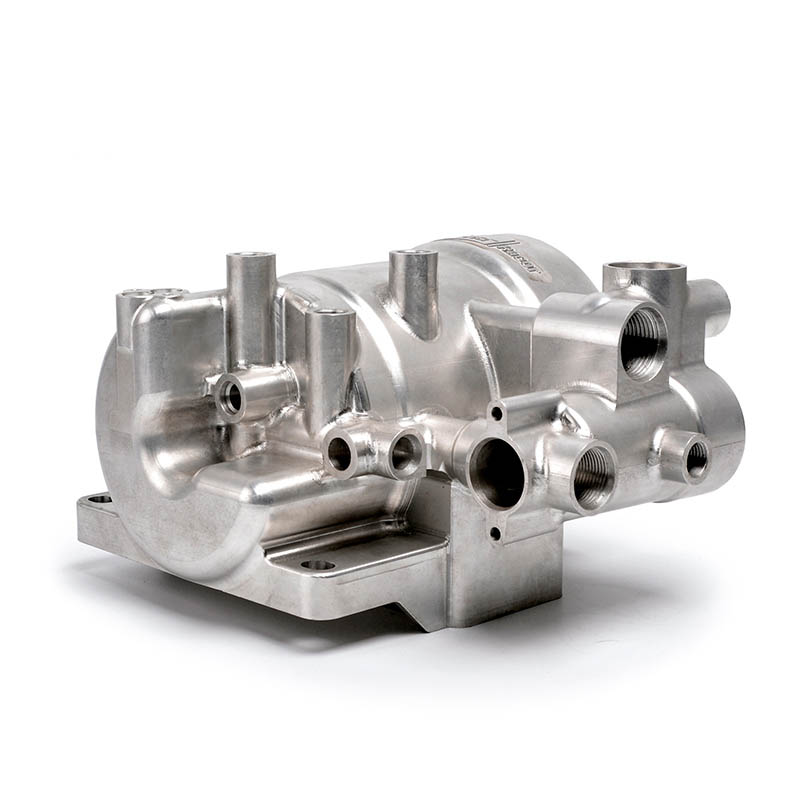
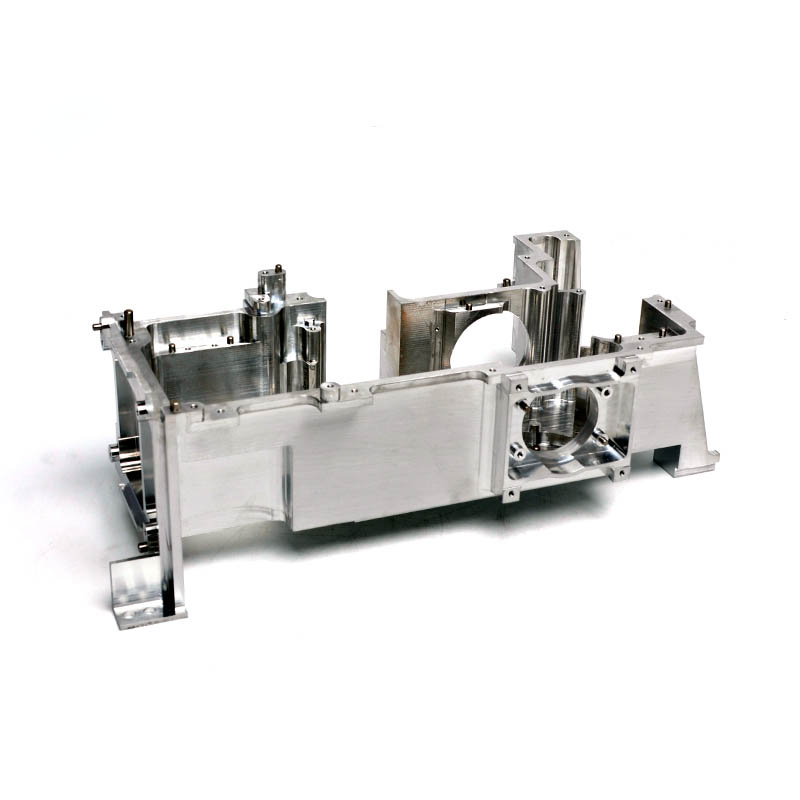
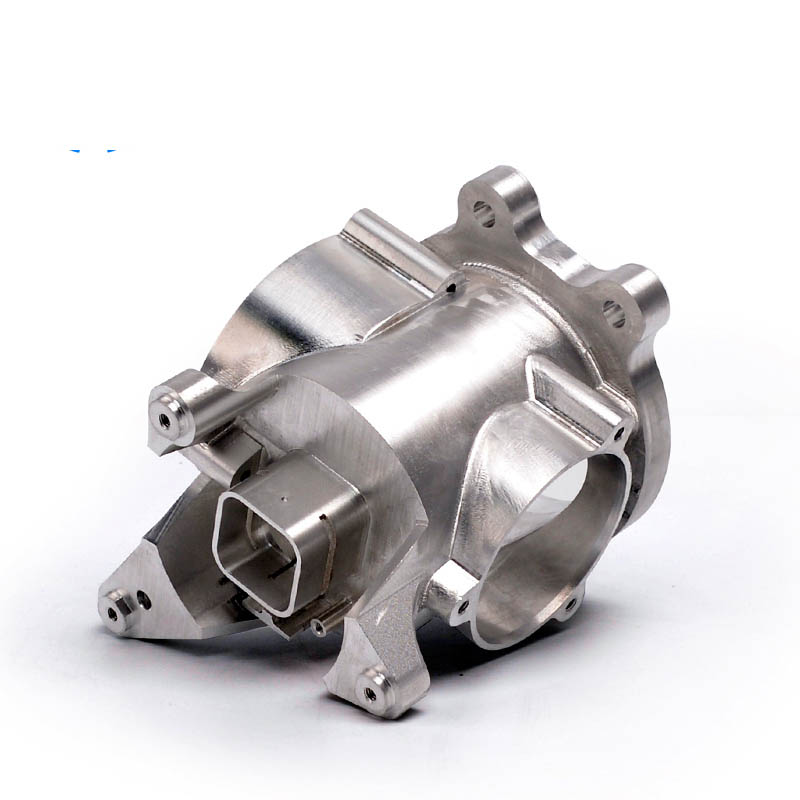

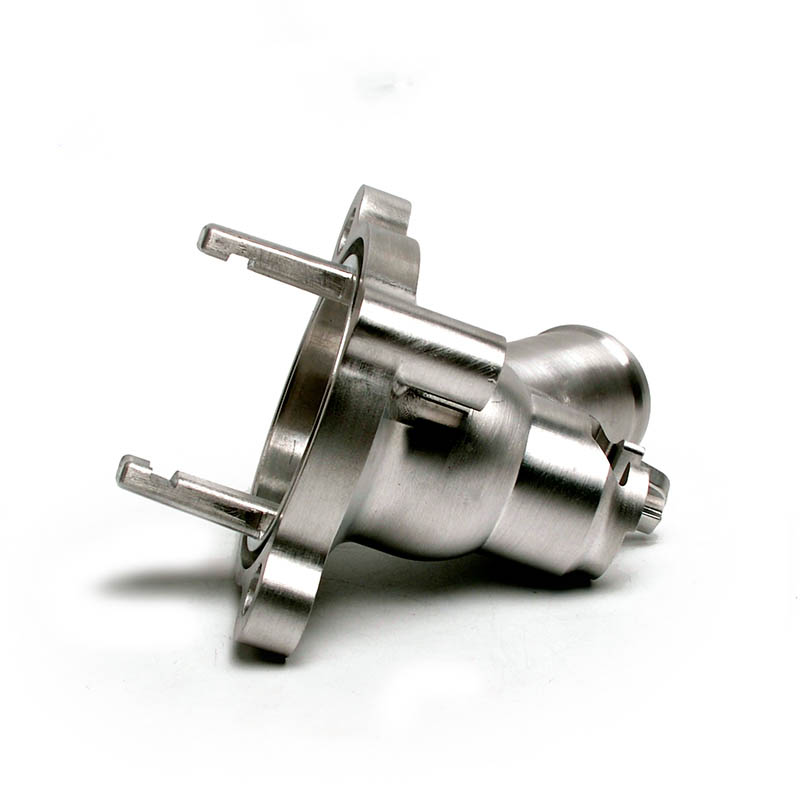
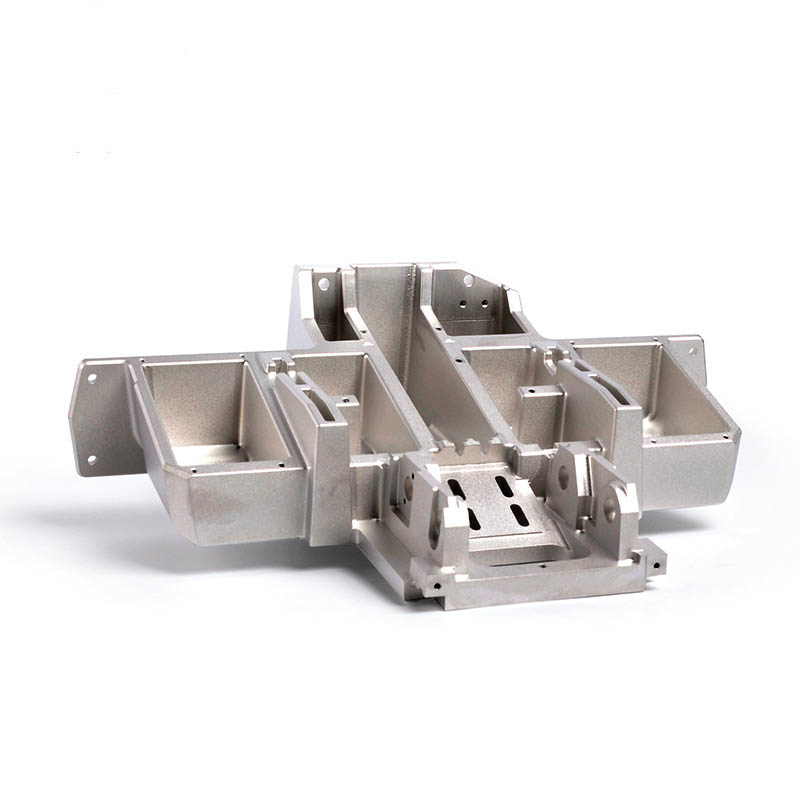
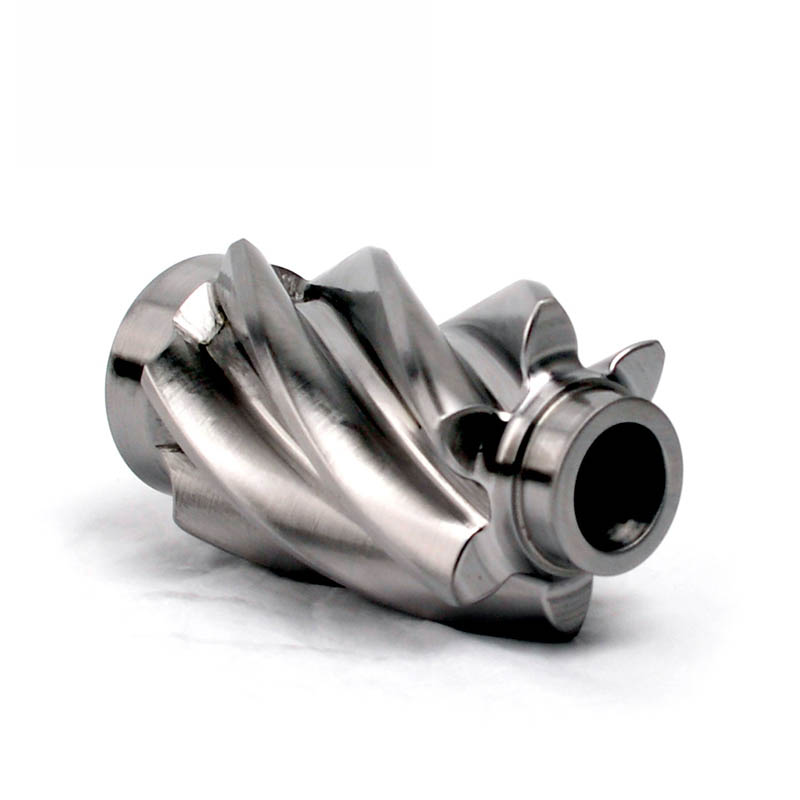
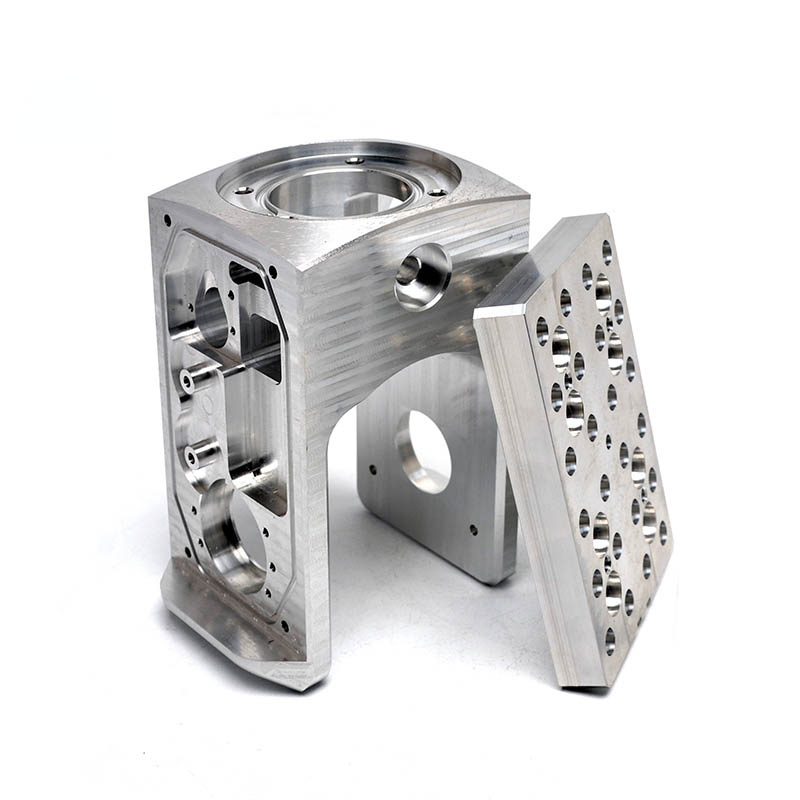
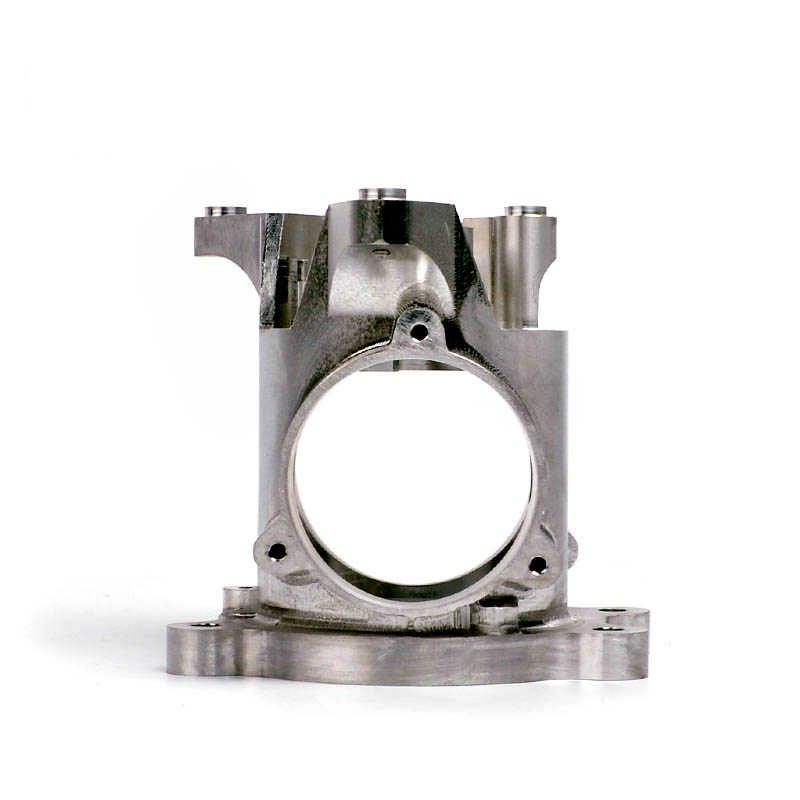
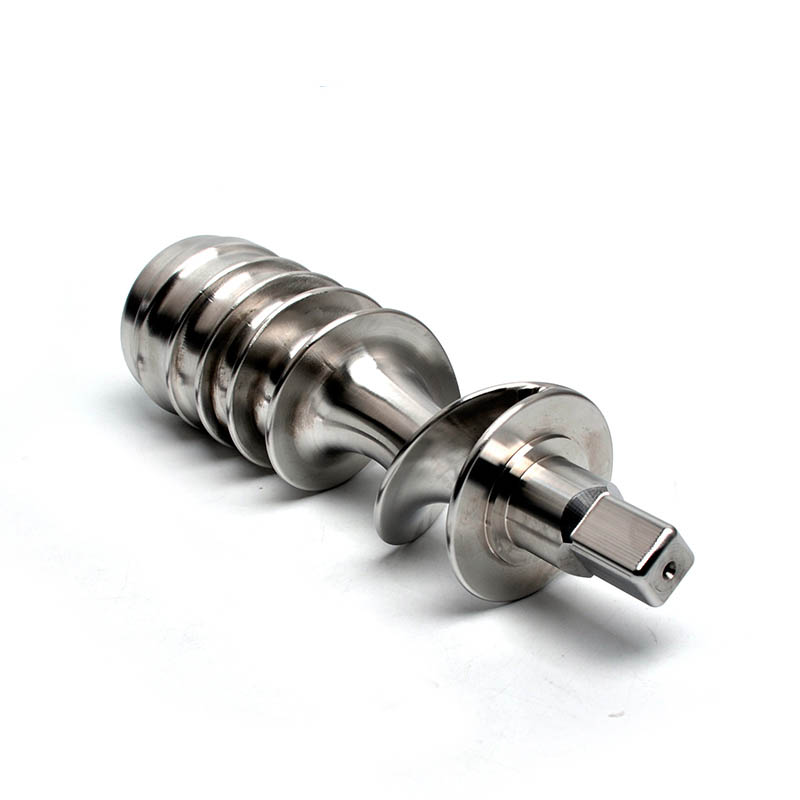
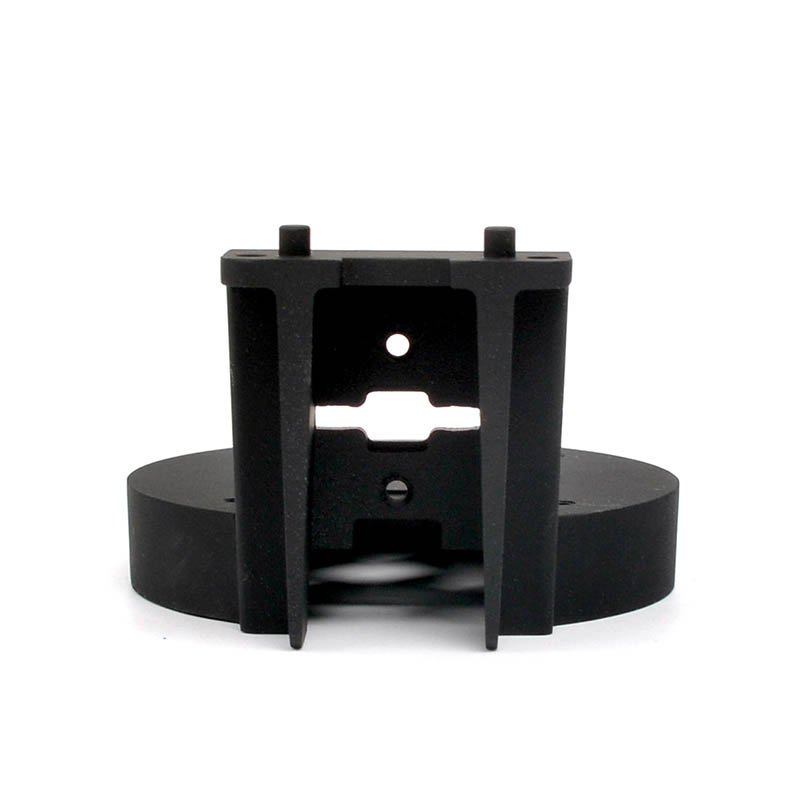
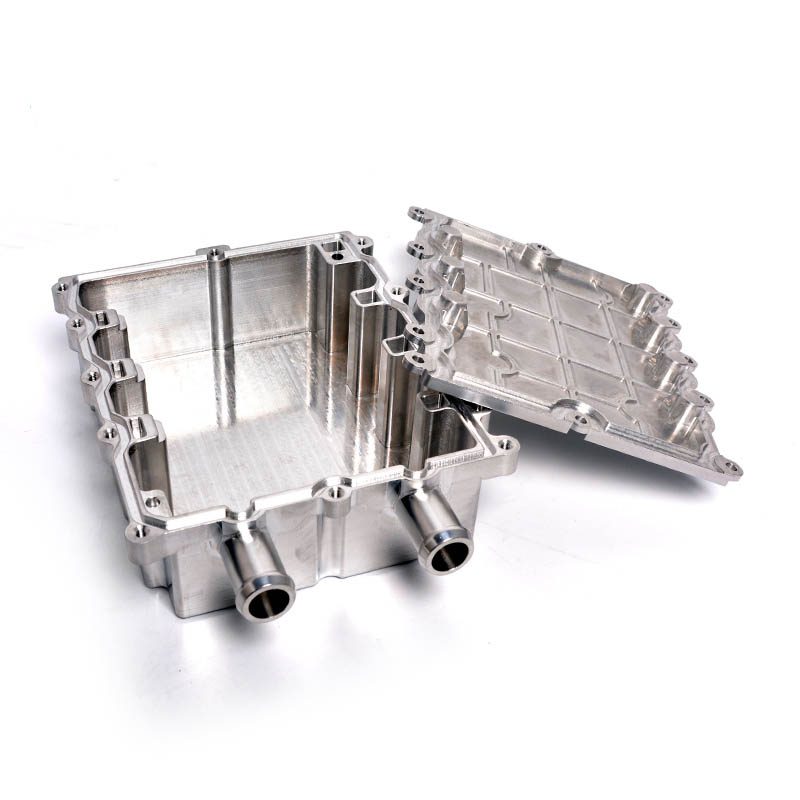
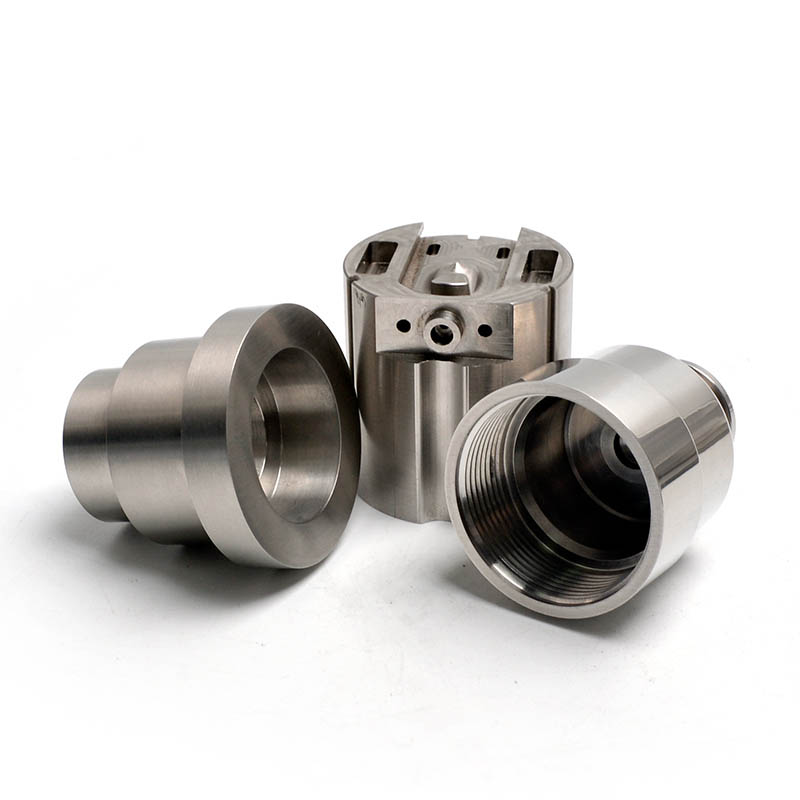
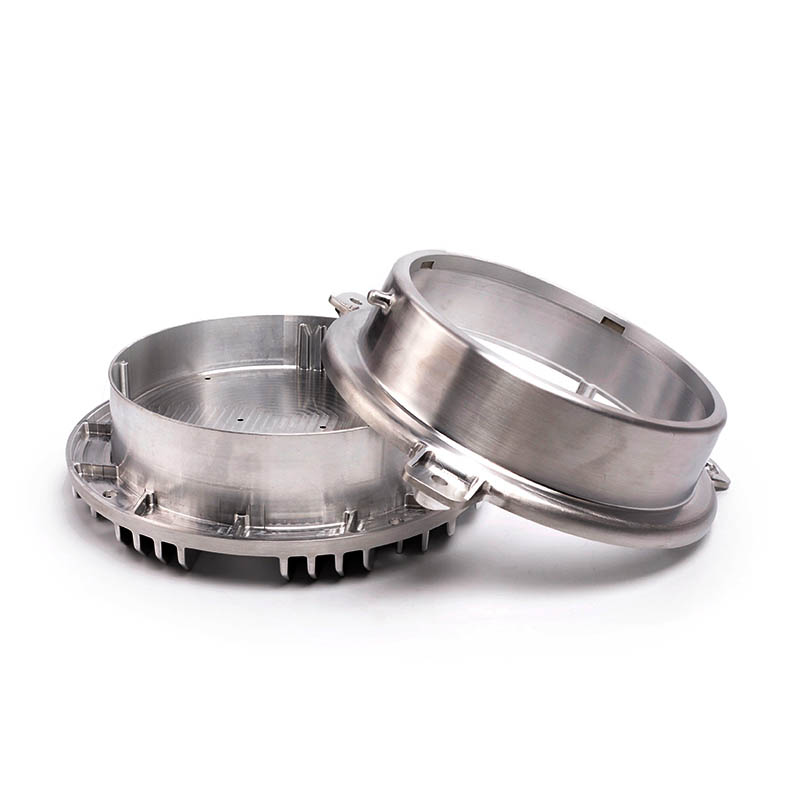
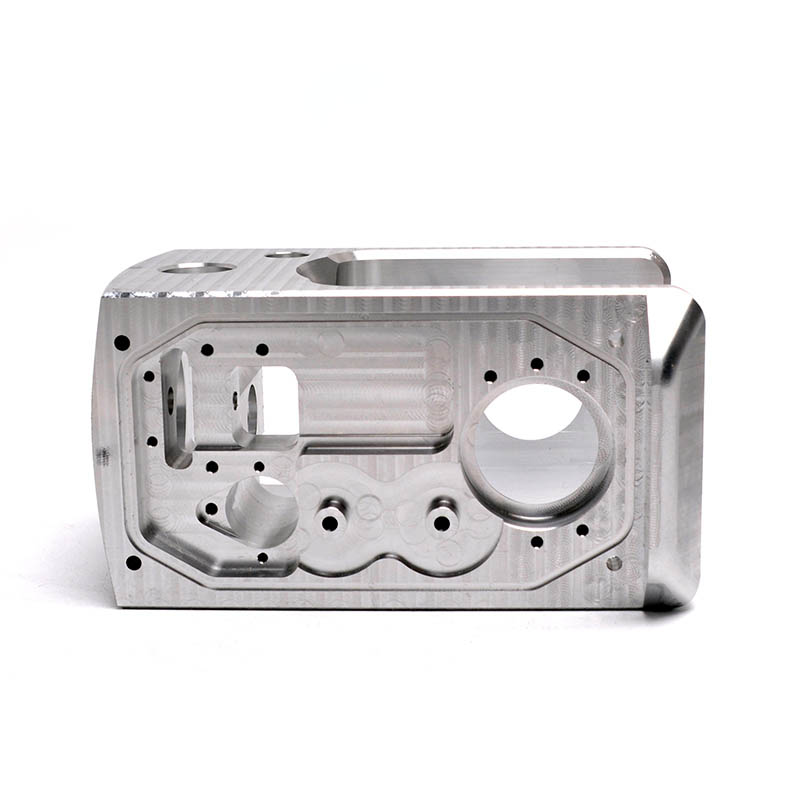
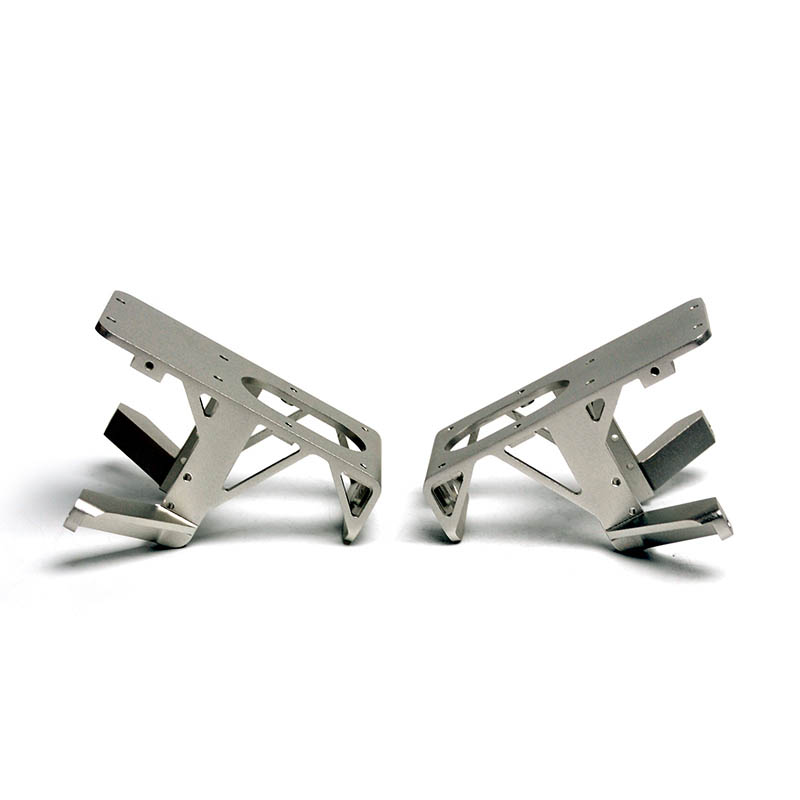
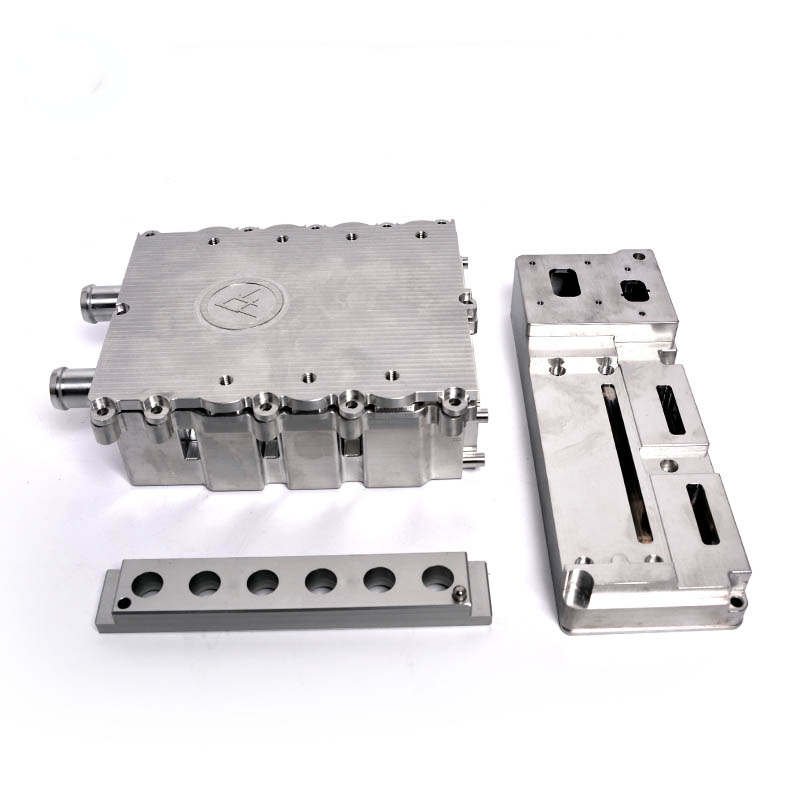
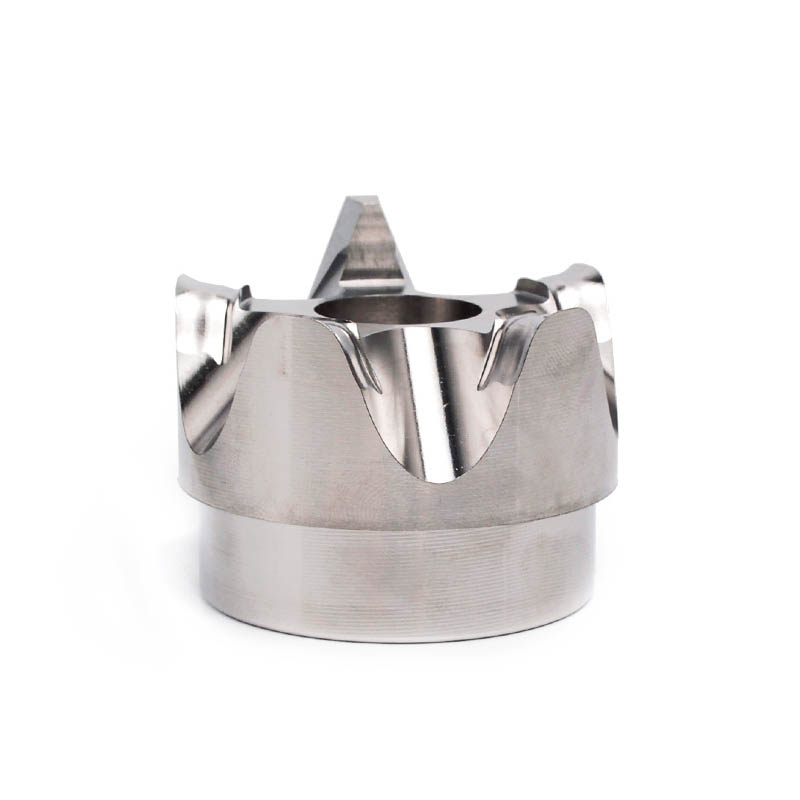
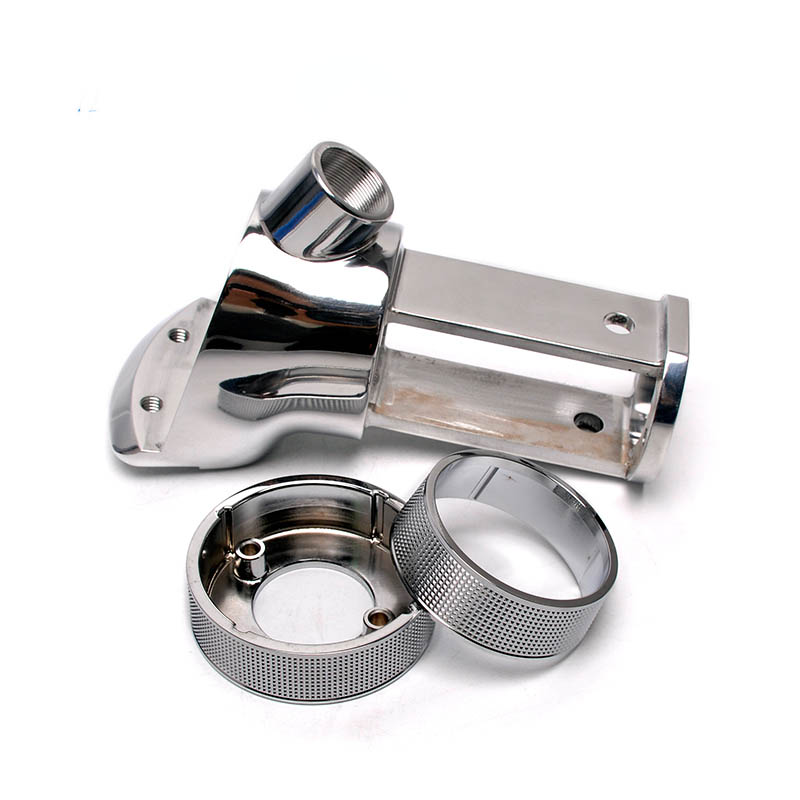
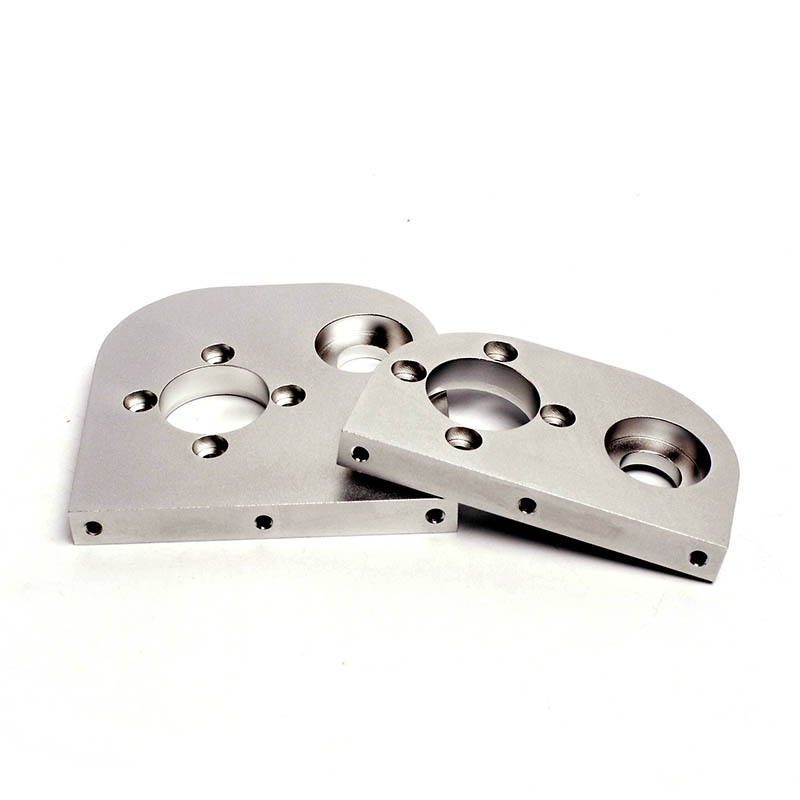
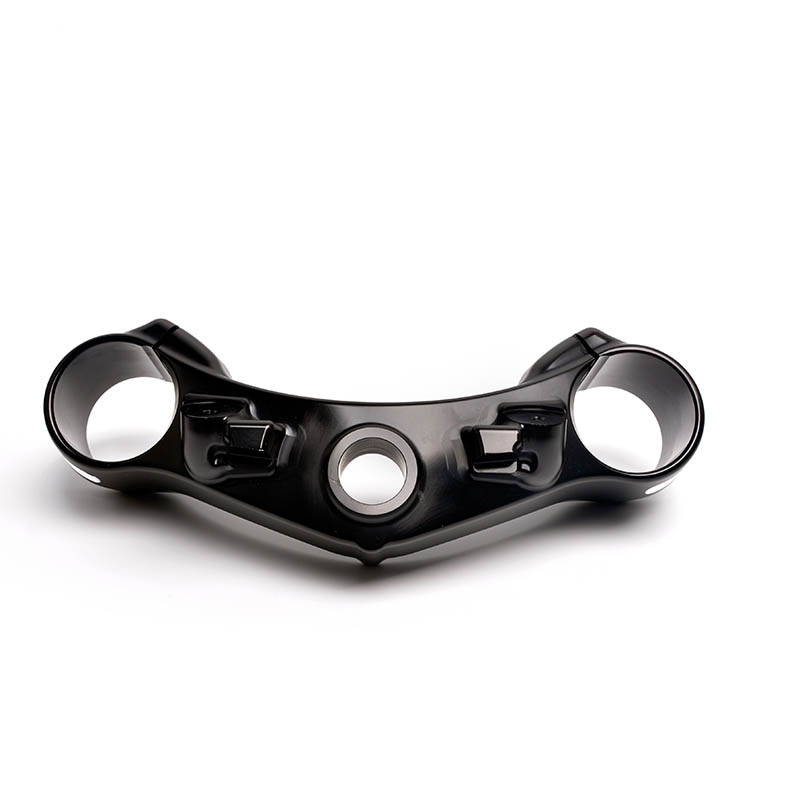
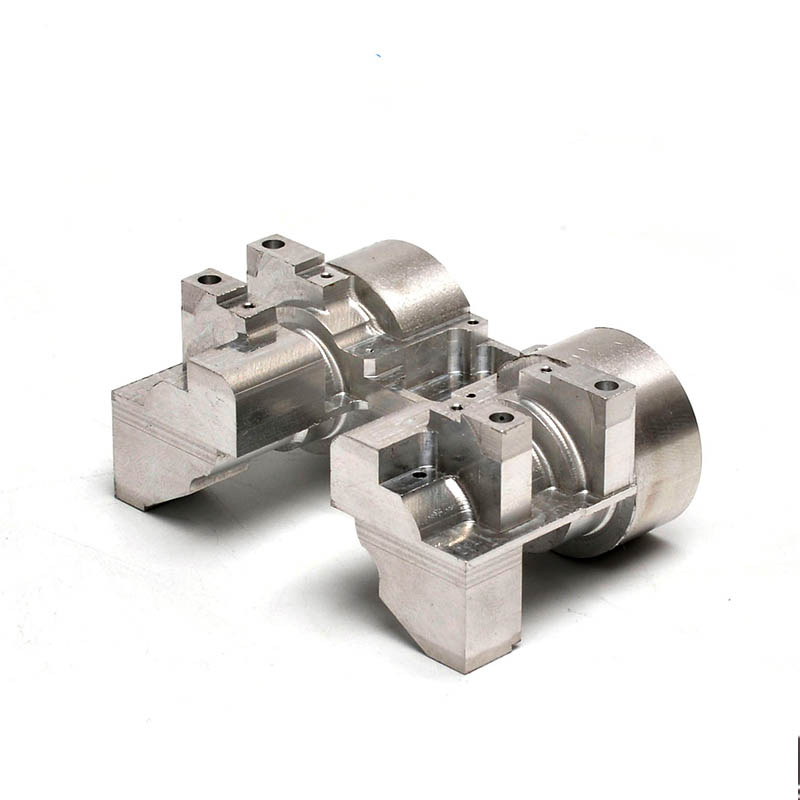
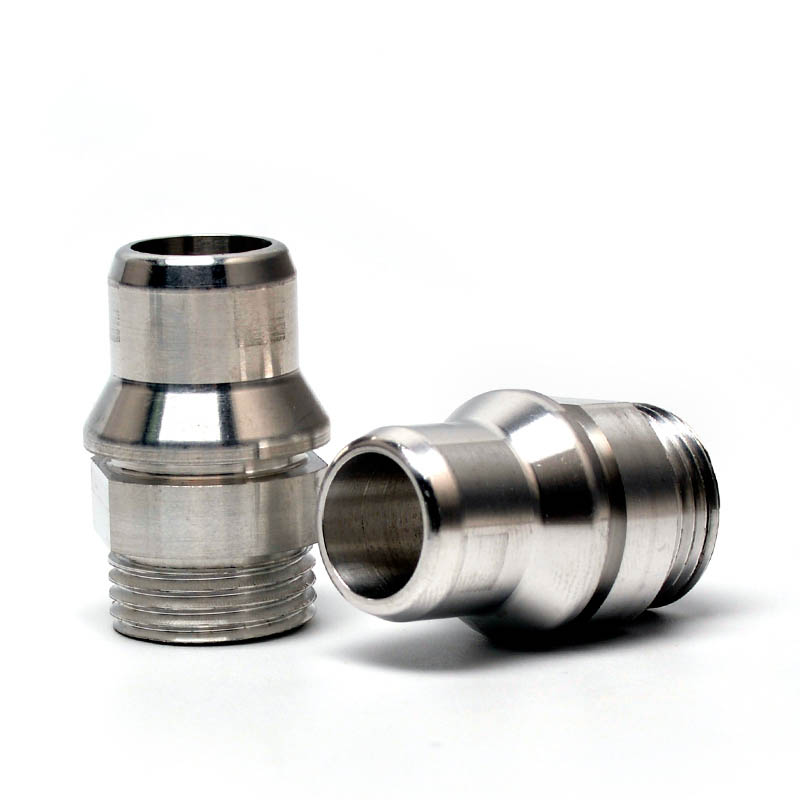
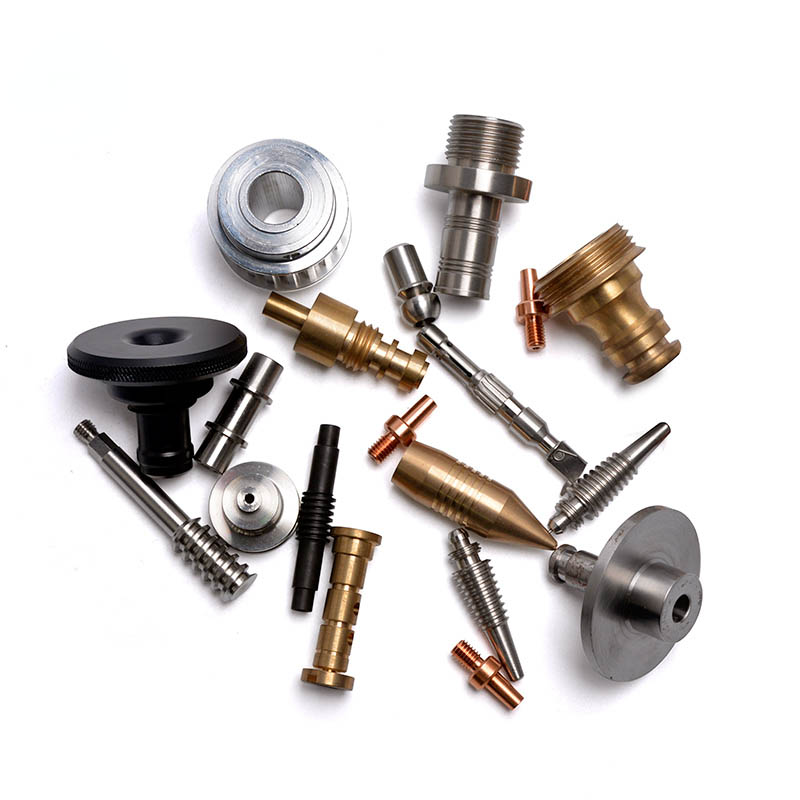
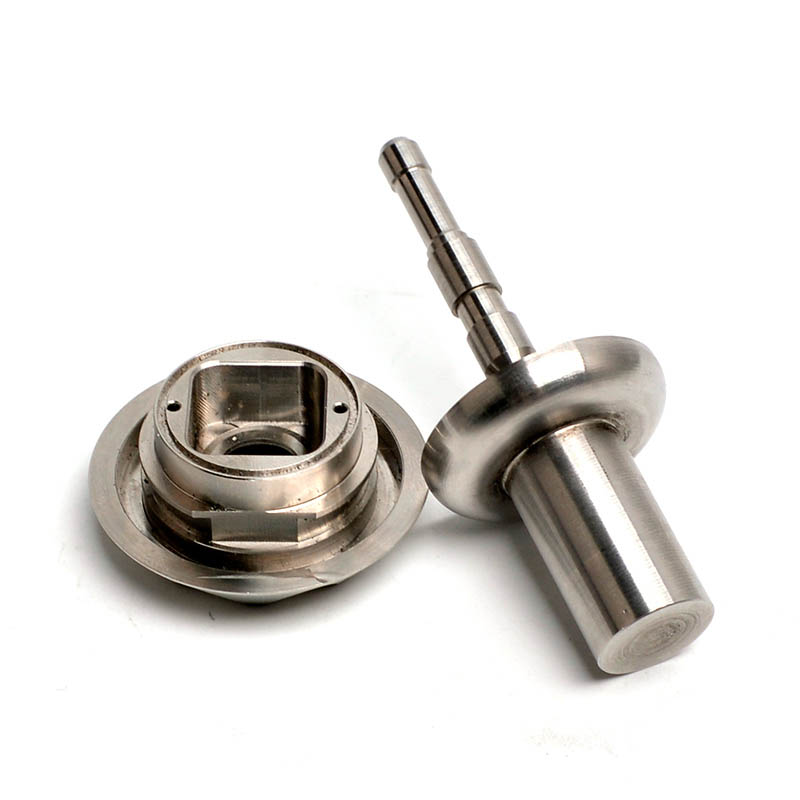
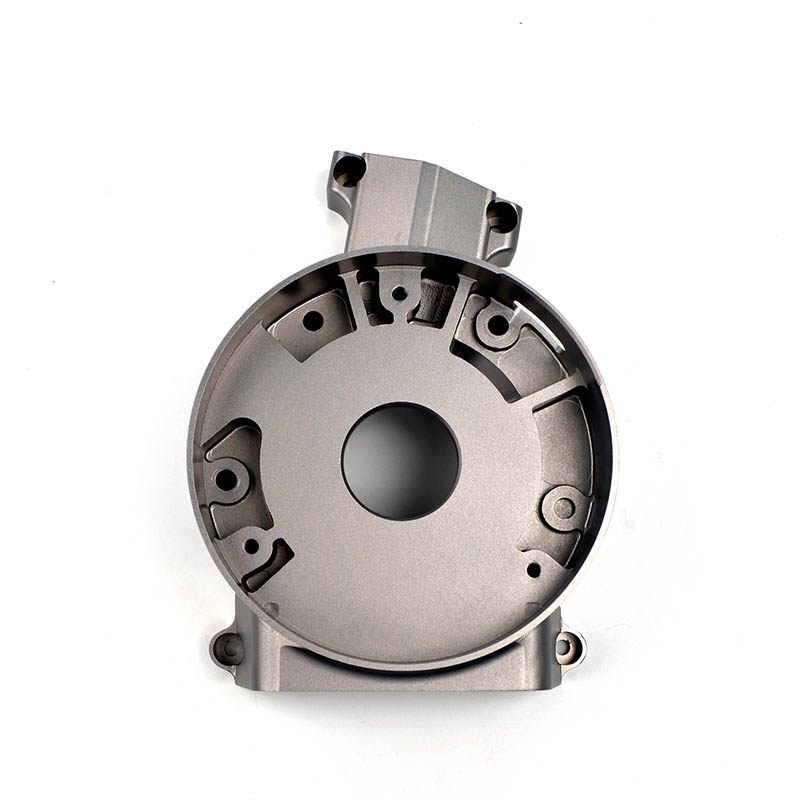
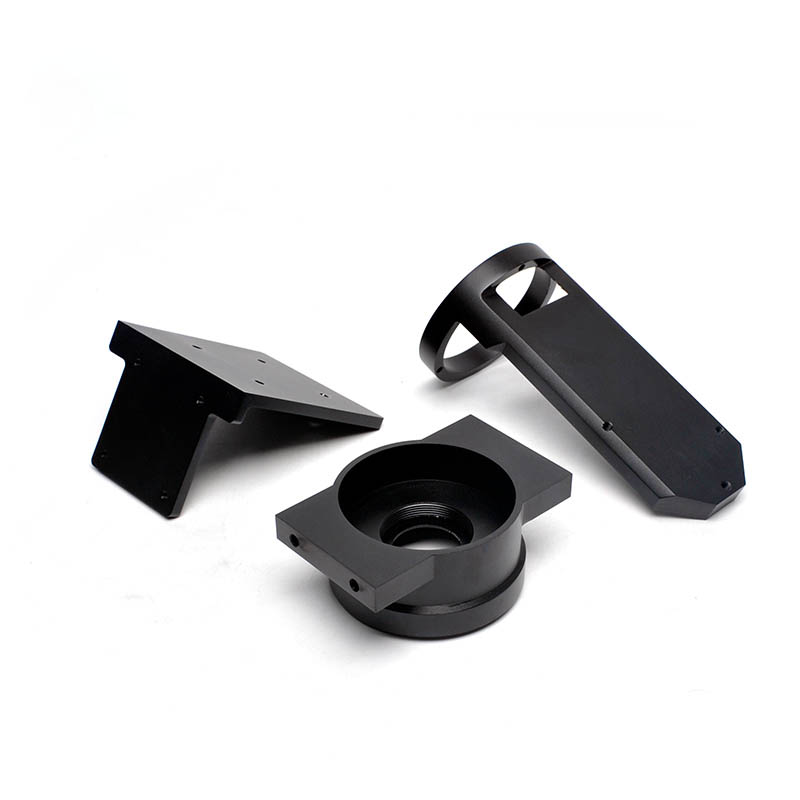
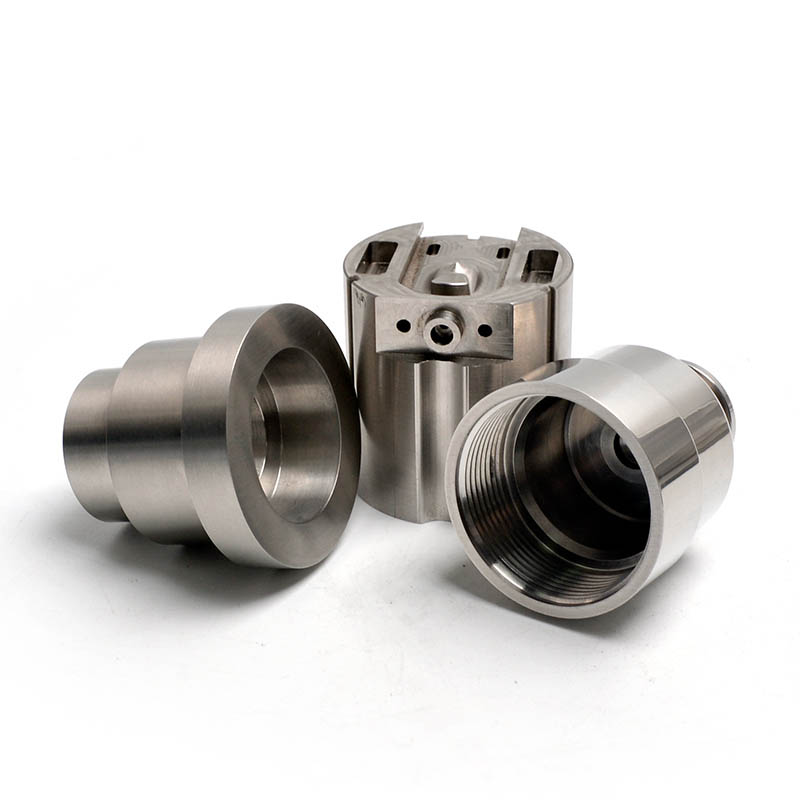
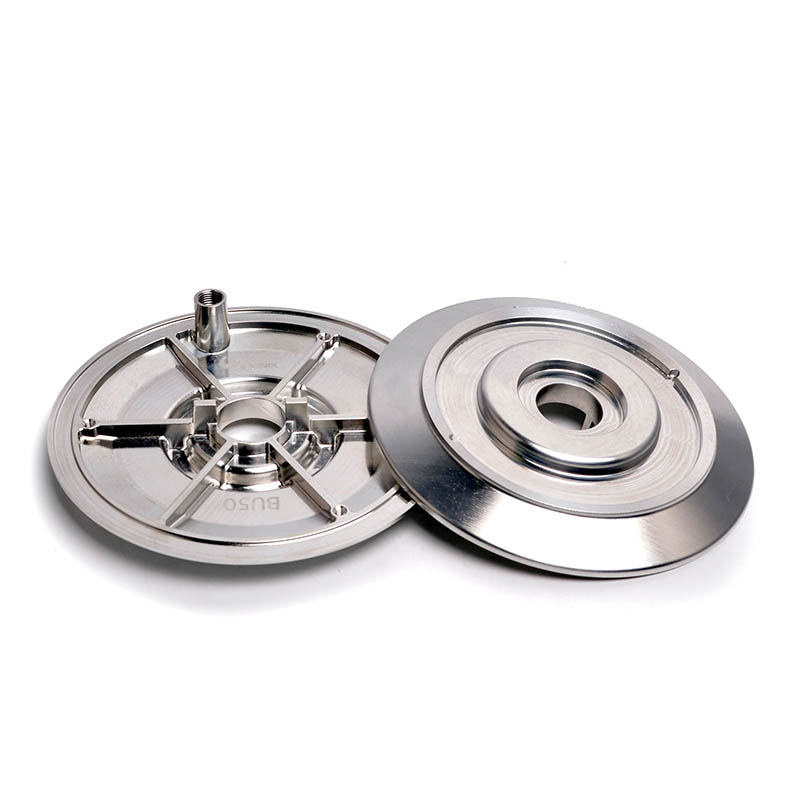
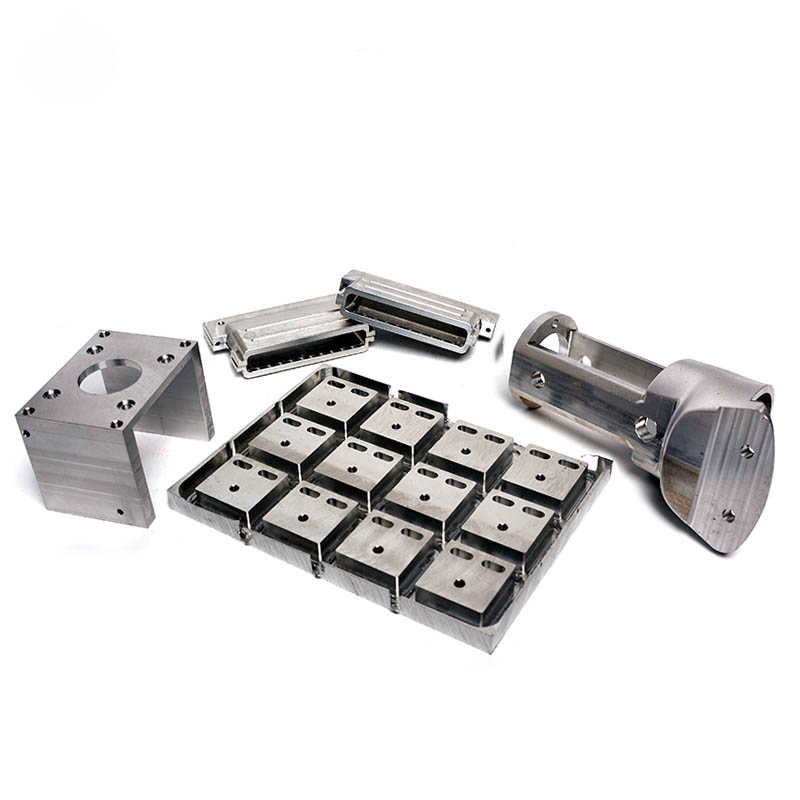
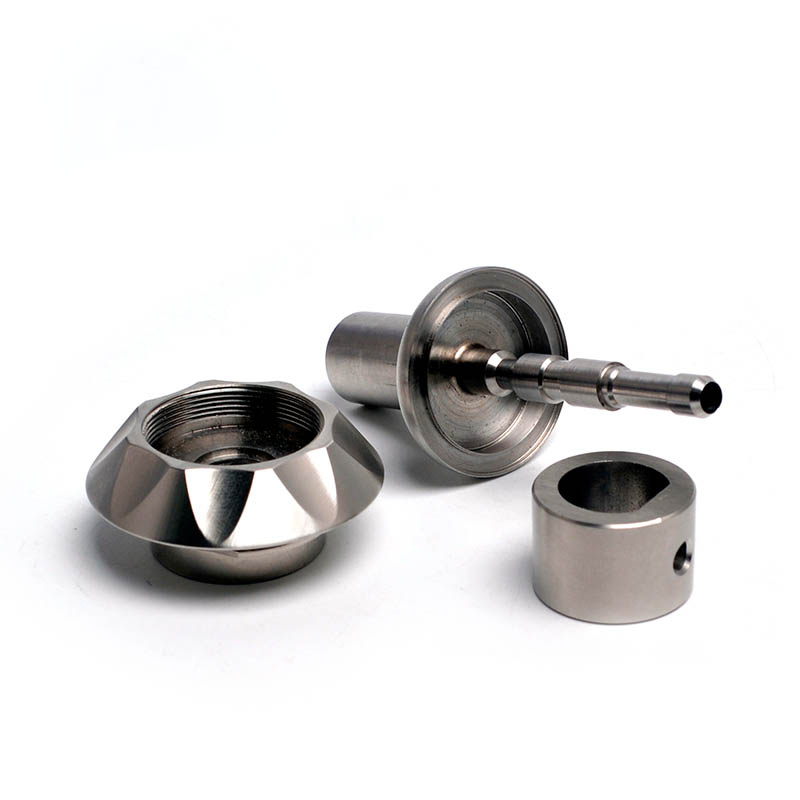
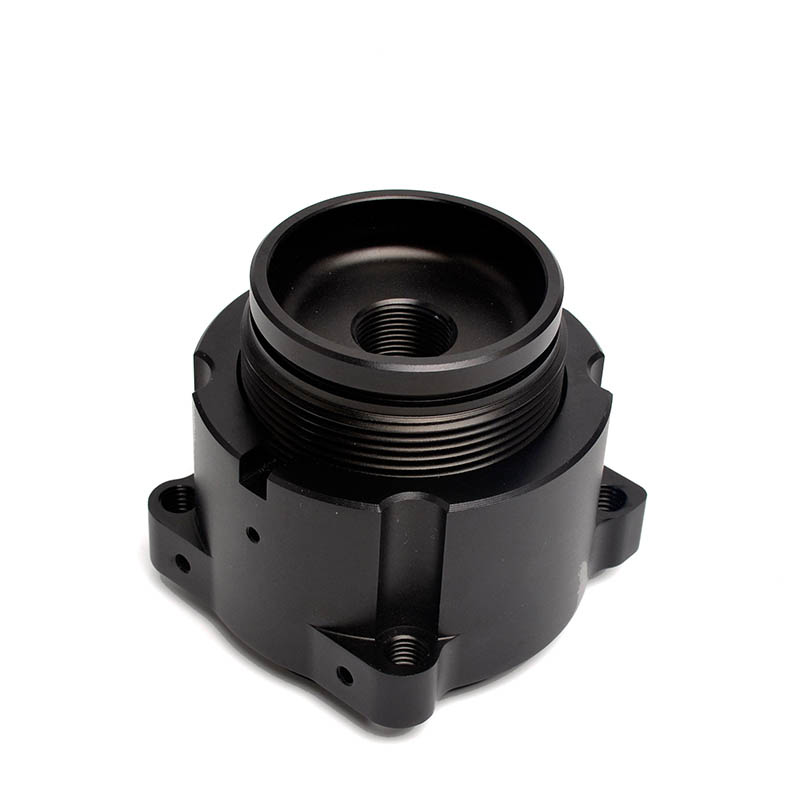
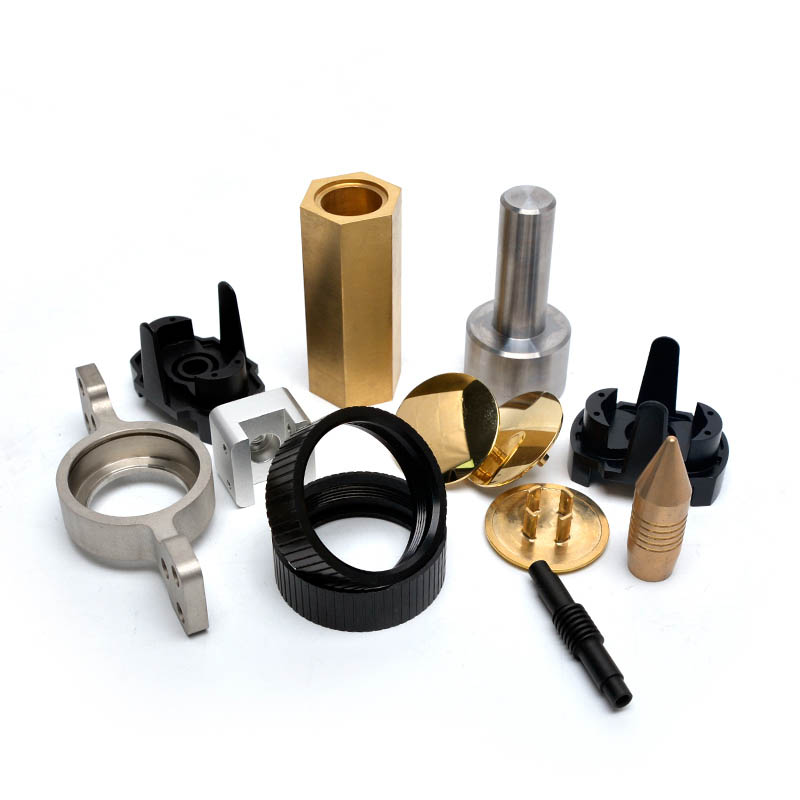
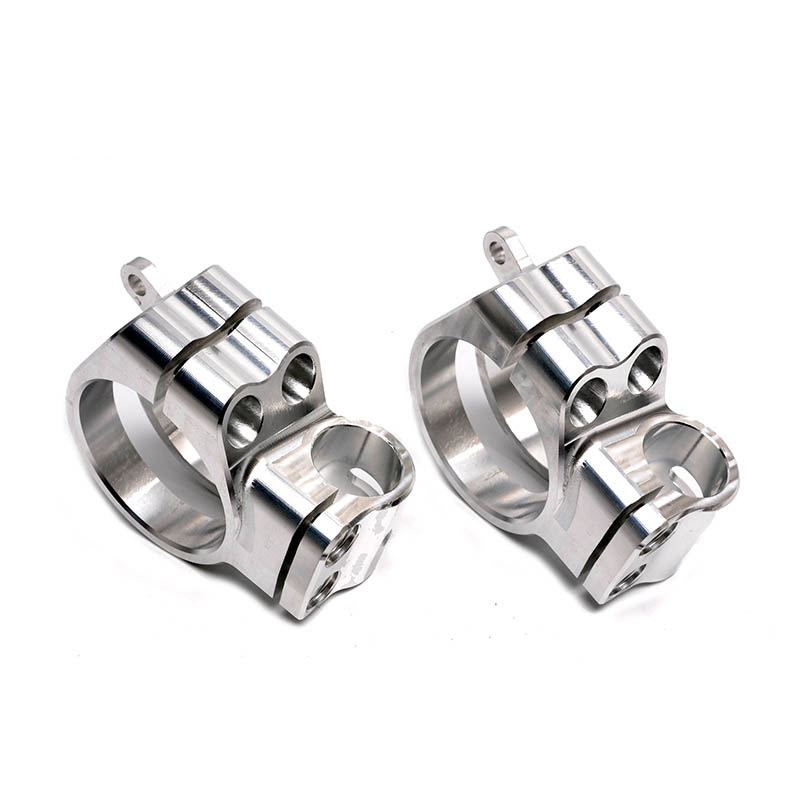
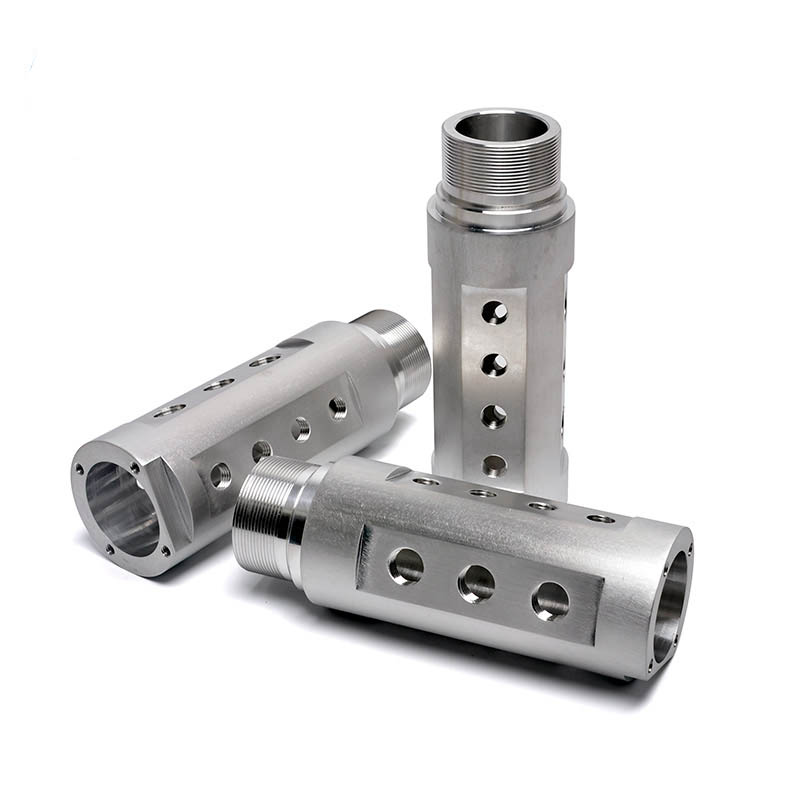
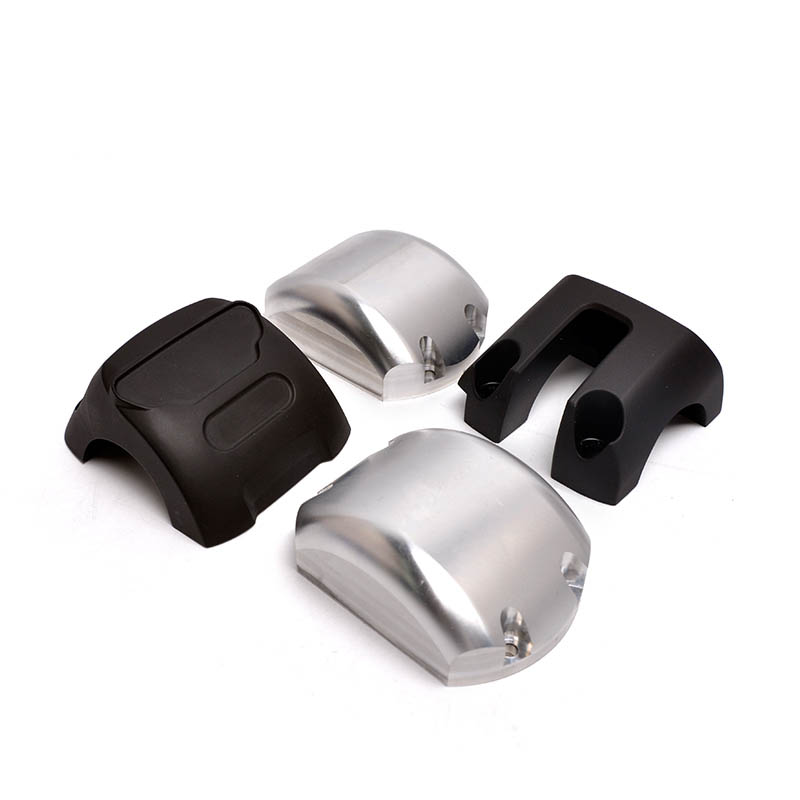
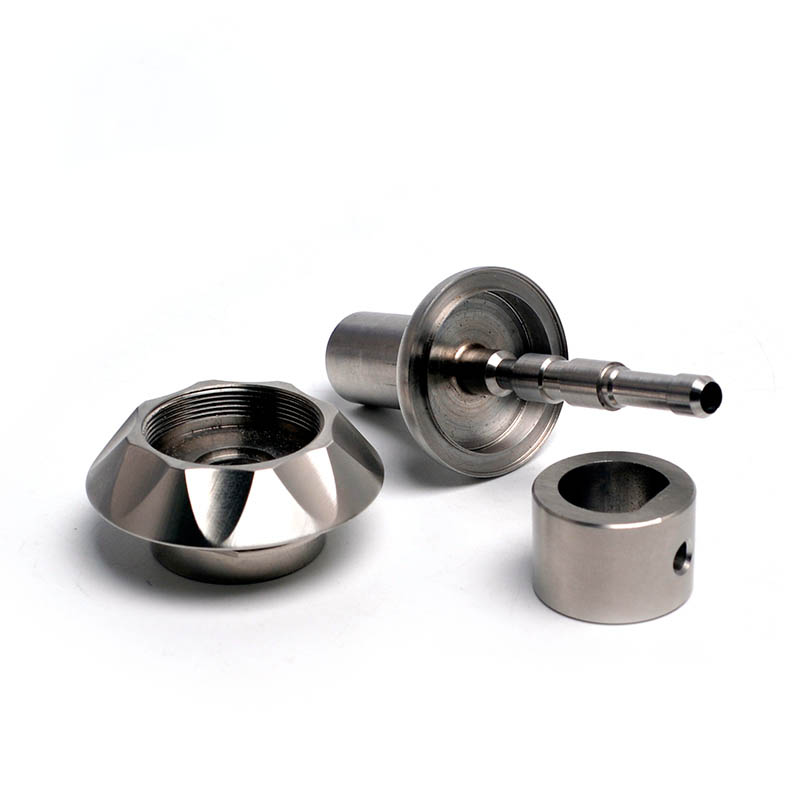
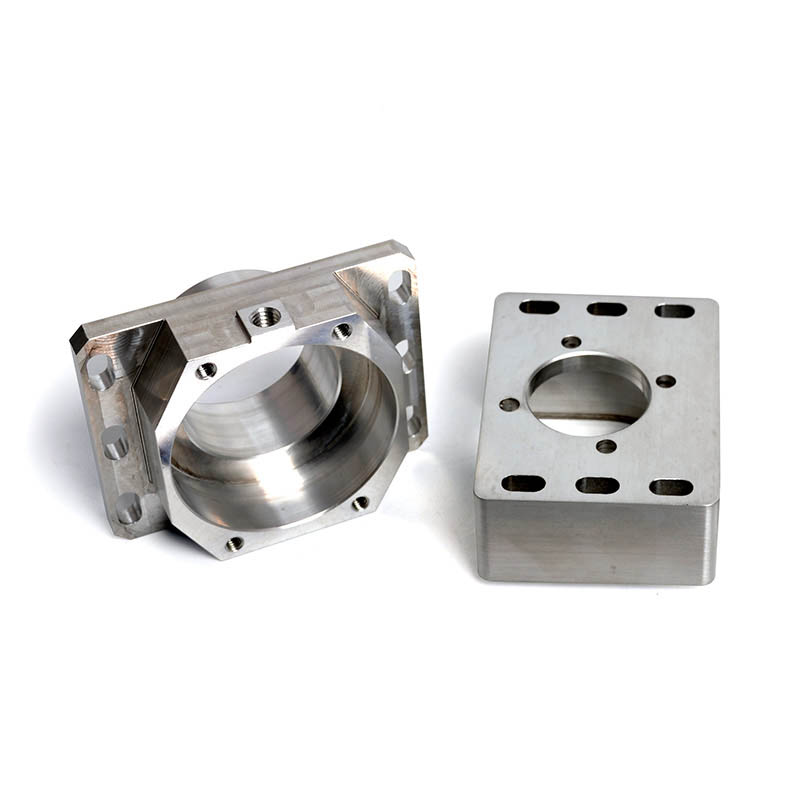
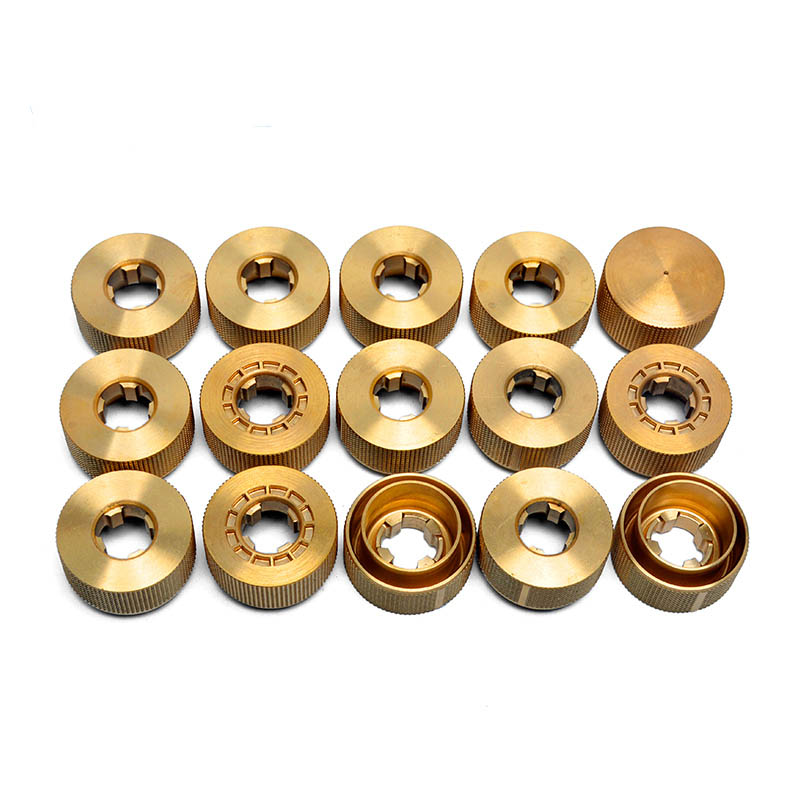
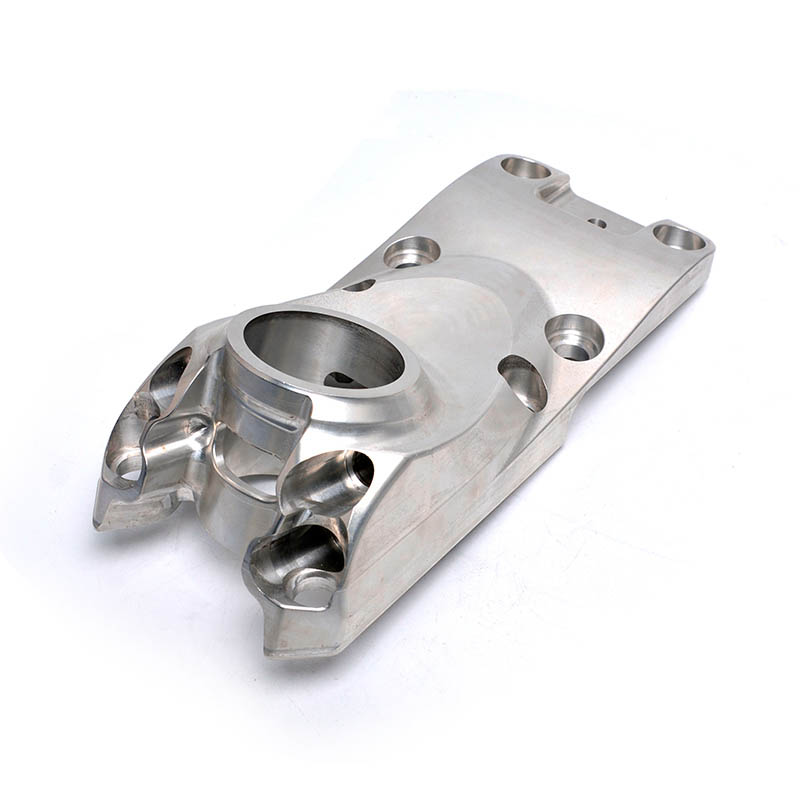
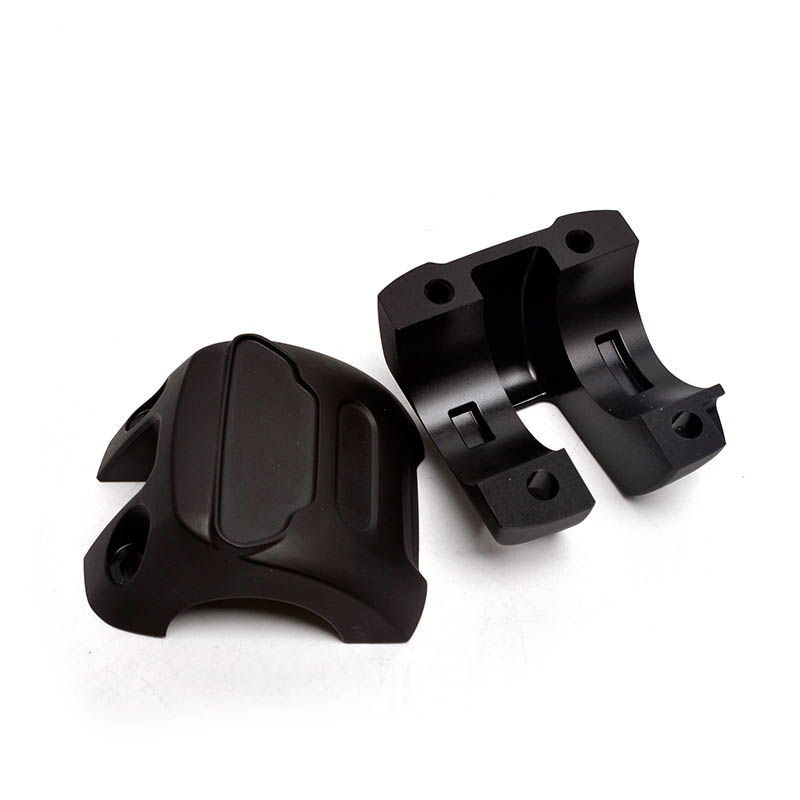
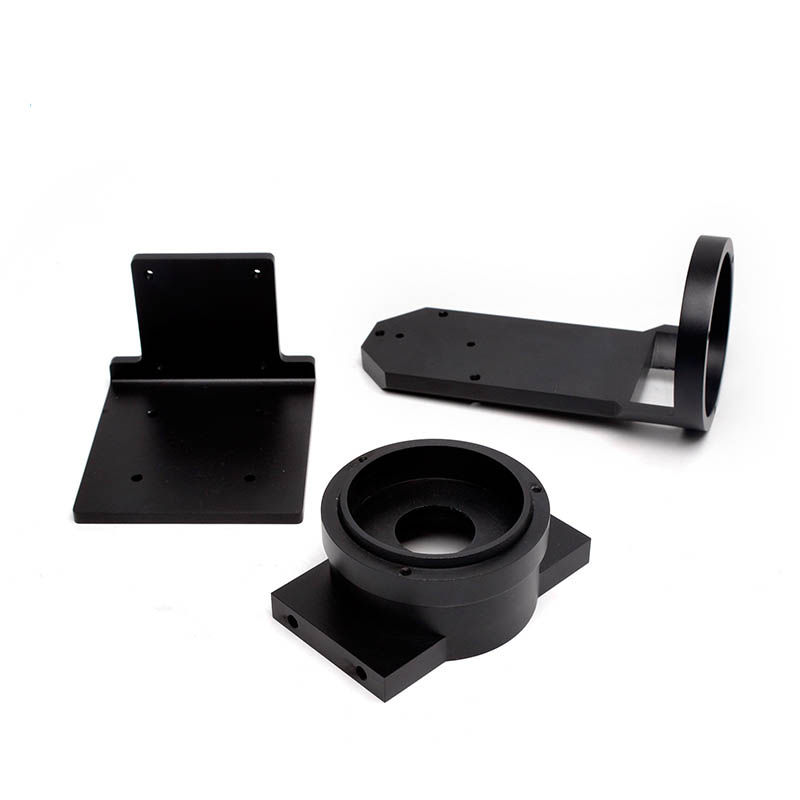
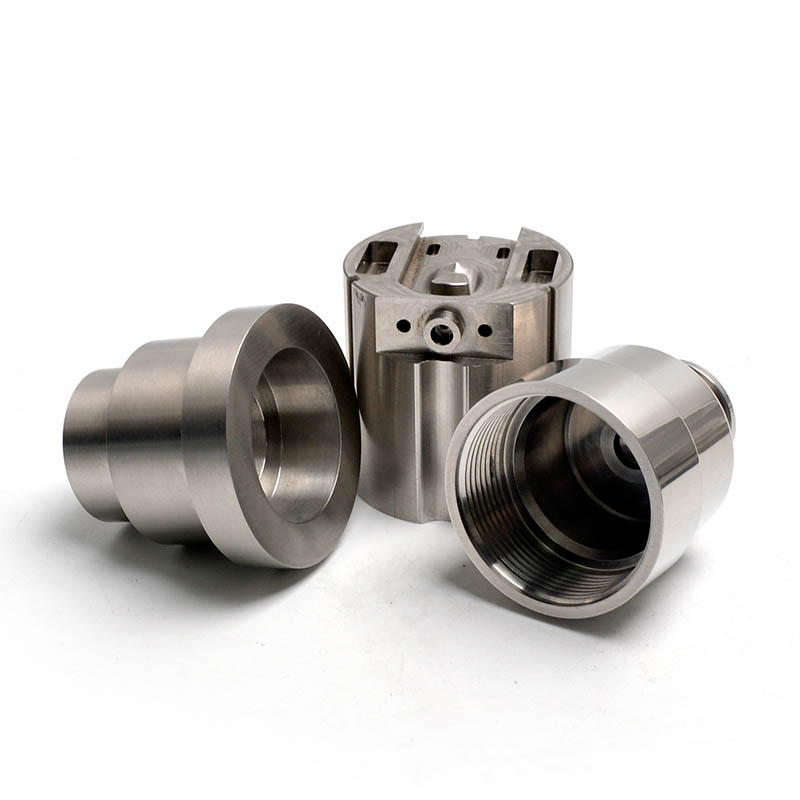
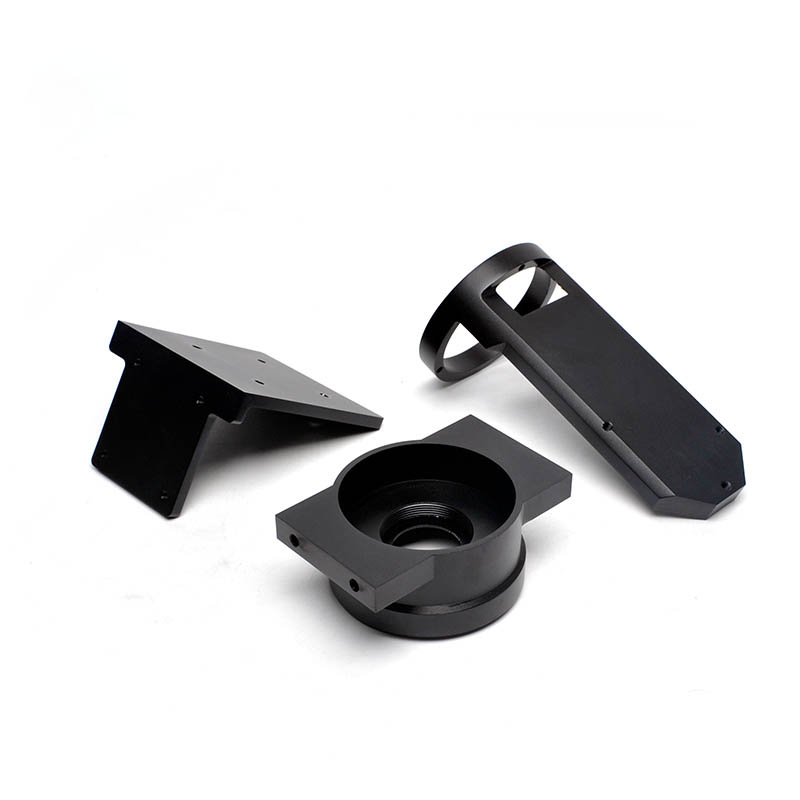
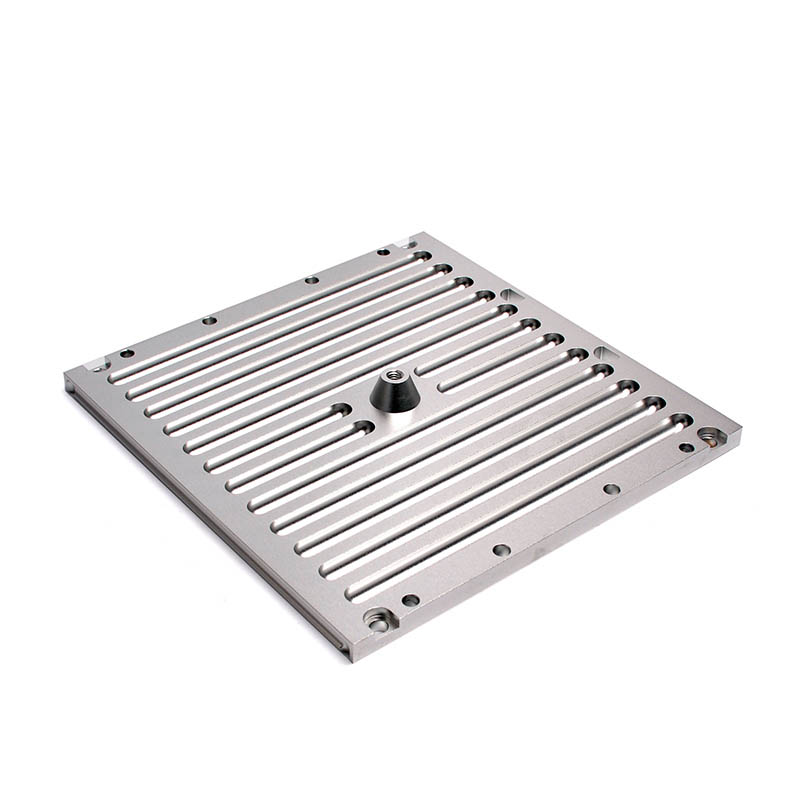
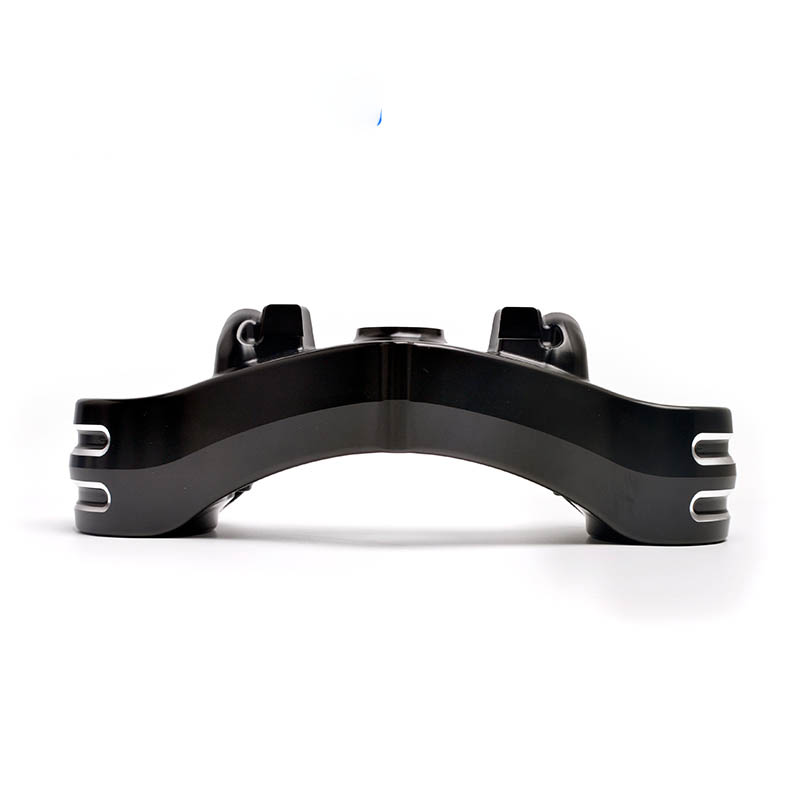
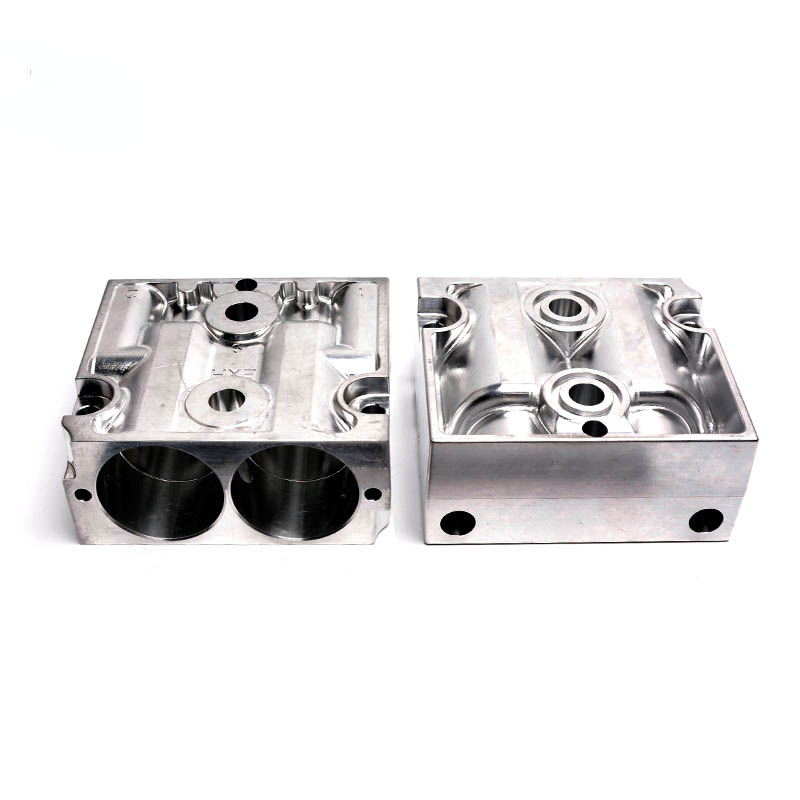
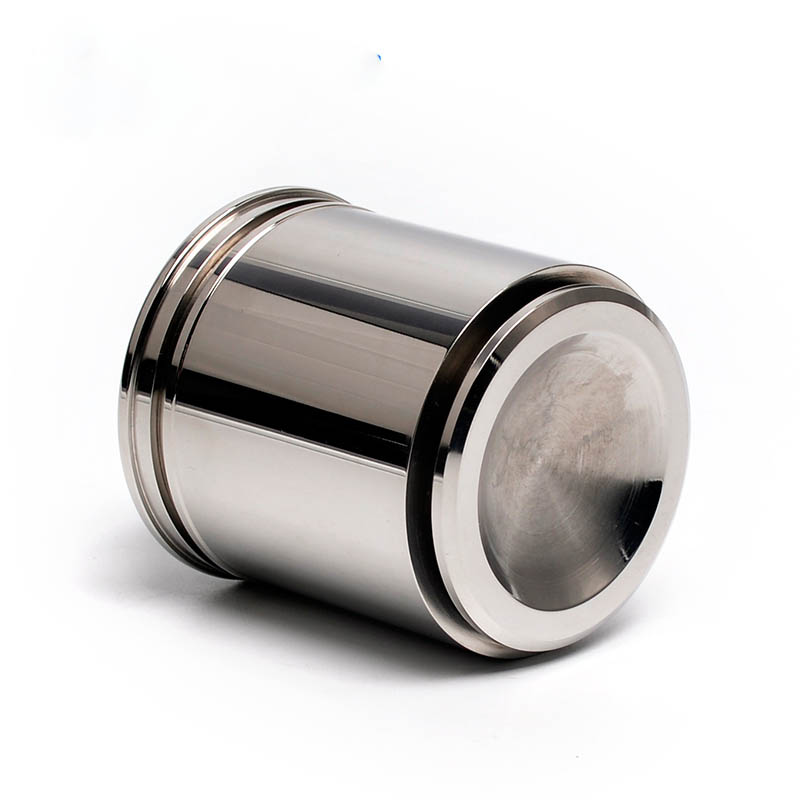
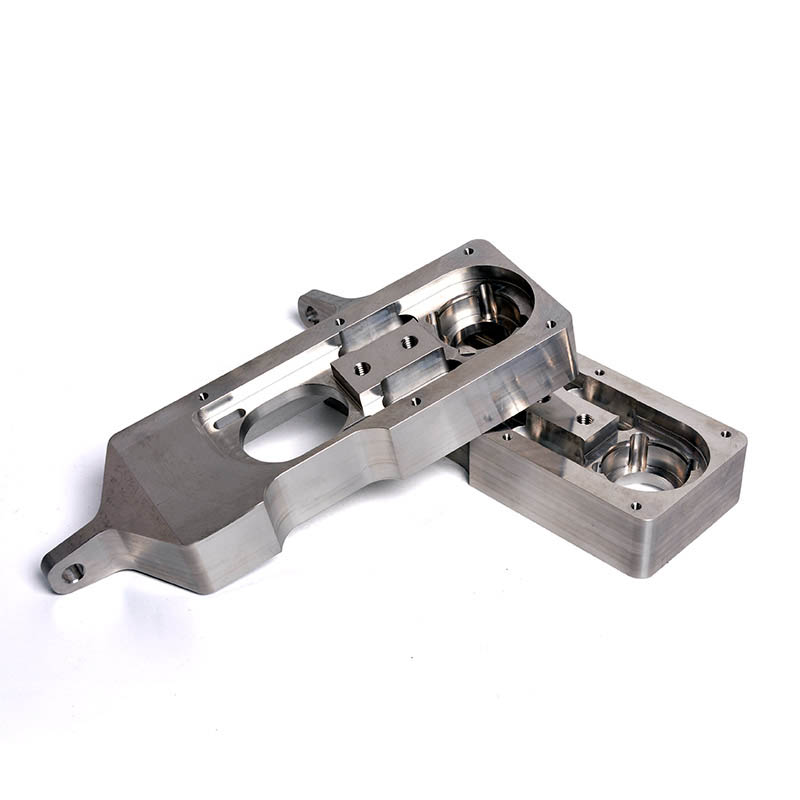
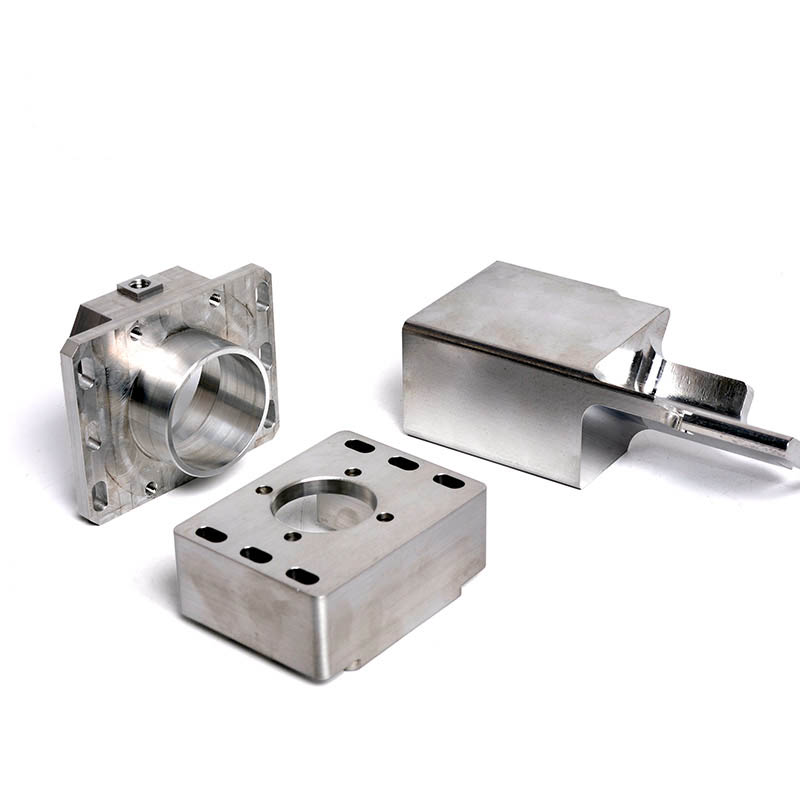
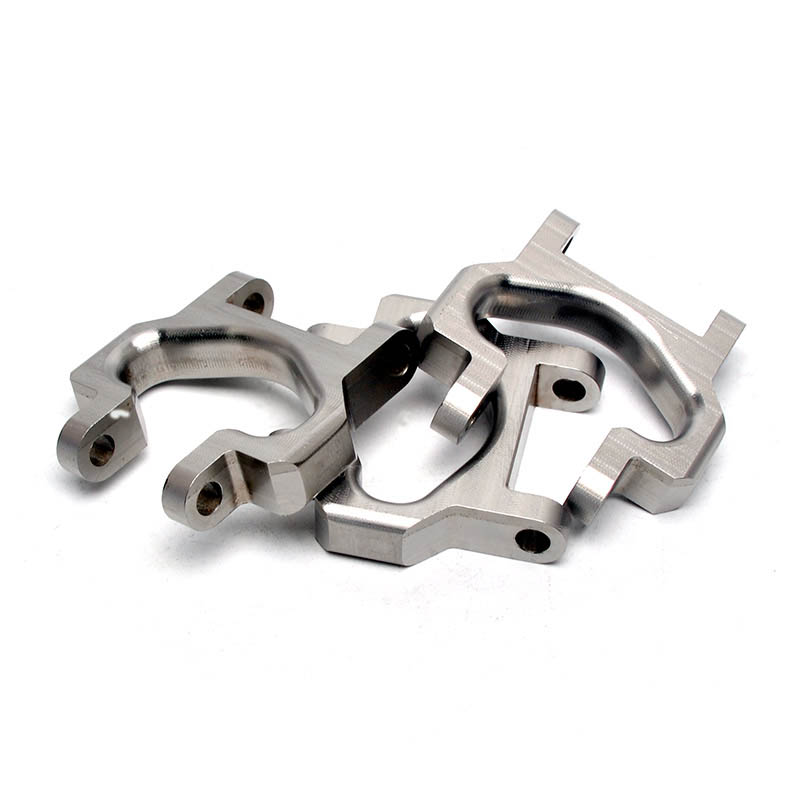
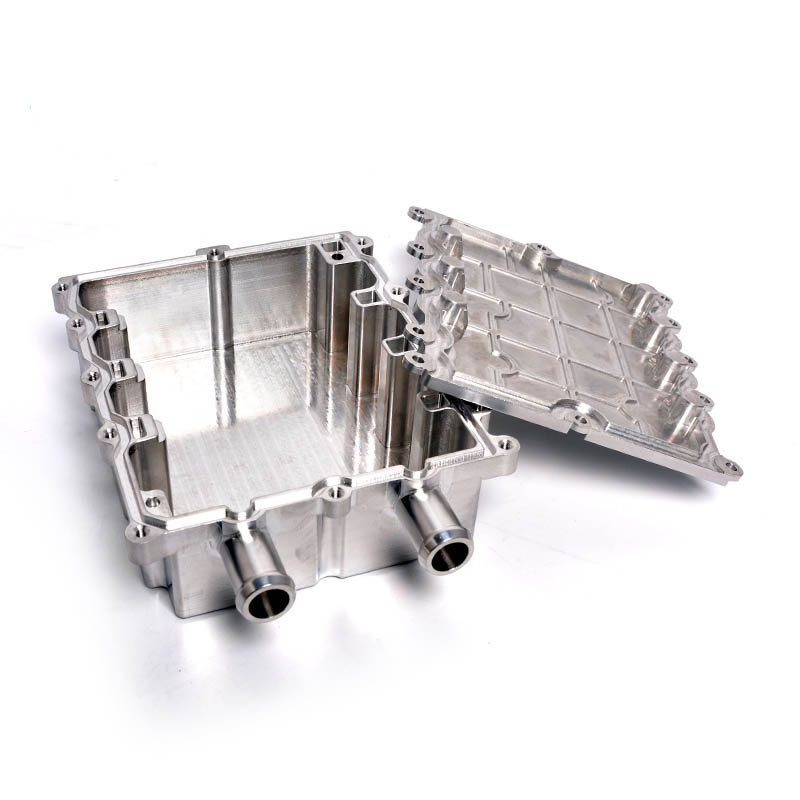
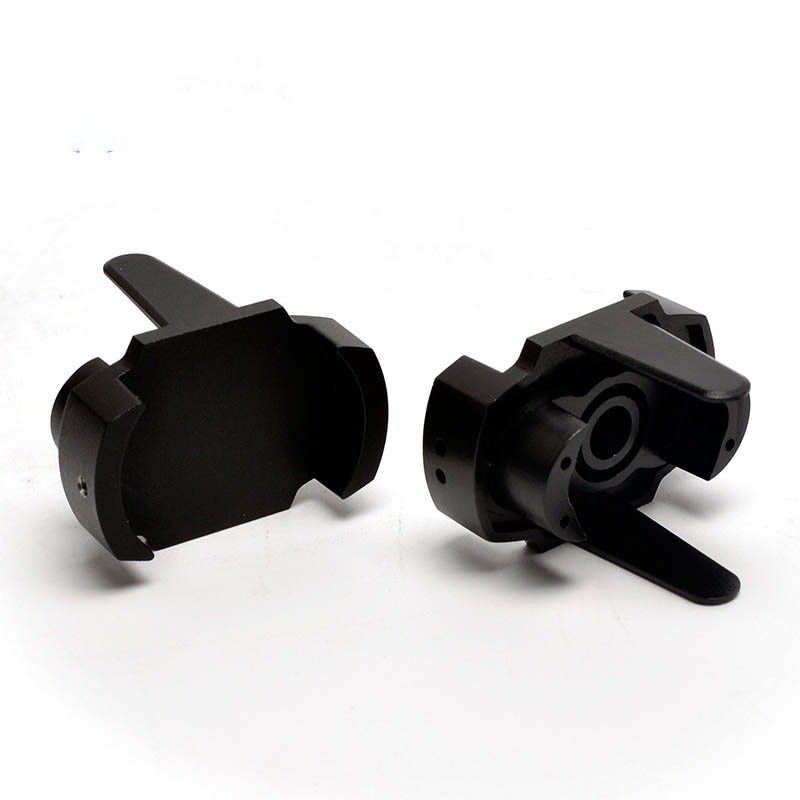
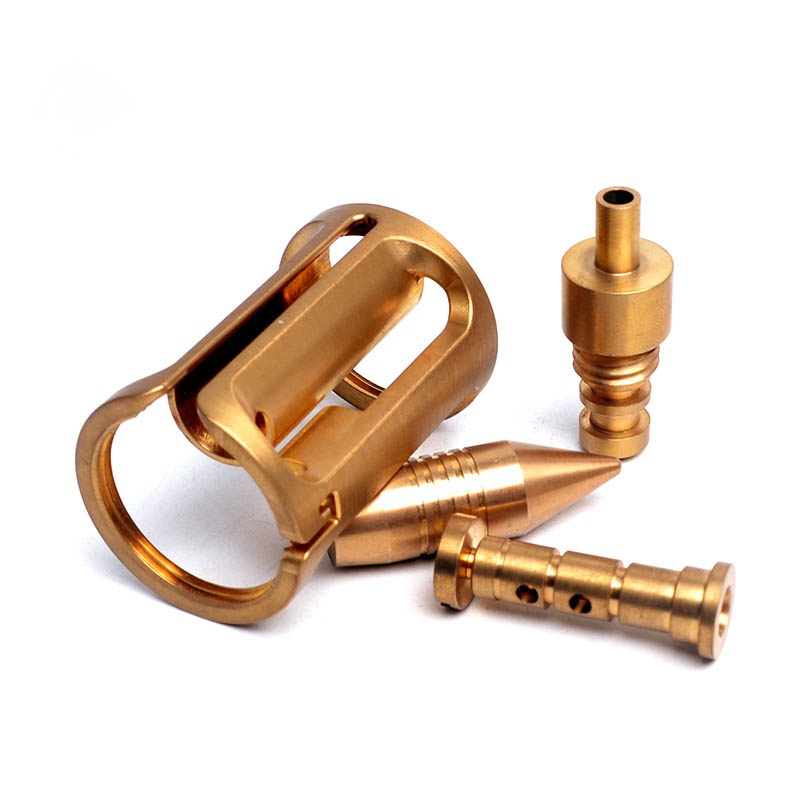
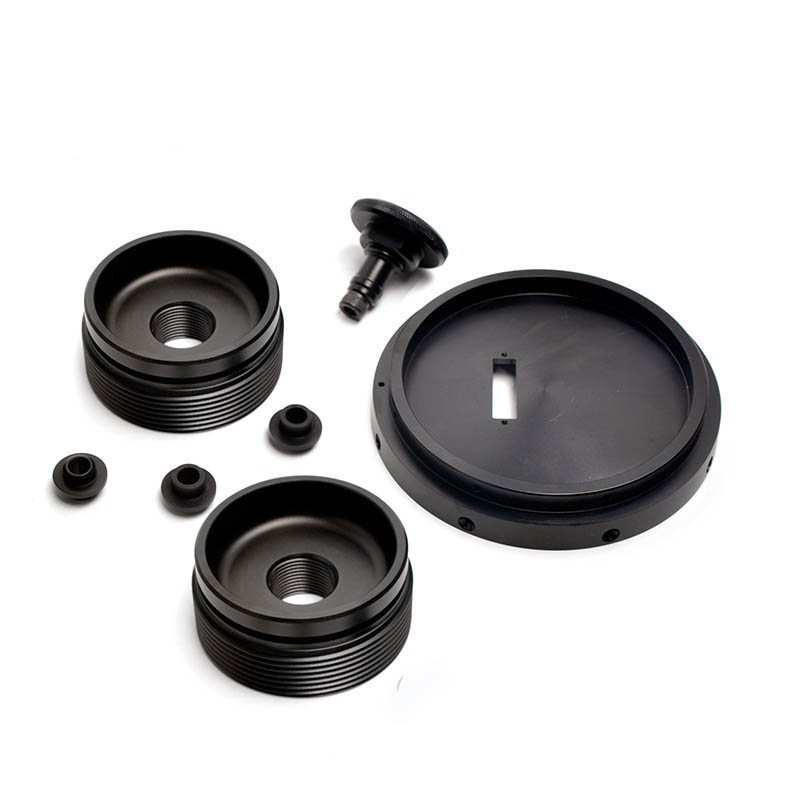
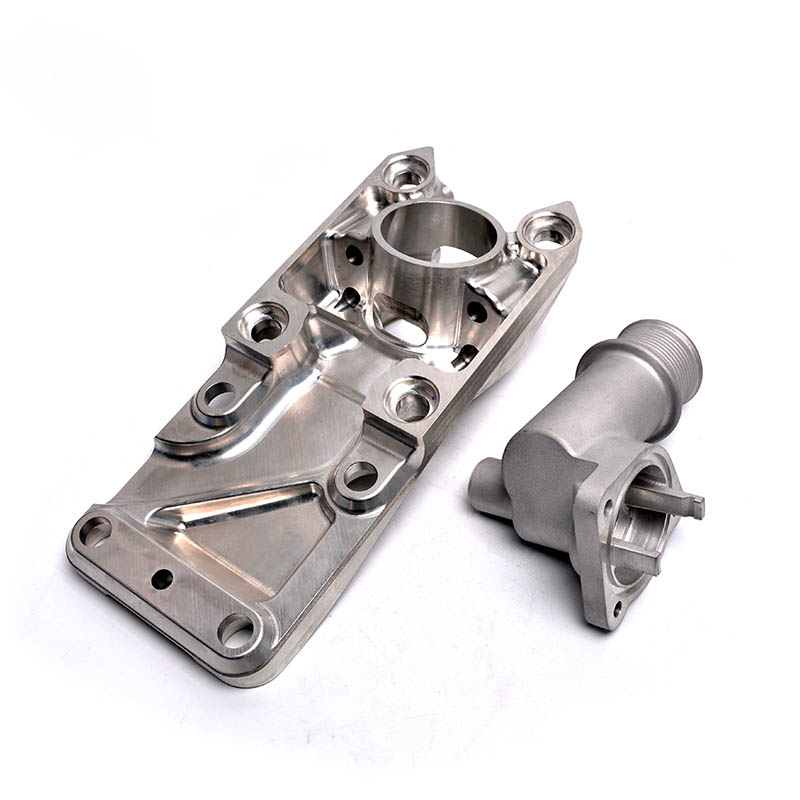
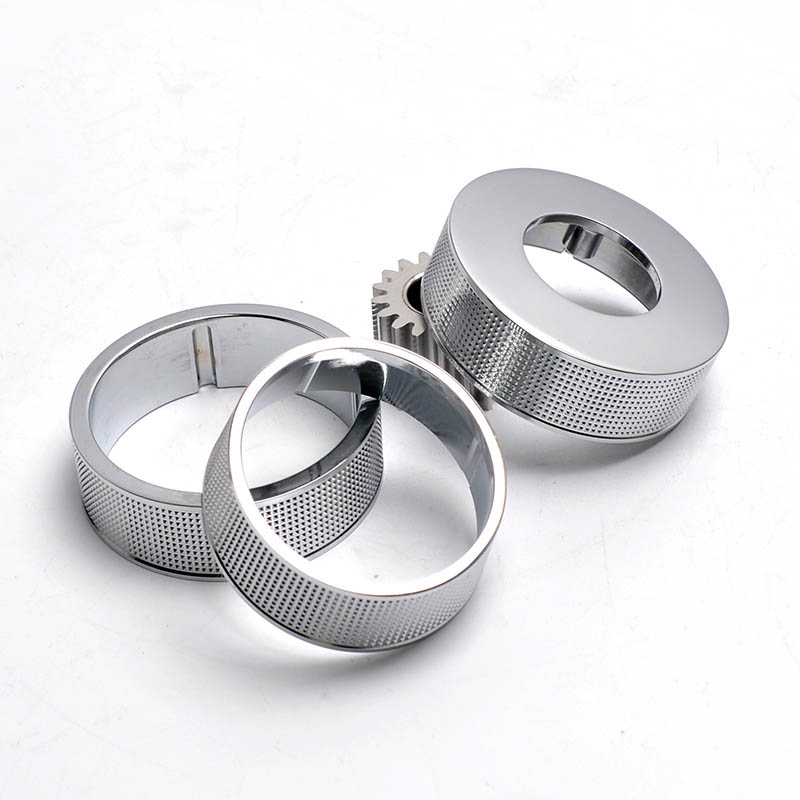
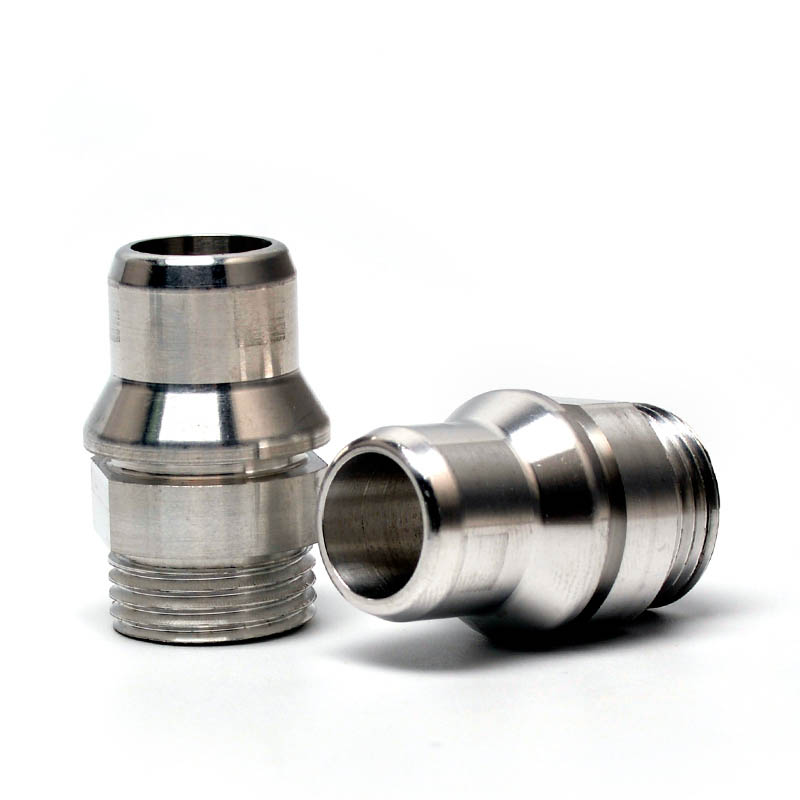
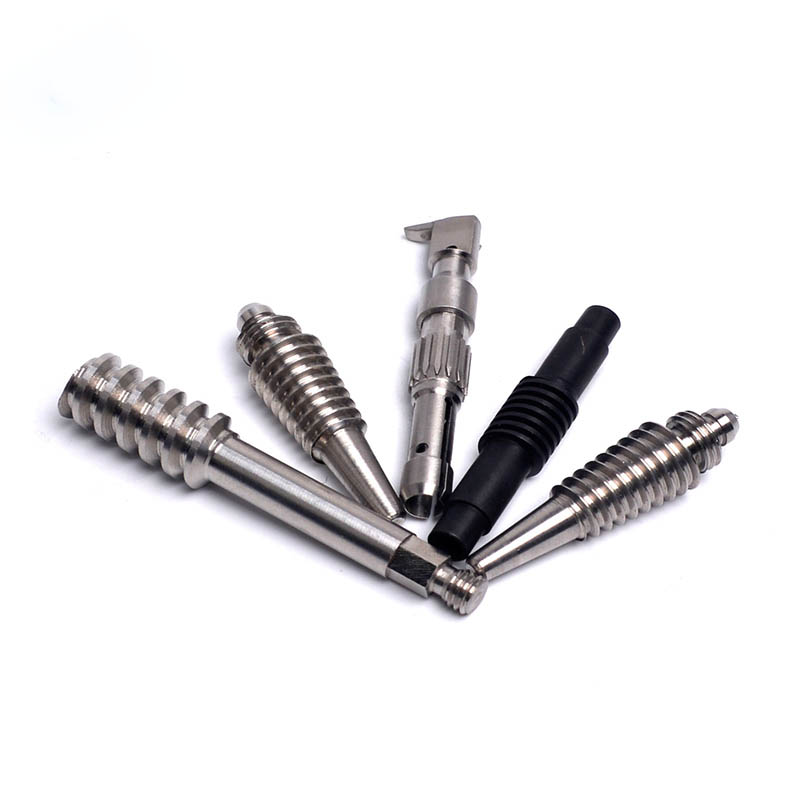
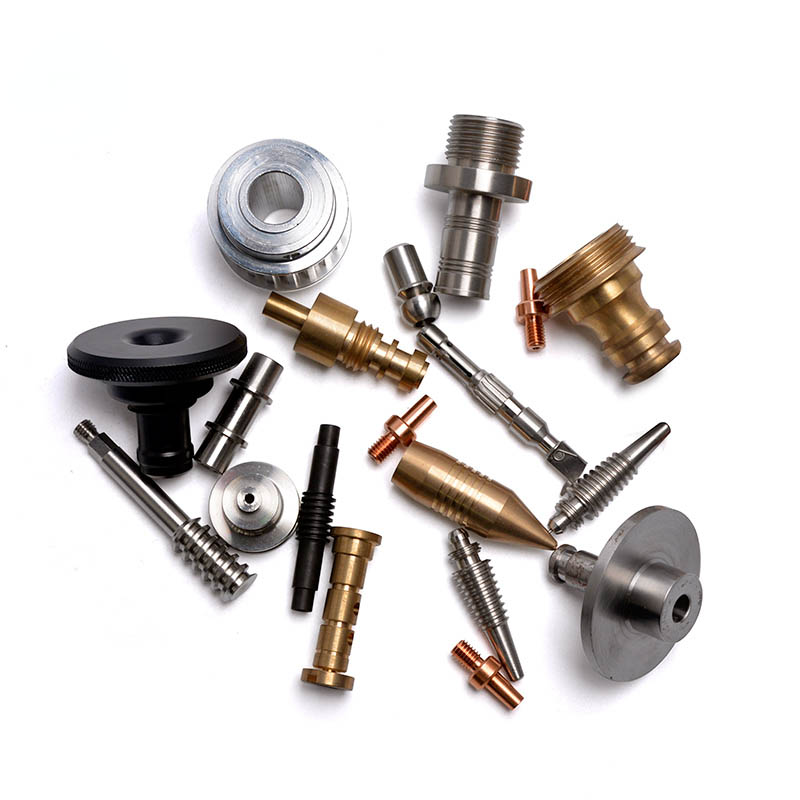
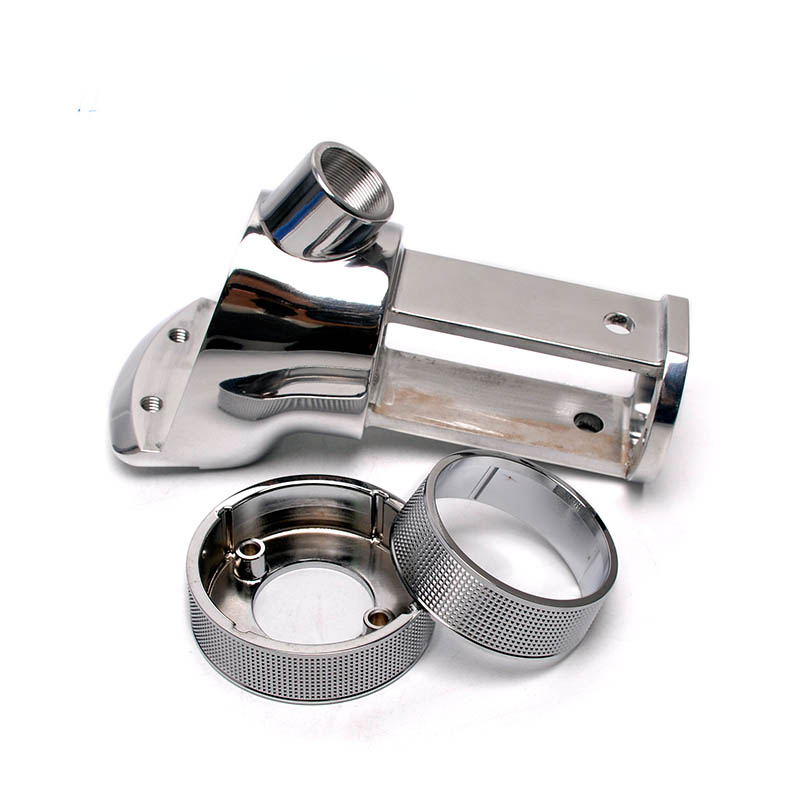
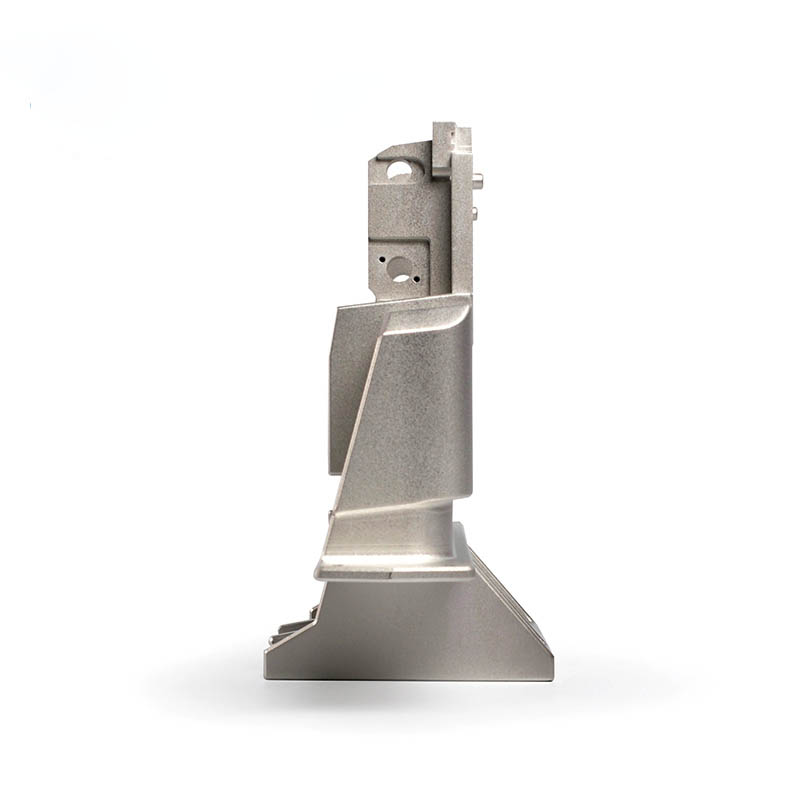
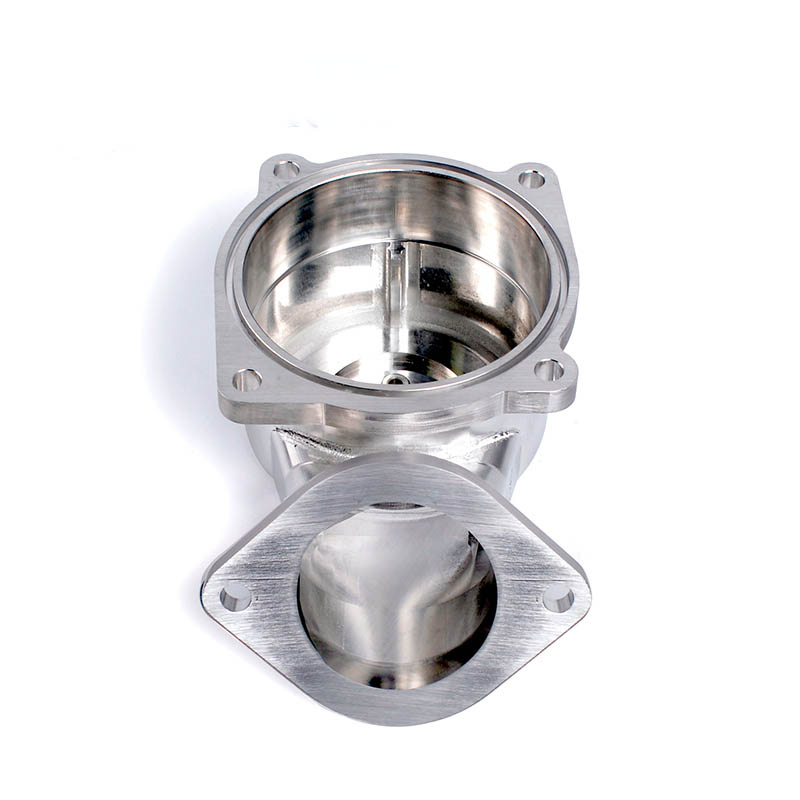
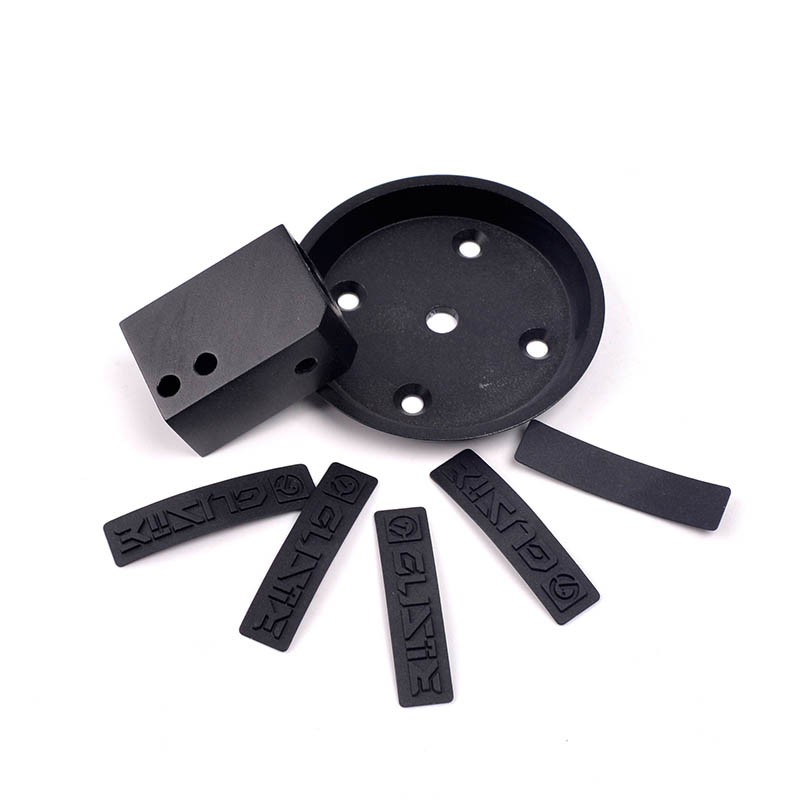
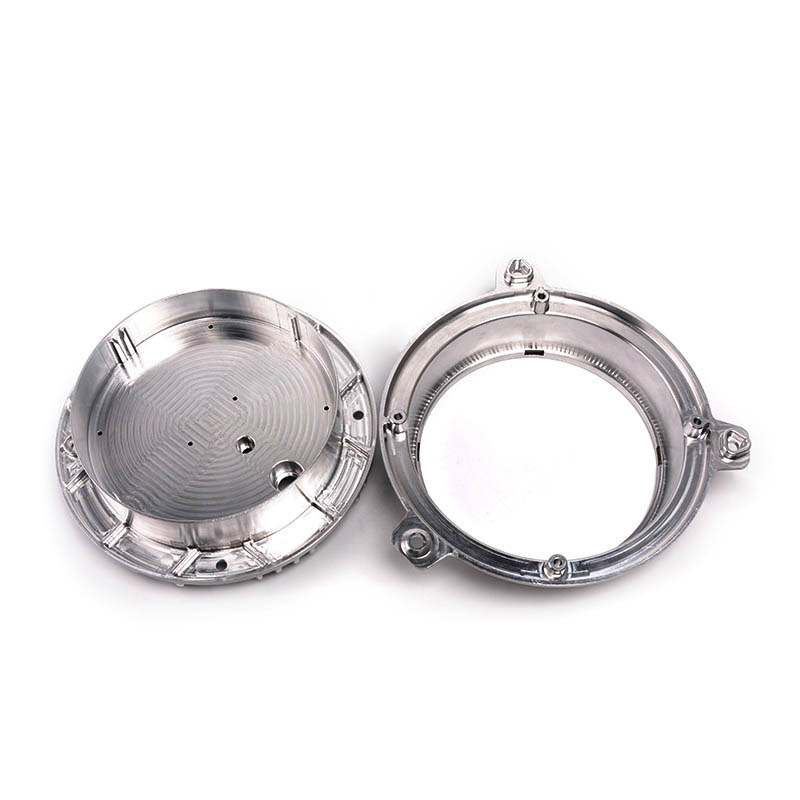

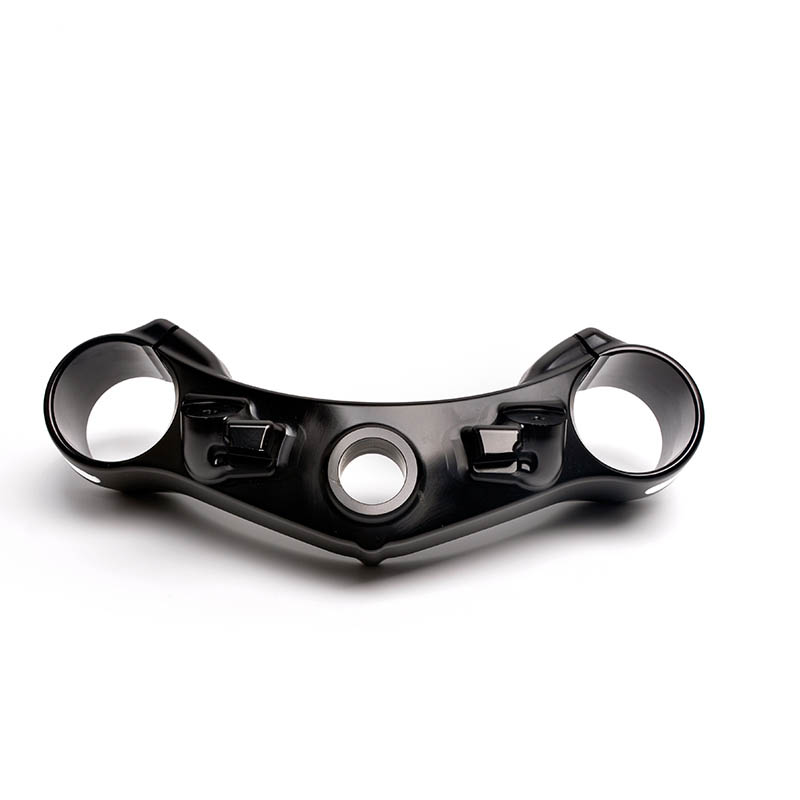
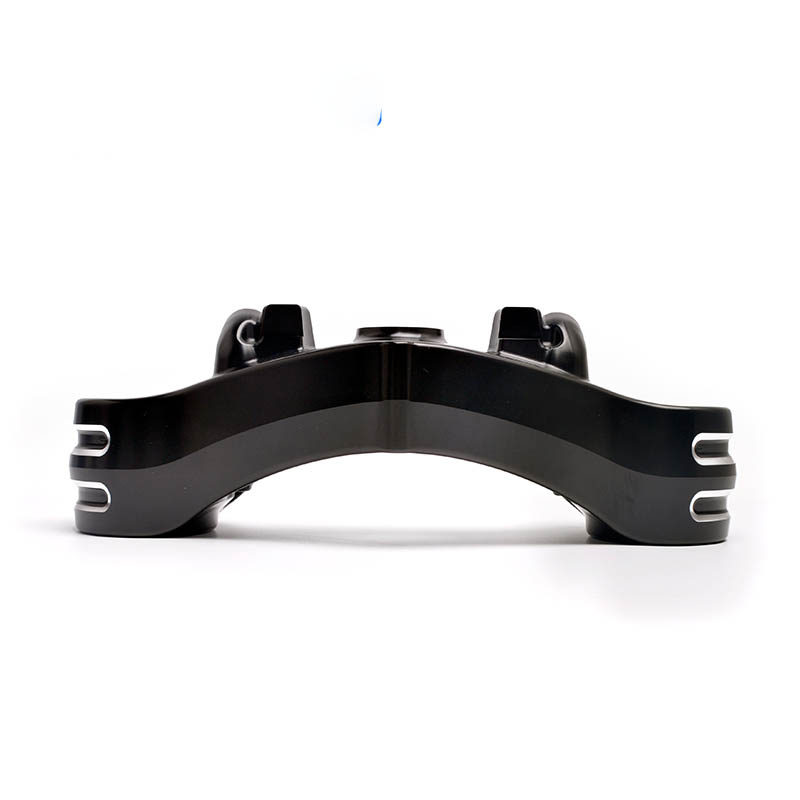
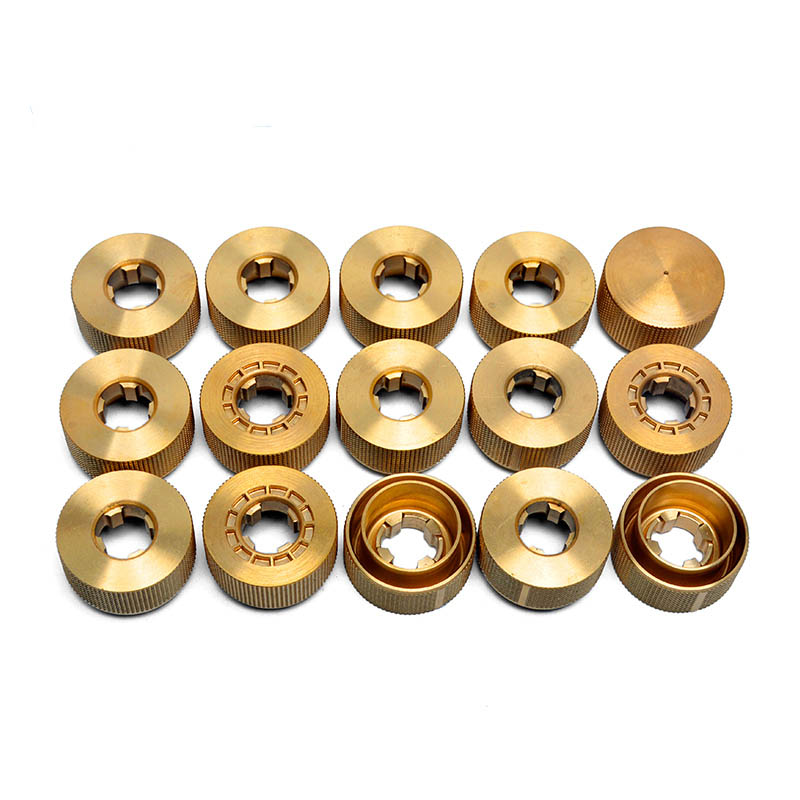
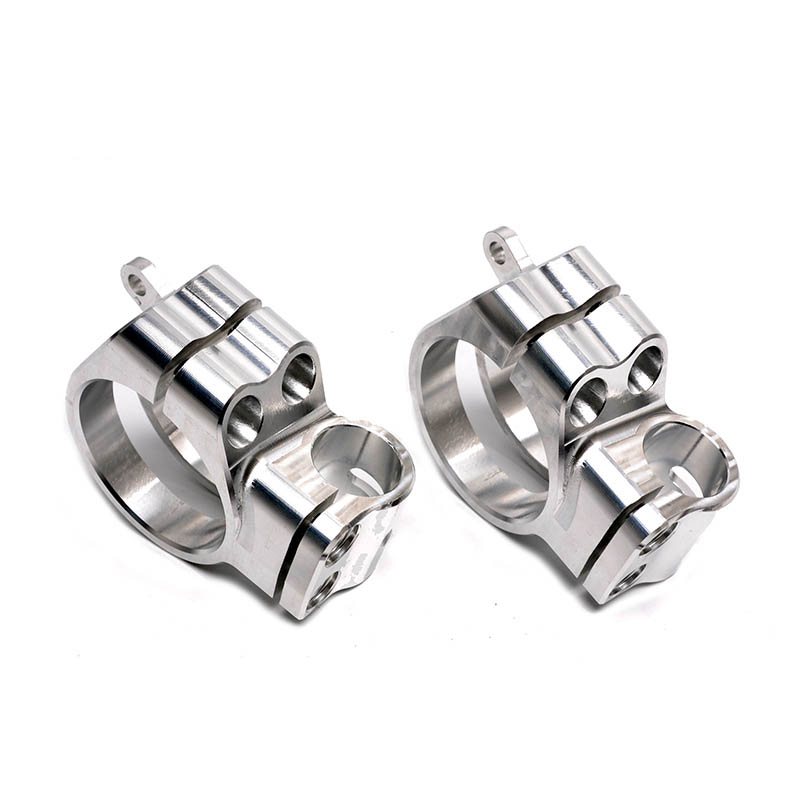
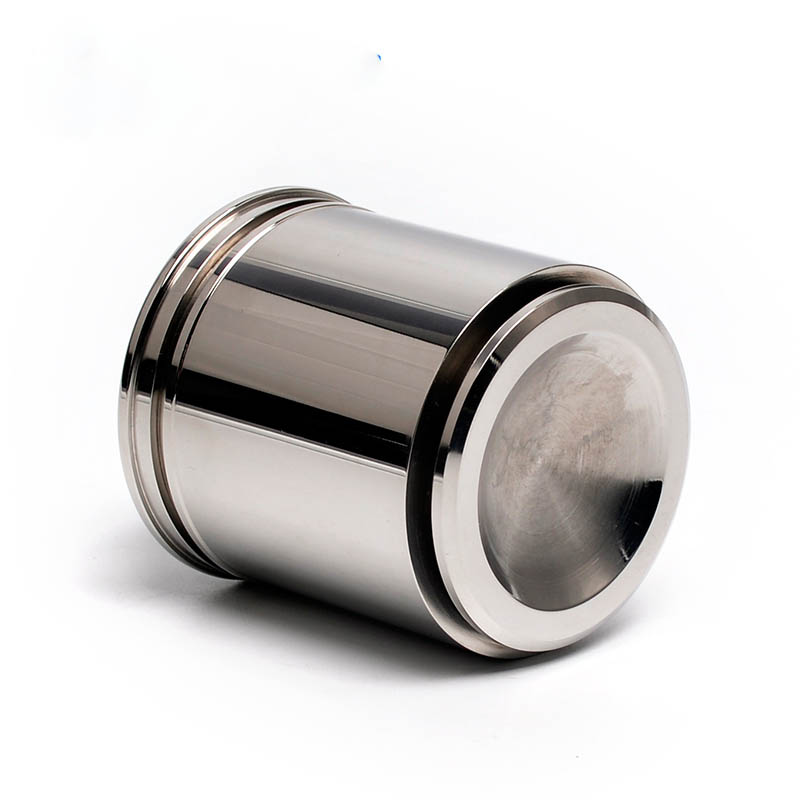
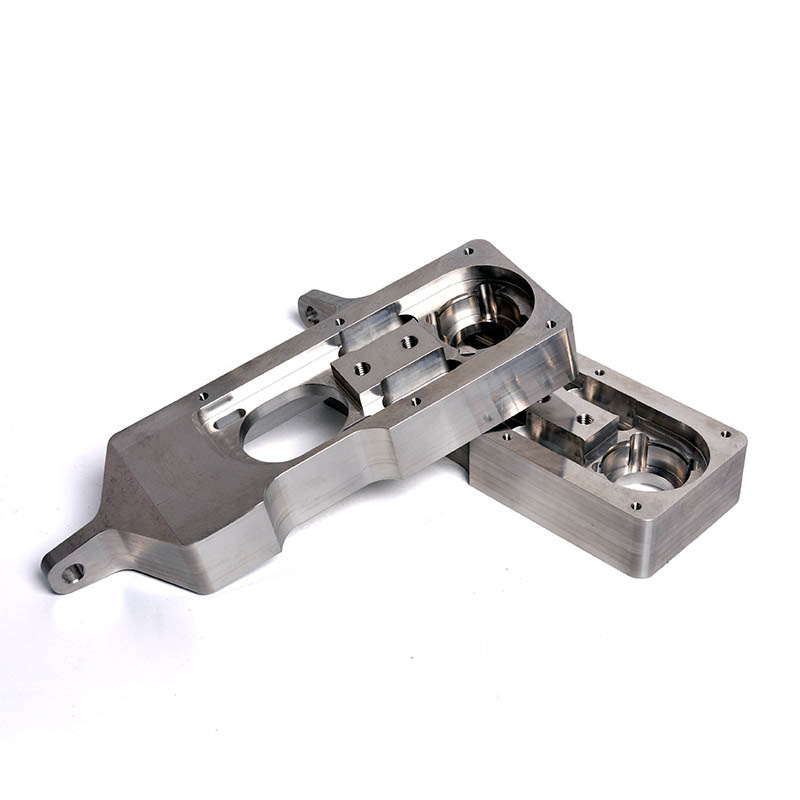
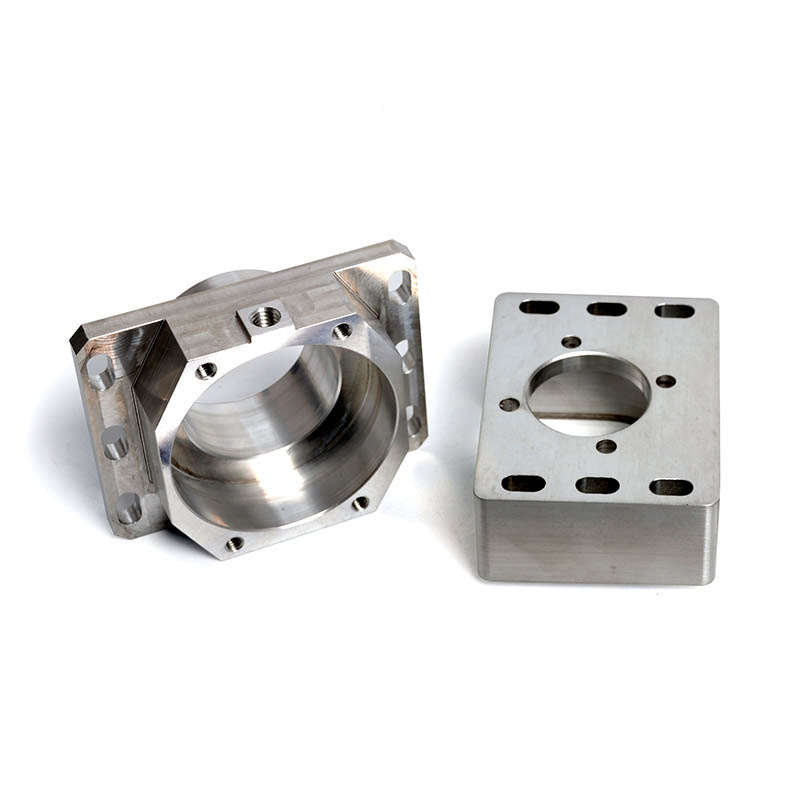
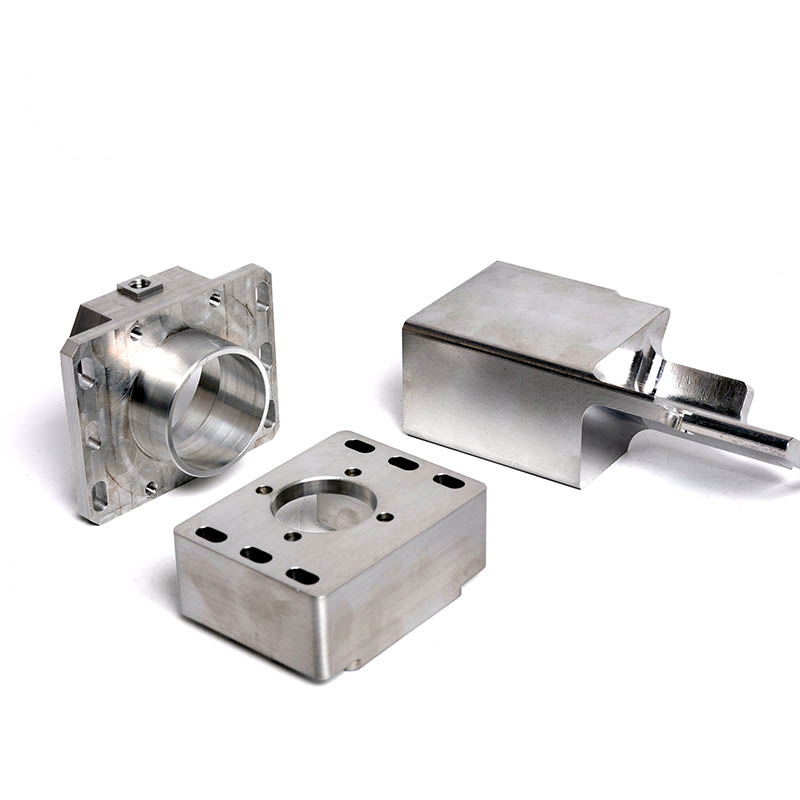
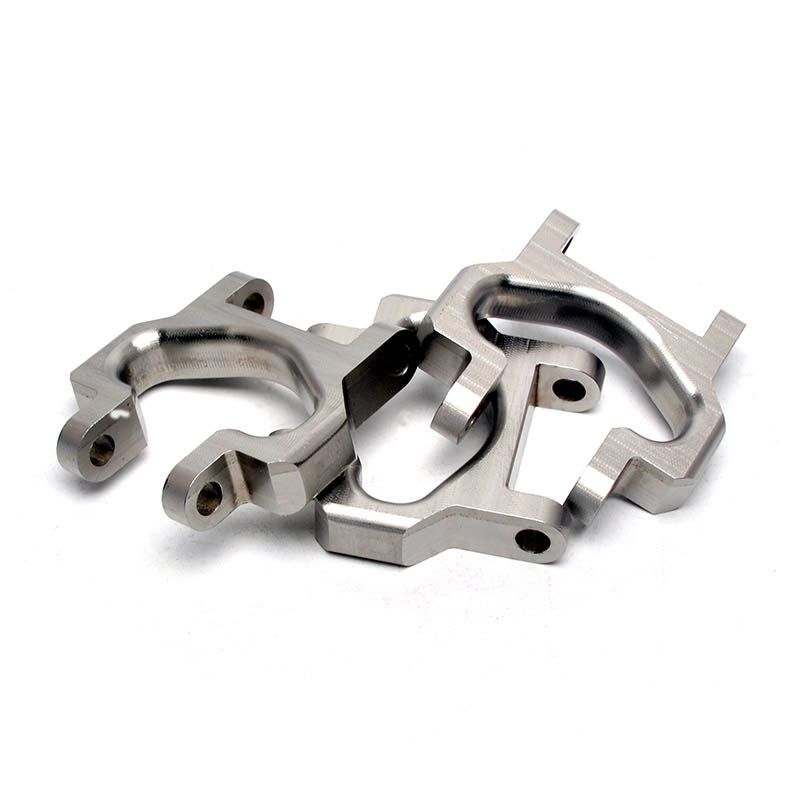

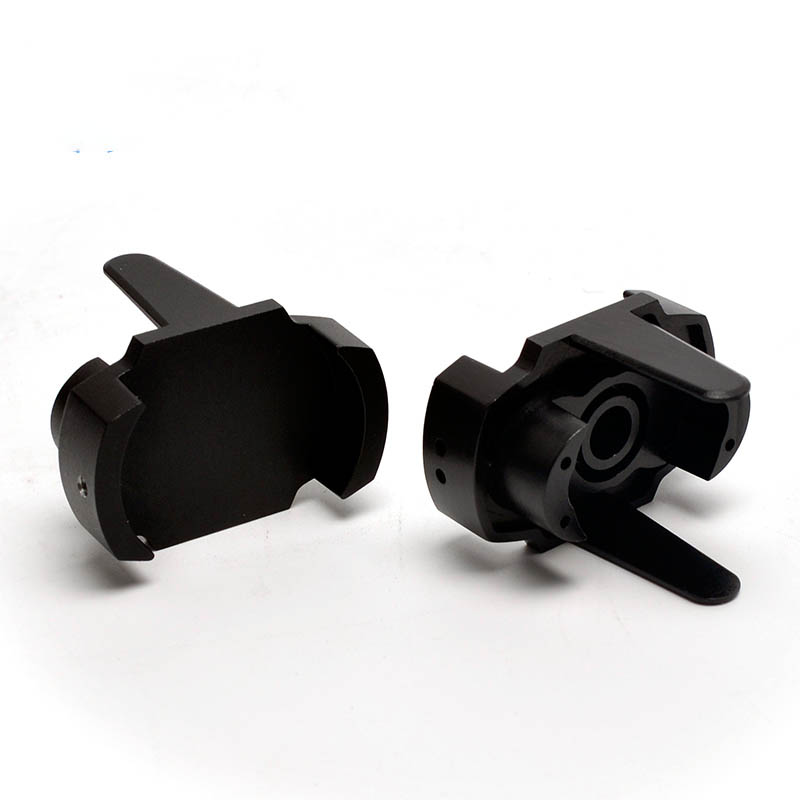
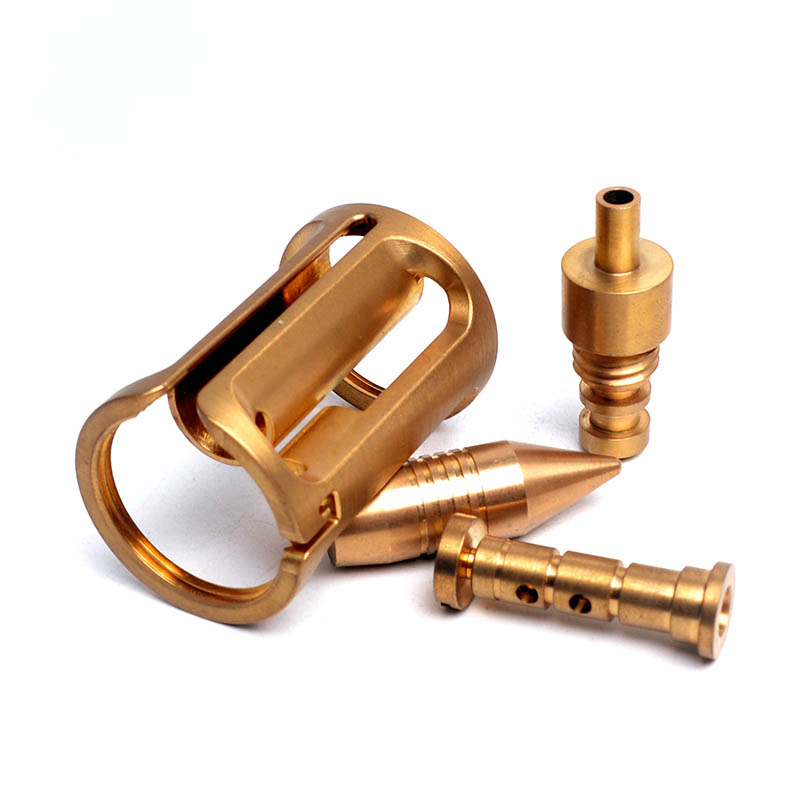
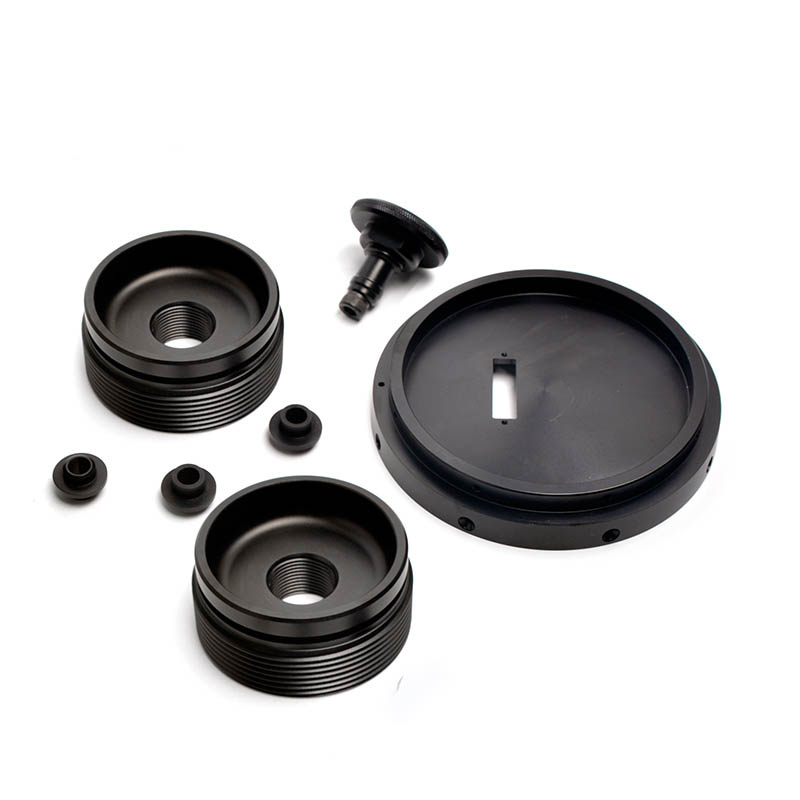
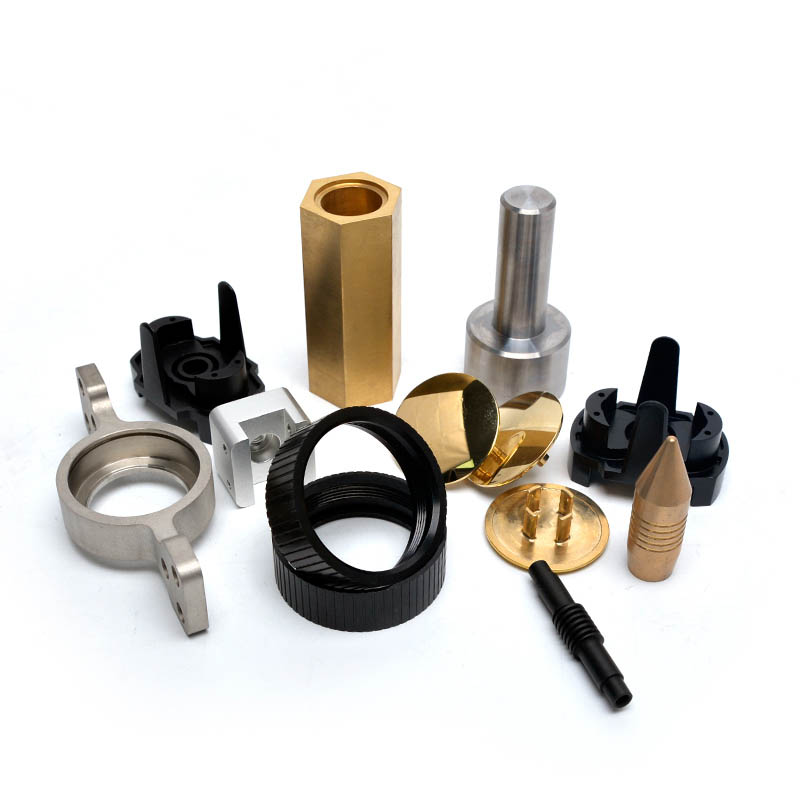
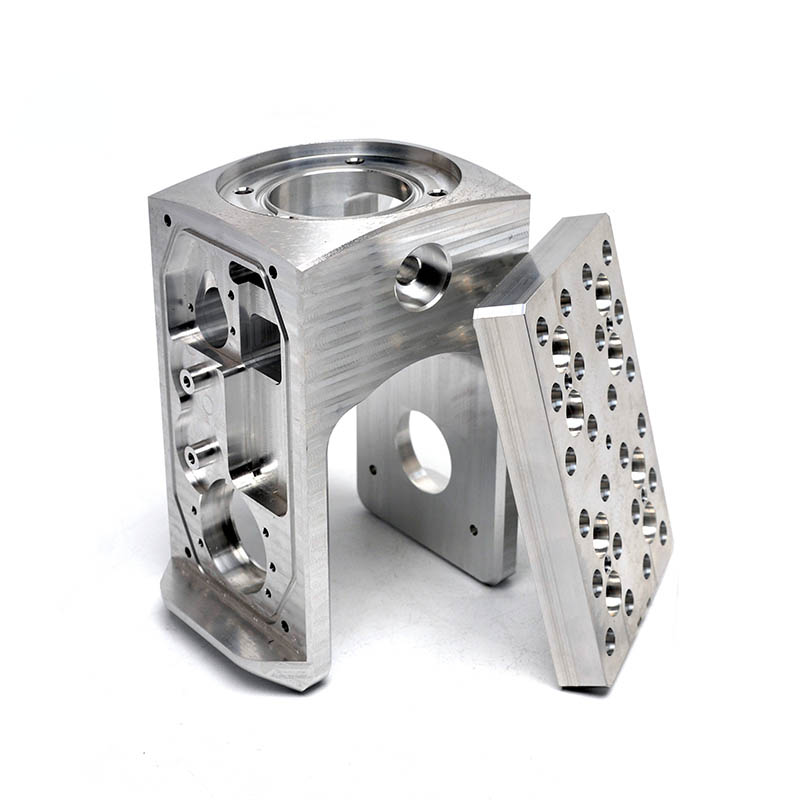
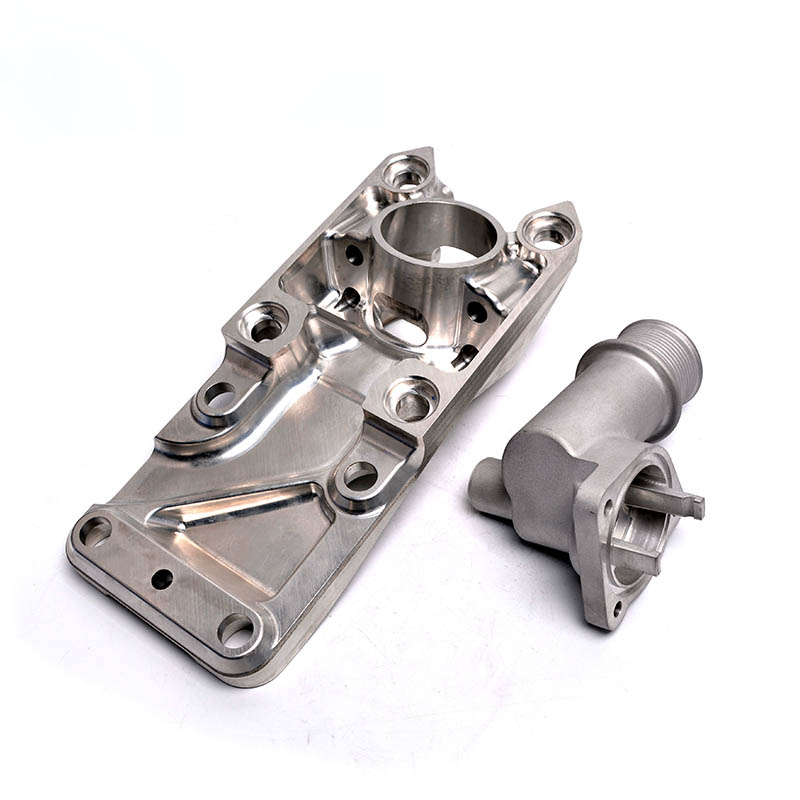
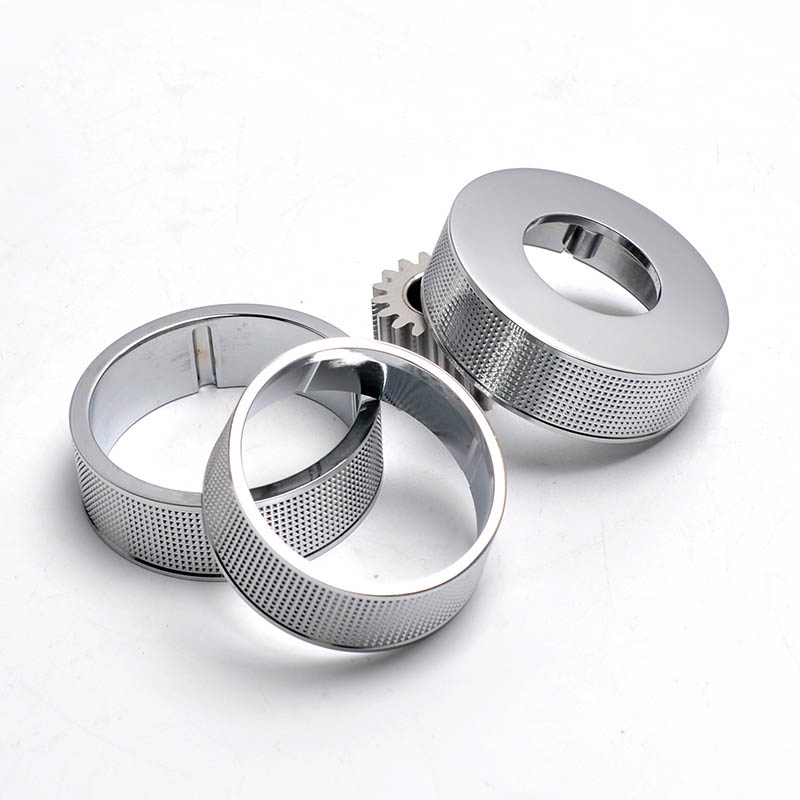
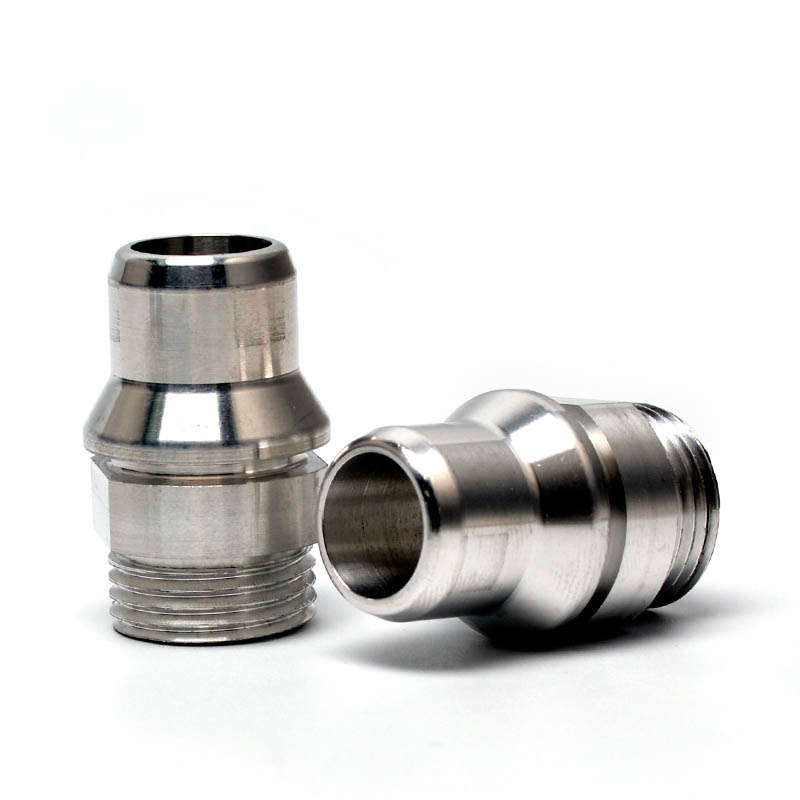
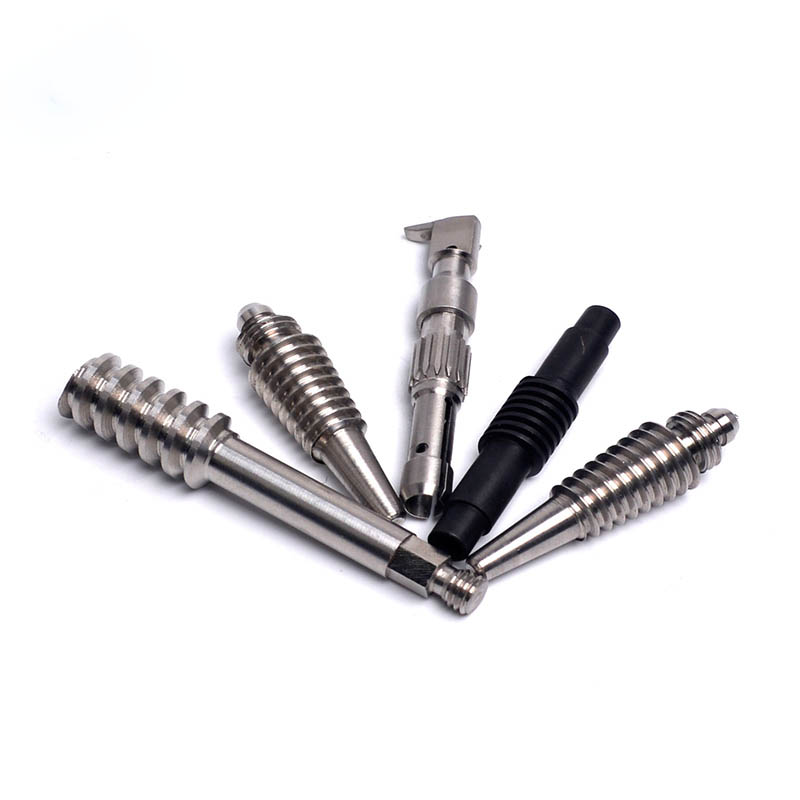
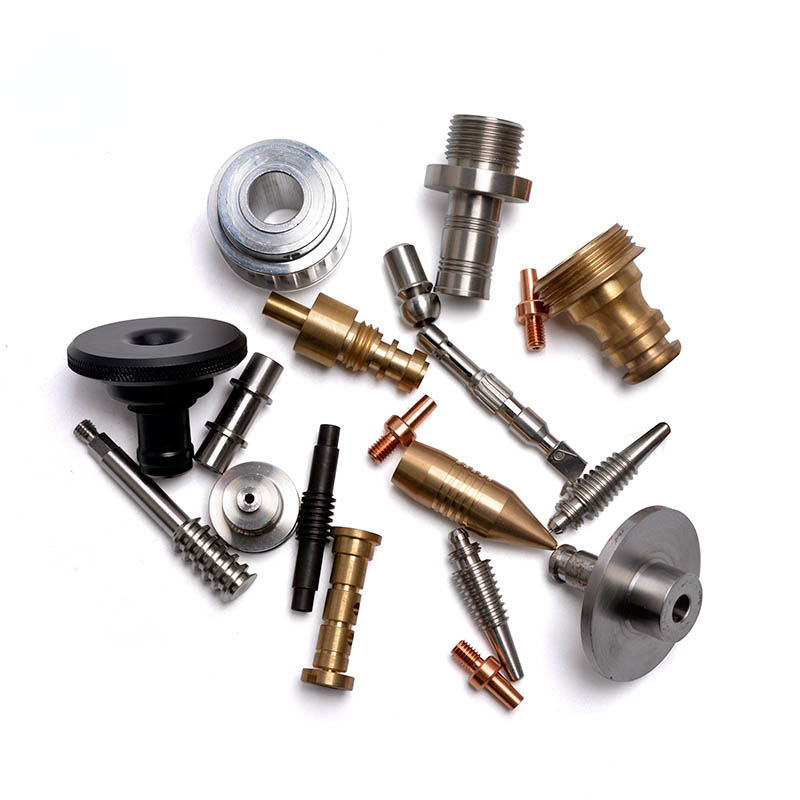
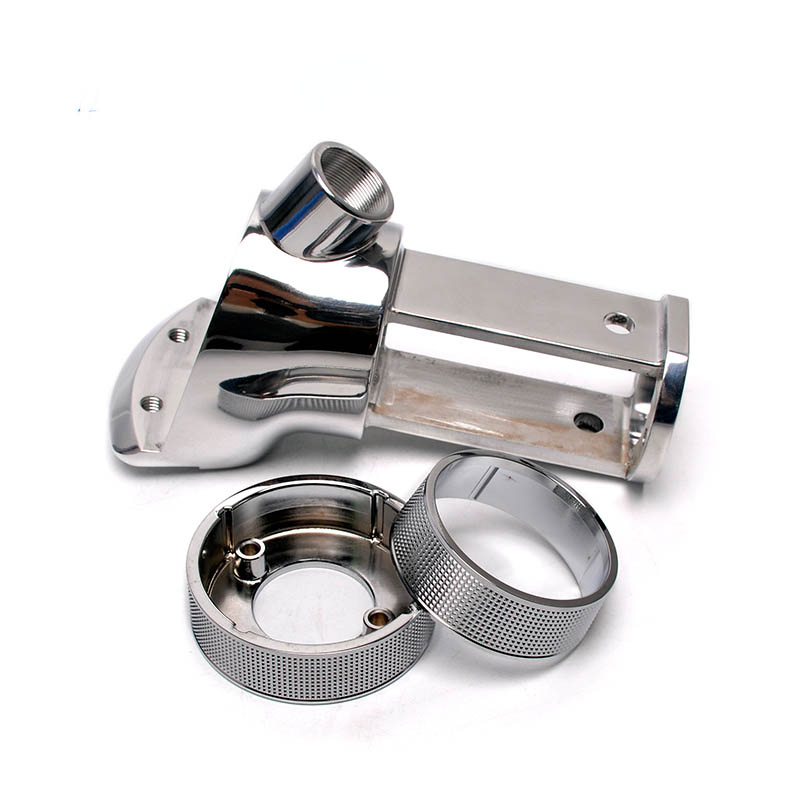
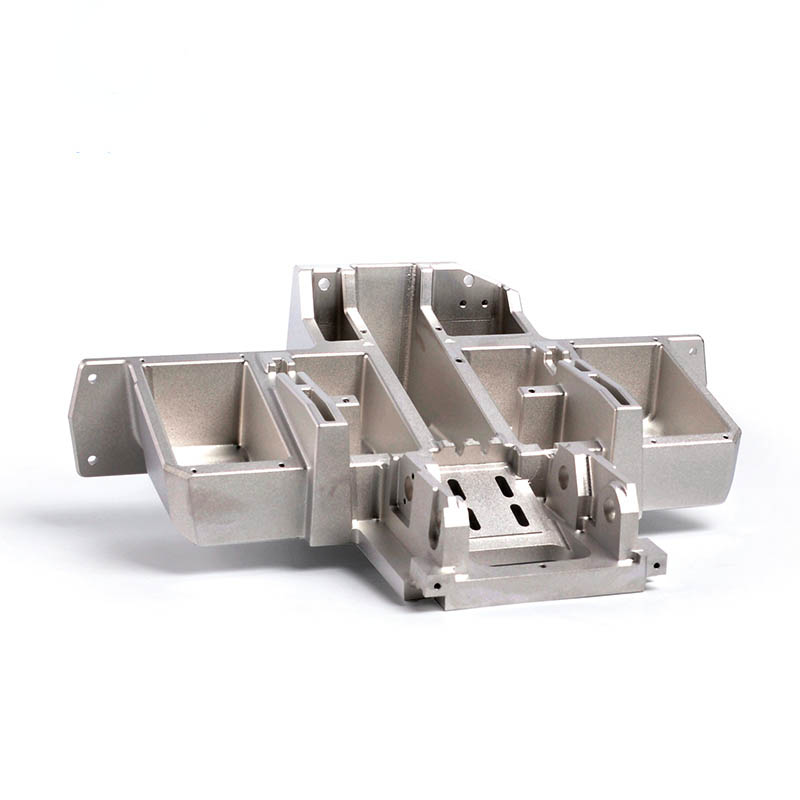
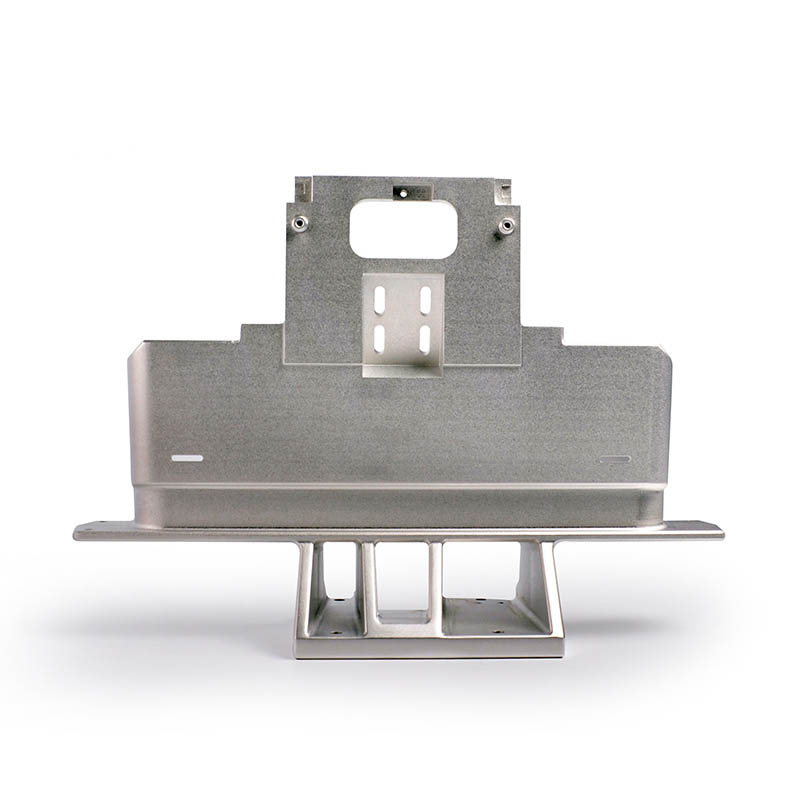
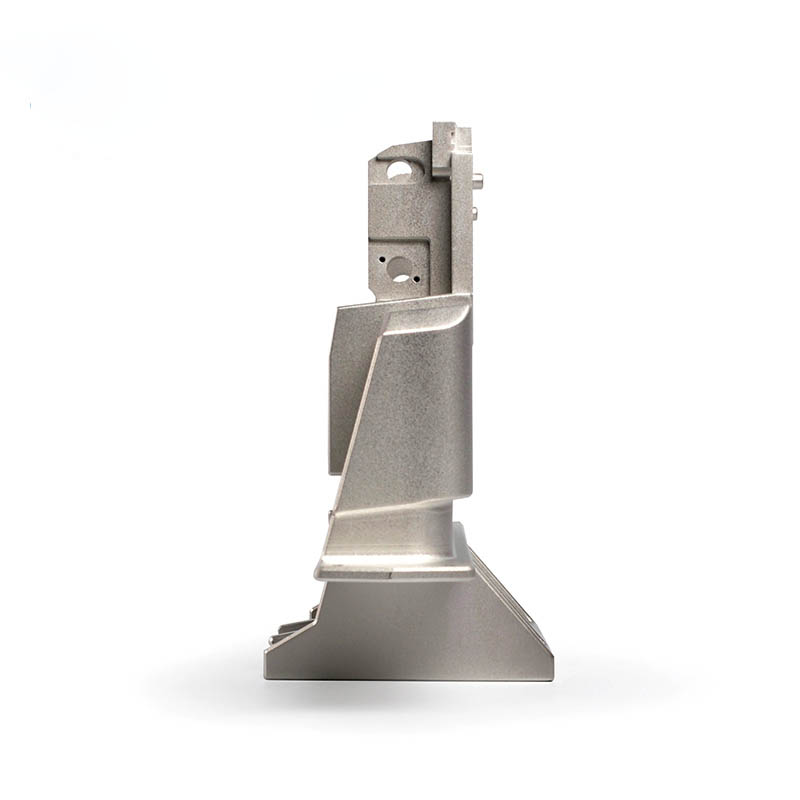

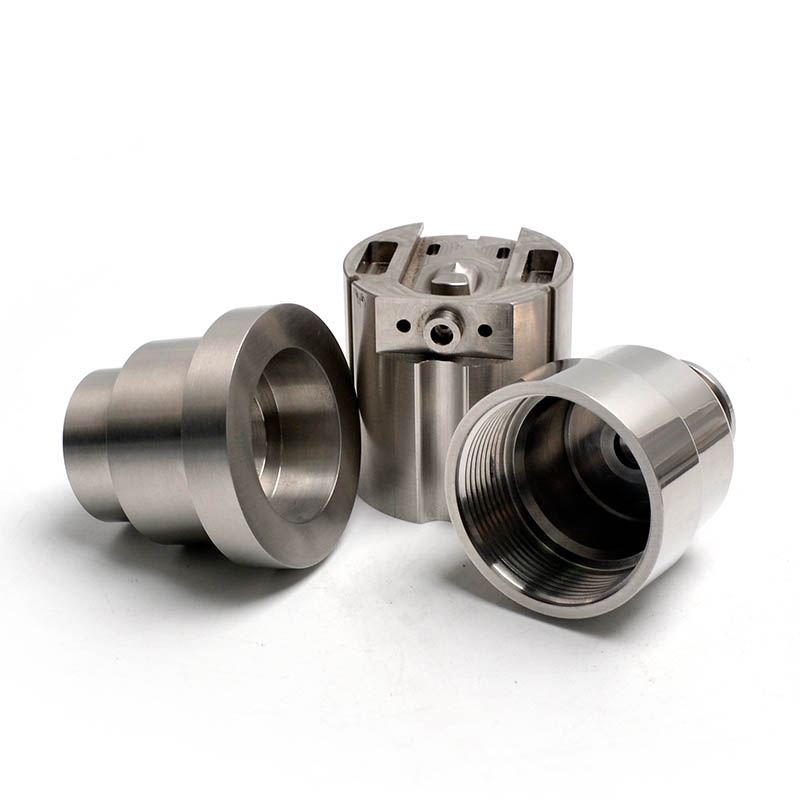
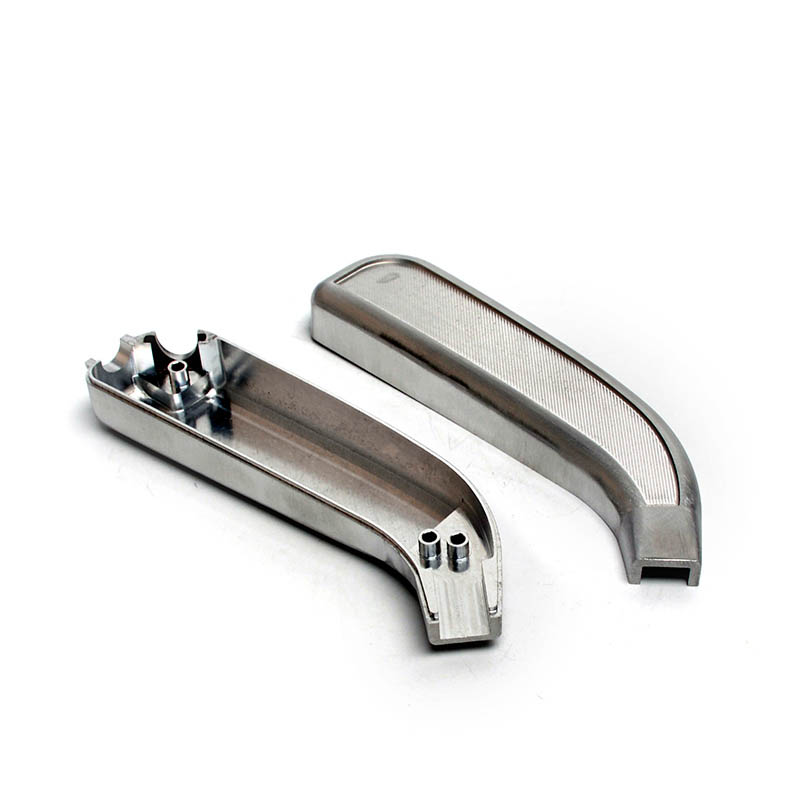

At CS Mold, a CNC machining company in china, we offer an extensive array of precision custom CNC machining services, including CNC milling, CNC turning, EDM, wire cutting, and surface grinding. With cutting-edge CNC centers (equipped with 3-axis, 4-axis, and 5-axis capabilities) and a skilled team, we handle any custom design, no matter its complexity. Count on us for your CNC parts manufacturing needs today!
CNC Process
CNC milling is a specialized process within precision CNC machining. It involves the use of a cutting tool that moves into the workpiece at different angles to remove material. This movement is precisely controlled by computer instructions, enabling exceptional precision and consistency. CNC milling machines are highly versatile and capable of creating intricate shapes and designs with great accuracy. They are widely utilized across industries to manufacture a diverse range of components, prototypes, and custom parts.
CNC Turning
CNC turning is a unique method within precision machining that involves removing material from a rotating workpiece using a cutting tool. The precise movement of the machinery is controlled by computer instructions, ensuring exceptional accuracy and consistency.
Unlike CNC milling, where the cutting tool rotates and approaches the stationary workpiece from different angles, CNC turning revolves around rotating the workpiece itself in a chuck. This rotational motion enables the creation of round or tubular shapes with precise and smooth curved surfaces, surpassing the capabilities of CNC milling or other machining processes.
Similar to CNC milling, CNC turning is utilized for both rapid prototyping and the production of end-use parts, offering efficient and accurate manufacturing solutions.
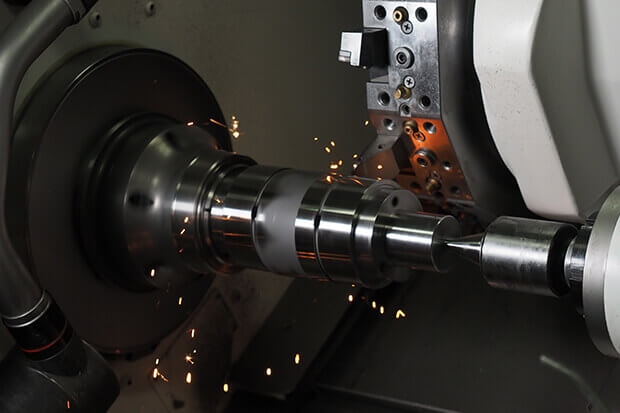
Tolerance Of CNC Machining
Feature size:
- Standard tolerance: +/- 0.005 inches
- Minimum tolerance for metal: +/- 0.002 inches
- Minimum tolerance for plastic: +/- 0.003 inches
Hole diameter:
- Standard tolerance: +/- 0.005 inches
- Minimum tolerance for metal: +/- 0.001 inches
- Minimum tolerance for plastic: +/- 0.002 inches
Flatness, Run Out, Cylindricity, Perpendicularity, and other Geometry:
- Standard tolerance: +/- 0.005 inches
- Minimum tolerance for metal: +/- 0.002 inches
- Minimum tolerance for plastic: +/- 0.003 inches
Please note that the above tolerances may not be applicable in certain scenarios. For instance, when machining a weldment or a plate below 1/4″ thickness exceeding 20″ in length (or 1/8″ thickness exceeding 10″ in length), the CS Mold team will evaluate and determine the appropriate tolerances on a case-by-case basis. This ensures that the tolerances are carefully reviewed and adjusted to meet the specific requirements of the project.
Available Materials
We offer an extensive selection of plastic and metal materials, including magnesium, mild steel, stainless steel, aluminum, brass, titanium, and engineering-grade plastic resins. These materials are readily available from our trusted suppliers, who have undergone a thorough evaluation process to ensure their reliability. We maintain a standard stock of these materials for immediate access.
In addition to our standard materials, we can also provide specialty options, such as super hard alloys, to cater to unique project requirements. Our team of engineers is available to discuss your specific needs and assist you in selecting the most suitable material for your application.
To ensure that all our materials meet regulatory requirements, we have an incoming materials inspection lab. Within this facility, we utilize sophisticated analytic testing instruments, including Raman spectroscopy, to meticulously examine and confirm the exact chemical and physical properties of our raw materials. This rigorous inspection process leaves no room for uncertainties, providing you with complete confidence and assurance in the quality and compliance of the materials we use in your project.
Titanium
Carbon Steel Alloys
Ultem
LDPE
ABS
Magnesium
PEEK
Aluminum
Polycarbonate
Acetal/Delrin
Radel
Acrylic
Nylon
Brass
Noryl
CPVC
Stainless Steel
Copper
- Alloy Steels
- HDPE
- Polycarbonate
- PET
- UHMW
Available surface treatment
- Plating
- Passivation
- Powder coating
- Screen printing
- Heat treating
- Custom
- Polishing
- Painting
- As machined (standard)
- Bead Blasting
- Engraving
- Anodizing
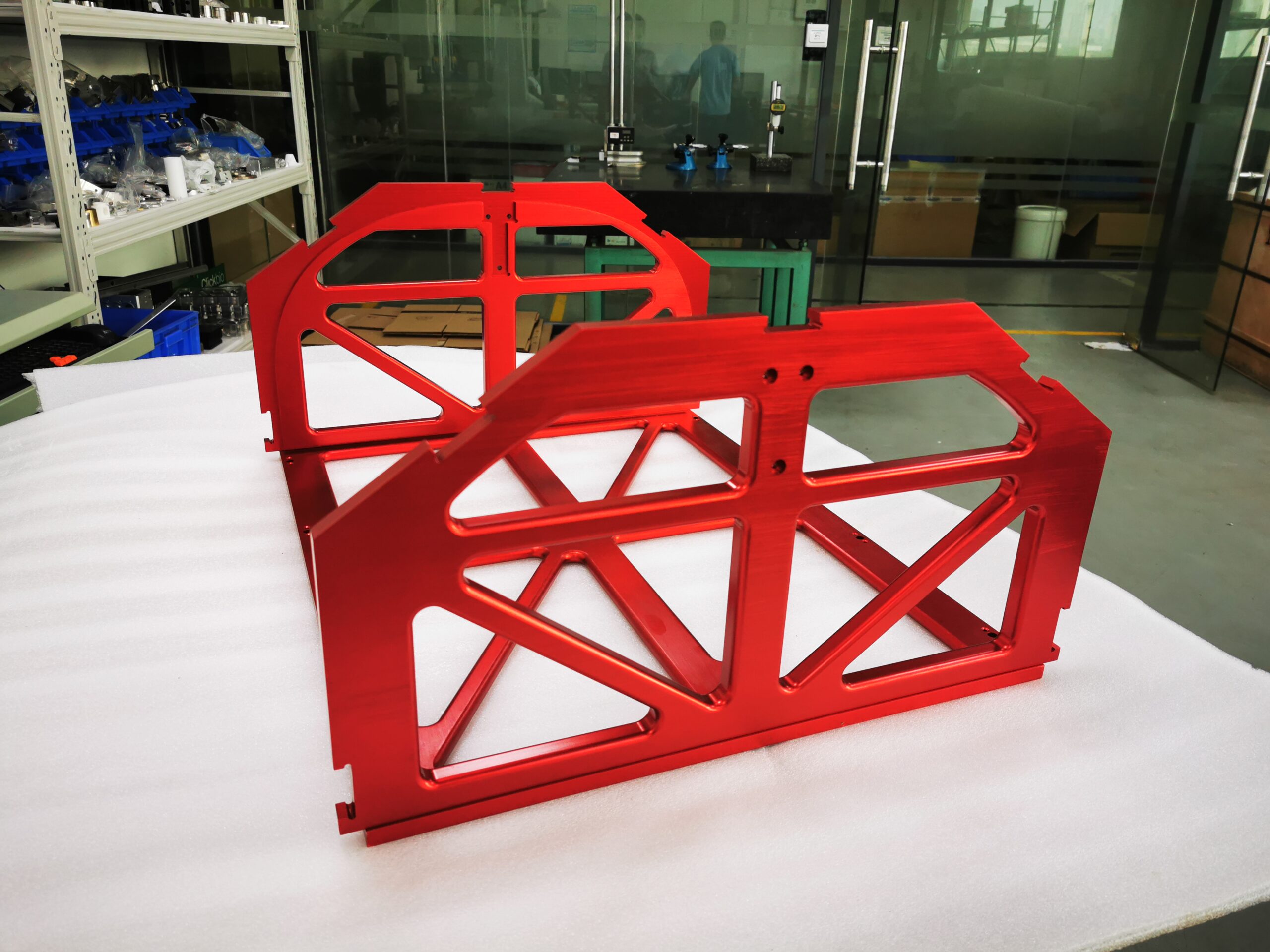
CNC machining offers several advantages:
Precision: CNC machines achieve high levels of accuracy and repeatability, ensuring consistent and precise parts with tight tolerances.
Versatility: CNC machining is flexible and capable of producing parts with complex geometries, intricate details, and a variety of sizes and shapes to meet diverse requirements.
Efficiency: CNC machines operate at high speeds, allowing for faster production times and increased productivity, optimizing manufacturing processes.
Automation: CNC machining is computer-controlled, enabling automation and reducing the need for manual intervention, resulting in improved efficiency and reduced labor costs.
Material Compatibility: CNC machining works with a wide range of materials, including metals, plastics, wood, and composites, providing versatility in material selection for different applications.
Economical and fast turnaround: CNC machining offers cost-effectiveness and rapid production turnaround, allowing for efficient manufacturing processes.
Ability to hold tight tolerances: CNC machines deliver precise and consistent results, maintaining tight tolerances to ensure the desired specifications of the parts.
Scalability and repeatability: CNC machining supports scalable production volumes, from single parts to high-volume production, while ensuring consistent quality and specifications.
Parts machined directly from 3D CAD models: CNC machines can directly process 3D CAD models, streamlining the manufacturing workflow and ensuring accurate replication of designs.
Standard delivery time of 1-2 weeks based on order: CNC machining typically offers prompt delivery times, ensuring timely production and delivery of parts.
Shorter lead time: In certain cases, CNC machining can accommodate shorter lead times based on available production capacity. At CS Mold, we can finish your parts in 2 days.
Common Applications: CNC machining finds extensive use in industries such as aerospace, automotive, electronics, medical, industrial equipment, and consumer goods, catering to a wide range of manufacturing needs.
Applications
CNC machining finds applications in diverse industries. Our team of experts specializes in delivering production solutions that expedite your product’s time to market.
WHY CHOOSE US
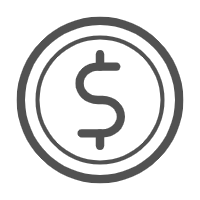
INSTANT QUOTING
Timely reply and provide the quote within 24 hours
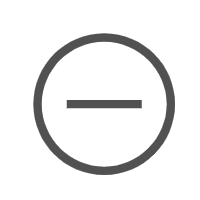
NO MOQ REQUIRED
Hord does not have minimum order quantity
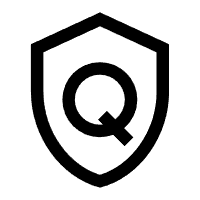
HIGH QUALITY
ISO 9001 & IATF 16949 certificated and inspect every step
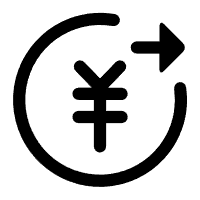
COST-EFFICIENT
+30% cost lower than western competitors
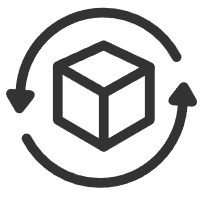
QUICK TUAROUND
Parts make in 7 days and delivery on time
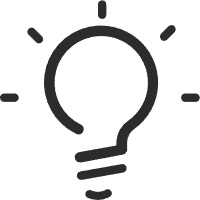
DFM ANALYSIS
Once receiving the inquiry, we will provide you with a preliminary DFM report
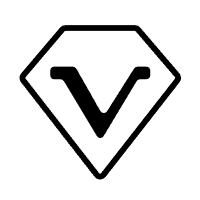
PROFESSIONAL SERVICES
More than 20 years of rapid tooling making
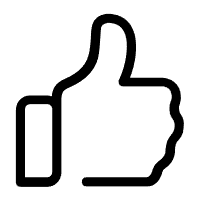
GOOD RAPUTATION FROM CUSTOMERS
Customers are satisfied with our services, products quality and delivery time.
OUR ADVANTAGE
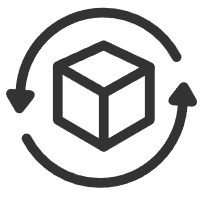
QUICK TUAROUND
Parts make in 5 days and delivery on time
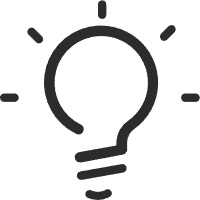
DFM ANALYSIS
Once receiving the inquiry, we will provide you with a preliminary DFM report
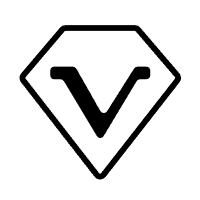
PROFESSIONAL SERVICES
More than 10 years of rapid tooling making
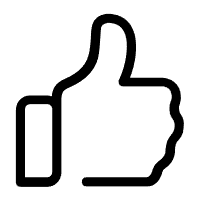
GOOD RAPUTATION FROM CUSTOMERS
Customers are satisfied with our services, products quality and delivery time.
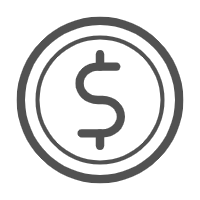
INSTANT QUOTING
Timely reply and provide the quote within 12 hours
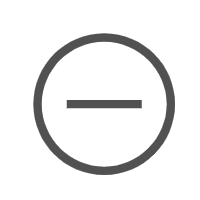
NO MOQ REQUIRED
CS Mold does not have minimum order quantity
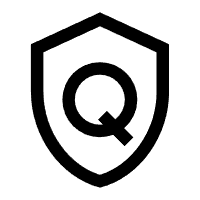
HIGH QUALITY
ISO 9001 & IATF 16949 certificated and inspect every step
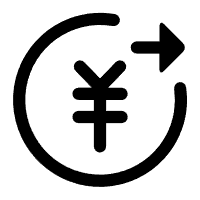
COST-EFFICIENT
+30% cost lower than western competitors
Production Workshop
Advantages of CNC Machining for Rapid Prototyping
CNC machining is a technology that utilizes computers and compatible software throughout the entire machining process. Program the machining path and production process before actual manufacturing to ensure ideal results are achieved. The following characteristics of this technology make it a suitable choice for rapid prototyping
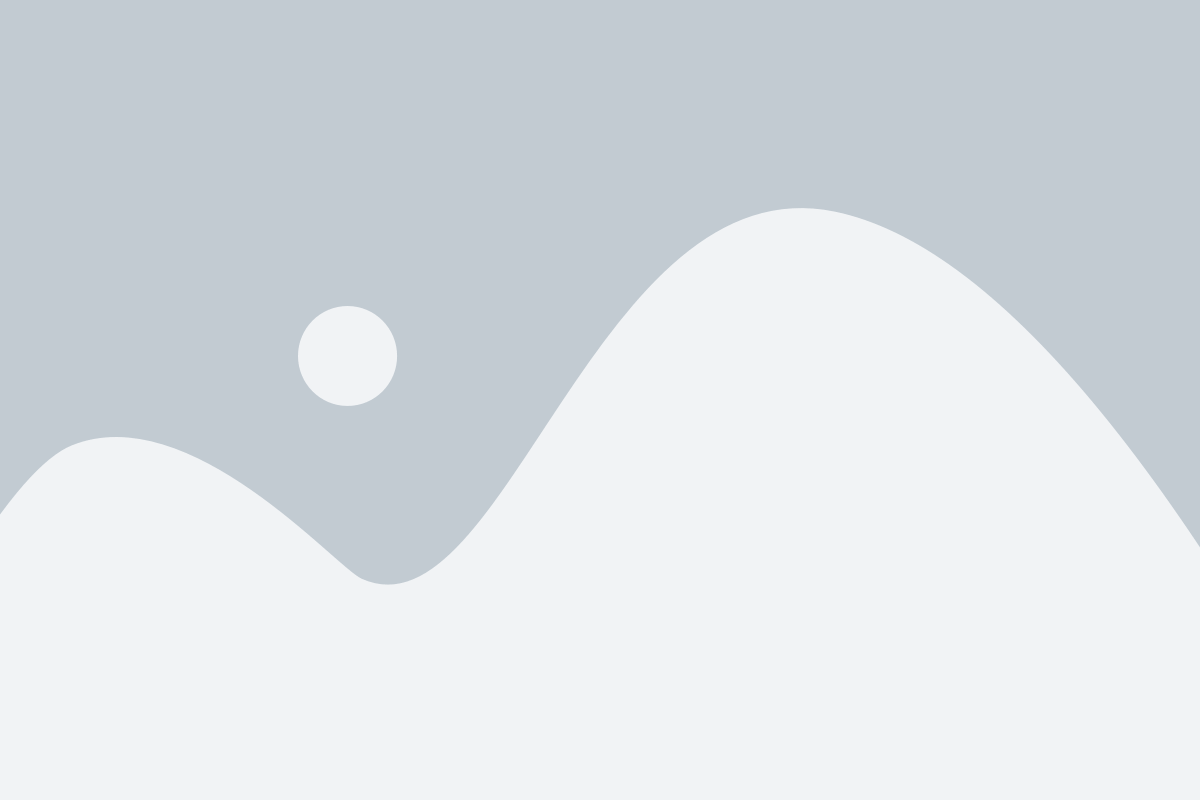
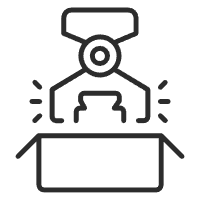
Rapid Production
CNC machining is a fast and automated process that complements rapid prototyping. It allows for simultaneous and effortless production of multiple prototypes. Additionally, CNC machining offers flexible tooling, enabling easy tool changes during production without interruptions. This versatility allows for the use of different tools to meet diverse machining needs.

Flexible Tooling
CNC machining provides flexible tools. Tools can be replaced within the production cycle without interrupting or stopping production. CNC machining can use different tools such as single point cutting tools, drilling tools, tapping tools, milling tools, etc
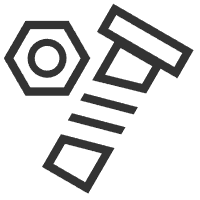
Minimum tolerance
CNC machining is a precision machining process. It can achieve the minimum tolerance. Therefore, by using this process, the expected dimensional accuracy can be easily achieved. In addition, CNC manufactured components typically do not require surface treatments such as polishing, so dimensional accuracy remains unchanged
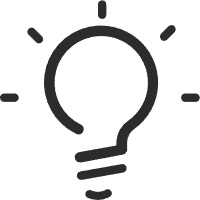
Modification scope
The CNC production cycle can be modified according to the design. Different techniques can be used to create a feature. For example, grooves can be formed by using grooving or deep cutting. CNC machining provides flexibility in selecting machining processes during the programming process.

Various materials
CNC machining can be used to process various materials, including various plastics and metals. This makes it an ideal choice for cross industry rapid prototyping design
Traditional machining is typically manual and requires human operators to control the machining tools. In contrast, CNC machining is automated, with computer programs controlling the machine’s movements. CNC machining offers higher precision, faster production times, and greater design flexibility compared to traditional methods.
Commonly used file formats for CNC machining include STEP, IGES, DXF, and STL. These formats contain the 3D CAD model or 2D vector data that guides the CNC machine in producing the desired part.
Tolerances refer to the allowable deviation from the desired dimensions of a part. The achievable tolerances in CNC machining depend on various factors, including the material, geometry, and machine capabilities. Generally, tolerances ranging from +/- 0.001″ to 0.005″ (or +/- 0.025mm to 0.127mm) are achievable with CNC machining.
CNC machining is versatile and can be used for both prototyping and production. It is particularly useful for prototyping due to its ability to produce high-quality parts quickly. For production runs, CNC machining offers cost-effective and efficient manufacturing processes, especially for small to medium batch sizes.
The time required for CNC machining depends on factors such as part complexity, material, quantity, and machine availability. Simple parts may be completed in hours, while more complex or larger production runs may take several days or weeks. Rapid prototyping services can often deliver parts within 1-5 days.